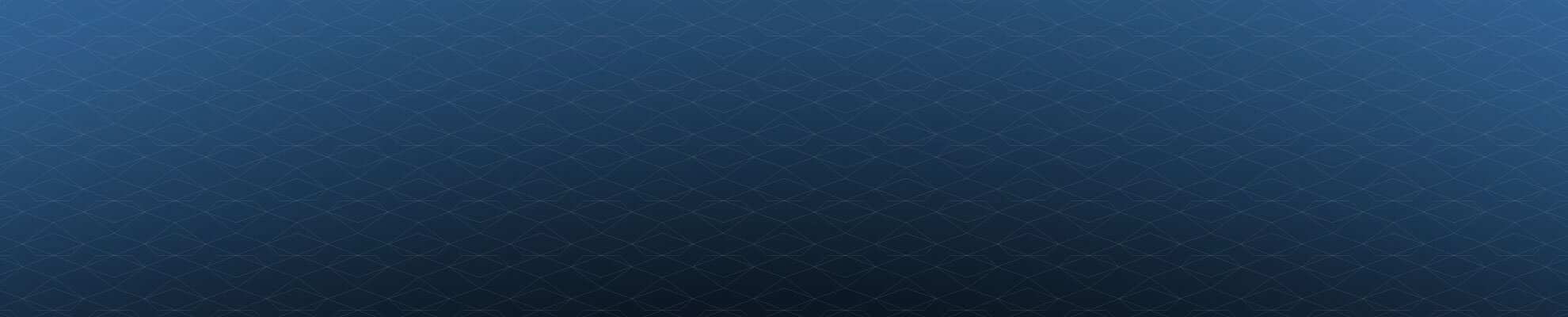
News and Resources
Browse by Category
Browse by Product
- All Dressing Products
- All Grinding Products
- CBN-Diamond Superabrasives
- Conventional Abrasives
- Diamond Lapping Compounds
- Diamond Rotary Dressers
- Diamond Stationary Dressers
- Hybrid Bond Grinding Tools
- Metal Bond Grinding Tools
- Plated Grinding Tools
- Resin Bond Grinding Tools
- Vitrified Bond Grinding Tools
Core Matters: How Different Wheel Body Materials Impact Grinding
Learn how grinding wheel core materials like steel, aluminum, and carbon fiber impact performance, precision, and cost to optimize your grinding applications.
When using superabrasive grinding wheels in precision manufacturing, selecting the right abrasive, bond type, and wheel core material is critical for optimal grinding performance and wheel life. While abrasives and bond types often take center stage, the wheel core can be equally important. The core material is the foundation that provides structural support and stability. The right core material ensures high performance while preventing machine strain, excessive grinding wheel wear, and unnecessary cost. But how do you determine the best core material for your specific needs?
In Episode 10 of The Grinding Chronicles, CDT Engineering Manager Jeff Wirth breaks down the essential properties of core materials and how they influence grinding applications. Watch the video or read the article below to learn how to choose the best option for your application.
The Grinding Chronicles - Episode 10
Selecting the Right Core Material for Grinding Wheels
The core of a superabrasive grinding wheel does more than just hold the abrasive—it directly impacts machine efficiency, grinding precision, and tool longevity. Choosing the right core material not only optimizes performance but also helps prevent unnecessary damage to the wheel, machine, and workpiece while enhancing operator safety.
Common core materials for superabrasive grinding wheels include metals—such as steel, aluminum, and copper—as well as non-metals like ceramics and resin composites. Ceramic or vitrified cores are commonly found in conventional abrasive grinding wheels and are also used in some superabrasive grinding wheels. Resin composite cores may be made from materials like bakelite, abrasive composites, or carbon fiber. Each of these materials has unique properties that affect grinding performance, and understanding their characteristics helps manufacturers make more informed decisions.
Understanding Core Material Properties
Density – Defined as mass per unit volume, density directly affects the weight of a grinding wheel. Heavier cores put added stress on machines and spindle bearings, which is why large-diameter grinding wheels are often designed with lighter core materials like carbon fiber, bakelite, or ceramic. An overly heavy wheel can reduce machine longevity, increase energy consumption, and pose handling risks for operators, making weight an important consideration for both performance and safety.
Expansion – Core materials expand due to heat and mechanical forces, which can impact grinding accuracy. Minimizing expansion is crucial for applications with tight tolerances, as it helps prevent wheel distortion and ensures consistent precision. Expansion occurs in two forms:
Mechanical Expansion: At high speeds, some core materials naturally expand due to centrifugal forces. Materials with high tensile strength resist this growth, maintaining stability and accuracy over time.
Thermal Expansion: Heat generated during grinding can cause materials to expand, leading to dimensional changes and reduced precision. Materials with low thermal expansion coefficients are essential for consistently achieving tight tolerances.
For high-speed and high-precision grinding applications, grinding wheels with cores made from high-tensile steel, carbon fiber, or vitrified ceramic often perform better. These materials minimize mechanical and/or thermal expansion, ensuring consistent performance, reduced deformation, and greater accuracy under extreme conditions.
Thermal Conductivity – This property determines how well a core material dissipates heat. Efficient heat transfer prevents thermal damage (burning) to the workpiece, improves surface quality, and extends tool life. Metal materials like Copper and Aluminum with high thermal conductivity remove heat, leading to lower wear and improved performance in high heat applications such as fluting drills.
Modulus of Elasticity (MOE) – This measurement indicates a material’s ability to resist deformation under stress. A higher MOE means the material is stiffer and less likely to flex or deform. Steel has a very high MOE. This can be beneficial for applications with high grinding forces that require tight tolerances, as a flexible core can introduce inconsistencies in grinding performance.
Comparing Core Materials: Strengths and Weaknesses
Each core material offers specific advantages and drawbacks. Here’s how some of the most common materials compare:
Steel is strong, durable, and resistant to mechanical expansion. However, its heavy weight can strain machinery.
Aluminum is lighter and often more affordable than steel, with higher thermal conductivity and resistance to corrosion. However, it has significantly higher thermal expansion compared to steel and other materials.
Copper offers excellent thermal conductivity and a high modulus of elasticity (MOE), but its weight and cost make it less suitable for large grinding wheels.
Ceramic is lightweight, cost-effective, and resistant to expansion, but low thermal conductivity and high stiffness or brittleness can be a drawback.
Resin composites, including bakelite, are affordable and lightweight. However, they lack stiffness and high thermal conductivity, making them more susceptible to expansion and heat buildup in high-force grinding applications.
Carbon fiber is ideal for demanding applications due to its high stiffness and low weight. However, it tends to trap heat and is more expensive than other materials.
Choosing the Right Core Material for Your Application
Selecting the best core material depends on several factors, including the type of grinding being performed, the machine’s limitations, and cost considerations. For example:
Flute grinding and medical drill bits operate at traditional speeds with lower grinding forces. This means that a wide variety of core materials can be used without significant performance issues. In these cases, ceramic cores are often recommended because they provide an excellent balance of cost and functionality.
High-speed applications like camshaft grinding generate significant heat and grinding forces. This makes high-stiffness materials like carbon fiber or high-tensile steel essential to be able to perform effectively and safely.
Hybrid or combination cores are an innovative solution for balancing weight, stiffness, and cost. This approach involves layering or combining different materials to optimize performance while keeping costs manageable. For instance, a steel core can be reinforced with carbon fiber to reduce weight without sacrificing strength.
Practical Considerations in Core Material Selection
Beyond material properties, cost plays a major role in selecting the right core material for grinding wheels. While core materials like carbon fiber and vitrified ceramic are both resistant to mechanical and thermal expansion and lighter weight, they come at very different price points. Once all process requirements are met, cost is usually the deciding factor, as manufacturers balance performance needs with material costs to avoid unnecessary expenses.
Budget-Friendly Options – Ceramic and resin composites provide cost-effective solutions for applications with lower grinding forces and minimal heat generation. These materials perform well in traditional grinding operations without adding unnecessary expense.
Mid-Range Solutions – Aluminum and standard steel cores offer a balance between affordability and durability. These materials are commonly used in medium-duty grinding applications where moderate strength and thermal properties are required, optimizing cost per part without sacrificing performance.
Premium Core Materials – High-tensile steel and carbon fiber provide top-tier performance, making them ideal for high-speed and high-force applications. While their higher price point increases the initial cost of the grinding wheel, their longevity and reliability often justify the investment by reducing long-term cost per part through extended tool life and efficiency gains.
When selecting a core material, it is essential to consider not just the upfront cost but also long-term savings from reduced machine wear, improved grinding efficiency, and longer tool life. CDT’s engineering team can help assess cost-effectiveness based on your specific grinding application, ensuring the best balance between performance and cost per part.
Optimize Your Grinding Wheel Performance with CDT
Choosing the right core material is critical for achieving consistent, high-performance grinding results. Whether you're working with grinding applications for heavy-duty industrial engine components or high-precision medical tool manufacturing, the engineering team at Continental Diamond Tool is ready to assist in customizing a grinding wheel with the materials that are best for your needs.
If you have questions about selecting the best core material for your specific application, CDT’s engineers are here to help. Reach out to TheGrindingChronicles@cdtusa.net for expert advice.
Check out more videos from The Grinding Chronicles and follow CDT on Linked In for the latest news in grinding technology.
Celebrating Our Apprentices
Apprenticeships at CDT offer hands-on experience, critical skills, and leadership opportunities—more than training, they’re a launchpad for a lifelong career.
CDT Ltd.'s current and former interns (left to right): Corey Lloyd-Jones, Joe Bowles, Stephanie Hughes-Jones, Daniel Hughes-Jones, and Rhys Butler.
Investing in the Future: Celebrating Our Apprentices for National Apprenticeship Week
At Continental Diamond Tool (CDT), we take great pride in nurturing the next generation of engineers through our apprenticeship programs. In celebration of National Apprenticeship Week in the U.K., we’re highlighting the inspiring journeys of five apprentices at our manufacturing center in Wales. Read on to see how these talented individuals have developed their skills, grown within the company, and are shaping the future of engineering.e.”
From Apprentice to Supervisor – Joe Bowles’ Journey
Joe Bowles began his career with Continental Diamond Tool Ltd. in September 2007 as an engineering apprentice. Over the years, his dedication and willingness to learn saw him progress into new roles, gaining invaluable experience along the way. Today, he is the Supervisor of the Grinding Department, where he leads a skilled team and ensures high standards of quality and precision.
Reflecting on his journey, Joe shares:
"From an apprentice 17 years ago to a supervisor, my path has been driven by hard work and the support of a company that values growth, innovation, and investment in people. I look forward to furthering my career with CDT and being part of its bright future."
Joe’s success is a testament to the long-term benefits of apprenticeships, illustrating how they can open doors to leadership and career progression.
Daniel Hughes-Jones – A Key Player in CNC Machining
Daniel joined CDT Ltd. in March 2021, quickly making an impact in the CNC Machining Department. He successfully completed his HNC in Engineering, further strengthening his knowledge and technical expertise. Now, as a key team member, he operates multiple CNC machines and plays an important role in training new apprentices.
