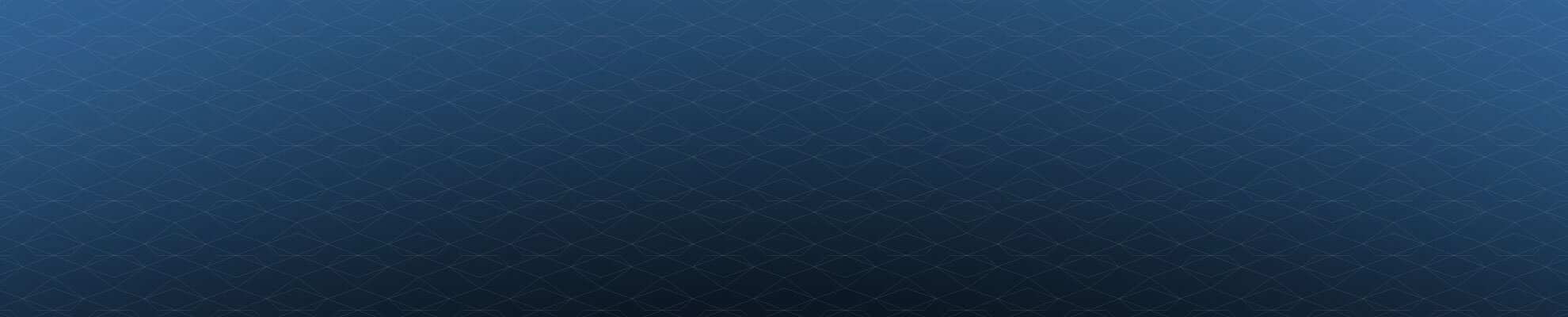
News and Resources
Browse by Category
Browse by Product
- All Dressing Products
- All Grinding Products
- CBN-Diamond Superabrasives
- Conventional Abrasives
- Diamond Lapping Compounds
- Diamond Rotary Dressers
- Diamond Stationary Dressers
- Hybrid Bond Grinding Tools
- Metal Bond Grinding Tools
- Plated Grinding Tools
- Resin Bond Grinding Tools
- Vitrified Bond Grinding Tools
CNC Machining vs. Traditional Machining: A Comparative Analysis for Precision Grinding Tools
Discover how CDT's advanced machining methods enhance the quality, reliability, and cost efficiency of our cBN and diamond grinding wheels. Learn more in our latest comparative analysis.
When it comes to the manufacture of high-precision grinding wheels in diamond or cBN (Cubic Boron Nitride), the choice of machining method can significantly impact the quality and efficiency of production. At Continental Diamond Tool (CDT), we leverage traditional machining, CNC (Computer Numerical Control) machining, and automated robotic CNC machining to deliver high-precision grinding tools for many global industries. Having a skilled workforce and modernized equipment in all three types of machining is a distinct advantage for us and our customers.
In this article, we will compare the pros and cons of these machining methods. You’ll learn how we incorporate all three into our manufacturing process to get the highest quality and most cost-effective results for our grinding tools and wheels. Finally, we will share insights from our machinists about what it takes to excel in these roles and contribute to the production of superior precision tooling.
Machining Methods: Pros and Cons
Traditional Machining
Advantages:
Flexibility: Traditional machining is highly adaptable for a wide range of tasks and can be used for both simple and complex geometries without the need for extensive programming.
Human Expertise: Skilled machinists can make real-time adjustments based on their experience and intuition, which can be beneficial for unique or custom jobs.
Lower Initial Cost: The initial investment for traditional machining equipment is generally lower than that for CNC machines, making it more common in low-volume or smaller operations.
Challenges:
Lower Precision: Traditional machining typically relies on manual control, which can lead to variations in precision and consistency, particularly with high-volume orders.
Slower Production: Manual operations can be time-consuming, reducing overall productivity compared to automated processes.
Higher Labor Costs: Skilled machinists are required to operate traditional machines, which can equate to higher labor costs over time.
CNC Machining
Advantages:
High Precision and Consistency: CNC machining offers unparalleled precision and repeatability, which is crucial for manufacturing high-quality grinding tools like electroplated diamond and resin bond grinding wheels.
