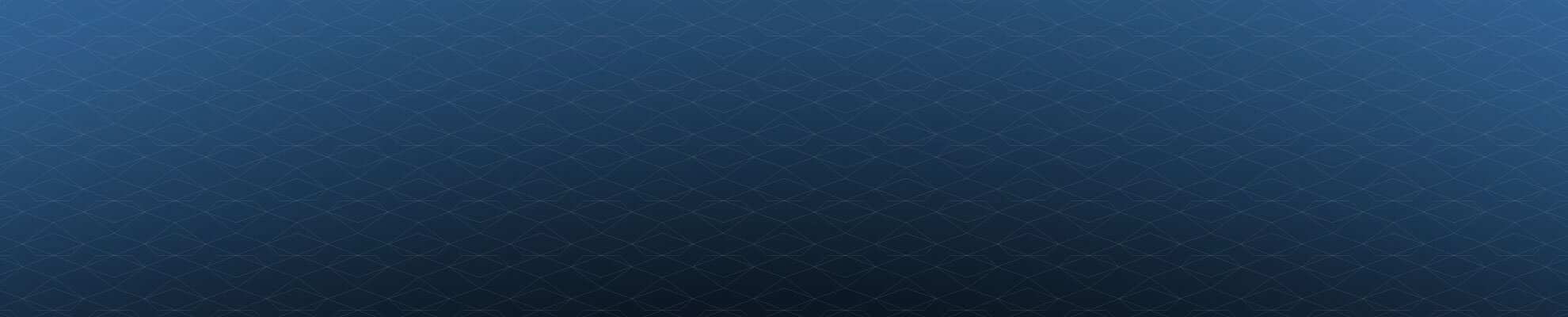
News and Resources
Browse by Category
Browse by Product
- All Dressing Products
- All Grinding Products
- CBN-Diamond Superabrasives
- Conventional Abrasives
- Diamond Lapping Compounds
- Diamond Rotary Dressers
- Diamond Stationary Dressers
- Hybrid Bond Grinding Tools
- Metal Bond Grinding Tools
- Plated Grinding Tools
- Resin Bond Grinding Tools
- Vitrified Bond Grinding Tools
Understanding Precision Polishing Film and Its Role in Precision Manufacturing
Did you know you can order Precision Polishing Film through CDT? In this article, we talk about Precision Polishing Film and its role in refining surface quality on metals, ceramics, optics, and more. Learn about its types, applications, and integration into precision manufacturing solutions.
In precision manufacturing, achieving a flawless surface finish is fundamental for product functionality and aesthetics. Precision polishing film, a specialized material used in the final polishing stages, stands as an important tool in refining and perfecting surface quality to meet rigorous industry standards.
What is a Precision Polishing Film?
At its core, precision polishing film is crafted by coating an abrasive material onto a flexible polyester substrate. This film refines surfaces and ensures precision across a variety of materials including metals, ceramics, optics, and semiconductor wafers.
3 Types of Precision Polishing Film
There exists several varieties of precision polishing film, each tailored to specific surface refinement requirements:
Mirror Film: Noted for its fine-graded abrasive grains uniformly coating the polyester film, mirror film offers superior sanding capability and durability.
Lapping Film: With micron-graded abrasive grains uniformly distributed in resin adhesive, lapping film consistently delivers accurate and high-quality finishes.
Diamond Lapping Film: The diamond abrasive in this lapping film makes it particularly suitable for precision finishing of extremely hard substances or challenging materials such as ceramic and ferrite compounds.
Broad Industry Applications
Precision polishing films are useful for many applications across diverse industries. They play an essential role in enhancing the surface of roll and shaft materials, flat displays, commutator shafts of micro motors, and magnetic heads and disks. These films are equally prevalent in the manufacture of many disc applications such as plastic lenses, optical devices, fibers, and painted surfaces. Additionally, sheet applications like print circuit boards and optical devices incorporate precision polishing film in their manufacturing processes.
Extending Beyond Our Core Specialties
While Continental Diamond Tool (CDT) is known for its high-quality, custom diamond and CBN grinding products, alongside precision diamond dressing tools, our commitment to excellence encompasses more than our specialized niche. Our expertise extends to supplying other essential grinding and polishing solutions, including precision polishing film, to address the evolving needs of our customers. This highlights our dedication to addressing a wide array of precision manufacturing requirements.
The CDT Advantage:
A Legacy of Quality: We ensure consistent, superior-grade products that adhere to stringent industry standards.
Customized Solutions: Our skilled technicians offer customized solutions, ensuring optimal performance for unique customer requirements.