"My apprenticeship at CDT provided me with vital knowledge and a developed skill set, and I’m grateful to pass on my knowledge and experiences to the next generation of apprentices." – Daniel Hughes-Jones
Daniel’s ability to mentor new apprentices showcases the value of experienced employees sharing their knowledge, ensuring a strong and skilled workforce for the future.
Corey Lloyd Jones – Building a Strong Foundation
Corey started his apprenticeship with CDT Ltd. in September 2023 and is currently in his second year, working towards his HNC in General Engineering while also completing a Level 3 NVQ. With a strong ambition to learn, Corey is eager to develop his expertise across multiple machines and broaden his engineering knowledge.
"After finishing my apprenticeship, I would like to progress further within the company and learn more skills on more machines. I chose this career path as it looked like a good challenge. I am doing the general engineering HNC course because it opens up a lot of opportunities for me in the future, rather than having just mechanical or electrical HNC." – Corey Lloyd Jones
Corey’s enthusiasm for engineering showcases how apprenticeships provide a solid foundation for career growth, allowing young professionals to tailor their learning to suit their ambitions.
Rhys Butler & Stephanie Hughes-Jones – The Next Generation of Engineers
Rhys Butler and Stephanie Hughes-Jones, Daniel’s younger sister, are the newest members of CDT Ltd.’s apprenticeship program, having joined in September 2024. Though early in their careers, both are already embracing the challenges and opportunities that come with learning on the job.
Rhys shares his thoughts on his apprenticeship so far:
"I've been on my apprenticeship for around seven months now, and I've thoroughly enjoyed it because it has provided hands-on experience, and a deeper understanding of how complex systems come together. The opportunity to apply theoretical knowledge in real-world settings has been both challenging and rewarding. I've gained valuable skills in problem-solving, teamwork, and technical expertise, which have made me more confident in my abilities. Looking ahead, I would love to further develop my expertise in engineering and continue to grow in a role where I can contribute to impactful projects." – Rhys Butler
Stephanie, who was drawn to engineering for its balance of hands-on work and intellectual challenge, shares her experience:
"I chose engineering because I like jobs that are both physically challenging and mentally interesting. My apprenticeship helps me improve my skills as a machinist while giving me chances to keep learning and growing." – Stephanie Hughes-Jones
Their journeys emphasize how apprenticeships provide real-world experience, technical expertise, and career-building opportunities from day one.
Apprenticeships are more than just training—they’re a launchpad for a successful career. They provide a solid foundation for career progression, hands-on experience, and the opportunity to develop vital skills in a fast-paced, innovative environment.
The apprentices above are prime examples of what can be achieved through dedication, hard work, and the right support. From those just starting out to those who have grown into leadership roles, their journeys highlight the value of apprenticeships and the opportunities they create.
👉 Interested in an apprenticeship or know someone who is? CDT Ltd. works closely with Coleg Llandrillo to identify promising candidates for our highly competitive engineering apprenticeship programme. Each year, we offer placements to 2 to 3 students. The next apprenticeships will begin in September 2025. If you’re interested, we encourage you to explore Coleg Llandrillo’s Engineering Programme as the best route to be considered for a future opportunity with us. Learn more about Coleg Llandrillo here: https://www.gllm.ac.uk/
Continental Diamond Tool Limited (CDT Ltd.), based in Kinmel Bay, Rhyl, U.K., is the European subsidiary of Continental Diamond Tool Corporation, headquartered in New Haven, Indiana, U.S.A. For more than 40 years, CDT Ltd. has been a leader in diamond rotary dresser technology, originally operating as Consort Precision Diamond. Since joining CDT, the company has expanded its product line, delivering high-performance diamond plated grinding wheels and other premium superabrasive products to customers worldwide.
Global Growth and Local Jobs Spurred by Cutting Edge Investments at Kinmel Bay Facility
Cllr Nigel Smith visited CDT Ltd. earlier this month to see how £100,000 from the UK Shared Prosperity Fund is driving innovation, growth, and 40 new jobs in North Wales.
Cllr Nigel Smith (left), Conwy Council’s Cabinet Member for Sustainable Economy, visits with Production Manager Justin Hughes (right), showcasing one of the precision-engineered tools made possible by our new cutting-edge equipment, funded in part by the UK Shared Prosperity Fund secured with the help of Conwy Council.
A precision engineering company in North Wales is gearing up for global growth by investing £250,000 in cutting edge equipment.
Recruitment is also underway at Continental Diamond Tool (CDT) in Kinmel Bay as part of an ambitious expansion plan that will create 40 new jobs.
It’s all preparation for a move next year to a 30,000 sq ft factory nearby that’s three times the size of the current premises on the Tir Llwyd Industrial Estate.
Overall, the firm’s Indiana-based American owners, who took it over six years ago, are pumping £4 million into the company to triple production capacity and start making new products.
The niche company specialises in the manufacture of diamond-encrusted rotary dressers and grinding wheels, with tolerances of down to 1,000th of a millimetre in terms of accuracy.
It’s one of only two similar outfits in the UK and supplies a range of manufacturing sectors, including aerospace, automotive, medical and semi-conductors.
The company’s customers include blue chip corporations like Rolls Royce and Tenneco, with more than 60 per cent of the products being exported.
According to the loyal workforce, the investment is the “perfect present” for the company that’s celebrating its 40th anniversary this year.
It was also music to the ears of Cllr Nigel Smith, Conwy Council’s cabinet member for Sustainable Economy, who is one of three councillors who represent Kinmel Bay on the authority.
The council helped CDT secure £100,000 in funding from the UK Shared Prosperity Fund towards the cost of the new equipment.
He came on a visit to see how the money had been spent on “space age kit”, including a high tech machinery centre, lathe and inspection equipment.
Cllr Smith said: “What they do is very impressive, both in terms of the state-of-the-art technology and the high skill employment they provide in Kinmel Bay.
“It’s fantastic that they’re selling their world-leading products to an international market and they have a raft of blue chip customers like Rolls Royce.
“Over the years there has been a good relationship between the company and the council’s business development team and long may that continue.
“We were delighted to be able to help in securing £100,000 towards the cost of these cutting edge machines.
“It’s impressive, top-of-the-range technology and the level of precision they work to is mind-boggling – their tolerances are within microns. It’s engineering of the highest pinnacle.
“With them moving now to larger premises, I’ll be speaking to our team if there is anything more we can do to help them moving forward to help them grow and expand.
“Employment is a key issue in Conwy so have foster and support business where we can to retain our young people.
“It’s good to see the emphasis on training here and the apprenticeships, helped by the fact that they have a very good relationship with the local college.
“It’s always been a great company and there is now a new momentum under the American ownership and it’s very pleasing to see them invest in Kinmel Bay and that will pay dividends.
“The excellent legacy of the original company is now being turbo-charged by the Americans.
“It’s a company with ambition and it’s plain to see how committed the team are here – everybody has a good work ethic and it bodes very well for the future.”
Cllr Smith’s visit was hosted by Production Manager Justin Hughes, whose father was one of the founders of the original company, Peter Hughes.
Justin said: “In this latest investment we have spent £250,000 on the three machines and it’s well in excess of £1 million just on new equipment in the last two or three years.
“We’re very grateful to Conwy Council for their help in facilitating the £100,000 that’s come from the UK Shared Prosperity fund. It’s made a massive difference because it enables us to employ the people to use those machines.
“The skill required by the people we have to do that is of the highest order and is just as important as the machine.
“Training and developing those people is just as key as our processes and our high precision machinery so working with the engineering centre at the local college is a big help.
“I am immensely proud of the company’s legacy and the way things are moving forward. It’s in my blood, this company.
“These are really exciting times with the move to the larger premises which will enable us to have new product lines.
“Continental Diamond Tool are the third biggest superabrasives supplier in the USA and they are looking to become the biggest.
“The American side of the business is growing at a rate of 30 per cent a year and we are the European arm and they are looking to us to emulate that success over here.
“We are developing a name for ourselves against the big multi-national household names and we are becoming one of those names.
Finance Manager Michaela Lawton added: “The expansion into the new premises will enable us to increase capacity and the number of products we make so the sky is the limit.
“All this is happening in the year we are celebrating our 40th anniversary and the American side of the company is celebrating its 50th.
“We’ve got a great team of people here and there’s a shared pride in what we’re achieving.
“The expansion will create another 40 jobs and we have started to recruit people because of the skill sets required and the time it takes to train them.
“We’ve had a steady number of new employees joining us, particularly over the last four or five months so we can get all our ducks in a row.
“We make our products to 1,000th of a millimetre in terms of accuracy so we have to conduct the whole operation with the same level of exceptional quality.”
CDT Ltd. Unveils £4m Expansion Creating 40 New Jobs
Continental Diamond Tool has announced a £4 million expansion plan at its North Wales operation that will double the workforce there by creating 40 new jobs and triple production.
From left: CDT Ltd. Managing Director Jeff Wirth, Finance Manager Michaela Lawton, General Manager Troy Giacherio, Production Manager Justin Hughes, President of Sales Shane Vardaman, and Director Nick Viggiano stand outside the 30,000 sq. ft. factory that the North Wales operation will soon be occupying.
A fast-growing precision engineering firm has announced a £4 million expansion plan that will double the workforce at its North Wales operation by creating 40 new jobs and triple production.
The investment by the American owners of Continental Diamond Tool (CDT) will include moving to a 30,000 sq ft factory that’s nearly three times the size of its current premises in Kinmel Bay and is less than half a mile away on the Tir Llwyd Industrial Estate.
The move is being hailed by staff as the “perfect birthday present” for the North Wales operation which is celebrating its 40th anniversary this year, having been founded as Consort Precision Diamond in 1984, specialising in the manufacture of diamond-encrusted rotary dressers and grinding wheels.
The niche outfit – still one of only two similar companies in the UK – supplies a range of manufacturing sectors, including aerospace, automotive, medical and semi-conductors.
Its products are used in Boeing 777 and 787 Dreamliner aircraft, as well as the Airbus range A330-A380 whose wings are made at the giant Airbus factory in Broughton in Flintshire.
The firm was taken over and rebranded in 2018 by CDT which has its headquarters in New Haven, Indiana.
News of the investment was delivered by company President Nick Viggiano, during his visit to the Kinmel Bay site, along with Shane Vardaman, CDT’s President of Sales.
The bigger factory will enable the company to increase the range of products they make, adding several new types of high precision grinding wheels.
Nick Viggiano said: “Things have worked out even better than I thought and the investment is a real big vote of confidence in the workforce here because they have a similar work ethic and there’s good camaraderie between everyone.
“We expect to be three times the size we are in a few years’ time because there is a very big market for the products we are going to bring over here.
“We expect a swift ramp-up. Given our extensive expertise with these products in the States, we can help the team over here to quickly hit the ground running.
“The new building is like a blank canvas so we can set everything up exactly the way we want, so we’re very excited about it.”
It was as sentiment endorsed by the American Managing Director, Jeff Wirth, who said: “This investment has been a long time coming, with six years of preparation and teambuilding leading up to this moment.
“Our Kinmel Bay team, known for their rotary dressers, has already started producing electro-plated products on a small scale.