Increased Efficiency: Computerized control allows for faster production cycles, reducing lead times and increasing throughput.
Reduced Labor Costs: Once programmed, CNC machines require less manual intervention, reducing the need for highly skilled labor for routine operations.
Challenges:
Higher Initial Investment: The cost of CNC machines and the necessary software can be significantly higher than traditional machining equipment.
Programming Requirements: CNC machining requires specialized programming knowledge, which can be a barrier for some operations.
Maintenance and Repairs: CNC machines can be more complex to maintain and repair, requiring specialized technicians.
Automated Robotic Machining
Advantages:
Enhanced Productivity: Automated CNC grinding uses robotic arms that can operate continuously with minimal supervision, significantly increasing production rates and efficiency for producing grinding wheel components.
Consistency and Quality: Automation ensures that every grinding tool in a series is machined to the exact same specifications, reducing the likelihood of defects and ensuring uniform quality.
Labor Optimization: Automation frees human workers to focus on more complex and value-added tasks, optimizing labor utilization and reducing repetitive strain injuries.
Challenges:
High Upfront Costs: Integrating automation involves significant initial investment in both equipment and software, which can be a barrier for smaller companies.
Technical Complexity: Automation systems require a high level of technical expertise to implement and maintain, which can pose challenges for operations without such capabilities.
Adaptability: Automated systems can be less flexible than manual operations when it comes to handling custom or unique jobs that require careful planning and programming.
How Machining Fits in CDT's Manufacturing Process
At CDT, machining plays a crucial role in the manufacturing process of our superabrasive products. Whether using resin, metal, vitrified, or hybrid bonds — or our sophisticated electroplating process — precision machining ensures our grinding tools meet the stringent requirements of our customers.
Resin, Metal, Vitrified, and Hybrid Bonds
Initial Machining: Depending on the tool, CNC machining sometimes occurs before the molding and sintering processes to prepare the core elements.
Post-Sintering Machining: After molding and sintering, additional CNC machining and manual grinding fine-tune the precision of the finished grinding wheel within customer tolerances.
Plating Process
Initial Machining: All machining is completed at the beginning, where the desired wheel size and geometry are typically CNC-machined onto a steel core or blank.
Minimal Finishing: Once electroplated, minimal finishing is required as the plating process closely mimics the core geometry, allowing for the programming of complex shapes and geometries with minimal additional work.
High Volume Orders
Initial Machining: With high-volume repeat orders, we utilize automated robotic CNC machining to prepare the core or blank. These systems can run 24/7 to stockpile common wheel sizes.
Finishing: Every order, large and small, goes through final finishing/machining and several quality checks to ensure that each grinding tool meets our stringent quality standards. This meticulous process guarantees that all products, from vitrified grinding wheels to metal bond diamond tools, adhere to the precise specifications and tolerances required by our customers.
Examples of Machinist Roles at CDT
CNC Operator
The CNC operator at CDT is responsible for programming, setting up, and operating CNC lathes or mills. This role is essential for producing high-precision grinding tools, from electroplated grinding tools to vitrified and resin bond grinding wheels.
Key Responsibilities:
Programming CNC machines for various tasks.
Setting up CNC lathes or mills for production runs.
Operating CNC machines to produce precision grinding tools.
Skills and Qualities:
A passion for learning and problem-solving.
Logical thinking and attention to detail.
Willingness to be trained on new technologies.
"To be a good fit as a CNC machinist, you need to enjoy the challenge of looking at a problem and solving it logically. One of the great things here at CDT is if you have limited experience or no experience, we are willing to train." — Ron Fuller, Lead Operator
Manual Lathe Operator
The manual lathe operator at CDT typically works in the metal bond department but sometimes with others as well, handling tasks that require manual precision and expertise. This role can come into play at the beginning, middle, or end of the production process, especially for metal bond diamond tools.
Key Responsibilities:
Operating manual lathes to produce grinding tools.
Ensuring quality and precision through manual adjustments.
Overseeing the product quality through all manufacturing stages.
Skills and Qualities:
High motivation and a readiness to “get your hands dirty.”
Reliability and willingness to work overtime on occasion.
