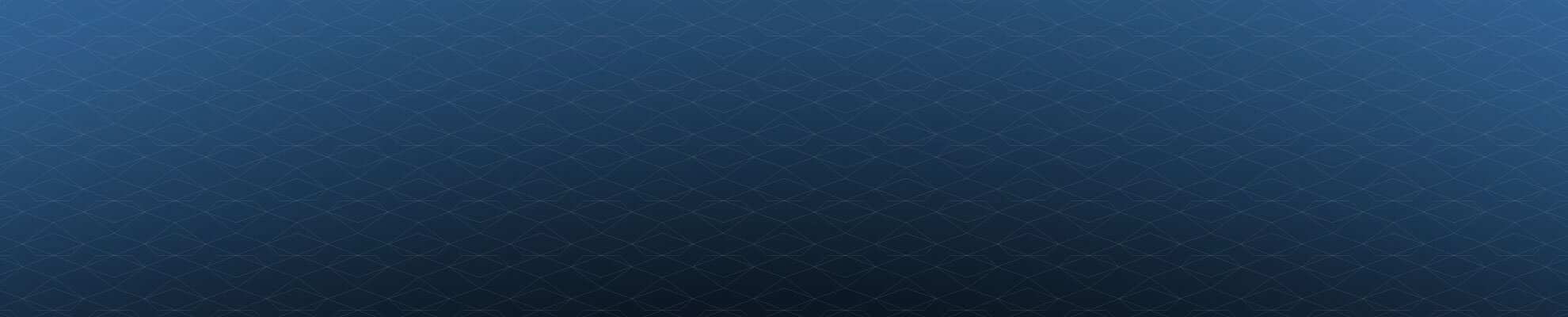
News and Resources
Browse by Category
Browse by Product
- All Dressing Products
- All Grinding Products
- CBN-Diamond Superabrasives
- Conventional Abrasives
- Diamond Lapping Compounds
- Diamond Rotary Dressers
- Diamond Stationary Dressers
- Hybrid Bond Grinding Tools
- Metal Bond Grinding Tools
- Plated Grinding Tools
- Resin Bond Grinding Tools
- Vitrified Bond Grinding Tools
CDT Is Boosting Capacity of Plated Grinding Wheels and Dressing Tools
Learn how Continental Diamond Tool is expanding capacity with a new PUMA Lathe, OGP SmartScope, and Doosan Milling Machine for plated grinding wheels and diamond rotary dressers.
An electroplated grinding wheel completes machining on CDT’s new PUMA DNT 2600LM CNC Lathe.
At Continental Diamond Tool, we invest in cutting-edge technology, skilled professionals, and continuous improvement. We aim to be the world’s most reliable source for innovative, high-quality, customized precision grinding solutions, offering exceptional performance and long life. The market has responded, and the last several years we have experienced tremendous growth.
To meet growing demand, our manufacturing center in North Wales has recently acquired three new pieces of equipment, made possible in part by the Conwy – UK Shared Prosperity Grant. This strategic investment is set to significantly expand our production capabilities for the manufacture of electroplated grinding wheels and diamond rotary dressers.
The Journey of Investment
In Q3 2023, CDT Ltd. in the United Kingdom embarked on an ambitious venture with the introduction of a new product line at its facility: custom-engineered electroplated cBN and diamond grinding wheels and tools. To support this initiative, we purchased dedicated electroplating tanks, stripping lines, and specialized manufacturing equipment for product testing and prototyping. This setup has been essential in ensuring that these products maintain the same precision and quality customers expect from CDT.
Meanwhile, our Rotary Diamond Dressers line — the specialty of this business center — continues to thrive. Sharing machining equipment between this booming line and the growing orders for electroplated products has become a challenge. Additionally, we are starting to see strain in our inspection capacity with the increased demand for these two technologies.
Strategic Acquisitions for Expanding Production
The introduction of a Puma lathe, OGP SmartScope, and Doosan milling machine addresses these challenges and paves the way for sustainable growth, diversification, and more efficient delivery for our customers.
Puma DNT 2600LM CNC Lathe
The first new equipment delivery took place in May with the arrival of the Puma DNT 2600LM CNC Lathe. This piece of equipment is crucial to meet the increasing demand for electroplated products independently from our rotary diamond dressers. Having a dedicated Puma Lathe for plated products assists in the timely delivery of these high-quality tools to our customers without compromise.
OGP SmartScope
In June we received the OGP SmartScope, a revolutionary 3-axis video measurement system. The SmartScope E7, with its IntelliCentric™ fixed lens optical system, 6-megapixel camera, and 5-position digital zoom, delivers high-resolution images that are essential for precise metrology. This state-of-the-art equipment will expand our inspection capacity to maintain the high standards expected of our precision products.
Doosan Milling Machine
Delivered in early September, the Doosan Milling Machine completes our trio of new equipment purchased with the government grant. This addition further bolsters production, ensuring we have the capacity to meet growing demands and continue our commitment to excellence.
A CNC operator programs CDT’s new PUMA Lathe that was delivered and installed in May.
A CDT quality tech measures a coupon on the new OGP SmartScope that was delivered in June.
A technician operates CDT's Doosan Milling Machine that was delivered in September.
Impact and Future Prospects
With the Puma Lathe, OGP SmartScope, and Doosan Milling Machine now up and running, we are already seeing the benefits in our production processes. The ability to utilize these machines for Plated products independently of our Rotary Diamond Dressers line has optimized our workflow and improved our overall efficiency.
These investments also support a long term strategy for CDT Ltd. They not only address our current production challenges but also set the stage for future growth and diversification at this facility. As we continue to innovate and expand our capabilities, we remain committed to the timely delivery of the high-quality products our clients expect.
Stay tuned for more updates as we continue to enhance our production capabilities and explore new horizons in the industry.
For more information on the Puma DNT 2600LM CNC Lathe, visit here.
Continental Diamond Tool Ltd., located in Kinmel Bay on the Western Coast of North Wales in the United Kingdom, is dedicated to providing top-tier superabrasive products for precision grinding and dressing.
At Continental Diamond Tool, we are excited about these investments and look forward to leveraging this equipment to further our mission of excellence in the industry. If you need a solutions provider for your precision grinding applications, please contact our sales team through our website contact form or
call +44 1745-343951 (UK) / 1-800-443-6629 (USA).
A Breakdown of the 4 Common Bond Systems in High Precision Grinding
Discover CDT's four essential bond systems for superabrasive grinding wheels: Resin, Metal, Vitrified, and Electroplated. Optimize operations with expert insights from Jeff Wirth.
If precision grinding is a critical component of your manufacturing process, understanding the bond system of your grinding wheel will help you in maintaining operational efficiency and product quality. In this detailed overview, we will explore the four most common bond systems used in superabrasive grinding wheels: Resin, Metal, Vitrified, and Electroplated. Continental Diamond Tool Engineering Manager Jeff Wirth breaks down the components of these bond systems, discussing their composition, manufacturing processes, and ideal applications in Episode 6 of The Grinding Chronicles. Watch Jeff’s video or read on to learn more about selecting the right bond to optimize your grinding operations.
The Grinding Chronicles - Episode 6
Understanding the Four Common Bond Systems
Resin Bonds
Resin bonds are plastic-based compounds typically made from phenolics or polyimides. These bonds are versatile and can be enhanced with fillers such as copper or silicon carbide to improve performance. The manufacturing process for resin bonds at CDT begins with creating a tailored formulation that includes the bond material, abrasive, and fillers. This dry powder mixture is blended in special tumblers and then carefully and uniformly packed into mold cavities. The molds undergo hot pressing, where temperature and pressure are meticulously controlled to achieve the desired density. Finally, the wheels are finished by machining and grinding them to the specified size and geometry.
Properties and Applications:
Tough and Durable: Resin bonds are fully dense and easy to use, making them suitable for a variety of grinding applications.
Versatile: They can work with nearly any material, from hard metals to softer alloys.
Enhanced Performance: Fillers like copper or silicon carbide can be added to improve heat dissipation and grinding efficiency.
Wide Range of Applications: Suitable for diverse grinding tasks, including tool and cutter grinding, centerless grinding, and surface grinding.
Metal Bonds
Metal bonds can be composed of various metals, including bronze, copper, and iron, and may sometimes be alloyed with precious metals like silver. Metal bonds are known for their hardness, toughness, and durability, making them ideal for grinding highly abrasive materials such as glass and ceramics. Although metal bonds grind more slowly than other types, they offer the longest lifespan. The manufacturing process for metal bonds at CDT is similar to that of resin bonds, involving formulation, mixing, molding, hot pressing, and finishing.
Properties and Applications:
Hardest and Toughest: Metal bonds are the most challenging to use but provide superior durability.
Long-Lasting: They offer the longest lifespan among bond types, reducing the frequency of wheel changes.
Ideal for Abrasive Materials: Best suited for grinding materials like glass, ceramics, and carbide.
Durability: Excellent for applications requiring extreme durability and extended wheel life, such as in the automotive and aerospace industries.
Vitrified Bonds
Vitrified bonds are made from glass or ceramic materials, creating a porous structure that significantly reduces grinding force. This allows for higher grinding speeds, making vitrified bonds ideal for high-production applications. These bonds offer moderate to high material removal rates and excellent form accuracy, as they can be dressed and profiled in-process using rotary dressers. The manufacturing process for vitrified wheels at CDT involves formulation, mixing, cold pressing, and a sintering (baking) process to fuse the glass or ceramic together. The final step is finishing, similar to the other bond types.
Properties and Applications:
Porous Structure: Lowers grinding force and allows increased speeds, enhancing efficiency.
High Production: Ideal for high-production applications such as automotive part manufacturing.
Moderate to High Material Removal Rates: Efficient for large-scale operations, balancing speed and precision.
High Form Accuracy: Can be dressed and profiled in-process using rotary dressers, making them suitable for precise and consistent grinding tasks.
Electroplated Bonds
Electroplated (or plated) bonds consist of a single layer of abrasive held by a nickel-based metal bond. The process begins with machining the desired wheel size and geometry onto a steel wheel core. The non-plated surfaces are masked to prevent unwanted plating. The wheel core is then placed in a bath with a nickel-based solution and the abrasive material. By applying a positive charge on one side and a negative charge on the other, nickel plating is deposited onto the wheel core, causing a single layer of abrasive to adhere. Excess abrasive is removed, and the plating process continues until the abrasive layer is encapsulated to the desired level, typically 50-100% depending on the application. Electroplated products are suitable for complex geometries and low to medium production applications due to their high material removal rates and fast grinding speeds.