“Moving to the new building that’s nearly three times the size will give us the space to expedite that process. Additionally, we plan to manufacture two vitrified products and a hybrid product in the new space.
“This is a big step and it goes hand in hand with the expansion we’re doing in the United States.
“It comes down to Nick having a belief in the people and the team. This is going to put rocket boosters under the company to continue with the growth trajectory.
“With everything consolidated under one roof, we will get to lay it out to maximise efficiency instead of having to work around the nooks and crannies of the current building.
“The accommodation will also be improved for the employees with nice fresh locker rooms and a cafeteria.
“Nick has a supercharged, can do mentality and we expect to be up and running in the new building in the first quarter of next year.”
According to Finance Manager Michaela Lawton, the Kinmel Bay staff were delighted to have the opportunity to finally meet Nick and Shane in person.
She said: “We have a solid leadership team here and a fantastic workforce that has the full backing of our American owners and it’s clear that the team here has proved itself worthy of this massive investment.
“It’s going to be a process over the next few years, with recruitment, upskilling and training and a lot of capital expenditure on fitting out the new factory with the specialist equipment that we need.
“We are aiming to follow in the footsteps of our American counterparts who have seen huge growth over the last 10 years.
“They’ve gone from our current size to employing over 200 people and we want to follow the same path.”
Justin Hughes, the production manager in Kinmel Bay, has worked at the Kinmel Bay site for 17 years and is the son of the retired technical director, Peter Hughes, who was among the founders of Consort Precision Diamond.
He said: “The takeover has been a marriage made in business heaven because the operations on both sides of the Atlantic dovetail perfectly with each other.
“The news about the investment is incredibly exciting and is the perfect birthday present as we celebrate our 40th anniversary.
“It will undoubtedly inspire us to reach even greater heights and become a truly global player. The sky really is the limit.”
An Essential Guide to Grinding Process Optimization for Boosting Performance in Precision Manufacturing
Optimize your grinding process with expert tips on speeds, feeds, Q-prime, and advanced bond technology to boost efficiency in precision manufacturing.
To stay competitive in precision manufacturing, grinding operations require continuous improvement in performance and efficiency. Understanding the factors that influence grinding, such as speeds, feeds, and material removal rates, can significantly impact your results. In this comprehensive guide from Continental Diamond Tool, Product Engineer Thi Dang and Engineering Consultant Jon VanSant share their expertise as they unpack the essential elements of grinding process optimization. Episode 8 of The Grinding Chronicles offers valuable insights into maximizing Q-prime, balancing G ratios, and selecting the right grinding wheel speeds. Whether you’re looking to refine your current operations or upgrade to the latest in bond technology, our engineering team’s breakdown outlines the key factors you need to consider to enhance your grinding processes. Watch the video or read on to discover practical tips and advanced strategies for getting the most out of your grinding tools.
The Grinding Chronicles - Episode 8
Unlocking the Secrets to Optimizing Your Grinding Process
In this article, you will learn the essentials for optimizing your grinding process, focusing on the metrics that matter most for achieving peak performance. From understanding the basics of speeds and feeds to exploring advanced bond technology, this guide provides actionable insights for any precision manufacturing operation. Whether you're new in the field or looking to enhance your current practices, this informative article from The Grinding Chronicles team offers valuable knowledge to help you get ahead in the industry.
Understanding the Basic METRICS in GRINDING
One of the first considerations when optimizing a grinding process is understanding the basics—speeds, feeds, and material removal rates. These elements are fundamental to the grinding process and play a crucial role in determining the efficiency and quality of the finished product.
Speeds and Feeds:
Speeds refer to the rotational speed of the grinding wheel, typically measured in surface feet per minute (SFM). Feeds, on the other hand, relate to the rate at which the workpiece is fed into the grinding wheel. Together, these parameters influence the rate of material removal, surface finish, and the overall efficiency of the grinding process.
It's essential to understand that faster isn't always better. While higher speeds can increase material removal rates, they can also lead to increased wheel wear and the potential for thermal damage to the workpiece. Therefore, finding the optimal balance between speed and feed is key to maintaining both efficiency and quality.
Material Removal Rate (Q-prime):
Q-prime, or material removal rate, is a critical measure of grinding performance. It is calculated by multiplying the depth of cut by the feed rate, resulting in the amount of material removed per unit time. Higher Q-prime values typically indicate shorter cycle times, which can significantly enhance productivity.
However, achieving high Q-prime values requires careful consideration of other factors, such as wheel wear and the quality of the finished surface. A high Q-prime might reduce cycle times, but if it leads to excessive wheel wear or poor surface quality, the overall efficiency of the process may suffer. Thus, optimizing Q-prime involves balancing it with other critical parameters, such as the G ratio.
The G Ratio:
The G ratio is another vital metric in grinding. It is defined as the volume of material removed from the workpiece divided by the volume of wheel wear. A high G ratio indicates efficient grinding, where more material is removed with less wheel wear. However, similar to Q-prime, achieving an optimal G ratio requires balancing various factors.
Maximizing Q-prime WHILE Balancing the G Ratio
Maximizing Q-prime while maintaining a high G ratio is the key to optimizing grinding processes. To achieve this balance, it’s important to consider the following:
Wheel Speed: Higher wheel speeds can lead to increased wheel wear due to elevated temperatures. Therefore, it’s crucial to find an optimal speed that maximizes material removal without excessively wearing the grinding wheel.
Coolant Delivery: Proper coolant delivery is essential in controlling the temperature during grinding. Efficient coolant systems help dissipate heat, reducing thermal damage to the workpiece and wear on the grinding wheel. This, in turn, helps maintain a high G ratio.
Machine Stiffness and Power: The stiffness of the grinding machine and the power of the spindle also play significant roles. Machines with low power or poor stiffness may limit the achievable Q-prime and G ratio, restricting the overall efficiency of the grinding process.
By carefully considering these factors, manufacturers can optimize their grinding operations to achieve both high Q-prime and G ratios, leading to improved productivity and efficiency.
The Evolution of Bond Technology
Bond technology plays a critical role in the performance of grinding wheels, particularly in their ability to achieve high Q-prime and G ratios. The history of bond technology in grinding wheels is a testament to the continuous advancements that have been made in this field.
A Look Back:
In the 1960s, phenolic resin bonds were the standard, offering Q-prime values of around three. By the 1970s, the introduction of polyimide bonds pushed Q-prime values to around five. The year 2000 marked another leap with hybrid bonds, which increased Q-prime to approximately seven.
Today, we are capable of removing material at rates between 10 and 15, thanks to the latest advancements in bond technology. This evolution highlights the importance of continuously upgrading to the latest bond technology to stay competitive in the market.
Introducing CDT's EVO Hybrid Bond:
Continental Diamond Tool has been at the forefront of these advancements with its EVO Hybrid Bond. Released earlier this year, the EVO Hybrid Bond represents a significant step forward in bond technology, offering the ability to achieve Q-prime values over 10 without compromising the G ratio.
The development of the EVO Hybrid Bond was driven by the need for a bond system that could grind aggressively while minimizing wear and maintaining excellent corner retention. This bond was also designed with thermal conductivity in mind, to transfer heat away from the part and prevent damage to the diamond, which is sensitive to high temperatures. Learn more about CDT’s EVO Hybrid Bond product here.
Practical Tips for Optimizing Your Grinding Process
Now that we’ve covered the theoretical aspects of grinding optimization, let’s look at some practical tips that can help you apply this knowledge to your operations:
Evaluate Your Current Operations: Start by assessing your current grinding processes. Measure your Q-prime and G ratio to establish a baseline. Identify areas where improvements can be made, whether in speed, feed rate, or wheel selection.
Invest in the Latest Technology: Consider upgrading to the latest bond technology, such as CDT’s EVO Hybrid Bond. Newer bonds can significantly improve your material removal rates and reduce wheel wear, leading to better overall efficiency.
Optimize Coolant Delivery: Ensure that your coolant system is operating efficiently. Proper coolant delivery is essential for controlling temperatures and reducing thermal damage, which can extend the life of your grinding wheels and improve the quality of your finished products.
Regularly Maintain Equipment: Regular maintenance of your grinding machines is crucial. Ensure that your machines are running at optimal stiffness and power to maximize performance and avoid limitations in Q-prime and G ratios.
Train Your Team: Make sure your team is trained on the latest grinding techniques and technologies. A well-informed team can make better decisions on the shop floor, leading to improved productivity and efficiency. At Continental Diamond Tool, our application engineers are here to help. We regularly connect with our customers to fine-tune their equipment and train their operators on the optimized speeds and feed rates to use with our grinding wheels.
Optimizing grinding processes is essential for staying competitive in precision manufacturing. By understanding and balancing key factors like Q-prime, G ratio, and wheel speed, manufacturers can significantly enhance their grinding operations. Continental Diamond Tool’s latest advancements, including the EVO Hybrid Bond, provide valuable tools for achieving these goals. Whether you’re looking to improve your current processes or invest in new technologies, the insights provided in this guide offer a clear path to optimizing your grinding operations. Implement these strategies to ensure your manufacturing processes are both efficient and effective, helping you to stay ahead in a demanding industry.
How to Diagnose Surface Pattern Problems in Grinding
Learn how to diagnose and fix common surface pattern problems in precision grinding with expert insights from CDT's Senior Product Engineer, Paul Christy.
Many precision grinding operations require impeccable surface finishes for both function and aesthetics. Addressing surface pattern problems is vital for ensuring the quality of the final product, eliminating waste, and controlling costs. In this detailed overview, we expand on the insights provided by Paul Christy, Senior Product Engineer at Continental Diamond Tool, as he explains how to troubleshoot and fix common causes of surface patterns. In Episode 7 of The Grinding Chronicles, Paul covers the complexities of surface patterns caused by various types of vibrations, runout, and servo system instability. Watch Paul’s video or read on to learn more about identifying and addressing these issues to optimize your grinding operations.
The Grinding Chronicles - Episode 7
Surface Pattern Troubleshooting Guide
Surface pattern problems in grinding can significantly impact the quality and precision of your workpieces. Diagnosing and resolving these issues requires a deep understanding of the underlying causes and appropriate troubleshooting techniques. This article explores common causes of surface patterns in grinding and provides expert insights into their diagnosis and elimination.
Self-Excited Vibration
One of the primary causes of surface pattern problems is self-excited vibration, which occurs at the natural frequency of the machine system. This type of vibration indicates that some component within the machine—such as the spindle, the part, or the dresser—is being excited. The resulting oscillating pattern is called chatter. Notably, this vibration only manifests when the grinding wheel and the workpiece (or the wheel and the dresser) are in contact.
Self-excited vibration results from a lack of sufficient component stiffness. The key to mitigating this issue lies in increasing the machine's stability, which requires a greater machine stiffness compared to the process stiffness. There are three main process variables that can be adjusted to help eliminate self-excited vibration:
Velocity of the Workpiece: Lowering the workpiece's speed can reduce process stiffness.
Velocity of the Grinding Wheel: Decreasing the grinding wheel's speed similarly lessens process stiffness.