Appreciation for quality, taking pride in your work, and seeing the product evolve.
"What I like about working in the metal bond department is seeing the product go through the process and the steps, and then ending up with the finishing piece. It's satisfying to see that through." — Brian Yates, Supervisor
The CDT Machining Edge
At CDT, we understand the importance of choosing the right machining method to meet the demands of precision grinding tool production. By leveraging traditional machining, CNC machining, and automated CNC grinding, we can offer our customers high-quality diamond grinding wheels, vitrified grinding wheels, electroplated diamond grinding wheels, resin bond grinding wheels, and other superabrasive tools with exceptional precision and efficiency. Each method has its advantages and challenges, and our integrated approach allows us to optimize production based on the specific needs of each project.
As technology continues to evolve, we are committed to adopting the best practices and innovations to deliver the highest standards in the industry. If you are interested in joining our team, apply today at cdtusa.net/careers.
Recognizing the Importance of Cleaning and Maintenance at Continental Diamond Tool
Discover how the cleaning and maintenance teams at Continental Diamond Tool are essential to producing high-quality diamond tools while ensuring workplace safety and efficiency.
In manufacturing, the spotlight often shines on the experienced engineering team, the cutting-edge machinery, and the high precision grinding products we produce. Yet, behind the scenes, two critical forces work tirelessly to ensure that everything operates smoothly: the cleaning and maintenance crews. At Continental Diamond Tool, we recognize the indispensable role these teams play in our daily operations and overall success.
Keeping Operations Running Smoothly
The primary role of cleaning and maintenance is to ensure that all equipment and facilities are in top working condition. In the manufacturing process, even minor disruptions can lead to significant delays and costs.
Dan Becker, Maintenance Supervisor, details the meticulous care his team puts into preserving operational efficiency: "We maintain all of the manufacturing equipment in the building. For example, we manage the coolant in 5 dozen CNC machines and routinely clear out all of the chips. We also have 12 grinders, which we take completely apart, clean out, and inspect the belts and pulleys for wear regularly." This is just a snapshot of the thoroughness with which they maintain operations.
Regular maintenance and thorough cleaning prevent machinery breakdowns, allowing operations to continue without interruption. These efforts are crucial for ensuring that our orders are delivered on time. In this way, our cleaning and maintenance teams ultimately contribute to customer satisfaction. Timely delivery is a priority our customers rely on.
Ensuring Safety and Quality Standards
Quality and safety are also top of mind at Continental Diamond Tool, and our cleaning and maintenance crews are key players in both of these areas.
Maintaining a safe working environment starts with cleanliness. By regularly removing debris, cleaning spills, and ensuring that all areas are free from hazards, our cleaning techs help prevent accidents and injuries. Likewise, well-maintained facilities and equipment are essential for operational efficiency. Their diligent work supports our commitment to providing a safe workplace for all employees.
Quality requires precision. In the manufacturing of our high-quality diamond tools, this means that even the smallest particles can impact the final product. Our cleaning crew works tirelessly to maintain a contaminant-free environment, directly influencing the quality and reliability of our products. This meticulous attention to detail ensures that we meet and exceed industry standards and customer expectations.
"At CDT, we like to keep a clean shop. To do this job well, you have to be on your feet a lot and always stay moving, stay motivated. It requires attention-to-detail and focus," says Boston Stopher, Cleaning Tech at CDT. Hear more from Boston in this video:
Enhancing Efficiency and Employee Morale
A clean and well-maintained environment not only extends the life of our equipment and enhances the quality of our products and service, but it also boosts overall efficiency and morale. Workers are able to perform their tasks more effectively in an orderly setting. Furthermore, regular maintenance can improve the performance of machinery, potentially increasing output and reducing energy consumption. A clean and well-organized workplace also boosts employee satisfaction and pride in their work environment. With tidiness comes increased productivity and a stronger sense of team overall.
