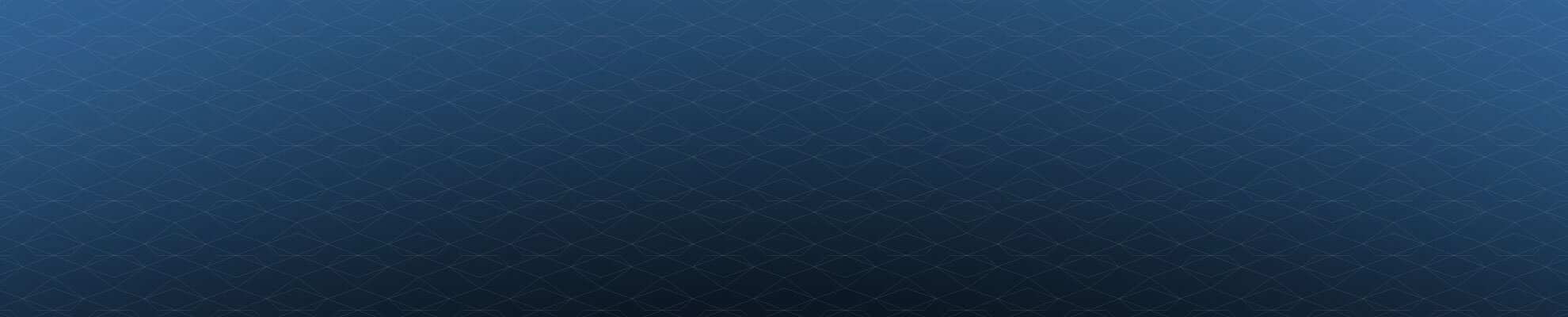
News and Resources
Browse by Category
Browse by Product
- All Dressing Products
- All Grinding Products
- CBN-Diamond Superabrasives
- Conventional Abrasives
- Diamond Lapping Compounds
- Diamond Rotary Dressers
- Diamond Stationary Dressers
- Hybrid Bond Grinding Tools
- Metal Bond Grinding Tools
- Plated Grinding Tools
- Resin Bond Grinding Tools
- Vitrified Bond Grinding Tools
2025 President's Message: Reflecting on Growth and the Future
Discover how Continental Diamond Tool's 2024 investments in people, processes, technology, and infrastructure are paving the way for enhanced customer solutions in 2025.
As we usher in 2025, Continental Diamond Tool is proud to reflect on an incredible year of progress and innovation. In this video update, CDT’s President, Nick Viggiano, shares his gratitude and insights, highlighting the milestones and lessons from the past year.
Strong Partnerships: Driven by GRIT
Thanks to the unwavering support of our customers and suppliers, CDT has thrived since 1973. We are grateful to our loyal partners who have been instrumental in making CDT an American manufacturing success story. Guided by our GRIT: Global, Responsive, Innovative Team, being a committed partner remains central to our mission as we deliver superior superabrasive solutions for advanced applications across the world.
2024 Highlights: Advancing to Better Serve You
In 2024, our focus was on making internal improvements to better serve you — our customers. By investing in people, infrastructure, and technology, we strengthened our ability to deliver the precision and quality you expect from us. Here are a few key achievements:
Strategic Leadership: Under the leadership of our new CEO, Brian VanHall, we are strengthening our strategy, structure, and systems to ensure your needs are met with efficiency and excellence.
People-Centered Investments: Our strongest competitive advantage is our people. By attracting and cultivating top talent, we have assembled a team that is committed to making every interaction and product surpass your expectations.
State-of-the-Art Expansion: Our newly expanded 72,000-square-foot Technology Center in New Haven, Indiana, will be a platform for the latest advancements in machining, inspection, and quality control for unmatched product reliability.
Global Growth: With a move underway in Wales to a larger 30,000-square-foot building, we are further increasing our capacity to provide timely support and advanced solutions to a global market.
Lessons Learned: Elevating the Customer Experience
In 2024, we put our focus on what truly matters:
People: By placing the right people in the right roles, our team is equipped and empowered to meet your needs with expertise and responsiveness.
