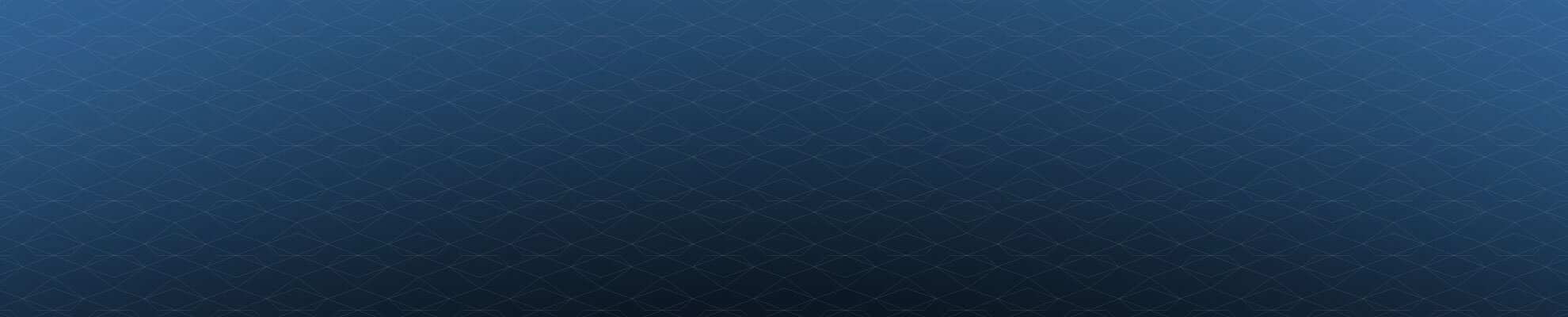
News and Resources
Browse by Category
Browse by Product
- All Dressing Products
- All Grinding Products
- CBN-Diamond Superabrasives
- Conventional Abrasives
- Diamond Lapping Compounds
- Diamond Rotary Dressers
- Diamond Stationary Dressers
- Hybrid Bond Grinding Tools
- Metal Bond Grinding Tools
- Plated Grinding Tools
- Resin Bond Grinding Tools
- Vitrified Bond Grinding Tools
CDT’s Lab Evaluates Blaser Coolants in Flute Grinding Applications
Check out how we tested Blaser coolants on EVO hybrid bond wheels in CDT’s grinding lab to see which best enhances cutting, tool life, and quality in precision flute grinding.
At Continental Diamond Tool (CDT), we pride ourselves on pushing the limits of grinding technology. In one recent trial, The Grinding Chronicles team has partnered with Blaser Swisslube to test the performance of different coolants on our EVO hybrid bond grinding wheels. This experiment in CDT’s grinding lab aims to determine which coolant best enhances cutting performance, tool life, and workpiece quality in precision flute grinding applications.
Parameters for Success
Leading this effort is CDT Application Engineer Harrison Sheldon and CDT Engineering Consultant Jon VanSant, who are testing three different Blaser fluids under controlled conditions. They are measuring key parameters such as power, force, and grinding wheel wear while closely inspecting the visual quality of the workpiece for signs of burn or other surface finish issues.
“Our focus is on how the grinding wheel cuts, wears, and the resulting workpiece quality,” Jon explains. “By measuring parameters like power and force, we aim to collect data that can objectively compare the performance of each coolant under consistent conditions.”
Three representatives from Blaser joined Harrison and Jon last week at CDT’s lab: Senior Application Engineer Brett Reynolds from the New York plant, and Grinding Business Development Managers Tom Cappadona, also from New York, and Simon Stalder, representing Blaser’s headquarters in Switzerland. For this trial, Blaser has provided the coolant fluids, while CDT is supplying the EVO hybrid bond grinding wheels and the data collection equipment in the grinding lab. This setup ensures a comprehensive, scientific approach to analyzing performance with these coolants.
“When Tom approached us about this trial, we saw an opportunity to try something new with the equipment in our grinding lab,” says Harrison. “We’re excited to see how each formula stacks up to help the team at Blaser guide their customers in optimizing their process.”
Simon Stalder expressed his enthusiasm for the trial results, eager to share the findings with his engineering team in Switzerland. These results will provide valuable insights into how Blaser’s latest coolant technology enhances grinding performance and efficiency. As a global leader in metalworking fluids, Blaser delivers tailored formulas for every material, industry, and application.
Benefits of a Dynamic Testing Environment
The dynamic testing environment in CDT's grinding lab allows Harrison and Jon to adjust parameters on the fly, testing variables such as feed rate while maintaining consistent wheel speed. This enables them to evaluate the optimal feed rate range for each coolant type.