Cleaning: A Pathway to Growth
Our cleaning department is made up of 8 to 10 dedicated individuals who manage the cleanliness of our soon-to-be 200,000 sq. ft. manufacturing space between our 1st and 3rd production shifts. Key responsibilities include:
Sweeping and mopping floors
Wiping down equipment
Disposing of trash and metal shavings
Many team members start their careers in this department right out of high school, gaining valuable insights into the workings of different departments and shaping their future career paths within the company. For those interested in exploring opportunities as a cleaning technician, more information is available on our careers page.
Maintenance: Proactive Problem Solvers
Our maintenance department, though small, is mighty, comprising just 4 individuals with 68 years of combined experience. They are responsible for maintaining more than 500 plating tanks, 60 CNC machines, plus numerous other pieces of equipment small and large. The efficiency of our processes, reliability of our products, and comfort and safety of our facilities hinge on the efforts of this team. As Maintenance Specialists, these professionals play a pivotal role in our seamless operations. Their tasks include:
Routine maintenance
Basic and minor repairs
Changing filters, coolant, and fluids
Some fabrication work
Collaboration with engineering and manufacturing teams on projects
This dynamic team is committed to upholding our high-quality and safety standards, keeping our state-of-the-art equipment in top-notch condition, and contributing to the overall growth of Continental Diamond Tool. Find information about our Maintenance Specialist role and other positions at CDT here.
Conclusion
At Continental Diamond Tool, we understand that our achievements are not solely the result of the sophisticated equipment we use or the exceptional products we create; they are also a testament to the dedication and hard work of various departments that frequently go unrecognized. Our cleaning and maintenance crews are vital to our operation, and their contributions are valued as an integral part of our success. By supporting their efforts, we reinforce the foundation of our company’s strength and ensure that we continue to lead in the industry with integrity and excellence.
Students Build Careers in Engineering with CDT Apprenticeships
Continental Diamond Tool Ltd. is shaping engineering careers for Kinmel Bay-area students like Rhys Butler and Corey Jones. Follow Rhys's eight-week work experience apprenticeship alongside Corey at CDT's precision manufacturing facility in North Wales.
(From left to right) Rhys Butler, left, and Corey Jones who are building careers in engineering with the apprenticeship programme at Continental Diamond Tool Ltd. in collaboration with Coleg Llandrillo in North Wales.
An 18-year-old sixth form student is getting a taste of the world of precision engineering after being inspired by the success of a high flying company.
Rhys Butler, a pupil at Ysgol Glan Clwyd in St Asaph, is now on an eight-week work experience programme after writing to Continental Diamond Tool, on the Tir Llwyd Industrial Estate in Kinmel Bay, which is withing walking distance of his home.
According to Rhys, he was prompted to get in touch when he read a news story about the firm which supplies sophisticated parts for production machinery for Rolls-Royce and other aerospace companies in the UK.
Continental Diamond Tool Ltd. (CDT), which employs 40 skilled staff and is celebrating its 40th anniversary this year, is one of only two companies of its kind in the UK.
It makes a range of highly specialised diamond tools for advanced manufacturing industries, including the aerospace, automotive, medical and semi-conductor sectors.
Rhys said: “I saw the story about the company being under new American ownership and I was looking for work experience for my CV so I emailed in an application and they came back to me straight away.
“They’ve given an eight-week programme so I go in one day a week and I’m going through the different processes they do and they show me and explain how they work.
“One Wednesday I was actually working on putting the diamonds into the tooling. It’s been a brilliant opportunity.
“I’ve always been interested in cars and how machines work and I’m doing engineering in sixth form and go to the Llandrillo College campus in Rhyl every Thursday which is really helpful.”
Rhys often works alongside Corey Jones, 19, also from Kinmel Bay, now in his second year as an apprentice who also took the work experience route to a place with CDT.
He said: “I did my A-levels at Eirias High School in Colwyn Bay and then did Level Three Engineering at Coleg Llandrillo’s site at Rhyl with work experience here and they offered me an apprenticeship.
“They wanted me to get used to what’s involved so I worked here through my summer holidays and started my apprenticeship in September in Level Four Engineering.
“I knew there was a lot of maths in engineering and I’d always enjoyed that and I like to challenge myself by learning about the different machines so I’m really enjoying it.
“I had tried a few places for work experience and Coleg Llandrillo suggested here and it’s been brilliant.