Development: Continuously investing in our people, processes, and products delivers better, more innovative solutions for you.
Quality: Enhancing processes that assess, analyze, and assure product quality, performance reliability, and customer satisfaction.
Looking Ahead to 2025: Focused on You
As we step into the new year, we are energized by the opportunities ahead. We remain deeply committed to our mission of delivering unparalleled solutions while fostering strong partnerships with our customers and suppliers. Our gratitude extends to every individual who contributes to our success, from the dedicated CDT team to our trusted partners.
From all of us at Continental Diamond Tool, we wish you in this dynamic world of manufacturing a prosperous and fulfilling 2025.
You can find CDT’s latest product innovations, expert grinding tips, and company news by visiting our blog, watching our videos, or connecting with us on LinkedIn. Together, let’s make this another year of partnership and success!
Cutting Cycle Times in Technical Ceramics Grinding with Vitrified Bond Wheel
Learn how CDT engineers optimized grinding of ceramics with a CDT vitrified bond wheel that cut cycle times by 86% while eliminating excessive heat and chipping.
What does it take to deliver cutting-edge solutions for some of the world’s most advanced applications? Success starts with strong foundational values. At Continental Diamond Tool, we value being a Global, Responsive, Innovative Team [GRIT].
One recent collaboration with a global manufacturer of technical ceramics exemplifies CDT’s GRIT in delivering timely, innovative, quality, custom solutions to our customers. This story highlights how our application engineers and Vitrified Bond department collaborated to provide a superior superabrasive solution that dropped cycle times by an astounding 86% for advanced ceramics operations that supply the world.
The Challenge: Improving the Grinding Process
This initiative started when this valued customer in the ceramics sector reached out to CDT to address a grinding operation that was inefficient and inconsistent. The challenge stemmed from a new material they were using for parts that needed to be produced in high quantities. Their existing process required an hour to correctly grind the preformed ceramic part; and they were experiencing significant challenges including excessive heat and chipping. The result was a frustrating combination of high cycle times and inconsistent quality.
Grinding technical ceramics is a very complex process due to the unique properties of the material. Ceramics are incredibly hard and brittle, making them prone to cracking and chipping under improper grinding conditions. Unlike metals, ceramics lack ductility, meaning there is little room for error when removing stock material. Achieving precision requires tools that maintain sharpness while withstanding the intense friction and heat generated during grinding. Furthermore, ceramics often feature intricate shapes and tight tolerances, adding another layer of difficulty to the process.
One of the most significant challenges is minimizing wear on grinding tools while maintaining efficiency. The wrong grinding wheel will wear down quickly or fail to deliver the necessary precision when working with ceramics. This is where Vitrified Diamond Bond grinding wheels are a superior solution, offering a balance of durability and performance that meets the rigorous demands of ceramic grinding. Our product managers and application engineers understand these challenges and work closely with customers to design, develop, and deliver quality custom tools for specific applications.
The Solution: Innovation through Product Development and Process Parameters
Our Application Engineer, Andrew Olvera, consulted with the customer to analyze their existing setup and recommend strategic changes. He travelled to their facility to see the process and speak with the operator firsthand. Reflecting on the project, Andrew said, "I really enjoyed working with the customer on this challenge. We first began seeing positive results after making tweaks to the machine's programming. When we introduced the customized wheel, the jump in efficiency really ramped up. The cycle times dropped even more than we expected without the chipping that the customer usually saw in their process."
By reprogramming the machine's grinding operations, custom engineering an optimized wheel, and fine-tuning parameters, the CDT team achieved a groundbreaking improvement. Here are the key adjustments that were made, and the results:
Enhanced Machine Parameters:
Increased spindle speed to 10,000 RPM.
Doubled table speed from 100 to 200 inches per minute.
Adjusted infeed to .0035-.004 inches with no measurable wheel wear.
Achieved .005” infeed with minor wear observed.
Reduced Cycle-Time:
The customer’s previous process took an hour; our optimized process completed the task in just 8 minutes—an astounding reduction in cycle time by over 86%.
Improved Quality:
We addressed the quality issues in the preformed parts and optimized for a consistent 0.170” stock removal. This enhancement balanced efficiency and consistency with minimized wheel wear.