Properties and Applications:
High Material Removal Rates: Provides the fastest grinding speeds, ideal for rapid material removal.
Cost-Effective: Single layer of abrasive can be stripped and replated, extending the wheel’s life.
Ideal for Complex Geometries: Precise form replication with minimal finishing, suitable for intricate designs.
Low to Medium Production: Suitable for specific applications requiring detailed shapes and efficient material removal.
Key Considerations for Selecting the Right Bond System:
Choosing the appropriate bond system for your grinding application is crucial for achieving optimal performance and quality. Each bond type offers unique properties and advantages, making them suitable for different materials and grinding conditions. By understanding the composition, manufacturing processes, and ideal applications of Resin, Metal, Vitrified, and Electroplated bonds, you can make informed decisions to enhance your grinding operations.
Factors in Bond System Selection:
Material to be Ground: The hardness and abrasiveness of the material significantly influence the choice of bond.
Grinding Speed and Efficiency: Consider whether the application requires high-speed grinding or if longevity and durability are more critical.
Application Specifics: Determine if the grinding operation involves complex geometries or requires high form accuracy.
Production Volume: High-production environments may benefit from vitrified bonds, while electroplated bonds are ideal for low to medium production with intricate details.
If you have any questions or want to learn more about which bond type would work best for your application, please reach out to our application engineers at TheGrindingChronicles@CDTUSA.net. For more industry insights and expert advice, check out these articles or watch our playlist for The Grinding Chronicles on YouTube. By leveraging the right bond system and understanding its properties, you can significantly improve your grinding efficiency, product quality, and operational cost-effectiveness.
Essential Role of Diamond Rotary Dressers in Precision Grinding
This article explores the essential role of Diamond Rotary Dressers in maintaining the efficiency and precision of grinding wheels across various industries, highlighting their types, bond structures, applications, and the expertise of Continental Diamond Tool in providing customized, high-quality solutions.
Grinding wheels, essential for precision manufacturing and shaping of materials, inevitably wear down with use. This wear occurs due to the abrasive action against hard materials, causing gradual degradation of the wheel’s surface. Over time, the cutting edges of the abrasive particles dull, and the bond holding these particles in place can break down, leading to a loss of material from the wheel. This wear not only reduces grinding efficiency but also affects the accuracy and finish of the ground parts.
"Every grinding wheel, whether it be conventional or superabrasive, requires dressing to maintain its profile and cutting performance. Rotary Diamond Dressers are especially useful for precision applications, when you're trying to achieve micron-level tolerances," explains Ed Pitock, Production Manager for Rotary Diamond Dressers.
The Best tool for Grinding Wheel maintenance
Types of Diamond Rotary Dressers
There are two primary types of diamond rotary dressers, also called diamond rolls:
Traverse-Style Diamond Rolls: Move across the grinding wheel, providing a comprehensive dressing solution. Often a single traverse-style dresser can be programmed for use with many different profiles.
Plunge-Style Diamond Rolls: Plunge directly into the grinding wheel, offering uniform dressing of a single precise profile for a specific application.
At Continental Diamond Tool, we custom design both types for our customers to meet the requirements of their processes, machines, and part specifications. This ensures that the desired surface finish and geometry are consistently achieved.
Bond Structures
The bond structure in Diamond Rotary Dressers refers to the material and method used to hold the abrasive diamond particles in place. The bond structure determines the strength, durability, and performance characteristics of the dresser. There are different types of bond structures, each suited for specific applications:
Infiltrated Bond Structure: Also known as sintered, this structure involves filling the spaces between diamond particles with a powdered metal that is then sintered. It is known for its robustness and longevity, making it suitable for demanding applications.
Reverse Plated Bond Structure: In this method, diamond particles are electroplated with a layer of nickel. While not as durable as infiltrated bonds, reverse plated bonds allow for more complex geometries and are used for specialized applications.
CVD Inserts
In the context of Diamond Rotary Dressers, CVDs refer to Chemical Vapor Deposition diamonds. These synthetic diamonds are created in a controlled environment, allowing for the production of high-purity and high-quality diamond material. Advantages include:
Purity: CVD diamonds have fewer impurities compared to natural diamonds, resulting in reliable and predictable performance.
Consistency: The controlled manufacturing process ensures uniformity and consistency in diamond quality for reliable results.
Customization: The CVD process allows for the production of diamonds with specific properties that are advantageous to industrial applications. This material can also be cut into specific sizes and shapes for reinforcing of a high wear areas or used as the main lot abrasive in the roll.
CVD diamonds are sometimes added to Diamond Rotary Dressers due to their unique properties, including exceptional hardness, wear resistance, and thermal conductivity. By incorporating CVD diamonds, rotary diamond dressers become a powerhouse in micron-scale precision, superior durability, and enhanced efficiency, making them ideal for highly demanding dressing applications.
Industrial Applications
Diamond Rotary Dressers are utilized across various industries, offering precise solutions for different needs. Key sectors include:
Automotive: These dressers ensure that automotive components meet stringent tolerance requirements, contributing to the reliability and performance of vehicles.
Aerospace: The precision of Diamond Rotary Dressers is critical for producing aerospace components capable of withstanding extreme conditions.
Cutting Tools: These dressers maintain the sharpness and efficiency of cutting tools, enhancing their performance and longevity.
Bearings: Precision dressing is essential for producing high-quality bearings that meet the rigorous demands of various applications.
By maintaining critical dimensions, enhancing longevity and sharpness, and providing smooth and flawless surfaces, Diamond Rotary Dressers play a vital role in supporting these key industries.
Quality and Customization in Manufacturing
The quality and custom design of Diamond Rotary Dressers are paramount to their effectiveness. "When customers visit our Indiana facility here, they're blown away," notes Troy Giacherio, Product Manager for Rotary Diamond Dressers. "They're going to see the attention to detail, the quality that's taken in every step of the process, and the meticulous customization that we do."
Each product is designed specifically for the customer's process, machine, and part, ensuring a precise fit and optimal performance. This level of customization ensures that the unique needs of each customer are met, providing the ideal solution to their grinding processes.
Customer Support and Technical Expertise
At Continental Diamond Tool, customers also benefit from our extensive support and technical expertise. In 1984, Consort Precision Diamond Company set out to build a reputation as the finest maker of the emerging Diamond Rotary Dresser technology.
Fast-forward 40 years, under Continental Diamond Tool’s leadership, these advancements have been added to the mix at its 200,000 sq. ft. manufacturing center in the United States. Combining the British ingenuity with CDT’s 50 years of excellence in superabrasive grinding wheels, CDT has solidified its position as a leader in offering this cutting-edge solution for precision manufacturing.
Our Diamond Rotary Dresser departments span two continents and have decades of combined experience. Our team is readily available to assist with any challenges, ensuring that customers receive tailored solutions and guidance. "Here at CDT, our customers can always rely on our experience, our technical expertise, and our customer service," Giacherio emphasizes.
An Essential in Advanced Manufacturing
Diamond Rotary Dressers provide essential solutions for maintaining the efficiency and precision of grinding wheels across multiple industries. With robust bond structures, customization options, and applications in sectors like automotive, aerospace, cutting tools, and bearings, these tools are critical for achieving high-precision outcomes. Continuous investment in advanced technology and quality assurance ensures that Diamond Rotary Dressers from Continental Diamond Tool meet and often exceed customer expectations. By utilizing the latest advancements in superabrasives and precision engineering, these tools address the evolving needs of various industries in their precision manufacturing processes.
Brian VanHall Hired as CEO of Continental Diamond Tool
Continental Diamond Tool announces Brian VanHall as the new CEO to advance the company's mission of delivering high-quality, custom-engineered tooling solutions to customers around the world.
New Haven, Indiana – May 31, 2024 – Continental Diamond Tool is delighted to announce the hiring of Brian VanHall as the Chief Executive Officer, starting June 3, 2024. Founded in 1973, Continental Diamond Tool is a global leader in the design, manufacture, and application of precision grinding products for a multitude of industries.
Brian VanHall has been hired as the Chief Executive Officer at Continental Diamond Tool, starting June 3, 2024
As CEO of Continental Diamond Tool, Mr. VanHall is excited to advance the company's mission of delivering high-quality, custom-engineered tooling solutions to customers around the world. “I am honored to be entrusted by the Viggiano family and CDT team to help grow the legacy of excellence in developing and delivering innovative solutions for advanced manufacturing applications” said VanHall.
Mr. VanHall previously served as Executive Vice President with Ambassador Enterprises. With over 20 years of executive experience, Mr. VanHall brings a record of leading innovative projects, transformative programs, and strategic partnerships for multinational organizations to grow economic value, organizational effectiveness, and social impact. Brian received his Master of Business Administration (MBA) from Baylor University and holds graduate certifications in organizational leadership, corporate governance, strategic planning, and project management.
Nick Viggiano, President of Continental Diamond Tool, said, “We are excited to welcome Brian VanHall to the team and look forward to a future of continued excellence and growth with his leadership.”
For more information about our management team at Continental Diamond Tool, click here.
About Continental Diamond Tool Corporation:
Established in 1973, Continental Diamond Tool Corporation (CDT) is a premier manufacturer of precision tooling solutions for industries worldwide. With a legacy of technical expertise and innovation, CDT is renowned for its custom superabrasive grinding wheels and diamond dressing tools. CDT is also North America’s exclusive source for Krebs & Riedel conventional abrasive wheels, which are custom profiled at our facility. Headquartered in New Haven, Indiana, CDT operates a state-of-the-art 200,000 sq. ft. manufacturing center dedicated to delivering high-quality products and exceptional customer service. Learn more >
Recognizing the Importance of Cleaning and Maintenance at Continental Diamond Tool
Discover how the cleaning and maintenance teams at Continental Diamond Tool are essential to producing high-quality diamond tools while ensuring workplace safety and efficiency.
In manufacturing, the spotlight often shines on the experienced engineering team, the cutting-edge machinery, and the high precision grinding products we produce. Yet, behind the scenes, two critical forces work tirelessly to ensure that everything operates smoothly: the cleaning and maintenance crews. At Continental Diamond Tool, we recognize the indispensable role these teams play in our daily operations and overall success.
Keeping Operations Running Smoothly
The primary role of cleaning and maintenance is to ensure that all equipment and facilities are in top working condition. In the manufacturing process, even minor disruptions can lead to significant delays and costs.
