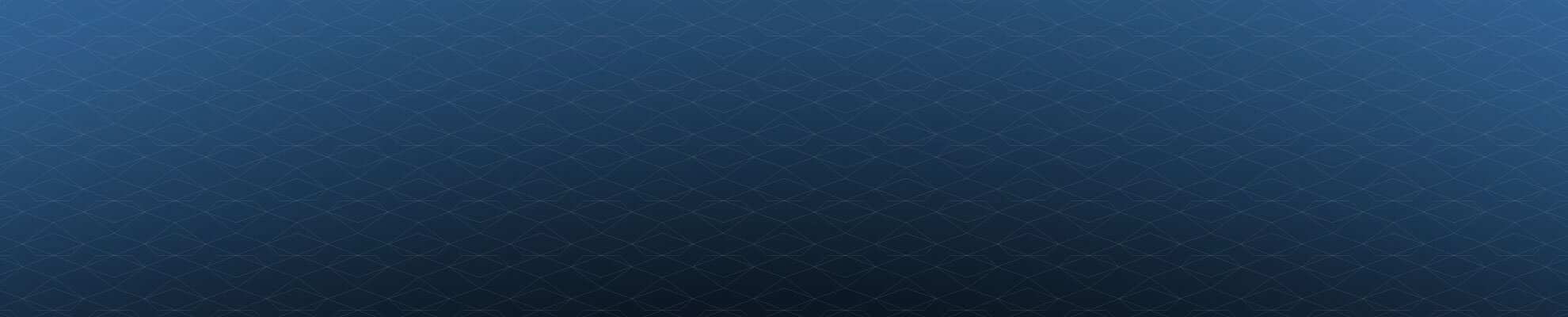
News and Resources
Browse by Category
Browse by Product
- All Dressing Products
- All Grinding Products
- CBN-Diamond Superabrasives
- Conventional Abrasives
- Diamond Lapping Compounds
- Diamond Rotary Dressers
- Diamond Stationary Dressers
- Hybrid Bond Grinding Tools
- Metal Bond Grinding Tools
- Plated Grinding Tools
- Resin Bond Grinding Tools
- Vitrified Bond Grinding Tools
5 Common Questions About Industrial Diamonds For Grinding
All of the most commonly asked questions are answered in Continental Diamond Tool's latest blog about industrial diamond technology for grinding.
1: What are industrial diamonds, and how are they used in grinding wheels?
Industrial diamonds can be either synthetic diamond or natural diamond and are specifically processed for industrial applications, rather than for jewelry.
Industrial diamonds are used in grinding wheels as an abrasive that removes material from a workpiece through friction and cutting. When the grinding wheel rotates against the workpiece, the diamond particles (abrasives) efficiently remove small particles of the workpiece – resulting in geometry, size, and finish desired.
Because diamond is the hardest known material, grinding wheels with diamond abrasives are commonly used in hard material applications that require high precision and accuracy such as in the aerospace, automotive, medical and semiconductor industries. CDT has experience working with grinding operations in all of these areas.
2: How are industrial diamonds manufactured?
Natural diamonds have been used for a long time in industrial grinding. They are mined from the earth and transported to a plant for processing. Through a system that includes x-ray machines and hand sorting, the gem quality diamonds are separated from industrial diamonds. These small, lower-quality stones, otherwise known as ‘boart,’ can be used in equipment such as grinding wheels, drill bits, and dressing tools.
Synthetic industrial diamonds used in grinding wheels can be made in one of two ways:
High-pressure and high-temperature (HPHT)
Chemical vapor deposition (CVD)
In the HPHT method, diamond-creating materials are put under high pressures and high temperatures to make it form into a diamond. In the CVD method, diamond-creating materials are put in a vacuum chamber where carbon gasses are then added to make it form into diamond.
Whether naturally or synthetically sourced, the industrial diamonds are then crushed, milled, cut, shaped, and polished to customizable sizes and shapes. Then, the particles are bonded together to form a grinding wheel or cutting tool, typically using metal, resin, vitrified materials or electroplated in a single layer onto a metallic substrate.
3: How do the properties of industrial diamonds affect the performance of grinding wheels?