The Response: A Testament to Teamwork
This project also highlights CDT's commitment to responsiveness in meeting our customer’s unique requirements. Recognizing the critical challenges posed by the customer’s quality issues and process inefficiencies, our Vitrified Bond Product Line Manager, Walt Baumbach, spearheaded efforts to provide a custom grinding wheel. Walt Baumbach noted, “Our team rallied together to design, develop, and deliver a solution in an impressive 15 days. This quick turnaround shows the abilities and flexibility of our team.”
Walt Baumbach, CDT’s Vitrified Bond Product Line Manager, reviewing custom grinding wheel designs. His team helped cut cycle times by 86% for advanced ceramics.
The Outcome: Setting a New Standard
The results speak for themselves: CDT partnered with this prominent global technical ceramics manufacturer to provide a superior superabrasive solution to their unique grinding challenges. The innovation improved process efficiency and enhanced the durability and reliability of the Vitrified Bond grinding wheel used for this task. The wheel’s ability to handle challenging stock removal with minimal wear underscores the superior performance of our custom engineered products for the manufacture of technical ceramics for a global market.
While the 15-day rapid turnaround was an exceptional circumstance, enabled by a focused allocation of resources, we consistently strive to meet customer needs with efficient lead times tailored to the scope and complexity of each project. The quick delivery for this customer minimized their downtime and accelerated productivity improvements that will have a lasting impact.
Living Our Values: GRIT in Action
In many ways, this example embodies CDT’s GRIT. By combining a global mindset and responding to customer needs with innovative products and services, our team delivered a superior superabrasive solution that exceeded expectations. It is opportunities like this that define our commitment to excellence and drive us to continue pushing the boundaries of what is possible in grinding technology.
At CDT, we are more than a tool provider; we are a tenacious partner in progress. As we continue to serve industries around the world, our focus remains on delivering cutting-edge solutions that empower our customers to achieve their goals. We look forward to sharing more success stories as we advance the future of manufacturing together.
For more information about our Vitrified Bond product line or to discuss your unique grinding challenges with ceramics or other materials, reach out to our team today.
How CDT Works Together to Serve Customers Better
Behind every precision tool is a team—and surprising fun facts! Guess who are neighbors, or how many interviews we conducted last year. Read the article to learn more.
Staying competitive in precision manufacturing is about more than customizing the most advanced grinding tools and cutting-edge dressing technology—it’s also about the people and processes that ensure everything runs smoothly. At Continental Diamond Tool, many departments work together to deliver exceptional products and service to our customers. In this blog, we’re highlighting the key players whose efforts behind the scenes uphold our standards of reliability and customer satisfaction.
Let’s explore how our departments—from Executive Leadership to Human Resources, Purchasing, Marketing, IT, Finance, and Administration—play a crucial role in better serving our customers.
Executive Leadership: Setting the Vision
Leadership is the compass that guides a company toward success. Our Executive Leadership team sets strategic direction, defines goals, and ensures alignment of our department initiatives with market demand. From expanding facilities for electroplating with diamonds to encouraging development of custom hybrid bonds, our leadership fosters a culture of innovation, reliability, and customer focus.
Fun Facts:
Continental Diamond Tool is a second-generation family-owned company. CDT President Nick Viggiano succeeded his father, Ray, who founded the company in 1973. Under Nick’s leadership, the company has become the fastest growing superabrasives company in North America.
Did you know CDT President Nick Viggiano and CEO Brian VanHall are neighbors? The family ties and neighborly spirit run deep in our organization.
Human Resources: Building a World-Class Team
The foundation of any successful company are people. Human Resources Director, Jenni Long, ensures we hire top talent, provide continuous training, and foster a positive workplace culture. By focusing on employee engagement and growth, HR builds a motivated, skilled team dedicated to excellence.
Fun Facts:
This month, Jenni single-handedly processed the open enrollment benefit selections for more than 180 employees. Plus, she’s conducted over 250 interviews this year.
We’re hiring! Join Jenni’s team as an HR Generalist. Click here to apply.