“One key advantage of running trials in the lab is the ability to collect objective data in controlled conditions,” says Jon. “Unlike in the field, where varied operator techniques can affect outcomes, our lab setting allows us to isolate variables and focus on actionable insights.”
While Blaser has come to CDT's lab primarily for the technical instrumentation and grinding know-how of our team, customers do not have to travel to take advantage of the lab’s capabilities. “CDT’s grinding lab is exceptionally flexible due to its portability. We frequently gather data directly from our customers’ processes by installing equipment at their site and analyzing it in our lab,” Harrison notes, “or we can simulate their operations on our machines and collaborate remotely to tweak their process.”
The expertise of Blaser’s application engineer, Brett Reynolds, has also been instrumental in these trials. “Brett brings a deep understanding of Blaser’s fluid formulation and their customer applications, which complements our grinding expertise,” adds Jon.
Trials on the Walter Helitronic Machine
As a 5-axis tool and cutter grinder, the Walter Helitronic is a purpose-built machine that is a centerpiece in CDT’s grinding lab and perfect for trials like this. Its versatility and precision are critical for evaluating different grinding configurations.
“The Walter machine is capable of thousands of functions, but it’s most commonly used for round cutting tools, making it perfect for flute grinding trials with our EVO Hybrid Bond fluting wheels,” Harrison says. “Its high precision, repeatability, and compatibility with advanced cooling systems make it the ideal platform for these tests.”
Jon elaborates, “The Walter allows us to make real-time adjustments to speed, feed rate, and pressure, which is essential for testing performance during these trials. Its automation and sensitive readings ensure accurate, repeatable results.”
The team at Blaser is currently reviewing the data gathered from last week’s trial and discussing how to incorporate the insights into future marketing and product development.
Accessing Our Grinding Lab Services
At CDT, we believe in the importance of real-world testing to optimize grinding processes and improve part quality. Our grinding lab is available for trials like these, whether you’re testing new grinding wheels or assessing some other metric of performance.
“Our team’s diverse areas of expertise ensures we can accommodate unique customer needs,” Harrison shares. “Whether it’s conducting tests in our lab or traveling to your site, we provide valuable solutions tailored to each challenge.”
If you’re interested in running a grinding trial with CDT, contact us with details about your process. We can recreate it in our lab or connect at your facility to gather data. From there, we develop testing parameters, share results, and make tailored recommendations for specific tools and production settings.
Learn more about Blaser Swisslube at:
Linkedin.com/company/blaser-swisslube
Youtube.com/user/blaserswisslube1
Understanding the Distinction Between CBN and Aluminum Oxide Abrasives
Uncover the secrets behind top-notch results in grinding and machining of tough steels and metals. Discover the unique properties of Cubic Boron Nitride (CBN) and Aluminum Oxide and learn how to choose the right abrasive for optimal efficiency and precision.
Are you ready to explore the fascinating world of abrasives? In manufacturing, we often encounter Superabrasives and Conventional abrasives. In the Superabrasives corner, we have Diamond and Cubic Boron Nitride (CBN), and their common Conventional abrasive counterparts are Silicon Carbide and Aluminum Oxide. Each serves a specific purpose. What makes CBN and Aluminum Oxide stand out is their exceptional ability to tackle those stubborn steels and metals that can't stand Carbon.
In this blog, we'll explore the properties and applications of CBN and Aluminum Oxide abrasives. Discovering their unique characteristics will help you choose the right abrasive for your specific machining needs, ensuring efficiency and top-notch results. Whether you're working with hardened steels or softer metals, the right abrasive is the key to achieving your desired outcome in grinding and machining. So, let's dive in and unlock the true potential of CBN and Aluminum Oxide abrasives.
What is CBN?
CBN is a synthetic Superabrasive known for its incredible hardness, high thermal conductivity, and thermal stability. Originally released with the trade name Borazon from GE Superabrasives, its cubic crystal lattice structure is similar to Diamond, giving it remarkable abrasive properties. With a hardness close to 10 on the Mohs scale, CBN excels in machining tough materials that require precision grinding. Its chemical composition and high thermal stability prevents chemical reactions and premature breakdown under high temperatures, when grinding ferrous metals and high-temperature alloys. What's more, because CBN doesn't react with ferrous materials, it doesn’t alter or change their properties resulting in longer life in use when ground with CBN.