Width of Contact: Reducing the contact width between the grinding wheel and the workpiece can also help.
By strategically lowering one or more of these variables, you can effectively diminish the impact of self-excited vibration.
Forced Vibration
Forced vibration occurs at a frequency corresponding to a driving force within or outside the machine. Common examples of such driving forces include unbalanced rotating bodies and pump pulsations. This type of vibration can often be diagnosed using a process of elimination. By sequentially turning on and off all rotating bodies within the machine, you can identify the source of the vibration when it ceases upon the deactivation of a specific component.
Runout
Runout is a prevalent issue in grinding due to the inherent imperfections of rotating components. It occurs when the outer surface of a rotating component does not maintain perfect concentricity with its axis or center line. Specifically, runout in a traversing diamond roll can create a pattern in the grinding wheel, which is then transferred to the workpiece. This pattern typically manifests as angled parallel lines, known as Barber Pole or Roping Patterns.
To address surface patterns caused by runout, it is essential to identify the optimal dresser and wheel RPMs. Varying the diamond roll speed during dressing can reduce the likelihood of pattern formation on the grinding wheel, preventing its transfer to the workpiece. Another effective solution is lapping the diamond roll to the machine's spindle bearings, thereby eliminating runout.
Servo System Instability
Servo system instability is another potential source of surface patterns on workpieces. The servo system controls the movement accuracy of machine components, using digital feedback to ensure precise positioning. Mechanical decoupling within components such as ball nuts, couplings, bearing support units, or scale mountings can create discord within the servo system. This results in oscillations as the system struggles to determine the correct position, leading to surface patterns on the workpiece.
Solving servo system instability typically requires sophisticated instrumentation and physics-based analysis. Iterative process changes alone are unlikely to resolve this complex issue.
Key Takeaways in Mastering Surface Finish
Diagnosing and fixing surface pattern problems in grinding necessitates a thorough understanding of the potential causes and their specific remedies. Whether dealing with self-excited vibration, forced vibration, runout, or servo system instability, targeted adjustments and precise troubleshooting are essential for maintaining the quality and precision of your grinding operations.
For more detailed information and expert guidance, refer to Episode 7 of The Grinding Chronicles, where Paul Christy shows specific measures you can take to diagnose and eliminate surface pattern problems. If you are experiencing surface patterns similar to those discussed in this article and require further assistance, do not hesitate to contact the Continental Diamond Tool engineering team at TheGrindingChronicles@cdtusa.net.
Understanding and addressing these grinding challenges will enhance your operational efficiency and ensure the superior quality of your manufactured products.
CDT Is Boosting Capacity of Plated Grinding Wheels and Dressing Tools
Learn how Continental Diamond Tool is expanding capacity with a new PUMA Lathe, OGP SmartScope, and Doosan Milling Machine for plated grinding wheels and diamond rotary dressers.
An electroplated grinding wheel completes machining on CDT’s new PUMA DNT 2600LM CNC Lathe.
At Continental Diamond Tool, we invest in cutting-edge technology, skilled professionals, and continuous improvement. We aim to be the world’s most reliable source for innovative, high-quality, customized precision grinding solutions, offering exceptional performance and long life. The market has responded, and the last several years we have experienced tremendous growth.
To meet growing demand, our manufacturing center in North Wales has recently acquired three new pieces of equipment, made possible in part by the Conwy – UK Shared Prosperity Grant. This strategic investment is set to significantly expand our production capabilities for the manufacture of electroplated grinding wheels and diamond rotary dressers.
The Journey of Investment
In Q3 2023, CDT Ltd. in the United Kingdom embarked on an ambitious venture with the introduction of a new product line at its facility: custom-engineered electroplated cBN and diamond grinding wheels and tools. To support this initiative, we purchased dedicated electroplating tanks, stripping lines, and specialized manufacturing equipment for product testing and prototyping. This setup has been essential in ensuring that these products maintain the same precision and quality customers expect from CDT.
Meanwhile, our Rotary Diamond Dressers line — the specialty of this business center — continues to thrive. Sharing machining equipment between this booming line and the growing orders for electroplated products has become a challenge. Additionally, we are starting to see strain in our inspection capacity with the increased demand for these two technologies.
Strategic Acquisitions for Expanding Production
The introduction of a Puma lathe, OGP SmartScope, and Doosan milling machine addresses these challenges and paves the way for sustainable growth, diversification, and more efficient delivery for our customers.
Puma DNT 2600LM CNC Lathe
The first new equipment delivery took place in May with the arrival of the Puma DNT 2600LM CNC Lathe. This piece of equipment is crucial to meet the increasing demand for electroplated products independently from our rotary diamond dressers. Having a dedicated Puma Lathe for plated products assists in the timely delivery of these high-quality tools to our customers without compromise.
OGP SmartScope
In June we received the OGP SmartScope, a revolutionary 3-axis video measurement system. The SmartScope E7, with its IntelliCentric™ fixed lens optical system, 6-megapixel camera, and 5-position digital zoom, delivers high-resolution images that are essential for precise metrology. This state-of-the-art equipment will expand our inspection capacity to maintain the high standards expected of our precision products.
Doosan Milling Machine
Delivered in early September, the Doosan Milling Machine completes our trio of new equipment purchased with the government grant. This addition further bolsters production, ensuring we have the capacity to meet growing demands and continue our commitment to excellence.
A CNC operator programs CDT’s new PUMA Lathe that was delivered and installed in May.
A CDT quality tech measures a coupon on the new OGP SmartScope that was delivered in June.
A technician operates CDT's Doosan Milling Machine that was delivered in September.
Impact and Future Prospects
With the Puma Lathe, OGP SmartScope, and Doosan Milling Machine now up and running, we are already seeing the benefits in our production processes. The ability to utilize these machines for Plated products independently of our Rotary Diamond Dressers line has optimized our workflow and improved our overall efficiency.
These investments also support a long term strategy for CDT Ltd. They not only address our current production challenges but also set the stage for future growth and diversification at this facility. As we continue to innovate and expand our capabilities, we remain committed to the timely delivery of the high-quality products our clients expect.
Stay tuned for more updates as we continue to enhance our production capabilities and explore new horizons in the industry.
For more information on the Puma DNT 2600LM CNC Lathe, visit here.
Continental Diamond Tool Ltd., located in Kinmel Bay on the Western Coast of North Wales in the United Kingdom, is dedicated to providing top-tier superabrasive products for precision grinding and dressing.
At Continental Diamond Tool, we are excited about these investments and look forward to leveraging this equipment to further our mission of excellence in the industry. If you need a solutions provider for your precision grinding applications, please contact our sales team through our website contact form or
call +44 1745-343951 (UK) / 1-800-443-6629 (USA).
A Breakdown of the 4 Common Bond Systems in High Precision Grinding
Discover CDT's four essential bond systems for superabrasive grinding wheels: Resin, Metal, Vitrified, and Electroplated. Optimize operations with expert insights from Jeff Wirth.
If precision grinding is a critical component of your manufacturing process, understanding the bond system of your grinding wheel will help you in maintaining operational efficiency and product quality. In this detailed overview, we will explore the four most common bond systems used in superabrasive grinding wheels: Resin, Metal, Vitrified, and Electroplated. Continental Diamond Tool Engineering Manager Jeff Wirth breaks down the components of these bond systems, discussing their composition, manufacturing processes, and ideal applications in Episode 6 of The Grinding Chronicles. Watch Jeff’s video or read on to learn more about selecting the right bond to optimize your grinding operations.
The Grinding Chronicles - Episode 6
Understanding the Four Common Bond Systems
Resin Bonds
Resin bonds are plastic-based compounds typically made from phenolics or polyimides. These bonds are versatile and can be enhanced with fillers such as copper or silicon carbide to improve performance. The manufacturing process for resin bonds at CDT begins with creating a tailored formulation that includes the bond material, abrasive, and fillers. This dry powder mixture is blended in special tumblers and then carefully and uniformly packed into mold cavities. The molds undergo hot pressing, where temperature and pressure are meticulously controlled to achieve the desired density. Finally, the wheels are finished by machining and grinding them to the specified size and geometry.
Properties and Applications:
Tough and Durable: Resin bonds are fully dense and easy to use, making them suitable for a variety of grinding applications.
Versatile: They can work with nearly any material, from hard metals to softer alloys.
Enhanced Performance: Fillers like copper or silicon carbide can be added to improve heat dissipation and grinding efficiency.
Wide Range of Applications: Suitable for diverse grinding tasks, including tool and cutter grinding, centerless grinding, and surface grinding.
Metal Bonds
Metal bonds can be composed of various metals, including bronze, copper, and iron, and may sometimes be alloyed with precious metals like silver. Metal bonds are known for their hardness, toughness, and durability, making them ideal for grinding highly abrasive materials such as glass and ceramics. Although metal bonds grind more slowly than other types, they offer the longest lifespan. The manufacturing process for metal bonds at CDT is similar to that of resin bonds, involving formulation, mixing, molding, hot pressing, and finishing.
Properties and Applications:
Hardest and Toughest: Metal bonds are the most challenging to use but provide superior durability.
Long-Lasting: They offer the longest lifespan among bond types, reducing the frequency of wheel changes.
Ideal for Abrasive Materials: Best suited for grinding materials like glass, ceramics, and carbide.
Durability: Excellent for applications requiring extreme durability and extended wheel life, such as in the automotive and aerospace industries.
Vitrified Bonds
Vitrified bonds are made from glass or ceramic materials, creating a porous structure that significantly reduces grinding force. This allows for higher grinding speeds, making vitrified bonds ideal for high-production applications. These bonds offer moderate to high material removal rates and excellent form accuracy, as they can be dressed and profiled in-process using rotary dressers. The manufacturing process for vitrified wheels at CDT involves formulation, mixing, cold pressing, and a sintering (baking) process to fuse the glass or ceramic together. The final step is finishing, similar to the other bond types.
Properties and Applications:
Porous Structure: Lowers grinding force and allows increased speeds, enhancing efficiency.
High Production: Ideal for high-production applications such as automotive part manufacturing.
Moderate to High Material Removal Rates: Efficient for large-scale operations, balancing speed and precision.
High Form Accuracy: Can be dressed and profiled in-process using rotary dressers, making them suitable for precise and consistent grinding tasks.
Electroplated Bonds
Electroplated (or plated) bonds consist of a single layer of abrasive held by a nickel-based metal bond. The process begins with machining the desired wheel size and geometry onto a steel wheel core. The non-plated surfaces are masked to prevent unwanted plating. The wheel core is then placed in a bath with a nickel-based solution and the abrasive material. By applying a positive charge on one side and a negative charge on the other, nickel plating is deposited onto the wheel core, causing a single layer of abrasive to adhere. Excess abrasive is removed, and the plating process continues until the abrasive layer is encapsulated to the desired level, typically 50-100% depending on the application. Electroplated products are suitable for complex geometries and low to medium production applications due to their high material removal rates and fast grinding speeds.
Properties and Applications:
High Material Removal Rates: Provides the fastest grinding speeds, ideal for rapid material removal.
Cost-Effective: Single layer of abrasive can be stripped and replated, extending the wheel’s life.