Purchasing: Ensuring Quality and Consistency
In precision manufacturing, quality starts with sourcing the right materials. The Purchasing department ensures our production teams have access to high-quality raw materials and supplies to meet exacting standards. Strong vendor relationships and effective inventory management keep operations efficient and cost-effective.
Fun Facts:
Inventory management is one of many functions this department handles. With more than 2,500 SKUs in our system, Dan Kortenber and Matt Sheehan ensure materials are always available to meet our customers' needs on time.
In his spare time, Matt referees both college and high school basketball.
Marketing: Connecting with Customers
Understanding customer needs is the first step to delivering outstanding service. Our Marketing team identifies trends, gathers feedback, and communicates the value of our products. From digital campaigns to trade shows, they ensure customers are informed, engaged, and confident in our expertise.
Fun Facts:
The Marketing team led by Carrie Fisher manages more than 150 projects at any given time, ensuring CDT stays innovative, engaged, and ahead of industry trends.
Did you know Marketing Generalist Stacy Viggiano is the wife of CDT President Nick Viggiano? In her role, she wears many hats, bringing her creativity, humor, and authenticity to the company’s communication initiatives.
IT: Empowering Precision with Technology
In today’s digital world, technology is integral to success. Our IT team ensures seamless communication, data security, and operational efficiency by managing robust networks and advanced software. Their work keeps CDT at the forefront of innovation, enabling precision and speed for our customers.
Fun Facts:
IT Director Jeremy Geier bridges the networks between our U.S. and U.K. facilities, enabling seamless and secure order processing and tracking between facilities.
Off the clock, Jeremy coaches the local, CDT-sponsored high school softball team in New Haven.
Finance: Driving Strategic Resource Management
The Finance team led by CFO Mike Brouwer ensures every resource decision is grounded in sound financial planning. They develop budgets, manage expenses, and forecast trends, allowing CDT to invest in resources needed for growth and innovation. Their expertise helps us maintain competitive pricing without compromising quality.
Fun Facts:
Did you know Accounting Manager Joseph Norris has been with CDT for 20 years? Joseph started as a part-time employee working with manual lathes on the shop floor. In 2014, he moved into a full-time role within the Electroplated team. In 2017, Joseph joined the Finance team and is instrumental with the many hats he wears.
Mike and Joseph both enjoy coaching sports outside of work.
Administration: Keeping TEAMS Running Smoothly
Behind every smooth operation is a team ensuring day-to-day activities run without a hitch. The Administration team provides essential support across departments, coordinating schedules, managing communications, and ensuring every detail is handled efficiently.
Fun Fact:
Amy Frecker at our front desk personally answers an average of 50 or more calls every day.
A Unified Effort for Superior Customer Service
Creating custom grinding tools for precision manufacturing applications is complex, but it’s made possible by the collaboration of diverse departments working toward a common goal: customer satisfaction. At Continental Diamond Tool, every team plays a important role in meeting and exceeding the demands of the industries we serve.
Whether it is our groundbreaking work in our grinding lab at CDT New Haven or our industry-leading processes in our 500-tank lab for electroplating with diamonds, it’s not just about what we make—it’s about how we work together to serve you better.
You’ll notice we share a love of teamwork and a spirit of camaraderie at CDT that extends beyond our workdays. Many of our team members coach or referee sports outside the office—be it basketball, softball, or other athletic programs—carrying forward the same principles of sportsmanship, collaboration, and high performance that we bring to serving our customers. These values are core to who we are, both on the shop floor and on the playing field.
Have questions about how we can help with your precision manufacturing needs? Contact us today to learn more about our commitment to excellence.
CDT’s Lab Evaluates Blaser Coolants in Flute Grinding Applications
Check out how we tested Blaser coolants on EVO hybrid bond wheels in CDT’s grinding lab to see which best enhances cutting, tool life, and quality in precision flute grinding.
At Continental Diamond Tool (CDT), we pride ourselves on pushing the limits of grinding technology. In one recent trial, The Grinding Chronicles team has partnered with Blaser Swisslube to test the performance of different coolants on our EVO hybrid bond grinding wheels. This experiment in CDT’s grinding lab aims to determine which coolant best enhances cutting performance, tool life, and workpiece quality in precision flute grinding applications.