“The people here are really great and very knowledgeable with lots of experience you can learn from – I work with someone who has experience on every machine and he’s a big help.
“We’re working for businesses like Rolls-Royce which is fantastic so I want to do the best I can and really build a career here.”
Michaela Lawton, CDT Finance Manager, said: “We have been running an apprenticeship scheme here for a long time and historically it’s been successful and two of our apprentices who moved on after a few years have actually come back to us.
“We have a very good relationship with Coleg Llandrillo and it really helps that they have a campus at Rhyl with a strong and well-equipped engineering department.
“What we do here is so unique and so niche that we expect our apprentices to learn the core skills in college to give them the platform to build on with the highly specialised work we do here.”
CDT has been boosted by a £1.6million investment by their American owners and has opened a second production unit on the Tir Llwyd Estate to house its new electro-plating operation which has received support from Welsh Government.
More than 60 per cent of the company’s products are exported to 30 countries, with sales growing particularly strongly across Europe and Asia, as well as North America.
The company, which celebrates its 40th anniversary this year, was founded originally as Consort Precision Diamond and in 2018 was bought and rebranded by Continental Diamond Tool Corporation, based in New Haven, Indiana.
Related Links:
https://www.gllm.ac.uk/news/rhys-and-corey-shine-with-diamond-tool-firm
Images captured by Mandy Jones Photography.
Part Masking of Plated Grinding Wheels
Learn about the process of part masking in the production of plated diamond and CBN grinding wheels. This technique ensures precision and quality in precision grinding across industries like manufacturing, automotive, and aerospace. Find out the specialized skills that are required to excel in this type of work.
Part masking is a crucial technique employed in the plating process for CBN (Cubic Boron Nitride) and diamond grinding wheels. This method involves selectively covering specific areas of a metal substrate before plating to protect them from the plating solution. Part masking plays a significant role in ensuring the precision, quality, and functionality of grinding wheels used in various industries, from manufacturing to automotive and aerospace. In this article, we will delve into what part masking is, how it is done, why it is essential in the plating process, and what it takes to excel at this intricate skill.
What is Part Masking?
Part masking is the process of shielding specific areas or features of a substrate to prevent them from being plated during the plating process. It is achieved by applying a masking material to the surface of the substrate in a controlled and precise manner. The masking material can be in the form of tapes, paints, or other coatings that can resist the heat and duration of time in the plating process.
How is Part Masking Done?
The process of part masking involves several steps:
Surface Preparation
Before masking, the metal substrate is thoroughly cleaned and prepared. This step ensures that the surface is free from contaminants, oils, coolants, machining residues and oxides, which can interfere with the adhesion of the masking material.
Masking Material Selection
The choice of masking material depends on factors such as the type of substrate being plated, the plating process used, and the specific areas that need protection. Common masking materials include specialized masking tapes, latex, and resin-based coatings. Continental Diamond Tool employs all of these methods in its process.
Application of Masking Material
The masking material is applied precisely to cover the areas that should not be plated. This can be done manually or using brushes, stencils, scribes or automated equipment. For more complex patterns, careful attention is given to ensure that there are no gaps or leaks in the masking material.
Cure or Drying
Depending on the type of masking material used, it may need to be cured or allowed to dry thoroughly. This step generally takes a specific amount of time and ensures that the masking material remains intact and impermeable during the plating process.
Plating
Once the wheel has been masked and cured, the substrate is immersed in the plating bath, where the exposed areas are plated with the desired abrasive material, such as diamond or CBN particles. The masked areas remain untouched, preserving their original characteristics.
Mask Removal
After the plating process is complete, the masking material is carefully removed, revealing the plated surface underneath. This can be done through various methods, such as peeling off tapes or dissolving the masking material with solvents.
Why is Part Masking Essential?
Part masking serves several crucial purposes in the plating process for diamond and CBN grinding wheels:
Precision and Quality
Part masking ensures that the plating is applied precisely to the intended areas, maintaining the tight tolerances, quality, and accuracy essential to precision grinding.
Functionality and Performance
By protecting specific features of the grinding wheel, such as arbor holes, flanges or threaded holes, from plating, part masking helps maintain their functionality and performance, ensuring they are dimensionally fit and operate correctly.