Ideal for Complex Geometries: Precise form replication with minimal finishing, suitable for intricate designs.
Low to Medium Production: Suitable for specific applications requiring detailed shapes and efficient material removal.
Key Considerations for Selecting the Right Bond System:
Choosing the appropriate bond system for your grinding application is crucial for achieving optimal performance and quality. Each bond type offers unique properties and advantages, making them suitable for different materials and grinding conditions. By understanding the composition, manufacturing processes, and ideal applications of Resin, Metal, Vitrified, and Electroplated bonds, you can make informed decisions to enhance your grinding operations.
Factors in Bond System Selection:
Material to be Ground: The hardness and abrasiveness of the material significantly influence the choice of bond.
Grinding Speed and Efficiency: Consider whether the application requires high-speed grinding or if longevity and durability are more critical.
Application Specifics: Determine if the grinding operation involves complex geometries or requires high form accuracy.
Production Volume: High-production environments may benefit from vitrified bonds, while electroplated bonds are ideal for low to medium production with intricate details.
If you have any questions or want to learn more about which bond type would work best for your application, please reach out to our application engineers at TheGrindingChronicles@CDTUSA.net. For more industry insights and expert advice, check out these articles or watch our playlist for The Grinding Chronicles on YouTube. By leveraging the right bond system and understanding its properties, you can significantly improve your grinding efficiency, product quality, and operational cost-effectiveness.
Students Build Careers in Engineering with CDT Apprenticeships
Continental Diamond Tool Ltd. is shaping engineering careers for Kinmel Bay-area students like Rhys Butler and Corey Jones. Follow Rhys's eight-week work experience apprenticeship alongside Corey at CDT's precision manufacturing facility in North Wales.
(From left to right) Rhys Butler, left, and Corey Jones who are building careers in engineering with the apprenticeship programme at Continental Diamond Tool Ltd. in collaboration with Coleg Llandrillo in North Wales.
An 18-year-old sixth form student is getting a taste of the world of precision engineering after being inspired by the success of a high flying company.
Rhys Butler, a pupil at Ysgol Glan Clwyd in St Asaph, is now on an eight-week work experience programme after writing to Continental Diamond Tool, on the Tir Llwyd Industrial Estate in Kinmel Bay, which is withing walking distance of his home.
According to Rhys, he was prompted to get in touch when he read a news story about the firm which supplies sophisticated parts for production machinery for Rolls-Royce and other aerospace companies in the UK.
Continental Diamond Tool Ltd. (CDT), which employs 40 skilled staff and is celebrating its 40th anniversary this year, is one of only two companies of its kind in the UK.
It makes a range of highly specialised diamond tools for advanced manufacturing industries, including the aerospace, automotive, medical and semi-conductor sectors.
Rhys said: “I saw the story about the company being under new American ownership and I was looking for work experience for my CV so I emailed in an application and they came back to me straight away.
“They’ve given an eight-week programme so I go in one day a week and I’m going through the different processes they do and they show me and explain how they work.
“One Wednesday I was actually working on putting the diamonds into the tooling. It’s been a brilliant opportunity.
“I’ve always been interested in cars and how machines work and I’m doing engineering in sixth form and go to the Llandrillo College campus in Rhyl every Thursday which is really helpful.”
Rhys often works alongside Corey Jones, 19, also from Kinmel Bay, now in his second year as an apprentice who also took the work experience route to a place with CDT.
He said: “I did my A-levels at Eirias High School in Colwyn Bay and then did Level Three Engineering at Coleg Llandrillo’s site at Rhyl with work experience here and they offered me an apprenticeship.
“They wanted me to get used to what’s involved so I worked here through my summer holidays and started my apprenticeship in September in Level Four Engineering.
“I knew there was a lot of maths in engineering and I’d always enjoyed that and I like to challenge myself by learning about the different machines so I’m really enjoying it.
“I had tried a few places for work experience and Coleg Llandrillo suggested here and it’s been brilliant.
“The people here are really great and very knowledgeable with lots of experience you can learn from – I work with someone who has experience on every machine and he’s a big help.
“We’re working for businesses like Rolls-Royce which is fantastic so I want to do the best I can and really build a career here.”
Michaela Lawton, CDT Finance Manager, said: “We have been running an apprenticeship scheme here for a long time and historically it’s been successful and two of our apprentices who moved on after a few years have actually come back to us.
“We have a very good relationship with Coleg Llandrillo and it really helps that they have a campus at Rhyl with a strong and well-equipped engineering department.
“What we do here is so unique and so niche that we expect our apprentices to learn the core skills in college to give them the platform to build on with the highly specialised work we do here.”
CDT has been boosted by a £1.6million investment by their American owners and has opened a second production unit on the Tir Llwyd Estate to house its new electro-plating operation which has received support from Welsh Government.
More than 60 per cent of the company’s products are exported to 30 countries, with sales growing particularly strongly across Europe and Asia, as well as North America.
The company, which celebrates its 40th anniversary this year, was founded originally as Consort Precision Diamond and in 2018 was bought and rebranded by Continental Diamond Tool Corporation, based in New Haven, Indiana.
Related Links:
https://www.gllm.ac.uk/news/rhys-and-corey-shine-with-diamond-tool-firm
Images captured by Mandy Jones Photography.
Part Masking of Plated Grinding Wheels
Learn about the process of part masking in the production of plated diamond and CBN grinding wheels. This technique ensures precision and quality in precision grinding across industries like manufacturing, automotive, and aerospace. Find out the specialized skills that are required to excel in this type of work.
Part masking is a crucial technique employed in the plating process for CBN (Cubic Boron Nitride) and diamond grinding wheels. This method involves selectively covering specific areas of a metal substrate before plating to protect them from the plating solution. Part masking plays a significant role in ensuring the precision, quality, and functionality of grinding wheels used in various industries, from manufacturing to automotive and aerospace. In this article, we will delve into what part masking is, how it is done, why it is essential in the plating process, and what it takes to excel at this intricate skill.
What is Part Masking?
Part masking is the process of shielding specific areas or features of a substrate to prevent them from being plated during the plating process. It is achieved by applying a masking material to the surface of the substrate in a controlled and precise manner. The masking material can be in the form of tapes, paints, or other coatings that can resist the heat and duration of time in the plating process.
How is Part Masking Done?
The process of part masking involves several steps:
Surface Preparation
Before masking, the metal substrate is thoroughly cleaned and prepared. This step ensures that the surface is free from contaminants, oils, coolants, machining residues and oxides, which can interfere with the adhesion of the masking material.
Masking Material Selection
The choice of masking material depends on factors such as the type of substrate being plated, the plating process used, and the specific areas that need protection. Common masking materials include specialized masking tapes, latex, and resin-based coatings. Continental Diamond Tool employs all of these methods in its process.
Application of Masking Material
The masking material is applied precisely to cover the areas that should not be plated. This can be done manually or using brushes, stencils, scribes or automated equipment. For more complex patterns, careful attention is given to ensure that there are no gaps or leaks in the masking material.
Cure or Drying
Depending on the type of masking material used, it may need to be cured or allowed to dry thoroughly. This step generally takes a specific amount of time and ensures that the masking material remains intact and impermeable during the plating process.
Plating
Once the wheel has been masked and cured, the substrate is immersed in the plating bath, where the exposed areas are plated with the desired abrasive material, such as diamond or CBN particles. The masked areas remain untouched, preserving their original characteristics.
Mask Removal
After the plating process is complete, the masking material is carefully removed, revealing the plated surface underneath. This can be done through various methods, such as peeling off tapes or dissolving the masking material with solvents.
Why is Part Masking Essential?
Part masking serves several crucial purposes in the plating process for diamond and CBN grinding wheels:
Precision and Quality
Part masking ensures that the plating is applied precisely to the intended areas, maintaining the tight tolerances, quality, and accuracy essential to precision grinding.
Functionality and Performance
By protecting specific features of the grinding wheel, such as arbor holes, flanges or threaded holes, from plating, part masking helps maintain their functionality and performance, ensuring they are dimensionally fit and operate correctly.
Cost Efficiency
Masking reduces the amount of plating material used, minimizing waste and lowering production costs. It also prevents the need for costly post-plating rework to remove unwanted plating.
Customization
Part masking, applied by hand, is customizable. This allows manufacturers to create tailored, complex products to meet specific customer requirements.
What It Takes to Be Good at Part Masking
Part masking is a specialized skill that requires attention to detail, precision, and an understanding of materials and processes. Here are some key attributes and considerations for those looking to excel in this field:
Attention to Detail
Successful metal part maskers must have a keen eye for detail. Precision is paramount in this process, as even the smallest imperfections or gaps in the masking material can lead to plating errors.
Material Knowledge
Familiarity with various masking materials and their properties is essential. Different materials may be required for specific applications, and understanding their characteristics can ensure the right choice is made.
Patience and Dexterity
The application of masking material can be a delicate and time-consuming task. Patience and manual dexterity are necessary to achieve consistent and high-quality results.
Problem-Solving Skills
Maskers may encounter challenges such as complex shapes or irregular surfaces that require creative problem-solving to ensure proper masking.
Adherence to Safety Protocols
Safety is paramount when working with masking materials and plating chemicals. Understanding and following safety protocols are crucial to prevent accidents and exposure to hazardous substances.
At CDT, our masking department has almost 50 years of combined experience in this highly specialized field. The superior quality and stellar reputation of our plated products are a testament to their expertise.
If you are passionate about precision craftsmanship and believe you have the skills and attributes required for part masking, we encourage you to consider career opportunities in this field. At Continental Diamond Tool, we value skilled professionals who can contribute to our commitment to excellence.
To explore potential positions and apply for a rewarding career in electroplating or other positions in our industry, visit our careers page.
How to Order a Custom Electroplated Grinding Wheel
At CDT, we take pride in the excellence of our masking and plating departments. Part masking is an indispensable technique in the production of plated diamond and CBN grinding wheels to ensure the delivery of the very best products. It requires a unique set of skills, including attention to detail, material knowledge, patience, and problem-solving abilities. Those who excel in this field play a vital role in providing the precision, quality, and functionality of grinding wheels used across various industries.
If you are interested in ordering a custom plated grinding wheel or have any inquiries, please don't hesitate to contact our customer service department. Our team can connect you with our experienced plating engineers to start the process today.
Advantages of Using Electroplated Diamond Grinding Wheels for Precision Grinding
Say goodbye to dressing downtime and hello to faster cycle times with electroplated grinding wheels for precision industries like aerospace, automotive, medical devices, and electronics. These wheel are even more cost-effective with our Strip and Replate Program: learn more.
With precision machining and grinding, the selection of tools plays a pivotal role in determining efficiency, profitability, and overall success. Among the many options available, electroplated diamond and CBN (cubic boron nitride) wheels rank high as indispensable assets for many manufacturers worldwide. These tools offer a unique combination of advantages that contribute significantly to superior performance and cost-effectiveness. In this article, we explore four key reasons why these tools are at the forefront of precision machining and grinding.