Parameters for Success
Leading this effort is CDT Application Engineer Harrison Sheldon and CDT Engineering Consultant Jon VanSant, who are testing three different Blaser fluids under controlled conditions. They are measuring key parameters such as power, force, and grinding wheel wear while closely inspecting the visual quality of the workpiece for signs of burn or other surface finish issues.
“Our focus is on how the grinding wheel cuts, wears, and the resulting workpiece quality,” Jon explains. “By measuring parameters like power and force, we aim to collect data that can objectively compare the performance of each coolant under consistent conditions.”
Three representatives from Blaser joined Harrison and Jon last week at CDT’s lab: Senior Application Engineer Brett Reynolds from the New York plant, and Grinding Business Development Managers Tom Cappadona, also from New York, and Simon Stalder, representing Blaser’s headquarters in Switzerland. For this trial, Blaser has provided the coolant fluids, while CDT is supplying the EVO hybrid bond grinding wheels and the data collection equipment in the grinding lab. This setup ensures a comprehensive, scientific approach to analyzing performance with these coolants.
“When Tom approached us about this trial, we saw an opportunity to try something new with the equipment in our grinding lab,” says Harrison. “We’re excited to see how each formula stacks up to help the team at Blaser guide their customers in optimizing their process.”
Simon Stalder expressed his enthusiasm for the trial results, eager to share the findings with his engineering team in Switzerland. These results will provide valuable insights into how Blaser’s latest coolant technology enhances grinding performance and efficiency. As a global leader in metalworking fluids, Blaser delivers tailored formulas for every material, industry, and application.
Benefits of a Dynamic Testing Environment
The dynamic testing environment in CDT's grinding lab allows Harrison and Jon to adjust parameters on the fly, testing variables such as feed rate while maintaining consistent wheel speed. This enables them to evaluate the optimal feed rate range for each coolant type.
“One key advantage of running trials in the lab is the ability to collect objective data in controlled conditions,” says Jon. “Unlike in the field, where varied operator techniques can affect outcomes, our lab setting allows us to isolate variables and focus on actionable insights.”
While Blaser has come to CDT's lab primarily for the technical instrumentation and grinding know-how of our team, customers do not have to travel to take advantage of the lab’s capabilities. “CDT’s grinding lab is exceptionally flexible due to its portability. We frequently gather data directly from our customers’ processes by installing equipment at their site and analyzing it in our lab,” Harrison notes, “or we can simulate their operations on our machines and collaborate remotely to tweak their process.”
The expertise of Blaser’s application engineer, Brett Reynolds, has also been instrumental in these trials. “Brett brings a deep understanding of Blaser’s fluid formulation and their customer applications, which complements our grinding expertise,” adds Jon.
Trials on the Walter Helitronic Machine
As a 5-axis tool and cutter grinder, the Walter Helitronic is a purpose-built machine that is a centerpiece in CDT’s grinding lab and perfect for trials like this. Its versatility and precision are critical for evaluating different grinding configurations.
“The Walter machine is capable of thousands of functions, but it’s most commonly used for round cutting tools, making it perfect for flute grinding trials with our EVO Hybrid Bond fluting wheels,” Harrison says. “Its high precision, repeatability, and compatibility with advanced cooling systems make it the ideal platform for these tests.”
Jon elaborates, “The Walter allows us to make real-time adjustments to speed, feed rate, and pressure, which is essential for testing performance during these trials. Its automation and sensitive readings ensure accurate, repeatable results.”
The team at Blaser is currently reviewing the data gathered from last week’s trial and discussing how to incorporate the insights into future marketing and product development.
Accessing Our Grinding Lab Services
At CDT, we believe in the importance of real-world testing to optimize grinding processes and improve part quality. Our grinding lab is available for trials like these, whether you’re testing new grinding wheels or assessing some other metric of performance.
“Our team’s diverse areas of expertise ensures we can accommodate unique customer needs,” Harrison shares. “Whether it’s conducting tests in our lab or traveling to your site, we provide valuable solutions tailored to each challenge.”