Dan Becker, Maintenance Supervisor, details the meticulous care his team puts into preserving operational efficiency: "We maintain all of the manufacturing equipment in the building. For example, we manage the coolant in 5 dozen CNC machines and routinely clear out all of the chips. We also have 12 grinders, which we take completely apart, clean out, and inspect the belts and pulleys for wear regularly." This is just a snapshot of the thoroughness with which they maintain operations.
Regular maintenance and thorough cleaning prevent machinery breakdowns, allowing operations to continue without interruption. These efforts are crucial for ensuring that our orders are delivered on time. In this way, our cleaning and maintenance teams ultimately contribute to customer satisfaction. Timely delivery is a priority our customers rely on.
Ensuring Safety and Quality Standards
Quality and safety are also top of mind at Continental Diamond Tool, and our cleaning and maintenance crews are key players in both of these areas.
Maintaining a safe working environment starts with cleanliness. By regularly removing debris, cleaning spills, and ensuring that all areas are free from hazards, our cleaning techs help prevent accidents and injuries. Likewise, well-maintained facilities and equipment are essential for operational efficiency. Their diligent work supports our commitment to providing a safe workplace for all employees.
Quality requires precision. In the manufacturing of our high-quality diamond tools, this means that even the smallest particles can impact the final product. Our cleaning crew works tirelessly to maintain a contaminant-free environment, directly influencing the quality and reliability of our products. This meticulous attention to detail ensures that we meet and exceed industry standards and customer expectations.
"At CDT, we like to keep a clean shop. To do this job well, you have to be on your feet a lot and always stay moving, stay motivated. It requires attention-to-detail and focus," says Boston Stopher, Cleaning Tech at CDT. Hear more from Boston in this video:
Enhancing Efficiency and Employee Morale
A clean and well-maintained environment not only extends the life of our equipment and enhances the quality of our products and service, but it also boosts overall efficiency and morale. Workers are able to perform their tasks more effectively in an orderly setting. Furthermore, regular maintenance can improve the performance of machinery, potentially increasing output and reducing energy consumption. A clean and well-organized workplace also boosts employee satisfaction and pride in their work environment. With tidiness comes increased productivity and a stronger sense of team overall.
Cleaning: A Pathway to Growth
Our cleaning department is made up of 8 to 10 dedicated individuals who manage the cleanliness of our soon-to-be 200,000 sq. ft. manufacturing space between our 1st and 3rd production shifts. Key responsibilities include:
Sweeping and mopping floors
Wiping down equipment
Disposing of trash and metal shavings
Many team members start their careers in this department right out of high school, gaining valuable insights into the workings of different departments and shaping their future career paths within the company. For those interested in exploring opportunities as a cleaning technician, more information is available on our careers page.
Maintenance: Proactive Problem Solvers
Our maintenance department, though small, is mighty, comprising just 4 individuals with 68 years of combined experience. They are responsible for maintaining more than 500 plating tanks, 60 CNC machines, plus numerous other pieces of equipment small and large. The efficiency of our processes, reliability of our products, and comfort and safety of our facilities hinge on the efforts of this team. As Maintenance Specialists, these professionals play a pivotal role in our seamless operations. Their tasks include:
Routine maintenance
Basic and minor repairs
Changing filters, coolant, and fluids
Some fabrication work
Collaboration with engineering and manufacturing teams on projects
This dynamic team is committed to upholding our high-quality and safety standards, keeping our state-of-the-art equipment in top-notch condition, and contributing to the overall growth of Continental Diamond Tool. Find information about our Maintenance Specialist role and other positions at CDT here.
Conclusion
At Continental Diamond Tool, we understand that our achievements are not solely the result of the sophisticated equipment we use or the exceptional products we create; they are also a testament to the dedication and hard work of various departments that frequently go unrecognized. Our cleaning and maintenance crews are vital to our operation, and their contributions are valued as an integral part of our success. By supporting their efforts, we reinforce the foundation of our company’s strength and ensure that we continue to lead in the industry with integrity and excellence.
How to Dress a Vitrified CBN Grinding Wheel with a Diamond Rotary Dresser
In episode 5 of The Grinding Chronicles, CDT Product Manager Troy Giacherio shares top techniques for dressing Vitrified CBN grinding wheels using Diamond Rotary Dressers. Learn how to use key parameters such as velocity ratio and overlap ratio to enhance dressing and truing operations in precision grinding.
If you work in manufacturing, particularly in the specialized area of precision grinding, it cannot be overstated the importance of wheel dressing to maintain operational efficiency and product quality. In this comprehensive guide, we will look at the best techniques for traverse dressing a vitrified cubic boron nitride (CBN) wheel using Rotary Diamond Dressers. In Episode 5 of The Grinding Chronicles, CDT Product Manager Troy Giacherio details the specific parameters and most important factors necessary for achieving peak performance in dressing and truing operations. Watch Troy’s video or read on to learn more.
The Grinding Chronicles - Episode 5
Best Techniques for Success When Dressing a Grinding Wheel
Before plunging into the specifics of dressing a Vitrified CBN wheel, it's imperative to understand the dichotomy between two fundamental processes: truing and dressing. Truing involves sculpting the shape or profile of the grinding wheel, while dressing focuses on sharpening the wheel and removing accumulated debris. While diamond rotary dressers serve both functions, understanding this distinction facilitates the implementation of effective dressing strategies.
Essential Parameters for Dressing Success
There are four key parameters to measure for optimizing the dressing of a grinding wheel:
Velocity Ratio At the heart of dressing lies the velocity ratio, calculated by dividing the velocity of the diamond roll by the velocity of the grinding wheel. This parameter holds significant importance in dressing operations. For Vitrified CBN wheels, the recommended velocity ratio stands at 0.8. Maintaining this ratio ensures that the diamond roll adeptly removes the bond material, laying bare fresh abrasives for optimal grinding performance.
Overlap Ratio The overlap ratio describes the velocity at which the diamond dresser traverses the wheel's face to sculpt its profile and hone its edge. For Vitrified Bond CBN wheels, an overlap ratio ranging between 2 to 4 is ideal. Sustaining a steady pace ensures a seamless traversal across the grinding wheel. It is important to prevent the dresser from dwelling in any single spot to guarantee uniform dressing proficiency.
Depth of Dress The depth of dress measures the extent to which the diamond roll plunges into the grinding wheel, thereby dictating the volume of material extracted per pass. When it comes to Vitrified CBN wheels, we recommend a precise depth of dress set at 0.0002 inches per pass. Adherence to this specification not only optimizes grinding efficiency and minimizes downtime, particularly in high-volume production environments, but also preserves the longevity of the grinding wheel, yielding an optimized return on investment.
Dress Interval The dress interval is defined as the frequency at which the grinding wheel needs dressing, and it is closely tied to the application at hand. Unlike their conventional abrasive counterparts, Vitrified CBN wheels do not require frequent dressing. On the contrary, it is not uncommon to grind hundreds of parts between each dressing session. However, it is important to remain vigilant. Keep an eye on the process and be prepared to adjust the dress interval if part quality diminishes.
When Should I Dress My Grinding Wheel?
Dressing frequency varies depending on several factors specific to your process. Here are two key indicators to monitor in order to assess grinding efficacy and determine when it's time to dress your grinding wheel.
Power Draw The power draw during grinding operations can be a reliable indicator for grinding wheel dressing. A drop in power draw signals that the wheel is cutting freely, with utmost efficiency, while an uptick in power suggests a looming need for dressing. Neglecting timely dressing can lead to issues such as burn or unwanted variations in surface finish. That’s why it is important to keep a close eye on power draw dynamics to prevent such issues.
Surface Finish The surface finish of machined parts relies heavily on consistently high levels of grinding performance. A well dressed wheel produces exceptional surface finishes characterized by minimal variations and unyielding consistency in part quality and dimensional accuracy. Therefore, regular dressing sessions conducted with meticulous technique are essential for maintaining superb parts quality and excellence.
Troubleshooting and Optimization
If you are still experiencing issues such as finish patterns or burn despite adhering to prescribed dressing parameters, it may be time to call in the assistance of an expert. Companies like Continental Diamond Tool have application engineers who are trained to analyze grinding processes, pinpoint underlying issues, and facilitate optimization for enhanced performance. Armed with a portable grinding lab, these experts bring their expertise on-site to meticulously evaluate coolant delivery systems, fine-tune machine settings, and traverse a gamut of other variables to resolve persistent challenges. With their help, you can galvanize productivity to unprecedented heights. If you would like help with your wheel dressing or grinding process, don't hesitate to reach out to our engineering team at TheGrindingChronicles@CDTUSA.net.
Mastering Wheel Dressing
Proper dressing of a Vitrified CBN grinding wheel with a Diamond Rotary Dresser is the key to optimal grinding performance and part quality. By incorporating the parameters and techniques we’ve outlined in this article, manufacturers can achieve reductions in downtime, extension of wheel life, and unwavering consistency in high quality results.
Additionally, by closely watching power draw and surface finish, you will know when it is time to dress before problems get out of hand. With consistent dressing, and seeking expert help when needed, companies can overcome grinding challenges and greatly improve productivity.
Whether transitioning from conventional abrasives to CBN or seeking to refine existing grinding processes, mastering proper dressing techniques with Diamond Rotary Dressers holds the key to consistent and dependable success. Check out more grinding related topics in other episodes of The Grinding Chronicles from Continental Diamond Tool.
Continental Diamond Tool Enters Strategic Partnership with Krebs & Riedel
Continental Diamond Tool Corporation partners with Krebs & Riedel, becoming the exclusive source for their abrasive products in North America. Learn more about the collaboration in this article.
New Haven, Indiana – April 30, 2024 – Continental Diamond Tool Corporation (CDT) proudly announces its partnership with Krebs & Riedel, a global leader in the abrasives industry. This collaboration positions CDT as the exclusive North American source for Krebs & Riedel abrasive products within the USA, Canada, and Mexico.
Nick Viggiano, President of Continental Diamond Tool (left), and Florian Riedel, Managing Director of Krebs & Riedel.
Erik Van Meter, Senior Product Manager of Conventional Abrasives at Continental Diamond Tool and Krebs & Riedel’s official representative, expresses enthusiasm about the new partnership, stating, "We are thrilled about the high-quality products Krebs & Riedel will bring to the table. They are a well-respected name in conventional grinding wheels and have products for many industrial grinding markets which include automotive, aerospace, gear and medical."