Industrial diamonds are valued for their extreme hardness, wear resistance, and thermal conductivity. All of these impact the performance of a grinding wheel.
Extreme Hardness:
Diamonds are known for their extreme hardness because they are made up of carbon atoms that are held together in a cubic crystal lattice structure. You can think of it like a brick wall, where the precise arrangement and spacing of the bricks represents the arrangement of atoms in the cubic crystal structure. Like a brick wall, diamond is strong and stable, making it difficult to break or become deformed.
Because diamond is the hardest known material, it is not readily scratched by other materials. Instead, it does the scratching. Because of the high strength of the carbon bonds, Diamond has the best wear properties of all abrasives unless chemically attacked by materials that react with carbon.
This gives grinding wheels the ability to precisely cut through and remove material from other hard substances like ceramics, glass and non-iron-containing metals with very precise geometries and dimensional tolerances.
Wear Resistance:
A diamond's wear resistance refers to its ability to maintain sharp edges and cutting ability for longer, which results in longer-lasting grinding wheels that don’t need to be replaced as often.
Diamond particles can withstand high pressures generated during the grinding process – a crucial aspect of grinding that can cause other abrasive options to break down. Whereas the wear-resistant nature of a diamond abrasive maintains a durable, precise size and finish.
Thermal Conductivity:
Diamonds have the highest thermal conductivity of any known material, which is ideal for grinding due to the heat generated by the friction that occurs during the grinding process. Heat can cause abrasive particles in the wheel to become dull and less effective at cutting, as well as cause thermal damage to your workpiece.
Diamonds can conduct heat away from the grinding area more effectively than other abrasive materials. This keeps it cooler, protecting the material being ground from thermal damage and preventing the abrasive from becoming dull.
4: What are the advantages and disadvantages of using industrial diamonds in grinding wheels compared to other abrasive materials?
Advantages:
Diamond is the hardest known material due to it’s strong covalent bonds between carbon atoms and perfect crystal symmetry. Because Diamond is harder than all other materials it is the best choice for grinding and wear resistance. Other abrasives are softer than diamond and therefore do not last nearly as long. Secondly, Diamond also has the best thermal conductivity and therefore removes/dissipates most effectively the heat generated during grinding.
All of this makes diamond an advantageous choice as an abrasive because it will provide a longer-lasting durability, an improved precision, and a better quality finish.
Disadvantages:
Because of its high hardness, it also means that diamonds can’t be easily shaped or molded into different forms. Dressing of diamond wheels is done with Diamond tools, and with Diamond on Diamond, dresser life is low when compared with other abrasive types. Secondly, Diamond grinding wheels are not recommended when grinding ferrous metals as a chemical reaction between Carbon (Diamond) and the metal is possible and results in changes of the material properties of the metal and premature wear of the Diamond grinding wheels, both of which can be detrimental. Therefore, diamond is typically suggested for use in specialized applications for grinding of hard materials such as Ceramics, Carbides, and glasses.
5: What are the latest trends and advancements in industrial diamond technology for grinding wheels?
One of the latest trends in industrial diamonds is the increasing use of synthetic or man made diamonds. Diamonds that are grown in a lab are as real as diamonds mined from the earth. They are identical to natural diamonds in every way, except that they are created in a lab and the specific material properties of the Diamond can be tailored to specific applications..
As this process has gotten more efficient, man made diamonds can now be sourced cheaper and more readily than natural diamonds. Diamond grinding products are becoming more economically viable for a growing number of industries. CDT uses both natural and synthetic diamonds in its superabrasive products.
Another advancement in industrial diamond grinding technology is the creation of hybrid bond grinding wheels. Hybrid wheels combine different types of bond to adhere the abrasive material, such as diamond, to the grinding wheel and achieve superior grinding performance.
Traditionally, diamond grinding wheels use one of a handful of bonding agents to adhere the superabrasive material to the grinding wheel. Bonding options include:
Electroplating
Resin bond
Metal bond
Vitrified bond
Each of these bonding options have different characteristics which result in different pros and cons for the grinding process. You can learn more about the different bond types here.