If you’re interested in running a grinding trial with CDT, contact us with details about your process. We can recreate it in our lab or connect at your facility to gather data. From there, we develop testing parameters, share results, and make tailored recommendations for specific tools and production settings.
Learn more about Blaser Swisslube at:
Linkedin.com/company/blaser-swisslube
Youtube.com/user/blaserswisslube1
Brian VanHall Hired as CEO of Continental Diamond Tool
Continental Diamond Tool announces Brian VanHall as the new CEO to advance the company's mission of delivering high-quality, custom-engineered tooling solutions to customers around the world.
New Haven, Indiana – May 31, 2024 – Continental Diamond Tool is delighted to announce the hiring of Brian VanHall as the Chief Executive Officer, starting June 3, 2024. Founded in 1973, Continental Diamond Tool is a global leader in the design, manufacture, and application of precision grinding products for a multitude of industries.
Brian VanHall has been hired as the Chief Executive Officer at Continental Diamond Tool, starting June 3, 2024
As CEO of Continental Diamond Tool, Mr. VanHall is excited to advance the company's mission of delivering high-quality, custom-engineered tooling solutions to customers around the world. “I am honored to be entrusted by the Viggiano family and CDT team to help grow the legacy of excellence in developing and delivering innovative solutions for advanced manufacturing applications” said VanHall.
Mr. VanHall previously served as Executive Vice President with Ambassador Enterprises. With over 20 years of executive experience, Mr. VanHall brings a record of leading innovative projects, transformative programs, and strategic partnerships for multinational organizations to grow economic value, organizational effectiveness, and social impact. Brian received his Master of Business Administration (MBA) from Baylor University and holds graduate certifications in organizational leadership, corporate governance, strategic planning, and project management.
Nick Viggiano, President of Continental Diamond Tool, said, “We are excited to welcome Brian VanHall to the team and look forward to a future of continued excellence and growth with his leadership.”
For more information about our management team at Continental Diamond Tool, click here.
About Continental Diamond Tool Corporation:
Established in 1973, Continental Diamond Tool Corporation (CDT) is a premier manufacturer of precision tooling solutions for industries worldwide. With a legacy of technical expertise and innovation, CDT is renowned for its custom superabrasive grinding wheels and diamond dressing tools. CDT is also North America’s exclusive source for Krebs & Riedel conventional abrasive wheels, which are custom profiled at our facility. Headquartered in New Haven, Indiana, CDT operates a state-of-the-art 200,000 sq. ft. manufacturing center dedicated to delivering high-quality products and exceptional customer service. Learn more >
Continental Diamond Tool Enters Strategic Partnership with Krebs & Riedel
Continental Diamond Tool Corporation partners with Krebs & Riedel, becoming the exclusive source for their abrasive products in North America. Learn more about the collaboration in this article.
New Haven, Indiana – April 30, 2024 – Continental Diamond Tool Corporation (CDT) proudly announces its partnership with Krebs & Riedel, a global leader in the abrasives industry. This collaboration positions CDT as the exclusive North American source for Krebs & Riedel abrasive products within the USA, Canada, and Mexico.
Nick Viggiano, President of Continental Diamond Tool (left), and Florian Riedel, Managing Director of Krebs & Riedel.
Erik Van Meter, Senior Product Manager of Conventional Abrasives at Continental Diamond Tool and Krebs & Riedel’s official representative, expresses enthusiasm about the new partnership, stating, "We are thrilled about the high-quality products Krebs & Riedel will bring to the table. They are a well-respected name in conventional grinding wheels and have products for many industrial grinding markets which include automotive, aerospace, gear and medical."
The collaboration between CDT and Krebs & Riedel signifies a partnership deeply rooted in a shared commitment to excellence. For more than half a century, Continental Diamond Tool Corporation has consistently delivered technically superior precision grinding products across a variety of industries. As a thriving second-generation family business, CDT’s commitment to innovation and quality is reflected in its state-of-the-art North American manufacturing facility, which is undergoing a sizable expansion to cater to new product development and meet diverse customer needs. With this and a growing subsidiary in the United Kingdom, it has solidified its status as a premier worldwide manufacturer of custom superabrasive grinding wheels and diamond dressing tools.