The collaboration between CDT and Krebs & Riedel signifies a partnership deeply rooted in a shared commitment to excellence. For more than half a century, Continental Diamond Tool Corporation has consistently delivered technically superior precision grinding products across a variety of industries. As a thriving second-generation family business, CDT’s commitment to innovation and quality is reflected in its state-of-the-art North American manufacturing facility, which is undergoing a sizable expansion to cater to new product development and meet diverse customer needs. With this and a growing subsidiary in the United Kingdom, it has solidified its status as a premier worldwide manufacturer of custom superabrasive grinding wheels and diamond dressing tools.
Similarly, Krebs & Riedel is a family-owned enterprise headquartered in Bad Karlshafen, Germany, since 1885. It has a proud century-long legacy in providing quality abrasive products globally. With over 30 distributors and subsidiaries, K&R's dedication to customer satisfaction aligns seamlessly with CDT's founding principles. This partnership promises cutting-edge solutions and unwavering commitment to superior products and customer service in the abrasive products landscape. In this strategic move, CDT and Krebs & Riedel are poised to tackle the most critical tooling requirements of a growing market of customers.
“This partnership marks an exciting chapter for Continental Diamond Tool Corporation as we join forces with Krebs & Riedel to expand our product offerings in North America,” said Nick Viggiano, President of CDT. “We are proud to align with Krebs & Riedel's esteemed reputation and look forward to delivering exceptional abrasive products and unparalleled service to our customers across the continent and beyond.”
“With CDT we have found the partner who complements our high-performance products with superior service. From the first meeting we felt the same level of professionality and passion for grinding. I am convinced that our customers in North America will feel the same,” said Florian Riedel, Managing Director of Krebs & Riedel.
For more information about Continental Diamond Tool Corporation and its comprehensive range of precision grinding products, including those from Krebs & Riedel, please visit www.cdtusa.net/products.
Continental Diamond Tool Corporate Office in New Haven, Indiana, USA
About Continental Diamond Tool Corporation:
Established in 1973, Continental Diamond Tool Corporation (CDT) is a premier manufacturer of precision tooling solutions for a variety of global industries. With a legacy of technical expertise and innovation, CDT is renowned for its custom superabrasive grinding wheels and diamond dressing tools. Headquartered in New Haven, Indiana, CDT operates from a state-of-the-art 200,000 sq. ft. manufacturing facility dedicated to delivering high-quality products and exceptional customer service.
Krebs & Riedel Head Office in Bad Karlshafen, Germany
About Krebs & Riedel:
Family owned since its start in 1885, Krebs & Riedel (K&R) has been a prominent global player in the abrasive products industry. With a vast network of over 30 distributors, subsidiaries, sales companies, and representatives worldwide, Krebs & Riedel is renowned for its quality abrasive products and commitment to customer satisfaction.
CDT Ltd. Marks Milestone with Employee Event
CDT Ltd celebrates 40 years of innovation and excellence in the diamond dresser manufacturing industry, thanking dedicated employees with a special event featuring local pizza van, Pizza Llan.
CDT Ltd, formerly known as Consort Precision Diamond, is excited to mark its 40th anniversary—a remarkable milestone in the company's history. Since 1984, CDT Ltd has been at the forefront of manufacturing rotary diamond dressers, playing a crucial role in industries like aerospace and automotive. This journey of four decades has been driven by innovation, precision, and an unwavering commitment to excellence.
As we celebrate this significant anniversary, we acknowledge that our success wouldn't have been possible without our dedicated employees. To show our appreciation, we've invited Pizza Llan, a local pizza van, to join us at our premises. It's a small token of our gratitude to the team whose hard work and dedication have made our achievements possible. Here's to 40 years of success—and many more to come!
Members of the leadership team at Continental DIamond Tool Ltd. present employees with a 40th anniversary cake. (From left) General Manager Troy Giacherio, Finance Manager Michaela Lawton, Production Manager Justin Hughes, and Managing Director Jeff Wirth.
Managing Director Jeff Wirth visits from CDT’s U.S. headquarters for the occasion.
Jeff expresses gratitude to employees for their commitment to the company, emphasizing a vision for the future and its continued success.
Recent retirees came back to celebrate the company’s 40th anniversary, marking four decades of legacy and achievement.
Employees enjoy Pizza Llan, a local pizza van, as part of the festivities.
Nothing says 'thank you' like a plate of pizza.
Who’s ready to dig in?
Smiles with every slice.
Former colleagues reunite, sharing memories and catching up on old times.
Celebrating 40 years of excellence: 1984-2024
CDT Ltd. Engineers Adopt Much-loved Hospice to Help Final Wishes Come True
St Kentigern, a much-loved North Wales hospice, has been adopted as a favored charity by Continental Diamond Tool Ltd. in Kinmel Bay, U.K., after staff voted to support it in honor of the facility's 40th anniversary year.
Kinmel Bay-based engineering company Continental Diamond Tool Ltd have made a £1,000 donation to St Kentigern Hospice in St Asaph and pictured are, from left, Becky McNay, Advanced Nurse Practitioner; Helen Turberville and Michaela Lawton of CDT with Alwyn Mason, corporate fund raiser at St Kentigern Hospice.
A much-loved North Wales hospice has been adopted as a favored charity by Continental Diamond Tool Ltd (CDT) after staff voted overwhelmingly to support it.
St Kentigern Hospice, which serves Denbighshire, eastern Conwy and western Flintshire, was chosen by CDT because of the “wonderful care” it has shown for relatives of team members, including both parents of engraver and dispatch officer Helen Turberville.
The company, which supplies sophisticated parts for production machinery for Rolls-Royce and other aerospace companies, has made its first donation to the charity with Helen handing over a cheque for £1,000 at the hospice in St Asaph. CDT employees encourage others to join them in supporting this worthwhile cause. You can make a donation here.
Their donation was made to mark the 40th anniversary of this CDT location – one of only two of its kind in the UK that specializes in precision diamond grinding products - which employs 40 skilled staff at its factory on the Tir Llwyd Industrial Estate in Kinmel Bay.
Helen said: “My parents, Maureen and Ted Felton, from Kinmel Bay, were both here and the care and support the hospice gave was a great comfort to them and to us as a family.
“My mum used to come to the day centre here and made many things I still have at home including a tie-dyed silk scarf.
“Then she was a resident here and was struggling with her mobility and they helped her a lot before she passed away here.
“My dad was in hospital in Liverpool and I asked for him to be moved to Ysbyty Glan Clwyd and they said he only had a matter of days so I requested that he come to St Kentigernand the staff here managed to get him in.
“He knew we were trying to get him here because on one of his good days we managed to tell him and it meant a lot to all of us as a family.
“St Kentigern is a wonderful place and my mum made a lot of friends here. It’s very comforting here and I’m delighted that CDT are supporting it.”
The hospice has been extended to 12 beds from eight but it also provides extensive day care and respite services as well as wide range of therapies and over the past 12 months more than 600 people from across the area have used its services.
They cost £3.6 million a year with three-quarters of that raised by St Kentigern team, of fundraisers who are currently working on one of the year’s major events, the Twilight Trek which takes place on Saturday, June 29.
They also provide a Wish Ambulance which aims to make the final wishes of its residents come true and they have included a lady in her 30s who wanted to spend a final couple of hours in her own home.
Another patient wanted to see a fireworks display for the last time and the Royal National Lifeboat Institute came in to stage a show
CDT are now partnering with St Kentigern to support the hospice and make those dreams come true. You can extend your support, too, by making a donation here.
CDT Finance Manager Michaela Lawton said: “It is a fantastic cause, it’s local and after a discussion with our employees about which charities to support St Kentigern was put forward and it was a no-brainer really.
“I came to visit the hospice and was so impressed by the work they are doing and by the fantastic range of services and activities they provide, not only to their patients but to their families at the most difficult time in their lives.
“This is the 40th anniversary of the company and we want to set up a long-term partnership with St Kentigern to mark that and we aim to support them with regular donations in the future.”
Advanced Nurse Practitioner Becky McNay, from Wrexham, joined St Kentigern four years ago and she said: “It’s been amazing. I’ve really loved it. It’s such a rewarding place to work.
“You can’t just come here to a place like this because it’s a job. You have to really want to do it and it’s really great to build relationships with the patients and with their families because they play such an important role.
“I had always wanted to do palliative care from when I was 16 when my nan came to live with us and she was terminally ill.
“Here’s it’s not just about the process of dying. There’s much more to it than that with respite care and outpatients services and the complementary therapies we offer like massages and a wellbeing programme which covers a different topic each week.
“There’s also now advanced care planning because if someone is diagnosed with a life-limiting illness it’s important to have advice on wills and legal matters and of course it is very rewarding if you can be there for someone emotionally as well.
“I really enjoy the one to one care and the privilege of having time to second with patients and their families – you just wouldn’t get the same amount of time in an acute ward of a hospital.”
The precision manufacturing company was founded in 1984 as Consort Precision Diamond and in 2018 was bought and rebranded by Continental Diamond Tool, based in New Haven, Indiana.
It makes a range of highly specialised diamond dressers and grinding tools for advanced manufacturing industries, including the aerospace, automotive, medical and semi-conductor sectors.
More than 60 per cent of the company’s products are exported to 30 countries, with sales growing particularly strongly across Europe and Asia, as well as North America.
Meet The Team Behind CDT's High Performance Resin Bond Products
Meet the skilled team driving innovation in precision grinding wheel manufacturing of CDT Resin Bond products. For over four decades, these professionals have crafted custom solutions that guarantee precision and reliability.
Behind every exceptional product is a dedicated team committed to excellence. At CDT, this is exemplified by our Resin Bond department, where talented individuals collaborate to create high-performance Resin Bond CBN and Diamond tools tailored to meet the unique needs of customers. This video and article tell the story of our remarkable team and their dedication to crafting superior products.
The Ingredients for Success in manufacturing Custom RESIN BOND Grinding Wheels
An Experienced Team
Since its launch in 1978, the Resin Bond product line has been a cornerstone of CDT's success, constituting a sizable market and just over 18% of CDT’s outgoing sales in 2023. With 40 years of experience in the industry, Resin Bond Product Line Manager Jim Fell proudly states, "We can tailor a product to anything that the customer needs, any type of specification that they need, and any type of application."