Comprehensive Support: From concept to implementation, our expert team provides guidance to maximize productivity and achieve the best possible outcomes.
Expanded Offerings: Alongside our core expertise, we equip customers with grinding and polishing essentials, including precision polishing film, ensuring a comprehensive suite of tools for optimal surface refinement.
Backed by Uncompromising Quality
Our precision polishing films, like all products supplied by CDT, are made of the highest quality materials with various thicknesses available, starting at a minimum of 25 microns. The polyester film’s uniform thickness, smooth surface, and strength provides strong resistance to pulling and tearing forces, with less elasticity.
This table outlines the extensive variety of options available:
For detailed information on our precision manufacturing grinding and finishing products and their benefits to your operations, contact us today.
Diamond Lapping Compounds
CDT lapping and polishing compounds are excellent for mold, die, and tool polishing.
CDT lapping and polishing compounds are excellent for mold, die, and tool polishing. These compounds also provide superior results when polishing to final tolerance of ceramic parts, tool-room use, and many other high finish and tight tolerance performance applications.
Diamond is the hardest and the most abrasive-resistant material used in nearly every type of industry. Our diamond lapping compounds use these unique characteristics to improve your finishing capabilities. You may choose to add diamond powders to the polishing paste in some instances.
Whether your job calls for high stock removal, fast polishing times, or superior finishes, you can find a compound that will help you achieve better results and a mirror finish. Both water and oil soluble compound are available in 5 and 18 gram syringes. Our syringes are disposable plastic dispensers that are convenient and safe from outside impurities.
Key features and benefits include:
Faster cut rates
High surface finish
Excellent surface tension
Quality viscosity
Low evaporation rate
Key adhesion to tools and surfaces
Easily cleans surfaces with both water and oil
Customers often ask what grit do we use for mold, die, and tool polishing? Our engineers are happy to assist you in finding the best compound for your specific application: 800-443-6629.
Since 1973, CDT has lead the field in providing technically superior precision tooling solutions to numerous industries. If you need rapid, accurate lapping, polishing and super-finishing, contact our technical team to learn more about our diamond lapping compounds.
Precision Finishing With Diamond Lapping Compounds
In many applications the finish resulting from grinding is good enough. When it isn't, the next step is lapping. As with grinding, diamond makes an excellent abrasive, but for best results needs to be selected and used appropriately.
A good quality grinding wheel on a rigid machine can produce a surface with a roughness around 0.25 microns Ra. In some applications this isn't enough; in others flatness is of greater importance than finish. In either situation the next step is to move on to lapping.
PRECISION FINISHING
In lapping an abrasive compound, composed of abrasive particles in a liquid or paste transport medium, is placed between the work piece and a lapping plate. Movement of the plate rolls the particles across the surface, removing raised peaks and flattening high regions. Depending on the work piece material, roughness numbers of under 0.30 microns Ra are achievable.
Other reasons for lapping are to bring something down to a precise and uniform final size and to produce a very flat surface. (Think of flatness as the rolling of hills and valleys, while roughness is the furrows plowed in the field.) Lapping doesn't put any stress or heat into the surface, and the low cutting forces make it a distortion-free way of finishing thin-wall parts.
LAPPING WITH DIAMOND COMPOUNDS
A number of abrasives can be used but diamond has several advantages:
highest material removal rates, by virtue of it's exceptional hardness
excellent surface finish, because the edges cut cleanly and diamond can be graded down to micron-level. (Producing a uniform, scratch-free surface demands particles of the same size: any that are larger will produce undesirable scratches.)
When lapping, standard practice is to use a cast iron lapping plate. For lapping with superabrasives (diamond or CBN) though it's recommended to use a composite metal plate such as tin, copper or cast iron.
The transport medium used in a diamond lapping compound can be either oil or water soluble. Oil soluble compounds are the most common and can be used on ceramics, carbides, cast iron and other metal surfaces.
A water soluble compound is used when the work piece is sensitive to oil. It's often employed for finishing electronic and electro-optical components and is widely used for magnetic read/write heads and semiconductor applications.
Companies like CDT supply precisely graded diamond lapping compound in syringes for easy dispensing. The coarsest grades, in the region of 40 to 90 microns, gives rapid stock removal while smaller particle sizes are used for finishing. To give one example, an application like preparing metallographic samples needs abrasives of less than two microns in size.
CHOOSE YOUR DIAMONDS CAREFULLY
In many applications the finish resulting from grinding is good enough. When it isn't, the next step is lapping. As with grinding, diamond makes an excellent abrasive, but for best results needs to be selected and used appropriately.