CBN is a game-changer when grinding hardened ferrous alloys or super alloys that are sensitive to heat. It efficiently grinds hardened steels while maintaining accuracy and surface finish. Plus, it's a favorite for grinding ferrous metals like cast iron and stainless steel, ensuring clean and precise results without chemical alterations. CBN is a must-have tool for achieving precise and efficient outcomes in critical machining tasks.
What is Aluminum Oxide?
Aluminum Oxide, also known as alumina, is a versatile Conventional abrasive. With high hardness and toughness, it is available in various grit sizes, making it perfect for a wide range of machining and finishing applications. Though not as hard as CBN, Aluminum Oxide is fantastic for soft metals, wood, and non-ferrous materials. While it may not match the precision of Superabrasives, it's still a reliable choice for many tasks.
In the machining industry, Aluminum Oxide is the go-to for grinding soft metals like aluminum, brass, and copper. It performs beautifully with non-ferrous materials such as bronze and titanium, without causing any chemical interactions. Its role in achieving desired surface finishes across various industries, from automotive to aerospace, is unparalleled.
Key Differences Between CBN and Aluminum Oxide Abrasives
While CBN and Aluminum Oxide both play significant roles in grinding and machining operations, they have many distinct properties that set them apart.
Crystal Structure and Hardness: CBN's crystal lattice structure is similar to Diamond, resulting in exceptional hardness and wear resistance. Aluminum Oxide, while still hard, has a lower hardness than CBN, making it more suitable for soft metals and certain alloys.
Heat Resistance and Thermal Conductivity: CBN exhibits superior heat resistance and thermal conductivity compared to Aluminum Oxide, making it perfect for grinding high hardness and heat sensitive alloys.
Material Compatibility and Reactivity: Both CBN and Aluminum Oxide are chemically inert with ferrous materials whereas Diamond and Silicon Carbide are not, thus why they are the abrasives for ferrous metals.
Cost and Practicality: CBN grain costs significantly more than Aluminum Oxide grain, resulting in higher grinding wheel prices. Because of higher hardness and better thermal conductivity, CBN wheels can provide lower grinding costs in applications where high workpiece hardness and thermal properties need to be maintained. In cases of grinding soft steels and low volume production, the lower wheel price of Aluminum Oxide makes it a more competitive option.
Safety Considerations and Handling
Whether you choose CBN, Aluminum Oxide, or another solution for your abrasive, ensuring safety during grinding and finishing processes is essential. Proper machine guarding, eye and respiratory protection, proper dust/mist extraction, and careful handling and storage of abrasives are crucial to protect workers and maintain a clean and safe work environment.
Selecting the Right Abrasive for Specific Applications
Choosing the right abrasive for your specific machining needs is vital to achieving optimal results. Making an informed decision will ensure efficient, accurate, and cost-effective grinding and finishing processes. Some factors to consider include:
Workpiece Material Characteristics: Soft metals like aluminum, brass, copper, and mild steels may need moderate hardness abrasives like Aluminum Oxide to prevent excessive material removal, while harder materials like hardened steels and high-temperature alloys such as inconel and hardened Stainless Steel require abrasives with superior hardness and high thermal conductivity like CBN for precise and efficient cutting and grinding.
Machining Operations and Efficiency: Superabrasives like CBN are preferred for high-precision tasks where tight tolerances and maintaining material properties are paramount, while conventional abrasives like Aluminum Oxide offer lower cost solutions for general grinding of mild steel and soft metals.
Surface Finish and Material Removal Rates: Superabrasives like CBN excel in production applications of hardened steels and Superalloys that are sensitive to heat, , while conventional abrasives like Aluminum Oxide are effective in low volume applications and for grinding of soft metals.
Tooling and Machinery Considerations: Abrasive selection also needs to account for machinery and tooling capabilities. The truing and dressing of Superabrasive and Conventional Abrasive grinding wheels can be different and require different tools (stationary or rotary dressers of different configurations). Because of the difference in hardness between CBN and Alumina, Alumina being much lower, the amount of grinding debris resulting from wheel wear during grinding can be 100-300 x’s greater with the conventional wheel, which in turn needs to be disposed of. .
Both CBN and Aluminum Oxide abrasives offer distinct advantages in grinding and machining. Considering their unique properties with specific application requirements will lead to efficient and precise processes, ensuring optimal results and safety in the workplace. And if you ever need assistance, our grinding experts at CDT are here to help. Whether it's Superabrasives or Conventional abrasives, we can help find the perfect solution for your process.
Meet The Next Generation In Hybrid Bond Technology: Ultra High Performance Grinding For The Cutting Tool Industry
At Continental Diamond Tool we are proud to announce that we have officially unveiled our latest breakthrough technology in hybrid bond products – the EVO Hybrid Bond.