Having worked at Continental Diamond Tool for more than two decades, Resin Bond Pressing Lead Nick Rorick embodies the spirit of craftsmanship and dedication that has put CDT Resin Bond CBN and Diamond Grinding Wheels on the map. In his video interview, Rorick emphasizes, "What sets us apart is the team we have behind our products here at CDT. They put their heart into every tool they make."
Customer Focus
At CDT, customer satisfaction is our top priority. Jackson Birkenbeul, a Resin Bond Design Engineer, emphasizes the importance of addressing customer needs promptly and precisely. In the video, he remarks, "Our focus is not just on manufacturing products but on solving customer challenges." This dedication to understanding and meeting customer requirements underscores CDT's commitment to excellence and service.
Innovative Process
Using a combination of phenolic resin and CBN or Diamond superabrasive, our Resin Bond engineering and production team can design and manufacture thousands of product combinations. The production process begins with formulating a recipe that is tailored to the customer's specific application. A unique blend of bond material, abrasive, and fillers are purposefully selected to optimize grinding performance.
The custom formulation undergoes meticulous mixing in specialized tumblers before being poured and packed into mold cavities. Then, molds undergo hot pressing, where precise control over temperature and pressure ensures the creation of grinding wheels with the desired density. Finally, the wheels proceed to finishing, where they are machined and ground to achieve the intended size and geometry, allowing our Resin Bond products to be tailored to any specification required.
A Multitude of Applications
"Anything that can be cut, ground, polished, or sharpened, we can do," says Kyle Hockemeyer, CDT Pressing Tech. "In precision grinding, the consistency and repeatability of our product is one of our main goals. We strive to get a repeatable process that can be done on a regular basis to have quality, consistency, and delivery in a timely fashion."
Inside the Resin Bond department, 20+ employees work hard to make sure every order meets CDT's high standards for quality and performance. With the addition of a third shift in 2021 and an expansion in 2024 to accommodate new technology and machinery, this product line continues to grow in step with customer demand.
Putting it all together
The Resin Bond team at CDT epitomizes craftsmanship, innovation, and dedication. Their relentless pursuit of excellence and deep-seated commitment to customer satisfaction set them apart in the competitive landscape of precision grinding wheel manufacturing. As our team continues to innovate and push boundaries, customers can trust that CDT's Resin Bond products represent the pinnacle of quality, performance, and reliability.
Conventional Abrasives vs. Superabrasives
In Episode 4 of The Grinding Chronicles learn how the properties of common abrasives impact wheel life and cutting efficiency. Avoid pitfalls with industry expert Jon VanSant.
In Episode 4 of The Grinding Chronicles, Continental Diamond Tool Engineering Consultant Jon VanSant investigates the history of common abrasive materials and their key differentiating characteristics that impact wheel life, cutting performance, and efficiency. Using the wrong abrasive for your application can significantly increase your cost per part. Watch Jon’s video or read the article below to learn the differences between conventional abrasives and superabrasives.
The Grinding Chronicles - Episode 4
Understanding Abrasive Evolution
In the early 1800s, precision grinding relied on naturally occurring abrasives like emery. Fast forward to the late 19th century, and we witnessed pivotal developments with the advent of "Carborundum" or silicon-carbide by Dr. Edward Acheson in 1891, followed by the patenting of 'Alundum' or aluminum oxide by Aldus Higgins in 1904. The landscape changed once again with the introduction of synthetic diamond in 1954 and cubic boron nitride (cBN) in 1957, marking the emergence of superabrasives. Although superabrasives were first synthesized in the 1950’s, it took two decades before commercial products became available.
Distinguishing Characteristics
To understand the difference between conventional abrasives and superabrasives, let’s examine three key characteristics: hardness, thermal conductivity, and friability.
Hardness: An important consideration in abrasive selection, superabrasives like cBN and Diamond demonstrate superior hardness compared to Aluminum Oxide and Silicon Carbide. This is part of what makes superabrasives super, and makes them particularly efficient when grinding extremely hard materials.
Thermal Conductivity: Enhanced thermal conductivity facilitates efficient heat transfer during grinding operations, ensuring minimal damage to the workpiece. This is critical where surface finish is concerned.
Friability: Friability reflects the fracture or impact toughness of an abrasive and underscores another crucial aspect. Analysis reveal a substantial disparity between conventional and superabrasives, with the latter exhibiting remarkable compression fracture strength. When comparing the compression fracture strength of diamond and aluminum oxide at a particle size of 400 microns, there is a 10:1 difference between the conventional abrasive and the superabrasive.
Performance Metrics
Moving beyond physical attributes, an examination of performance metrics such as cut, wear, and dressing efficiency further demonstrates superabrasives prowess.
Cutting Efficiency: Superabrasives like Diamond and cBN require less power and force for cutting operations, ensuring efficient material removal.
Wear Resistance: Superabrasives demonstrate significantly higher wear resistance, leading to prolonged wheel life and reduced downtime when compared to conventional abrasives.
Dressing Efficiency: Superabrasives also excel when considering downtime for dressing since they maintain dressing efficiency over extended periods. In some cases, we have seen up to 20 times the parts per dress. With less frequent dressing comes more consistent performance. Plus, you’re only taking off a tenth of the material in dressing, so your wheel lasts much longer.
Cost Considerations
Superabrasives, with their many advantages, do come with a substantial up-front investment. Even so, many companies see sustainable returns.
Long-Term Value: Superabrasives offer enhanced productivity and cost-effectiveness that often results in lower cost per part over time.
Application Considerations: Recognizing that not every application warrants a superabrasive grinding wheel, factors such as machine tools, fluid compatibility, and work volume must be considered. Superabrasives are most cost effective in high volume, extremely demanding applications.
Expert Guidance
Thank you for joining us on this exploration of grinding wheel abrasives. If you would like help deciding which abrasive would work best to optimize your grinding process, don't hesitate to reach out to our engineering team at TheGrindingChronicles@CDTUSA.net. Until next time, check out additional insights and discoveries on other episodes of The Grinding Chronicles.
Streamlined Finishing and Shipping of Precision Grinding Wheels
Continental Diamond Tool ensures each grinding wheel meets exacting standards, emphasizing precision, quality, and customer satisfaction. Learn more about our meticulous processes in this article.
From aerospace components to medical devices, industries rely on a reliable supply of finely tuned machinery and tooling to achieve optimal, cost effective results. At the heart of many precision machining operations lie custom CBN and Diamond grinding wheels, meticulously crafted to exact specifications. However, the journey from concept to completion involves more than just production. It ends with two critical stages — finishing and shipping —which ensure that these essential tools reach their destinations in prime condition. This article looks at the intricacies of these processes.
Precision in Finishing
Finishing is the bridge between production and the end-user, where the grinding wheels undergo meticulous inspection and refinement. Each custom wheel is subjected to rigorous quality control measures at this final stage, along with incremental checks earlier in the production process, to ensure it meets the stringent standards set forth by the industry and the customer.
Balancing & Surface Enhancement
Surface finish plays a pivotal role in the performance of grinding wheels. Through a combination of advanced and timeless techniques in polishing, the surface is refined to minimize friction and maximize efficiency during operation. Whatever the particular grit size, bond type, or configuration, this step ensures that the wheel’s customization aligns perfectly with its intended use.
It is at this stage that our Finishing Department balances the grinding wheel, making minor modifications as needed. Balancing ensures that our tools produce high quality parts for the customer with reduced scrap, less vibration, and less wear on the spindle and machine.
"The key to working in the Finishing Department is to be a hard worker, detail-oriented, and someone who takes pride in their work," says Tony Police, CDT Finishing Tech. “In this department, we clean and polish tools to get them ready for the quality department to check and ship.”
Inspection and Quality Assurance
At CDT, every order ends with a comprehensive inspection of each grinding wheel. Highly trained technicians meticulously examine every aspect, from dimensional accuracy to surface finish, verifying that it aligns precisely with the specifications dictated by the engineer. Any deviations are promptly addressed to maintain the highest levels of precision for diamond grinding wheels.
“In the quality department, we use advanced technology to compare the tools to the print, make sure they are to spec, and exactly what the application requires,” says CDT Quality Tech Leslie Gurzynski. “At CDT, we regularly invest in new processes to ensure the best results for our customers.”
Customization and Labeling
At this final stage, the grinding wheel is either white labeled or engraved with the CDT logo. Additional labeling with essential information such as part numbers and usage instructions facilitates seamless integration into the customer’s workflow.
Efficient Shipping Solutions
With the finishing touches complete, the focus shifts to the final stage of the process – shipping. Timely and secure delivery is crucial to minimize downtime and keep operations running smoothly. Leveraging efficient shipping solutions ensures that custom precision grinding wheels reach their destination promptly and intact.
Packaging
Proper packaging is crucial to safeguarding the integrity of the grinding wheel during transit. Specialized packaging materials and techniques are employed to minimize vibration and impact, reducing the risk of damage en route. Each wheel is securely encased to withstand the rigors of transportation, providing peace of mind to both the manufacturer and the end-user. Product safety information is accessible through a QR code printed on the packaging. Dressing sticks for wheel maintenance are also routinely included when appropriate for the convenience of our customers.
Logistics Optimization
Efficient logistics management is essential to streamline the shipping process. Leveraging advanced tracking systems and strategic partnerships with reliable carriers, Continental Diamond Tool can ensure timely delivery while optimizing costs. Each month, CDT ships out more than 1,600 boxes of custom products. From domestic shipments to international exports, meticulous planning and coordination ensure that custom grinding wheels reach global destinations efficiently.
"Maximizing quality and efficiency for our customers is our primary goal," says Brad Miller, Shipping Manager at CDT. "With our move into the new building six years ago, and with each expansion, we've created more space to work and a better flow of tooling through final inspection and out the shipping doors."
Customer Support
A commitment to customer satisfaction extends through production, shipping, and beyond. Dedicated technical support teams stand ready to address any inquiries or concerns throughout the shipping process. From tracking updates to post-delivery assistance, proactive communication fosters trust and reinforces our dedication to excellence.
“If a customer faces challenges installing or adjusting the settings for a new grinding wheel, that's where our expertise comes into play,” says Blu Conrad, CDT Application Engineer. “Our application engineers don't just offer remote support; we go the extra mile by personally visiting customers' locations when needed to fine-tune their operations onsite, ensuring optimal performance and satisfaction.”
In conclusion, the finishing and shipping of custom precision grinding wheels are integral components of the manufacturing process. By upholding uncompromising standards of quality and efficiency, Continental Diamond Tool can ensure that these essential tools meet the exacting demands of modern industry. From concept to the production floor, precision drives innovation and excellence every step of the way.