Cost Efficiency
Masking reduces the amount of plating material used, minimizing waste and lowering production costs. It also prevents the need for costly post-plating rework to remove unwanted plating.
Customization
Part masking, applied by hand, is customizable. This allows manufacturers to create tailored, complex products to meet specific customer requirements.
What It Takes to Be Good at Part Masking
Part masking is a specialized skill that requires attention to detail, precision, and an understanding of materials and processes. Here are some key attributes and considerations for those looking to excel in this field:
Attention to Detail
Successful metal part maskers must have a keen eye for detail. Precision is paramount in this process, as even the smallest imperfections or gaps in the masking material can lead to plating errors.
Material Knowledge
Familiarity with various masking materials and their properties is essential. Different materials may be required for specific applications, and understanding their characteristics can ensure the right choice is made.
Patience and Dexterity
The application of masking material can be a delicate and time-consuming task. Patience and manual dexterity are necessary to achieve consistent and high-quality results.
Problem-Solving Skills
Maskers may encounter challenges such as complex shapes or irregular surfaces that require creative problem-solving to ensure proper masking.
Adherence to Safety Protocols
Safety is paramount when working with masking materials and plating chemicals. Understanding and following safety protocols are crucial to prevent accidents and exposure to hazardous substances.
At CDT, our masking department has almost 50 years of combined experience in this highly specialized field. The superior quality and stellar reputation of our plated products are a testament to their expertise.
If you are passionate about precision craftsmanship and believe you have the skills and attributes required for part masking, we encourage you to consider career opportunities in this field. At Continental Diamond Tool, we value skilled professionals who can contribute to our commitment to excellence.
To explore potential positions and apply for a rewarding career in electroplating or other positions in our industry, visit our careers page.
How to Order a Custom Electroplated Grinding Wheel
At CDT, we take pride in the excellence of our masking and plating departments. Part masking is an indispensable technique in the production of plated diamond and CBN grinding wheels to ensure the delivery of the very best products. It requires a unique set of skills, including attention to detail, material knowledge, patience, and problem-solving abilities. Those who excel in this field play a vital role in providing the precision, quality, and functionality of grinding wheels used across various industries.
If you are interested in ordering a custom plated grinding wheel or have any inquiries, please don't hesitate to contact our customer service department. Our team can connect you with our experienced plating engineers to start the process today.
Top 10 Reasons to Work Third Shift at CDT
From longer weekends to higher pay, check out the top ten reasons you should apply for a third shift position at CDT.
Here at Continental Diamond Tool, we take our work seriously, but that doesn’t mean we don’t have a sense of humor! Whether you think of third shift as a “late shift” or a “late show,” there are lots of great reasons to work nights at CDT.
From longer weekends to higher pay, watch the video below to see the top ten reasons you should apply for third shift at CDT.
Drumroll please…..
CDT Starting A New Third Shift
Continental Diamond Tool has experienced extensive growth in Three of their most popular product lines, and they are now adding a third shift to their schedule to increase production and continue to fulfill global orders in a competitive timeframe. Apply today >
Continental Diamond Tool Starting A New Third Shift, Now Hiring
Continental Diamond Tool has experienced extensive growth in three of their most popular product lines, and they are now adding a third shift to their schedule to increase production and continue to fulfill global orders in a competitive timeframe.
The new shift will consist of four 10-hour shifts per week, from 8 p.m. to 6 a.m. This third shift will begin as soon as the open positions are filled, which may be as soon as August. All positions are entry-level and require a high school diploma. Job training will be provided.
CDT fosters an innovative, team-oriented environment for their employees, who enjoy paid lunch breaks, competitive wages, and health insurance benefits, along with additional benefits and overtime opportunities, in a clean, climate-controlled environment.
In business since 1973, CDT is a leading producer in the global market for superabrasive grinding wheels and custom tooling. Their 128,000 sq. ft. manufacturing facility in New Haven, Indiana, utilizes the latest technology to serve numerous industries including medical, aerospace, power generation, and more.
Additional information and applications are available by calling 800-443-6629 or visiting CDTUSA.net/careers.