Similarly, Krebs & Riedel is a family-owned enterprise headquartered in Bad Karlshafen, Germany, since 1885. It has a proud century-long legacy in providing quality abrasive products globally. With over 30 distributors and subsidiaries, K&R's dedication to customer satisfaction aligns seamlessly with CDT's founding principles. This partnership promises cutting-edge solutions and unwavering commitment to superior products and customer service in the abrasive products landscape. In this strategic move, CDT and Krebs & Riedel are poised to tackle the most critical tooling requirements of a growing market of customers.
“This partnership marks an exciting chapter for Continental Diamond Tool Corporation as we join forces with Krebs & Riedel to expand our product offerings in North America,” said Nick Viggiano, President of CDT. “We are proud to align with Krebs & Riedel's esteemed reputation and look forward to delivering exceptional abrasive products and unparalleled service to our customers across the continent and beyond.”
“With CDT we have found the partner who complements our high-performance products with superior service. From the first meeting we felt the same level of professionality and passion for grinding. I am convinced that our customers in North America will feel the same,” said Florian Riedel, Managing Director of Krebs & Riedel.
For more information about Continental Diamond Tool Corporation and its comprehensive range of precision grinding products, including those from Krebs & Riedel, please visit www.cdtusa.net/products.
Continental Diamond Tool Corporate Office in New Haven, Indiana, USA
About Continental Diamond Tool Corporation:
Established in 1973, Continental Diamond Tool Corporation (CDT) is a premier manufacturer of precision tooling solutions for a variety of global industries. With a legacy of technical expertise and innovation, CDT is renowned for its custom superabrasive grinding wheels and diamond dressing tools. Headquartered in New Haven, Indiana, CDT operates from a state-of-the-art 200,000 sq. ft. manufacturing facility dedicated to delivering high-quality products and exceptional customer service.
Krebs & Riedel Head Office in Bad Karlshafen, Germany
About Krebs & Riedel:
Family owned since its start in 1885, Krebs & Riedel (K&R) has been a prominent global player in the abrasive products industry. With a vast network of over 30 distributors, subsidiaries, sales companies, and representatives worldwide, Krebs & Riedel is renowned for its quality abrasive products and commitment to customer satisfaction.
Top 10 Reasons to Work Third Shift at CDT
From longer weekends to higher pay, check out the top ten reasons you should apply for a third shift position at CDT.
Here at Continental Diamond Tool, we take our work seriously, but that doesn’t mean we don’t have a sense of humor! Whether you think of third shift as a “late shift” or a “late show,” there are lots of great reasons to work nights at CDT.
From longer weekends to higher pay, watch the video below to see the top ten reasons you should apply for third shift at CDT.
Drumroll please…..
CDT Starting A New Third Shift
Continental Diamond Tool has experienced extensive growth in Three of their most popular product lines, and they are now adding a third shift to their schedule to increase production and continue to fulfill global orders in a competitive timeframe. Apply today >
Continental Diamond Tool Starting A New Third Shift, Now Hiring
Continental Diamond Tool has experienced extensive growth in three of their most popular product lines, and they are now adding a third shift to their schedule to increase production and continue to fulfill global orders in a competitive timeframe.
The new shift will consist of four 10-hour shifts per week, from 8 p.m. to 6 a.m. This third shift will begin as soon as the open positions are filled, which may be as soon as August. All positions are entry-level and require a high school diploma. Job training will be provided.
CDT fosters an innovative, team-oriented environment for their employees, who enjoy paid lunch breaks, competitive wages, and health insurance benefits, along with additional benefits and overtime opportunities, in a clean, climate-controlled environment.
In business since 1973, CDT is a leading producer in the global market for superabrasive grinding wheels and custom tooling. Their 128,000 sq. ft. manufacturing facility in New Haven, Indiana, utilizes the latest technology to serve numerous industries including medical, aerospace, power generation, and more.
Additional information and applications are available by calling 800-443-6629 or visiting CDTUSA.net/careers.