1. Consistent Distribution of Abrasive Particles
In precision grinding, the even distribution of abrasive particles is often critical for consistency. Electroplated diamond grinding wheels excel in this aspect, ensuring a uniform dispersion of abrasive particles across their entire surface. Unlike alternative bonding methods that may result in irregular spacing of abrasive grains, electroplated tools embed diamond particles evenly in a single layer. This uniformity translates to predictably consistent grinding or cutting performance. The same is true for electroplated cbn grinding wheels.
In practical terms, this means achieving precision and accuracy in your workpiece everytime, pass after pass. Whether working with robust metals, fragile ceramics, or intricate composites, manufacturers can place their trust in electroplated grinding tools to deliver a reliable and uniform cutting or grinding action.
2. Strong Bond Between Abrasive and Substrate
Another distinguishing factor that sets electroplated diamond tools apart is the robust bond formed between the abrasive particles and the tool's substrate. During the electroplating process, diamond grains become firmly embedded within a nickel or other metallic matrix, creating a tool of exceptional durability and resilience.
This sturdy bond ensures that the diamond particles remain securely attached to the tool's surface, even when subjected to high-speed or high-pressure operations. Consequently, these tools maintain their sharpness and cutting efficiency over an extended period, eliminating the need for dressing and maximizing time between replacements. This durability translates into significant cost savings by reducing downtime and material wastage.
3. Free Cutting Action Equates to Fast Cycle Times
Electroplated diamond tools offer a "free cutting action" that speeds up the grinding and cutting process significantly. Unlike conventional tools that may generate excess heat, clog, or wear unevenly, electroplated diamond tools efficiently remove material with minimal resistance.
This means reduced cycle times for manufacturers. Jobs that used to take longer can now be completed faster and with more precision. Whether shaping aerospace components or fine-tuning medical devices, electroplated diamond tools deliver both speed and accuracy. Fast cycle times translate to increased throughput, shorter lead times, and enhanced competitiveness in today's manufacturing landscape.
4. Maintenance and Reconditioning: The Strip and Replate Program
At Continental Diamond Tool (CDT), we go above and beyond to extend the lifespan of electroplated grinding wheels through our innovative Strip and Replate Program. This program harnesses strip technology to safely remove worn-down abrasives without compromising the wheel's core. We employ a chemical solution to delicately eliminate old abrasives, preserving the integrity of the wheel's substrate. After stripping, a new layer of abrasive material is expertly applied through electroplating.
The outcome? A rejuvenated electroplated grinding wheel that performs at its best. These reconditioned wheels undergo rebalancing to ensure optimal performance during extended runs. This program not only maximizes tool lifespan but also minimizes waste, translating into cost savings and reduced downtime.
How Electroplated Grinding Wheels Yield Long-Term Cost Savings
At CDT, our electroplated grinding wheels are engineered to endure heavy usage, consistently deliver high performance, and enjoy an extra-long wheel life compared to other wheel types. This durability translates into substantial long-term cost savings — as much as 40% in some instances. Plus, the "free cutting action" of electroplated diamond tools is a powerful ally for manufacturers seeking faster cycle times without compromising quality. These tools optimize efficiency, boost productivity, and meet the precise demands of modern machining and grinding processes.
Industries Benefiting from Electroplated Grinding Tools
A wide array of industries benefit from the unique advantages that diamond plated tools offer. Here's a glimpse into some of the key sectors where these tools play a pivotal role:
Aerospace: In the aerospace industry, precision and quality are paramount. Diamond plated tools shape and finish critical components like turbine blades, engine parts, and aircraft structural elements. They deliver the precision required to ensure the safety and reliability of aircraft.
Automotive: The automotive industry relies on diamond plated tools for tasks such as sharpening cutting tools, honing engine components, and producing high-precision parts. These tools contribute to the efficiency and durability of automotive systems.
Medical Devices: The production of intricate and high-precision medical devices, including surgical instruments and implants, relies on diamond plated tools. They enable the manufacturing of components with tight tolerances and exceptional surface finishes, crucial for medical applications.
Electronics: Precision is essential in the electronics industry, where delicate components require fine grinding and cutting. Diamond plated tools play a pivotal role in shaping semiconductors, ceramic substrates, and other electronic components with microscopic precision.
Tool and Die Making: Tool and die manufacturers use diamond plated tools to create molds, dies, and precision cutting tools. These tools provide the accuracy needed to produce intricate and high-quality components.
Stone and Glass Processing: In the construction and architectural industries, diamond plated tools are used for cutting and shaping stone, glass, and composite materials. They offer the precision and control necessary for creating custom designs and finishes.
Fiberglass and Composites: Electroplated grinding tools are indispensable for shaping and refining composite materials used in many applications. From boat hulls to automotive body parts to architectural panels, their ability to provide precise shaping and surface finishing ensures the structural integrity and aesthetics of fiberglass and composite products.
The Competitive Edge of Electroplated Grinding Technology
In conclusion, electroplated grinding wheels offer an impressive array of advantages, including consistent distribution of abrasive particles, a robust bond between abrasive and substrate, fast and free cutting action, and an innovative reconditioning option with Strip and Replate. These benefits combine to deliver long-term cost savings, which establish electroplated grinding wheels as the preferred choice for precision machining across a diverse array of industries.
To harness the advantages of electroplated diamond and cbn grinding wheels for your specific machining needs and see the cost savings, consider partnering with trusted grinding wheel manufacturers like CDT, dedicated to delivering exceptional quality and performance.
Continental Diamond Tool Limited Soars with Record Sales Driven by £1.6 Million Investment
Learn about Continental Diamond Tool Limited's remarkable growth and success fueled by a £1.6 million investment and their expertise in crafting diamond-encrusted tools for diverse global industries.
Continental Diamond Tool Limited — CDT’s subsidiary stationed in Kinmel Bay, Conwy, in North Wales— is experiencing an era of remarkable growth thanks to a substantial £1.6 million investment initiative. According to Jeff Wirth, the Managing Director, this rapid expansion is a result of a perfect blend of Welsh dedication and backing from its American stakeholders.
"As part of our expansion strategy, we opened a second production unit, which has facilitated the establishment of a new electro-plating operation. With support from the Welsh Government, this move marks a significant leap for us," said Wirth.
Continental Diamond Tool Limited is a niche outfit, one of merely two similar enterprises in the UK that specializes in crafting diamond-encrusted rotary dressers and grinders. The team designs their custom products for diverse manufacturing sectors like aerospace, automotive, medical, and semiconductor industries.
"In aerospace, our rotary diamond dressers play a pivotal role in crafting engine parts for prominent aircraft like the Boeing 777 and 787 Dreamliner, as well as the Airbus A330-A380 series," commented Wirth. These aircraft parts are notably crafted at the Airbus facility in Broughton.
"Over 60% of our products find their way to 30 countries globally, experiencing substantial growth across Europe, Asia, and North America," added Wirth.
Originally founded as Consort Precision Diamond, the company will be celebrating its 40th anniversary in April of next year (2024). In 2018, it underwent a timely transition when Continental Diamond Tool Corporation acquired it. During the COVID-19 pandemic, the company showed resilience amid adversity as it pivoted its product range to mitigate a significant loss of orders in one of its largest sectors due to grounded passenger planes.
"It would have sunk most companies, but we had already started our diversification and a pretty significant culture change here," remarked Wirth during a visit from the States. "Sales are now at a record high. Over the last five years, our Rotary Diamond Dresser product line in Kinmel Bay has seen remarkable growth of over 70%, despite the negative effects of COVID," he continued.
CEO Nick Viggiano noted, "We believe in the workforce here, we believe in the people, their work ethic, their can do spirit, and the pride they take in their work. At CDT headquarters in New Haven, Indiana, the culture is the same. When you take modern technologies and join it with that culture, it’s a recipe for success.”
"The new energy and substantial investment brought by the new owners has been a game-changer," echoed Michaela Lawton, the finance manager. "We've also had a good relationship with the Welsh Government for some time. The latest support with the £90,000 we received from the Smart Cymru fund helped fast-track the new technology that we introduced through the electro-plated product."
The project has been a source of great pride to production manager Justin Hughes who’s been working at the Kinmel Bay site for the past 17 years.
He said: “We’ve got the backing of the American parent company behind us which enables us to push forward with investment in machinery and people to aim at new markets. It gives us reassurance and confidence as we continue to grow and develop.”
"The company is on an upward trajectory in terms of growth, turnover, profit, and being able to further diversify our product range is the next step forward,” adds Lawton. “It's a very exciting place to work, and the sky really is the limit.”
Related News Links:
https://www.business-live.co.uk/manufacturing/global-engineering-firm-north-wales-28144996
http://www.baysideradio.co.uk/news/kimmel-bay-global-engineering-firm-propelled-by-1-6m-boost-8260
The Story Behind Our Precision Grinding Solutions at Continental Diamond Tool Ltd.
Continental Diamond Tool Limited's Diamond Rotary Dressers set industry standards with cutting-edge technology and award-winning processes. With decades of expertise and product excellence, our dressing and grinding solutions meet the demands of diverse industries worldwide. Learn more about our innovative solutions in precision grinding.
At Continental Diamond Tool Limited, our 40 years of success has been built by delivering the finest custom Diamond Rotary Dressers available in the market. Also called Diamond Rolls, these tools are used extensively in a growing number of grinding operations to primarily facilitate the transfer of highly accurate repeated configurations onto components. What makes a Consort Precision Diamond Rotary Dresser stand out can be summarized in four key aspects: technology, expertise, process, and quality or product excellence. As we have expanded into other product lines, we bring that same commitment to every precision grinding product we produce.
Cutting Edge Technology
In a plunge-style dresser the Rotary Diamond Dresser is mounted onto a spindle of a drive unit which in turn is mounted onto a slideway arrangement that allows the formed periphery of the dresser to infeed into a grinding wheel, thereby transferring the desired shape into it. The form, or configuration, can then be 'ground' on to the component. Plunge dressers are especially accurate for precision grinding as there is no lost form or geometry due to machine movements. Plus, the dressers can be held to submicron levels of accuracy.
Traverse dressing is a grinding wheel dressing technique where the diamond rotary dresser traverses across the surface of the grinding wheel to create a specific profile or shape. Traverse Disc Dressers allow you the flexibility to make profile changes or dress in completely new profiles with the same tool, reducing down time for wheel change overs or roll changes.
INDUSTRY EXPERTISE
Such Industries as the Automotive and Aerospace as well land based Turbine Engine production units employ large quantities of Rotary Diamond Dressers. Typically, within the Aero manufacturing industry, such components as Turbine Blades and Nozzle Guide Vanes as well as Flap Actuating Shafts require their intricate features to be ground with grinding wheels that have been formed with Rotary Diamond Dressers. As can be seen reference is made on our following pages to the many applications within the automotive industry.
CDT Ltd. can offer expertise in the selection of the most appropriate type of Rotary Diamond Dresser by reference to the configuration required and to the grinding machine on which it is to be used. Basically, three processes are employed. Handset Sintered, Random Set Sintered and Reverse Plated. Within each of those categories, selection of diamond type and their placement into the periphery of the Rotary Dresser, plays a major part in determining its operational life and performance. Even before its establishment in 1984, the company’s principals and a large proportion of its employees had many previous years experience in the manufacture of Rotary Diamond Dressers. Bringing with them unique knowledge of the industry, CDT Ltd. — then Consort Precision Diamond — quickly established itself with this one product into the global market of prime and subcontract component manufacturers, earning the respect of competitors and customers alike.