At Continental Diamond Tool we are proud to announce that we have officially unveiled our latest breakthrough technology in hybrid bond products – the EVO Hybrid Bond – at the much anticipated Precision Machining Technology Show this past April 2023.
What is EVO Hybrid Bond?
A game-changer in the precision grinding industry, EVO is a custom-designed bond that delivers ultra-high performance results that are impossible for our competitor’s standard Resin Bond wheels to match.
This bond is a new and improved version of CDT's Resin Hybrid Bond, designed specifically to cater to the needs of Tool and Cutter Grinding.
One of the key benefits of EVO is its superior performance that helps produce high-quality cutting tools faster and more efficiently than its past versions.
The bond is uniquely formulated to achieve faster cycle times without compromising on the wheel edge, making it an ideal choice for:
Flute from solid
Regrind
Gash and end work
And relief
What are the benefits of EVO Hybrid Bond?
When you opt for CDT’s EVO Hybrid Bond technology, you can expect superior results in both form retention and surface finish because of its free cutting action.
Additionally, the EVO bond is self-sharpening. This type of technology ensures the life of your wheel is longer-lasting, as is the dressing interval.
It can also withstand much higher temperatures while still maintaining its stability, which makes high material removal rate not only possible, but incredibly precise.
Because CDT’s EVO Hybrid Bond offers excellent heat dissipation capabilities (while ensuring low and consistent power consumption) it enhances your overall efficiency and productivity of the grinding process.
It’s also a much more sustainable option. The wheel profile lends itself to a longer-lasting type of technology that reduces your grinding process costs in the long-term.
What sets EVO Hybrid Bond apart from the competition?
Beyond all of the benefits listed above, what sets EVO apart from other superabrasive grinding products is its unique blend of Resin Bond and Metal Bond.
Available exclusively through CDT, this customizable type of bond is designed specifically to deliver cutting edge results that standard wheels cannot hope to compete with.
For the high precision cutting tool industry, EVO is a long-awaited solution to many common grinding challenges.
The bond offers a faster cycle time, less dressing, and greater performance. It is an ideal solution for those looking to improve their grinding process and achieve their goals.
At CDT, we are committed to providing the latest technology solutions to help the precision cutting tool community overcome their machining challenges. EVO Hybrid Bond is a testament to our commitment, and we are confident that it will transform your grinding process and help you stay ahead of the competition.
Resin Hybrid Grinding Wheels are 'Gold' for the Cutting Tool Industry
Last month CDT released its response to the competition's hybrid wheels to handle the extreme cutting conditions in tool grinding. Cutting Tool manufacturers have been pleasantly surprised by the results.
Last month CDT released its response to the competition's hybrid wheels to handle the extreme cutting conditions in tool grinding. Cutting Tool manufacturers have been pleasantly surprised by the results.
In a head-to-head comparison, the competitor's fluting was originally done in two passes. The CDT Hybrid Bond achieved a single pass at double the feed rate with no damage to the workpiece while achieving a 25% increase in finish.
With equally outstanding primary and secondary grind results, the Hybrid Bond increased the primary and secondary operations by four times while continuing to produce a better finish.
The Hybrid Series for Tool & Cutter Grinding uses Advanced Bond technology, allowing for a quicker grind without losing the wheel edge. Flute from solid, regrind, gash and end work, and relief. Cutting Tool manufacturers will find:
Excellent precision at the highest feed rates
Increased productivity while lowering process costs
Superior wheel life and long dressing interval
Withstands cutting forces from high-speed, high-temperature applications
Because the Hybrid bond is not your standard “one size fits all” but is tailored to the specific grinding application, it allows for the highest quality tool in the most efficient amount of time in the Cutting Tool industry. This level of customization is unique to CDT's newest bond.
These one-of-a-kind properties improve the performance of the CNC Tool and Cutter Grinder in many ways:
Free cutting action with superior form retention and surface finish
Self sharpening bond lengthens wheel life and dressing interval
High material removal rate with high temperature stability
Maximum heat dissipation with low and constant power consumption
Optimal wheel profile stability lowers costs due to wear
If it's time to replace your old conventional worn parts with high quality precision grinding wheels and tools, you should consider CDT's Hybrid Series for Tool & Cutter Grinding. Backed by more than 40 years of superior craftsmanship and expertise in this field, CDT products are made in America and generally ship in 15 days. CDT customer service techs are happy to look through the parameters of your project, make recommendations, and supply a competitive quote - call 800-443-6629 for more information.