To request a quote or place an order for a custom precision grinding product, please call 800-443-6629 or submit your project specifications using our website’s contact form.
Students Build Careers in Engineering with CDT Apprenticeships
Continental Diamond Tool Ltd. is shaping engineering careers for Kinmel Bay-area students like Rhys Butler and Corey Jones. Follow Rhys's eight-week work experience apprenticeship alongside Corey at CDT's precision manufacturing facility in North Wales.
(From left to right) Rhys Butler, left, and Corey Jones who are building careers in engineering with the apprenticeship programme at Continental Diamond Tool Ltd. in collaboration with Coleg Llandrillo in North Wales.
An 18-year-old sixth form student is getting a taste of the world of precision engineering after being inspired by the success of a high flying company.
Rhys Butler, a pupil at Ysgol Glan Clwyd in St Asaph, is now on an eight-week work experience programme after writing to Continental Diamond Tool, on the Tir Llwyd Industrial Estate in Kinmel Bay, which is withing walking distance of his home.
According to Rhys, he was prompted to get in touch when he read a news story about the firm which supplies sophisticated parts for production machinery for Rolls-Royce and other aerospace companies in the UK.
Continental Diamond Tool Ltd. (CDT), which employs 40 skilled staff and is celebrating its 40th anniversary this year, is one of only two companies of its kind in the UK.
It makes a range of highly specialised diamond tools for advanced manufacturing industries, including the aerospace, automotive, medical and semi-conductor sectors.
Rhys said: “I saw the story about the company being under new American ownership and I was looking for work experience for my CV so I emailed in an application and they came back to me straight away.
“They’ve given an eight-week programme so I go in one day a week and I’m going through the different processes they do and they show me and explain how they work.
“One Wednesday I was actually working on putting the diamonds into the tooling. It’s been a brilliant opportunity.
“I’ve always been interested in cars and how machines work and I’m doing engineering in sixth form and go to the Llandrillo College campus in Rhyl every Thursday which is really helpful.”
Rhys often works alongside Corey Jones, 19, also from Kinmel Bay, now in his second year as an apprentice who also took the work experience route to a place with CDT.
He said: “I did my A-levels at Eirias High School in Colwyn Bay and then did Level Three Engineering at Coleg Llandrillo’s site at Rhyl with work experience here and they offered me an apprenticeship.
“They wanted me to get used to what’s involved so I worked here through my summer holidays and started my apprenticeship in September in Level Four Engineering.
“I knew there was a lot of maths in engineering and I’d always enjoyed that and I like to challenge myself by learning about the different machines so I’m really enjoying it.
“I had tried a few places for work experience and Coleg Llandrillo suggested here and it’s been brilliant.
“The people here are really great and very knowledgeable with lots of experience you can learn from – I work with someone who has experience on every machine and he’s a big help.
“We’re working for businesses like Rolls-Royce which is fantastic so I want to do the best I can and really build a career here.”
Michaela Lawton, CDT Finance Manager, said: “We have been running an apprenticeship scheme here for a long time and historically it’s been successful and two of our apprentices who moved on after a few years have actually come back to us.
“We have a very good relationship with Coleg Llandrillo and it really helps that they have a campus at Rhyl with a strong and well-equipped engineering department.
“What we do here is so unique and so niche that we expect our apprentices to learn the core skills in college to give them the platform to build on with the highly specialised work we do here.”
CDT has been boosted by a £1.6million investment by their American owners and has opened a second production unit on the Tir Llwyd Estate to house its new electro-plating operation which has received support from Welsh Government.
More than 60 per cent of the company’s products are exported to 30 countries, with sales growing particularly strongly across Europe and Asia, as well as North America.
The company, which celebrates its 40th anniversary this year, was founded originally as Consort Precision Diamond and in 2018 was bought and rebranded by Continental Diamond Tool Corporation, based in New Haven, Indiana.
Related Links:
https://www.gllm.ac.uk/news/rhys-and-corey-shine-with-diamond-tool-firm
Images captured by Mandy Jones Photography.
Coolant Application Techniques to Reduce Wheel Wear and Burn in Grinding
Discover essential coolant application strategies to enhance grinding performance, reduce wheel wear, and prevent burn in this article with video.
In Episode 3 of The Grinding Chronicles, Continental Diamond Tool Application Engineer Blu Conrad explains some essential aspects of coolant application that can impact your grinding performance. By having the correct placement of coolant lines and optimizing your coolant setup, you can significantly reduce cycle times, minimize wheel wear, and prevent burning during the grinding process. Watch Blu’s video or read the article below to learn how.
The Grinding Chronicles - Episode 3
Coolant Application and Its Impact on Grinding Performance
Most grinding operators know that reducing heat generation in grinding is crucial for avoiding excessive wheel wear and burn. However, you might not be aware of the various strategies available for achieving this goal. In this article, we will explore how coolant application can mitigate these factors. It starts with four key considerations in cooling: Velocity, Flow, Line Placement, and Temperature.
Velocity Matters
One critical factor in effective coolant application is ensuring that the coolant is spraying at the correct velocity, typically ranging between 70% and 100% of your grinding wheel speed. This velocity is essential because of a force called the air barrier.
As a grinding wheel rotates, it creates an air barrier around its perimeter. To penetrate this barrier and deliver coolant to the grinding zone, the coolant stream must travel at the appropriate velocity. If it is too slow, the grinding wheel can blow the coolant away. Conversely, if the velocity is too high, the coolant may make contact with the grinding wheel and bounce off, rendering it ineffective in reaching the desired area.
Balancing Flow Rate
In addition to velocity, the amount of coolant flowing from the coolant line, known as the Flow Rate, is equally crucial. Flow rate and velocity are interrelated, and their optimization is a balancing act.
In grinding, you often have a choice between low-pressure, high-flow setups, or high-pressure, low-flow configurations. If the flow rate is too low, there won't be enough coolant to adequately cool the grinding process, potentially leading to overheating and damage. Conversely, if the flow rate is excessively high, you will be wasting coolant, resulting in inefficiency and increased operational costs.
Utilizing Nozzles for Optimization
A practical approach to achieving the ideal Velocity and Flow is by using nozzles. While standard jet nozzles are suitable for many grinding applications, different grinding processes may require wheels with distinct shapes, such as flat or radial profiles.
In such cases, it is often more effective to employ nozzles and coolant lines that have been specifically engineered, designed, and tuned to accommodate these unique wheel types. This ensures that the coolant is delivered with the appropriate velocity, flow, and, equally importantly, in the correct position.
Positioning and Direction
The position and direction of the coolant are critical factors in coolant application efficiency. Ideally, you want your coolant jet to spray just before the point of contact, where the grinding wheel and workpiece meet. Additionally, the coolant should flow in the same direction as the rotation of the grinding wheel.
If the coolant stream strikes too far above or behind the point of grinding contact, it will fail to effectively enter the grinding zone, missing the opportunity to cool the process where it is needed most.
Achieving Efficiency in Your Grinding Process
Optimizing coolant applications is a fundamental aspect of enhancing the efficiency and performance of your grinding processes. By carefully considering Velocity, Flow, Line Placement, and Temperature, you can significantly improve cycle times, reduce wheel wear, and prevent burning during grinding operations.
At Continental Diamond Tool, we understand the importance of precision coolant applications and many other factors in achieving superior results. Whether you require standard jet nozzles or specialized coolant solutions tailored to your specific needs, we have the expertise and technology to help you isolate those parameters that are holding back your grinding performance.
To explore our range of grinding solutions and learn more about how we can assist you in achieving exceptional cycle times and wheel life, email us at TheGrindingChronicles@cdtusa.net. Our engineers welcome the opportunity to meet your most challenging tooling requirements.
Part Masking of Plated Grinding Wheels
Learn about the process of part masking in the production of plated diamond and CBN grinding wheels. This technique ensures precision and quality in precision grinding across industries like manufacturing, automotive, and aerospace. Find out the specialized skills that are required to excel in this type of work.
Part masking is a crucial technique employed in the plating process for CBN (Cubic Boron Nitride) and diamond grinding wheels. This method involves selectively covering specific areas of a metal substrate before plating to protect them from the plating solution. Part masking plays a significant role in ensuring the precision, quality, and functionality of grinding wheels used in various industries, from manufacturing to automotive and aerospace. In this article, we will delve into what part masking is, how it is done, why it is essential in the plating process, and what it takes to excel at this intricate skill.
What is Part Masking?
Part masking is the process of shielding specific areas or features of a substrate to prevent them from being plated during the plating process. It is achieved by applying a masking material to the surface of the substrate in a controlled and precise manner. The masking material can be in the form of tapes, paints, or other coatings that can resist the heat and duration of time in the plating process.
How is Part Masking Done?
The process of part masking involves several steps:
Surface Preparation
Before masking, the metal substrate is thoroughly cleaned and prepared. This step ensures that the surface is free from contaminants, oils, coolants, machining residues and oxides, which can interfere with the adhesion of the masking material.
Masking Material Selection
The choice of masking material depends on factors such as the type of substrate being plated, the plating process used, and the specific areas that need protection. Common masking materials include specialized masking tapes, latex, and resin-based coatings. Continental Diamond Tool employs all of these methods in its process.
Application of Masking Material
The masking material is applied precisely to cover the areas that should not be plated. This can be done manually or using brushes, stencils, scribes or automated equipment. For more complex patterns, careful attention is given to ensure that there are no gaps or leaks in the masking material.
Cure or Drying
Depending on the type of masking material used, it may need to be cured or allowed to dry thoroughly. This step generally takes a specific amount of time and ensures that the masking material remains intact and impermeable during the plating process.
Plating
Once the wheel has been masked and cured, the substrate is immersed in the plating bath, where the exposed areas are plated with the desired abrasive material, such as diamond or CBN particles. The masked areas remain untouched, preserving their original characteristics.
Mask Removal
After the plating process is complete, the masking material is carefully removed, revealing the plated surface underneath. This can be done through various methods, such as peeling off tapes or dissolving the masking material with solvents.
Why is Part Masking Essential?
Part masking serves several crucial purposes in the plating process for diamond and CBN grinding wheels:
Precision and Quality
Part masking ensures that the plating is applied precisely to the intended areas, maintaining the tight tolerances, quality, and accuracy essential to precision grinding.
Functionality and Performance
By protecting specific features of the grinding wheel, such as arbor holes, flanges or threaded holes, from plating, part masking helps maintain their functionality and performance, ensuring they are dimensionally fit and operate correctly.