AWARD-WINNING PROCESSES
In respect to the Reverse Plating technique, at Continental Diamond Tool Limited we are particularly proud of the fact that we have been awarded the accolade of winning the BOOST award in the U.K. in 1995 for the design and development of a high speed plating process which dramatically reduced previous lengthy plating times. This achievement gave us a competitive edge against alternative suppliers and satisfied the reduced lead times that customers continue to demand. In the same period, we gained the S.M.A.R.T 1995 award for the development of the electroforming process as an acknowledgement of the reduction in the process time employed in the manufacture of Reverse Plated Rotary Diamond Dressers. CDT Ltd. proudly holds the ISO 9001:2015 Registration Certificate for its Quality Management Systems.
A FOCUS ON PRODUCT EXCELLENCE
The Consort Precision name has become synonymous for outstanding quality and performance in Diamond Rotary Dressers. Since 1984, we have been perfecting the design, development, manufacture, install and maintenance of this advanced dressing technology. This long history with a singular focus has given us the unique ability to provide our customers with the best solution technology can offer. We have the engineering, design, manufacturing and staff resources to supply the highest quality Diamond Rotary Dressers available on the market. Our specialized experience ensures each product we supply is the optimum choice for each individual customer, however demanding and complex the configuration. If an application calls for traverse- or plunge-style rotary dressing, Consort Precision™ Diamond Rotary Dressers are the best tool for the job.
With investment from our parent company, Continental Diamond Tool Corporation, we have expanded our facility in Kinmel Bay to manufacture a wider range of superabrasive products and better cater to a global market. In 2021, an expansion of the Plating lab more than doubled our capacity to produce the high quality tight tolerance reverse plated rotary dressers used by some of the world’s most prestigious corporations. It also paved the way for diversification into electroplated grinding wheels, which we began producing in early 2023. As CDT Ltd. continues to evolve and adapt to the ever-changing technological landscape, we remain committed to delivering innovative solutions and superior products to meet the growing demands of our customers worldwide.
Consort Precision Diamond Company Announces New Identity As Continental Diamond Tool Limited
Consort Precision Diamond becomes Continental Diamond Tool Limited, strengthening its precision diamond tools legacy. Expect an expanded product line, unwavering quality, and innovation.
Kinmel Bay, Rhyl, U.K. (September 11, 2023) – Consort Precision Diamond Company, a top manufacturer of precision diamond tools in the United Kingdom, is pleased to share a major announcement. Effective July 10, 2023, the company has officially changed its name to Continental Diamond Tool Limited.
The new name aligns with its parent company, Continental Diamond Tool Corporation (CDT), which acquired Consort in 2018. With headquarters in New Haven, Indiana, U.S.A., CDT is recognized globally for manufacturing high-precision custom superabrasive grinding wheels, which integrates seamlessly with Consort as a distinguished and trusted producer of high-quality precision diamond rotary dressers.
At the core of this name change is a firm dedication to delivering premium quality and innovation. Over the past several years, the company has expanded its facility in Kinmel Bay to manufacture a wider range of superabrasive products and better cater to a global market. In 2021, an expansion of the Plating lab more than doubled the company’s capacity to produce the high quality tight tolerance reverse plated rotary dressers used by some of the world’s most prestigious corporations. It also paved the way for diversification into electroplated grinding wheels, which the facility began producing in early 2023.
This strategic growth is part of the company's unwavering commitment to delivering comprehensive solutions to customers. As the company continues to expand its offerings to encompass more high-performance grinding technologies in step with its parent company, aligning the name and marketing efforts of the two is a logical move.
In the coming weeks, on-lookers can expect to see updates across various aspects of Consort's branding and materials as it transitions to Continental Diamond Tool Limited. This includes revisions to its packaging, marketing materials, website, and all pertinent documentation. The company is committed to ensuring a smooth transition, with minimal disruption to the customer experience.
“For nearly four decades, Consort has faithfully served leaders in the automotive, aerospace, and other precision manufacturing industries. We look forward to continuing our longstanding relationships with customers under our new name,” says Jeff Wirth, Managing Director of Continental Diamond Tool Limited. For further information about this transition, please send any queries to info@cdtltd.com.
About Continental Diamond Tool Limited
Continental Diamond Tool Limited is a globally recognized leader in custom precision diamond tools, specializing in all forms of precision diamond rotary dressers and electroplated grinding products. With a commitment to excellence and innovation, the company serves a diverse range of industries from its advanced manufacturing facility located in the coastal town of Kinmel Bay in Conwy County Borough, Wales, United Kingdom. Learn more at CDTLTD.com.
Understanding the Distinction Between CBN and Aluminum Oxide Abrasives
Uncover the secrets behind top-notch results in grinding and machining of tough steels and metals. Discover the unique properties of Cubic Boron Nitride (CBN) and Aluminum Oxide and learn how to choose the right abrasive for optimal efficiency and precision.
Are you ready to explore the fascinating world of abrasives? In manufacturing, we often encounter Superabrasives and Conventional abrasives. In the Superabrasives corner, we have Diamond and Cubic Boron Nitride (CBN), and their common Conventional abrasive counterparts are Silicon Carbide and Aluminum Oxide. Each serves a specific purpose. What makes CBN and Aluminum Oxide stand out is their exceptional ability to tackle those stubborn steels and metals that can't stand Carbon.
In this blog, we'll explore the properties and applications of CBN and Aluminum Oxide abrasives. Discovering their unique characteristics will help you choose the right abrasive for your specific machining needs, ensuring efficiency and top-notch results. Whether you're working with hardened steels or softer metals, the right abrasive is the key to achieving your desired outcome in grinding and machining. So, let's dive in and unlock the true potential of CBN and Aluminum Oxide abrasives.
What is CBN?
CBN is a synthetic Superabrasive known for its incredible hardness, high thermal conductivity, and thermal stability. Originally released with the trade name Borazon from GE Superabrasives, its cubic crystal lattice structure is similar to Diamond, giving it remarkable abrasive properties. With a hardness close to 10 on the Mohs scale, CBN excels in machining tough materials that require precision grinding. Its chemical composition and high thermal stability prevents chemical reactions and premature breakdown under high temperatures, when grinding ferrous metals and high-temperature alloys. What's more, because CBN doesn't react with ferrous materials, it doesn’t alter or change their properties resulting in longer life in use when ground with CBN.
CBN is a game-changer when grinding hardened ferrous alloys or super alloys that are sensitive to heat. It efficiently grinds hardened steels while maintaining accuracy and surface finish. Plus, it's a favorite for grinding ferrous metals like cast iron and stainless steel, ensuring clean and precise results without chemical alterations. CBN is a must-have tool for achieving precise and efficient outcomes in critical machining tasks.
What is Aluminum Oxide?
Aluminum Oxide, also known as alumina, is a versatile Conventional abrasive. With high hardness and toughness, it is available in various grit sizes, making it perfect for a wide range of machining and finishing applications. Though not as hard as CBN, Aluminum Oxide is fantastic for soft metals, wood, and non-ferrous materials. While it may not match the precision of Superabrasives, it's still a reliable choice for many tasks.
In the machining industry, Aluminum Oxide is the go-to for grinding soft metals like aluminum, brass, and copper. It performs beautifully with non-ferrous materials such as bronze and titanium, without causing any chemical interactions. Its role in achieving desired surface finishes across various industries, from automotive to aerospace, is unparalleled.
Key Differences Between CBN and Aluminum Oxide Abrasives
While CBN and Aluminum Oxide both play significant roles in grinding and machining operations, they have many distinct properties that set them apart.
Crystal Structure and Hardness: CBN's crystal lattice structure is similar to Diamond, resulting in exceptional hardness and wear resistance. Aluminum Oxide, while still hard, has a lower hardness than CBN, making it more suitable for soft metals and certain alloys.
Heat Resistance and Thermal Conductivity: CBN exhibits superior heat resistance and thermal conductivity compared to Aluminum Oxide, making it perfect for grinding high hardness and heat sensitive alloys.
Material Compatibility and Reactivity: Both CBN and Aluminum Oxide are chemically inert with ferrous materials whereas Diamond and Silicon Carbide are not, thus why they are the abrasives for ferrous metals.
Cost and Practicality: CBN grain costs significantly more than Aluminum Oxide grain, resulting in higher grinding wheel prices. Because of higher hardness and better thermal conductivity, CBN wheels can provide lower grinding costs in applications where high workpiece hardness and thermal properties need to be maintained. In cases of grinding soft steels and low volume production, the lower wheel price of Aluminum Oxide makes it a more competitive option.
Safety Considerations and Handling
Whether you choose CBN, Aluminum Oxide, or another solution for your abrasive, ensuring safety during grinding and finishing processes is essential. Proper machine guarding, eye and respiratory protection, proper dust/mist extraction, and careful handling and storage of abrasives are crucial to protect workers and maintain a clean and safe work environment.
Selecting the Right Abrasive for Specific Applications
Choosing the right abrasive for your specific machining needs is vital to achieving optimal results. Making an informed decision will ensure efficient, accurate, and cost-effective grinding and finishing processes. Some factors to consider include:
Workpiece Material Characteristics: Soft metals like aluminum, brass, copper, and mild steels may need moderate hardness abrasives like Aluminum Oxide to prevent excessive material removal, while harder materials like hardened steels and high-temperature alloys such as inconel and hardened Stainless Steel require abrasives with superior hardness and high thermal conductivity like CBN for precise and efficient cutting and grinding.
Machining Operations and Efficiency: Superabrasives like CBN are preferred for high-precision tasks where tight tolerances and maintaining material properties are paramount, while conventional abrasives like Aluminum Oxide offer lower cost solutions for general grinding of mild steel and soft metals.
Surface Finish and Material Removal Rates: Superabrasives like CBN excel in production applications of hardened steels and Superalloys that are sensitive to heat, , while conventional abrasives like Aluminum Oxide are effective in low volume applications and for grinding of soft metals.
Tooling and Machinery Considerations: Abrasive selection also needs to account for machinery and tooling capabilities. The truing and dressing of Superabrasive and Conventional Abrasive grinding wheels can be different and require different tools (stationary or rotary dressers of different configurations). Because of the difference in hardness between CBN and Alumina, Alumina being much lower, the amount of grinding debris resulting from wheel wear during grinding can be 100-300 x’s greater with the conventional wheel, which in turn needs to be disposed of. .
Both CBN and Aluminum Oxide abrasives offer distinct advantages in grinding and machining. Considering their unique properties with specific application requirements will lead to efficient and precise processes, ensuring optimal results and safety in the workplace. And if you ever need assistance, our grinding experts at CDT are here to help. Whether it's Superabrasives or Conventional abrasives, we can help find the perfect solution for your process.