Cost Efficiency
Masking reduces the amount of plating material used, minimizing waste and lowering production costs. It also prevents the need for costly post-plating rework to remove unwanted plating.
Customization
Part masking, applied by hand, is customizable. This allows manufacturers to create tailored, complex products to meet specific customer requirements.
What It Takes to Be Good at Part Masking
Part masking is a specialized skill that requires attention to detail, precision, and an understanding of materials and processes. Here are some key attributes and considerations for those looking to excel in this field:
Attention to Detail
Successful metal part maskers must have a keen eye for detail. Precision is paramount in this process, as even the smallest imperfections or gaps in the masking material can lead to plating errors.
Material Knowledge
Familiarity with various masking materials and their properties is essential. Different materials may be required for specific applications, and understanding their characteristics can ensure the right choice is made.
Patience and Dexterity
The application of masking material can be a delicate and time-consuming task. Patience and manual dexterity are necessary to achieve consistent and high-quality results.
Problem-Solving Skills
Maskers may encounter challenges such as complex shapes or irregular surfaces that require creative problem-solving to ensure proper masking.
Adherence to Safety Protocols
Safety is paramount when working with masking materials and plating chemicals. Understanding and following safety protocols are crucial to prevent accidents and exposure to hazardous substances.
At CDT, our masking department has almost 50 years of combined experience in this highly specialized field. The superior quality and stellar reputation of our plated products are a testament to their expertise.
If you are passionate about precision craftsmanship and believe you have the skills and attributes required for part masking, we encourage you to consider career opportunities in this field. At Continental Diamond Tool, we value skilled professionals who can contribute to our commitment to excellence.
To explore potential positions and apply for a rewarding career in electroplating or other positions in our industry, visit our careers page.
How to Order a Custom Electroplated Grinding Wheel
At CDT, we take pride in the excellence of our masking and plating departments. Part masking is an indispensable technique in the production of plated diamond and CBN grinding wheels to ensure the delivery of the very best products. It requires a unique set of skills, including attention to detail, material knowledge, patience, and problem-solving abilities. Those who excel in this field play a vital role in providing the precision, quality, and functionality of grinding wheels used across various industries.
If you are interested in ordering a custom plated grinding wheel or have any inquiries, please don't hesitate to contact our customer service department. Our team can connect you with our experienced plating engineers to start the process today.
Advantages of Using Electroplated Diamond Grinding Wheels for Precision Grinding
Say goodbye to dressing downtime and hello to faster cycle times with electroplated grinding wheels for precision industries like aerospace, automotive, medical devices, and electronics. These wheel are even more cost-effective with our Strip and Replate Program: learn more.
With precision machining and grinding, the selection of tools plays a pivotal role in determining efficiency, profitability, and overall success. Among the many options available, electroplated diamond and CBN (cubic boron nitride) wheels rank high as indispensable assets for many manufacturers worldwide. These tools offer a unique combination of advantages that contribute significantly to superior performance and cost-effectiveness. In this article, we explore four key reasons why these tools are at the forefront of precision machining and grinding.
1. Consistent Distribution of Abrasive Particles
In precision grinding, the even distribution of abrasive particles is often critical for consistency. Electroplated diamond grinding wheels excel in this aspect, ensuring a uniform dispersion of abrasive particles across their entire surface. Unlike alternative bonding methods that may result in irregular spacing of abrasive grains, electroplated tools embed diamond particles evenly in a single layer. This uniformity translates to predictably consistent grinding or cutting performance. The same is true for electroplated cbn grinding wheels.
In practical terms, this means achieving precision and accuracy in your workpiece everytime, pass after pass. Whether working with robust metals, fragile ceramics, or intricate composites, manufacturers can place their trust in electroplated grinding tools to deliver a reliable and uniform cutting or grinding action.
2. Strong Bond Between Abrasive and Substrate
Another distinguishing factor that sets electroplated diamond tools apart is the robust bond formed between the abrasive particles and the tool's substrate. During the electroplating process, diamond grains become firmly embedded within a nickel or other metallic matrix, creating a tool of exceptional durability and resilience.
This sturdy bond ensures that the diamond particles remain securely attached to the tool's surface, even when subjected to high-speed or high-pressure operations. Consequently, these tools maintain their sharpness and cutting efficiency over an extended period, eliminating the need for dressing and maximizing time between replacements. This durability translates into significant cost savings by reducing downtime and material wastage.
3. Free Cutting Action Equates to Fast Cycle Times
Electroplated diamond tools offer a "free cutting action" that speeds up the grinding and cutting process significantly. Unlike conventional tools that may generate excess heat, clog, or wear unevenly, electroplated diamond tools efficiently remove material with minimal resistance.
This means reduced cycle times for manufacturers. Jobs that used to take longer can now be completed faster and with more precision. Whether shaping aerospace components or fine-tuning medical devices, electroplated diamond tools deliver both speed and accuracy. Fast cycle times translate to increased throughput, shorter lead times, and enhanced competitiveness in today's manufacturing landscape.
4. Maintenance and Reconditioning: The Strip and Replate Program
At Continental Diamond Tool (CDT), we go above and beyond to extend the lifespan of electroplated grinding wheels through our innovative Strip and Replate Program. This program harnesses strip technology to safely remove worn-down abrasives without compromising the wheel's core. We employ a chemical solution to delicately eliminate old abrasives, preserving the integrity of the wheel's substrate. After stripping, a new layer of abrasive material is expertly applied through electroplating.
The outcome? A rejuvenated electroplated grinding wheel that performs at its best. These reconditioned wheels undergo rebalancing to ensure optimal performance during extended runs. This program not only maximizes tool lifespan but also minimizes waste, translating into cost savings and reduced downtime.
How Electroplated Grinding Wheels Yield Long-Term Cost Savings
At CDT, our electroplated grinding wheels are engineered to endure heavy usage, consistently deliver high performance, and enjoy an extra-long wheel life compared to other wheel types. This durability translates into substantial long-term cost savings — as much as 40% in some instances. Plus, the "free cutting action" of electroplated diamond tools is a powerful ally for manufacturers seeking faster cycle times without compromising quality. These tools optimize efficiency, boost productivity, and meet the precise demands of modern machining and grinding processes.
Industries Benefiting from Electroplated Grinding Tools
A wide array of industries benefit from the unique advantages that diamond plated tools offer. Here's a glimpse into some of the key sectors where these tools play a pivotal role:
Aerospace: In the aerospace industry, precision and quality are paramount. Diamond plated tools shape and finish critical components like turbine blades, engine parts, and aircraft structural elements. They deliver the precision required to ensure the safety and reliability of aircraft.
Automotive: The automotive industry relies on diamond plated tools for tasks such as sharpening cutting tools, honing engine components, and producing high-precision parts. These tools contribute to the efficiency and durability of automotive systems.
Medical Devices: The production of intricate and high-precision medical devices, including surgical instruments and implants, relies on diamond plated tools. They enable the manufacturing of components with tight tolerances and exceptional surface finishes, crucial for medical applications.
Electronics: Precision is essential in the electronics industry, where delicate components require fine grinding and cutting. Diamond plated tools play a pivotal role in shaping semiconductors, ceramic substrates, and other electronic components with microscopic precision.
Tool and Die Making: Tool and die manufacturers use diamond plated tools to create molds, dies, and precision cutting tools. These tools provide the accuracy needed to produce intricate and high-quality components.
Stone and Glass Processing: In the construction and architectural industries, diamond plated tools are used for cutting and shaping stone, glass, and composite materials. They offer the precision and control necessary for creating custom designs and finishes.
Fiberglass and Composites: Electroplated grinding tools are indispensable for shaping and refining composite materials used in many applications. From boat hulls to automotive body parts to architectural panels, their ability to provide precise shaping and surface finishing ensures the structural integrity and aesthetics of fiberglass and composite products.
The Competitive Edge of Electroplated Grinding Technology
In conclusion, electroplated grinding wheels offer an impressive array of advantages, including consistent distribution of abrasive particles, a robust bond between abrasive and substrate, fast and free cutting action, and an innovative reconditioning option with Strip and Replate. These benefits combine to deliver long-term cost savings, which establish electroplated grinding wheels as the preferred choice for precision machining across a diverse array of industries.
To harness the advantages of electroplated diamond and cbn grinding wheels for your specific machining needs and see the cost savings, consider partnering with trusted grinding wheel manufacturers like CDT, dedicated to delivering exceptional quality and performance.
High Flying Engineering Firm Says Fond Farewell to Founder Steve
Celebrating the journey of Steve Noakes, founder of Consort Precision Diamond Company, which later became Continental Diamond Tool Limited. Hear about his retirement celebration and the company's bright future with CDT.
A specialist engineering company that keeps the world’s airlines flying will reach new heights thanks to investment from its new American owners, according to one of the firm’s founders.
Former production director Steve Noakes, 67, from Trefriw, in the Conwy Valley, was speaking at a presentation ceremony to mark his retirement from Continental Diamond Tool in Kinmel Bay which is celebrating its 40th anniversary this year.
Among his leaving gifts was a nickel plated version of the graphite mould for a diamond rotary dresser of the type used to grind the turbine blades of Rolls Royce aero engines, with the signatures of each of his 40 colleagues engraved onto it.
Steve was one of the eight people who established the niche company as Consort Precision Diamond in 1984, specialising in the manufacture of diamond-encrusted rotary dressers and grinders.
The firm – still one of only two similar companies in the UK – supplies a range of manufacturing sectors, including aerospace, automotive, medical and semi-conductors.
It’s products are used in Boeing 777 and 787 Dreamliner aircraft, as well as the Airbus range A330-A380 whose wings are made at the giant Airbus factory in Broughton.
The company was acquired and rebranded in 2018 by American outfit Continental Diamond Tool which has its headquarters in New Haven, Indiana.
Father-of-two Steve was the last man standing because all the other members of the original team had already retired.
He left “safe in the knowledge” that the company was in good hands. having seen the new management team investing £1.6 million to launch a second production line to make electro-plated grinding wheels, with record profits and sales soaring by 70 per cent.
Steve said: “I am extremely proud of what we have achieved, employing people for 40 years in skilled, well paid jobs.
“I’m also very proud that we’re now part of Continental Diamond Tool. Acquisitions can be messy affairs but this was actually a really happy process.
“They have the same mindset as a family-oriented company, looking after their employees and building a successful business with a very good future. The fit is excellent because they can invest more than we were able to as an independent company.”
He was delighted by the “perfect” gift of the inscribed nickel-plated mould which was presented by his old boss, the original managing director, Dave Morris, who came back for the emotional occasion.
He said: “Steve made a huge contribution – he’s a real diamond. In one sense this is a sad day but it’s also a good one for him because we know our legacy is safe. They’re a good bunch of people.”
There were also good wishes from CDT president, Nick Viggiano, who said: “We will always be indebted to Steve and his fellow founders for their grace, helpfulness and goodwill in managing the transition to the new ownership.
“Steve played an integral role in building a very successful company with a global reputation for excellence in a very competitive niche market. He should be incredibly proud of what he achieved.”
The current managing director, Jeff Wirth, adds, “We are determined to build on those firm foundations and continue to grow and prosper as we look forward to the next 40 years of success.”
The baton has also been passed to current production manager Justin Hughes, son of the firm’s original technical director, Peter Hughes.
He said: “We now have backing behind us which enables us to push forward and aim at new markets because we have a big safety net behind us. It gives us reassurance.
“I spoke to our new managing director, Jeff Wirth, who was incredibly complimentary about the existing workforce and said how brilliant it was and the high level of skill and work ethic here.”
It was a sentiment echoed by finance manager Michaela Lawton who said: “We have a lovely team here and everyone’s really very excited about the future.
“We’ve had an investment of £1.6 million and the company’s been on an upward trajectory in terms of growth, turnover and profit and being able to diversify our product range is the next step forward.
“It’s great for Steve, who’s been with the company from the very beginning, to see that that the company is going to continue to grow and expand into new markets.
“Every business goes through a life cycle and the acquisition happened at a perfect time with the original founders reaching retirement age. It was a marriage made in business heaven and the sky’s the limit.”
Related Links:
https://www.insidermedia.com/news/wales/engineering-firm-set-to-reach-new-heights
https://www.wales247.co.uk/high-flying-engineering-firm-says-fond-farewell-to-founder-steve
Releasing "The Grinding Chronicles" Your Gateway to Optimized Grinding Processes
Check out CDT's new video series 'The Grinding Chronicles' as our team explores strategies to optimization the grinding process. Watch episodes 1 and 2 now >
Exciting news for those involved in precision grinding! This month, Continental Diamond Tool (CDT) proudly unveiled "The Grinding Chronicles," a video series aimed at unraveling the complexities of grinding techniques. Led by our team of expert product and application engineers, this series aims to empower and educate individuals seeking to enhance efficiency and reduce costs in their grinding operations.
Episode 1
Introduction to The Grinding Chronicles
The series kicks off with Nick Viggiano, President of CDT, extending a warm welcome to viewers. He introduces the team and outlines the series' core mission: addressing common grinding queries and tackling significant challenges encountered during the grinding process. With decades of expertise in crafting precision grinding products and innovative solutions, CDT promises to share valuable insights throughout this series.
Episode 2
Harnessing the Power of a Grinding Lab
In episode two, CDT Application Engineer Harrison Sheldon explores the benefits of using a grinding lab to improve grinding processes. Relying solely on personal judgments during grinding can lead to mistakes. Sheldon shows how sensors gather objective data, providing more accurate measurements. Discover how CDT's lab collects and analyzes data in four critical areas: Cut, Wear, Quality, and Cost.
Engage with The Grinding Chronicles
"The Grinding Chronicles" isn't just a viewing experience; it's a platform tailored to your needs. CDT invites active participation, encouraging viewers to submit their questions, challenges, and episode ideas. This series aims to address specific concerns of industry professionals who use our products.
Email us at TheGrindingChronicles@cdtusa.net with your questions, and we will do our best to answer them.
Explore Further with CDT's Grinding Lab
CDT's grinding lab has been a game-changer for those who have used it, enhancing operations through data-driven decision-making rather than relying on instinct. It can simulate various grinding environments and offers on-site analysis, ensuring minimal downtime for CDT customers. Plus, it’s complimentary for our customers to use.
In episode 2, you can witness how lab-generated data optimizes real-world grinding processes. Sheldon demonstrates how manipulating and measuring variables, like wheel speed, can help make smarter choices, yielding better results and cost savings.
If you're interested in leveraging a data-centric approach for process development or optimization, reach out to us at TheGrindingChronicles@cdtusa.net. Improving efficiency and precision is what we do.
Subscribe and Stay Tuned
Subscribe to CDT's YouTube channel to catch new episodes of "The Grinding Chronicles." Here are some upcoming topics you won’t want to miss:
Coolant and Its Effect on Grinding Performance
Conventional Abrasives vs. Superabrasives
Q-Prime, G-Ratio, Speeds & Feeds
Year-End Update from Continental Diamond Tool President Nick Viggiano
Join Nick Viggiano, President of Continental Diamond Tool, as he shares a candid overview of our progress in 2023 and plans for 2024. Learn more >
In this video update, Continental Diamond Tool's President, Nick Viggiano, offers a candid overview of the company’s progress in 2023 and its plans for 2024. Viggiano's report centers on CDT's commitment to meeting customer needs and improving the partnership experience.
Viggiano highlights three core customer priorities: Quality, Delivery, and Price. First, he discusses CDT's efforts to bolster quality by investing in new measuring equipment, tightening tolerances, and expanding CDT’s engineering team to refine customers' processes and minimize waste.
In his message, Viggiano acknowledges delivery issues in the past year that were exacerbated by global supply disruptions, growing pains, and staffing shortages. He assures viewers of proactive measures for 2024. CDT has made significant investments in equipment and recently initiated an expansion project to enhance production capacity and mitigate delays.
Regarding the company’s approach to pricing, Viggiano emphasizes CDT's success in negotiating favorable prices with vendors due to its growth in the industry. “We’ve been able to flex our muscles and buy larger volumes of material to achieve better pricing, “says Viggiano. “This has been very evident over the last handful of years when our major competitors imposed multiple price increases per year or double digit increases annually. At CDT, we’ve been adamant about keeping increases to an absolute minimum.”
In addition, Viggiano highlights this year’s release of CDT's Evo Hybrid Bond wheels, designed to optimize operations for manufacturers of round tools and inserts. Customers are encouraged to reach out to CDT’s sales team to explore these new wheels for potential benefits.
Evo’s advancement in hybrid bond technology is the latest innovation to come from CDT’s expert engineering team and state-of-the-art grinding lab. In the video, Viggiano extends an invitation to customers to utilize CDT's grinding lab at no cost, emphasizing the company's commitment to supporting customers to achieve much better cycle times and reduce waste.
Finally, Viggiano announces an upcoming video series, "The Grinding Chronicles," to be released on CDT’s YouTube channel on January 4th. The series is set in CDT’s grinding lab where engineers will use the testing center to address grinding challenges and showcase its capabilities.
CDT's unwavering focus on continuous improvement, evident through process enhancements, equipment upgrades, and team empowerment, underscores the company's commitment to assisting customers in staying competitive. As Viggiano concludes, “We’re committed to helping you gain the edge you need to secure new business.”
Watch this video of Nick Viggiano's President's Report for a comprehensive look at Continental Diamond Tool’s customer-focused approach and plans for the future.
Join Nick Viggiano, President of Continental Diamond Tool, as he shares a candid overview of our progress in 2023 and plans for 2024. Learn how CDT's efforts to enhance quality, delivery, and fair pricing benefit our valued customers.
Understanding Precision Polishing Film and Its Role in Precision Manufacturing
Did you know you can order Precision Polishing Film through CDT? In this article, we talk about Precision Polishing Film and its role in refining surface quality on metals, ceramics, optics, and more. Learn about its types, applications, and integration into precision manufacturing solutions.
In precision manufacturing, achieving a flawless surface finish is fundamental for product functionality and aesthetics. Precision polishing film, a specialized material used in the final polishing stages, stands as an important tool in refining and perfecting surface quality to meet rigorous industry standards.
What is a Precision Polishing Film?
At its core, precision polishing film is crafted by coating an abrasive material onto a flexible polyester substrate. This film refines surfaces and ensures precision across a variety of materials including metals, ceramics, optics, and semiconductor wafers.
3 Types of Precision Polishing Film
There exists several varieties of precision polishing film, each tailored to specific surface refinement requirements:
Mirror Film: Noted for its fine-graded abrasive grains uniformly coating the polyester film, mirror film offers superior sanding capability and durability.
Lapping Film: With micron-graded abrasive grains uniformly distributed in resin adhesive, lapping film consistently delivers accurate and high-quality finishes.
Diamond Lapping Film: The diamond abrasive in this lapping film makes it particularly suitable for precision finishing of extremely hard substances or challenging materials such as ceramic and ferrite compounds.
Broad Industry Applications
Precision polishing films are useful for many applications across diverse industries. They play an essential role in enhancing the surface of roll and shaft materials, flat displays, commutator shafts of micro motors, and magnetic heads and disks. These films are equally prevalent in the manufacture of many disc applications such as plastic lenses, optical devices, fibers, and painted surfaces. Additionally, sheet applications like print circuit boards and optical devices incorporate precision polishing film in their manufacturing processes.
Extending Beyond Our Core Specialties
While Continental Diamond Tool (CDT) is known for its high-quality, custom diamond and CBN grinding products, alongside precision diamond dressing tools, our commitment to excellence encompasses more than our specialized niche. Our expertise extends to supplying other essential grinding and polishing solutions, including precision polishing film, to address the evolving needs of our customers. This highlights our dedication to addressing a wide array of precision manufacturing requirements.
The CDT Advantage:
A Legacy of Quality: We ensure consistent, superior-grade products that adhere to stringent industry standards.
Customized Solutions: Our skilled technicians offer customized solutions, ensuring optimal performance for unique customer requirements.
Comprehensive Support: From concept to implementation, our expert team provides guidance to maximize productivity and achieve the best possible outcomes.
Expanded Offerings: Alongside our core expertise, we equip customers with grinding and polishing essentials, including precision polishing film, ensuring a comprehensive suite of tools for optimal surface refinement.
Backed by Uncompromising Quality
Our precision polishing films, like all products supplied by CDT, are made of the highest quality materials with various thicknesses available, starting at a minimum of 25 microns. The polyester film’s uniform thickness, smooth surface, and strength provides strong resistance to pulling and tearing forces, with less elasticity.
This table outlines the extensive variety of options available:
For detailed information on our precision manufacturing grinding and finishing products and their benefits to your operations, contact us today.