How to Extend the Life of Your Electroplated Grinding Wheel
CDT’s “Strip and Replate” Program is designed to give our customers the highest quality grinding wheel abrasives for the longest time possible, in the most cost effective way for the customer. Learn how this process works and when you might need to do this >
CDT offers what’s called the “Strip and Replate” Program, designed to give our customers the highest quality grinding wheel abrasives for the longest time possible, in the most cost effective way for the customer (more on this in a moment)...
First, let’s cover when you’ll want to opt for this program, and how it works.
Stripping and replating a grinding wheel refers to the process of removing the old, worn-out abrasive material from the surface of a grinding wheel and replacing it with new abrasive material.
When customers opt in for this program, we work with you to create customized tooling that you will be able to use and then bring back to CDT for us to return it to “like new” condition after it begins to wear. This keeps your wheel fresh and performing at optimal levels without having to buy new.
When To Strip and Replate?
There are many reasons why you may need to replace your wheel with new abrasive, including:
The particles on the surface of your abrasive get clogged (potentially from metal shavings or debris from the grinding process)
Your wheel becomes dull from the worn out abrasive
You need to switch from grinding one material to another, and the new material requires a different type of abrasive to be put on your wheel
The grinding wheel has worn down unevenly, causing vibrations and reducing your wheel’s effectiveness
How Does The Process Work?
CDT is able to provide high quality strip and replate services through strip technology that will remove the remaining abrasive on your worn down wheel without damaging the surface finish of the core.
Electroplating involves depositing a thin layer of metal and abrasive particles onto the surface of a grinding wheel by using an electrical current in an electrolytic plating solution.
When a grinding wheel has reached its life, we remove the old abrasive material on your wheel by soaking the wheel in a chemical solution that will safely dissolve the deposited plating without damaging the integrity of the core.
Once the old deposit and abrasive have been removed, we apply a new layer of abrasive material through the electroplating process.
After the new abrasive material has been applied, the grinding wheel is re-balanced to ensure you continue to have smooth operation and optimal performance with your returned “like new” wheel.
When is An Electroplated Grinding Wheel The Best Choice?
Electroplated grinding wheels are considered the superior choice for applications that require complex shapes or geometries. Some specific applications include metal cutting tools, saw and knife sharpening, PCD grinding, and surgical tool blade sharpening – among others.
They’re used in a wide range of industries, including metalworking, woodworking, glass and ceramics, aerospace, automotive, medical, and electronics manufacturing.
Common materials that are compatible with an electroplated diamond grinding wheel include:
Cemented carbide
Glass
Ceramics
Fiberglass
Plastics
And more
Whereas common materials that are compatible with an electroplated CBN grinding wheel include:
Die steel
Hardened carbon steels
Hardened stainless steels
Alloy steels
Aerospace alloys
And more
When you add in the ability to strip and replate, it makes electroplating a superior choice in many ways:
It provides a more consistent and uniform distribution of abrasive particles on the surface of your grinding wheel, which can help ensure consistent grinding results and prevent uneven wear in the future.
Electroplating creates a strong bond between the abrasive particles and the wheel substrate, which helps prevent the abrasive from separating or shedding from your wheel during use.
It can be used to apply a wide variety of abrasive materials, including diamond, cubic boron nitride (CBN), and various types of abrasive grains – and it can be used with both brittle materials and soft metals.
Stripping and replating an electroplated grinding wheel is a relatively quick and straightforward process because they are a single layer wheel. It also allows for precise control over the thickness of the abrasive layer, making it an ideal choice for achieving any customizations you may need for your wheel.
Electroplated wheels can withstand heavy use and provide consistent grinding performance. They don’t need to be reconditioned as frequently as other types of grinding wheels, making them a more cost-effective choice in the long run.
Overall, opting for an electroplated grinding wheel to be reconditioned and used again through the CDT “Strip and Replate” Program can result in 40% more in savings, with consistent performance results, rather than opting for brand new plated products.
If you’re ready to learn how CDT can work with you for a customized electroplated grinding wheel that qualifies for our “Strip and Replate” Program, click the button below to request a quote!
The CDT technical team is ready to provide abrasive solutions to your questions that will increase your performance while reducing waste.
Top 10 Reasons to Work Third Shift at CDT
From longer weekends to higher pay, check out the top ten reasons you should apply for a third shift position at CDT.
Here at Continental Diamond Tool, we take our work seriously, but that doesn’t mean we don’t have a sense of humor! Whether you think of third shift as a “late shift” or a “late show,” there are lots of great reasons to work nights at CDT.
From longer weekends to higher pay, watch the video below to see the top ten reasons you should apply for third shift at CDT.
Drumroll please…..
Plated CBN for Aerospace
The mechanics of producing aircraft to safely transport people in such harsh conditions, however, is particularly challenging. The solution? Plated CBN grinding wheels.
Commercial airline travel may have taken a dramatic hit during the pandemic, but a rebound for the aerospace industry has already begun. 2021 marked the first all-civilian flight into space, and the possibilities this presents are especially exciting.
The mechanics of producing aircraft to safely transport people in such harsh conditions, however, is particularly challenging. Modern jet engines depend on superalloys to handle combustion temperatures of 1400ºC or more. These high-performance nickel-based materials have very high temperature stability, which makes machining components like turbine vanes extremely challenging. The solution is to use plated CBN wheels. Here’s why.
AEROSPACE DEMANDS
The aerospace industry asks a lot from their high-precision grinding tools. Specifically, aerospace grinding wheels must:
Remain hard at high temperatures
Be chemically inert to resist chemical reactions between grinding wheel and the nickel alloys
Provide excellent size control throughout a production run
Be available in complex forms
Not damage the workpiece – no burning or microcracking
Minimize residual stresses in the finished workpiece
Missing from this list is wheel life. While grinding wheel durability is important for Nickel based alloy grinding, it is less of a consideration for aerospace applications since their production runs are generally shorter than other industries like automotive. In this respect, plated grinding wheels provide a perfect middle ground.
Plated wheels are longer lasting than conventional abrasives, and they are capable of being refurbished through replating to extend their use. On the flip side, a plated wheel does not require the downtime for wheel dressing that a longer lasting Vitrified CBN wheel needs to maintain optimal performance. This makes plated wheels particularly well suited for applications with smaller lot sizes that don’t need an especially long life.
All of these considerations make plated CBN wheels an excellent option for aerospace applications.
ADVANTAGES OF CBN GRINDING TECHNOLOGY
As the hardest known substance, diamond might seem the obvious choice for grinding exceptionally hard materials. However, it doesn't perform so well at temperatures over 700ºC as it tends to react chemically with the material and deteriorates due to oxidation at higher temperatures. It's also vulnerable to attack by some of the chemicals found in grinding coolants, which reduces wheel life.
The alternative to diamond is Cubic Boron Nitride (CBN). This is a man-made or synthetic abrasive material that's not as hard as diamond but is harder than anything else. Unlike diamond, it retains its hardness at elevated temperatures. CBN offers superior resistance to chemical attack when grinding ferrous metal alloys. It exhibits no affinity to iron and doesn’t alter the material properties like Diamond does.
WHY PLATED WHEELS?
An electroplated grinding wheel has a single layer of superabrasive tightly bonded by a metallic layer to a solid metallic core. This has several advantages:
The bond material is below the tops of the grains, creating a free-cutting wheel that removes material rapidly with low power consumption, and helps keep interface temperatures down.
Good thermal conductivity helps take heat away from the grinding zone.
Wheel forms are readily achievable by machining needed geometries onto the metallic cores.
Worn wheels can be stripped and re-plated, making them an economical choice.
Costly dressing systems and rotary dressers aren’t needed, thus simplifying and lower capital expenditure on equipment.
THE AEROSPACE PROBLEM-SOLVER
Plated CBN grinding wheels are used extensively in aerospace. They perform well on exceptionally hard superalloys, providing high material removal rates coupled with excellent dimensional control throughout a production run.
The engineers at Continental Diamond Tool Corporation have extensive experience developing tools that can hold up to the rigorous demands of aerospace production. Contact us for a free grinding wheel analysis and quote.
CDT Starting A New Third Shift
Continental Diamond Tool has experienced extensive growth in Three of their most popular product lines, and they are now adding a third shift to their schedule to increase production and continue to fulfill global orders in a competitive timeframe. Apply today >
Continental Diamond Tool Starting A New Third Shift, Now Hiring
Continental Diamond Tool has experienced extensive growth in three of their most popular product lines, and they are now adding a third shift to their schedule to increase production and continue to fulfill global orders in a competitive timeframe.
The new shift will consist of four 10-hour shifts per week, from 8 p.m. to 6 a.m. This third shift will begin as soon as the open positions are filled, which may be as soon as August. All positions are entry-level and require a high school diploma. Job training will be provided.
CDT fosters an innovative, team-oriented environment for their employees, who enjoy paid lunch breaks, competitive wages, and health insurance benefits, along with additional benefits and overtime opportunities, in a clean, climate-controlled environment.
In business since 1973, CDT is a leading producer in the global market for superabrasive grinding wheels and custom tooling. Their 128,000 sq. ft. manufacturing facility in New Haven, Indiana, utilizes the latest technology to serve numerous industries including medical, aerospace, power generation, and more.
Additional information and applications are available by calling 800-443-6629 or visiting CDTUSA.net/careers.
Not Your Standard Plating!
Continental Diamond Tool now offers a new generation plated product available on carbide, aluminum, copper, or steel substrate bodies.
Now available in Carbide, Aluminum, Copper, and Brass
Plating has traditionally been a single layer of abrasive with either CBN or diamond attached to a steel body. CDT now has a new generation of plated products available on carbide, aluminum, copper, or steel substrate bodies.
Carbide is a great option for mandrels and similar processes where extra rigidity is needed. Carbide provides superior hardness, unsurpassed corrosion resistance, and the ability to retain its strength at extreme temperatures.
Aluminum is light weight and easier to handle than steel, making it better for processes that require labor intensive lifting. There is less strain on your operator when working with this tool. The reduced weight also exerts less stress and wear on your machine, prolonging the life of spindles and spindle bearings. This material is also resistant to rust and corrosion and has a high strength-to-weight ratio.
Copper also offers great corrosion resistance, and it is also malleable. Its inherent flexibility allows it to maintain adhesion even if a substrate is bent and manipulated post plate. This feature makes it ideal for processes that need extra pliability.
Brass is a solution we also turn to for its malleability. It is also a good choice for dressers, because it will not cause sparking. Many grinding machines run oil-based coolant, and sparks can cause the oil to ignite. Brass is superior for these especially flammable conditions.
Steel substrate is still a highly durable option for aggressive grinding applications. The strength of the steel is long lasting and prevents damage to the core.
Each material has its advantages. When you talk to a CDT grinding specialist, they will gather information about your manufacturing goals and recommend the substrate that has the right features for your application. Stop trying to succeed with the same grinding tools your competitors are using and instead gain an advantage with grinding solutions that are specially design with your process in mind for optimal performance.
If you would like to see if your plated grinding wheels would work better with a different substrate — or to find out about innovations in vitrified, resin bond, or metal bond grinding wheels that may benefit you — contact us for a free quote: 800-443-6629.