By combining bonds, hybrid wheels can be tailored to the needs of specific grinding applications, resulting in higher efficiency and reduced costs. CDT specializes in cutting edge, customizable hybrid bonds using diamond abrasives to provide superior results for our customers. You can learn more about our hybrid bonds here.
Industrial diamonds are a crucial component in many grinding processes, and they continue to play a vital role in the manufacturing industry. Because of their ideal thermal conductivity, wear resistance, and hardness, the technology will continue to advance to make the most use out of this favorable material. It is safe to say that industrial diamonds are not going away anytime soon, and their importance in the manufacturing industry will only continue to grow from here!
If you are wondering if diamond grinding wheels or tools would be a good fit for your specific application, contact CDT for a free quote.
Why Choose Continental Diamond Tool?
There are a lot of reasons to consider Continental Diamond Tool, but we’ve narrowed it down to the top three reasons customers choose CDT. Check it out >
There are a lot of reasons to consider Continental Diamond Tool, but the top three reasons customers choose CDT are our high level of service, quality, and consistency.
Quality is the highest priority at CDT. We’re ISO Certified, with checks and balances in place to make sure each tool is the highest quality, every time.
Consistency means repeatability, so your tool is the same from one order to the next. You don’t deviate in your usage, so we have to nail it every time, with the tightest tolerances.
CDT has made customer service a main focus. Jeff Turner, Inside Sales, says, “It’s a priority that I take very seriously. Each customer should feel like they’re our biggest one.”
If you’re wondering why CDT, reach out to us. We will follow up so you can see if we can meet your needs, including our Grinding Lab, where we can show you first hand the benefits that you can get from our tooling.
Learn more about the reasons CDT is committed to you here:
What should you look for in a grinding wheel manufacturer?
Finding the right supplier of custom manufactured grinding wheels is crucial when your production is on the line. Here’s why you should consider trusting in CDT >
When you’re in search of a supplier of custom manufactured grinding wheels, we know you’re going to be focused on three main components: delivery, performance, and support.
At CDT, we deliver engineered solutions to help you complete your project on time. We will also meet or exceed any requirements you have for surface finish, tolerance holding, cycle time reduction, or anything else for which you are needing engineer solutions. We also provide support throughout the duration of the entire project, from beginning to end.
“We provide information and support all along the way,” says Harrison Sheldon, Application Engineer.
Watch our video to find out more about our commitment to excellence for our customers:
What is the benefit of having a grinding lab on site?
Our grinding lab gives us the opportunity to work with customers to develop grinding processes that are specific to their materials, equipment, and applications. Learn more >
Here at CDT, we have a technologically advanced research and development grinding lab. This gives us the opportunity to work with customers to develop grinding processes that are specific to their materials, equipment, and applications. Our setup is unique, in that we’ve added numerous extra sensors to capture data on every element of the grinding process, to replicate what’s happening in the customer’s actual facilities.
We have a twofold product commitment to the Grinding Lab. One, we can develop processes for the customer and their specific application. Two, we can internally develop advanced new products that solve issues for customers before they are even known.
CDT’s customer service commitment includes the lab as well, inviting customers to reach out to us, to use our grinding lab to solve their grinding problems. Benefits to CDT customers include:
Faster product development
Cost savings/reduced risk
Opportunities to innovate
Valuable data
Remote product testing
Read more about these benefits here or watch clips of the Grinding Lab in action, and hear more about it from Jeff Wirth, our Engineering Manager in this video:
Why Superabrasives?
Superabrasive grinding wheels last longer, grind faster, cut cleaner, leave a better finish and create a sharper edge. The real question is—Why not?
When the material you are trying to process is either too hard or too delicate for conventional abrasives, custom superabrasive grinding tools might be the best solution.
What are Superabrasives?
The term “superabrasives” refers to a class of tools used in precision grinding for many industries. Superabrasive grinding products contain natural diamond, manmade diamond, and/or CBN — some of the hardest materials that can be made. Superabrasives are also sometimes called industrial diamonds: an industrial diamond is a non-gem quality small diamond that is for abrasives, cutting, and drilling tools. Other types of superabrasives include:
Cubic boron nitride (CBN): Usually called CBN, this is the second hardest cutting tool material after a diamond.
Polycrystalline: This is an abrasive material that has multiple collections of crystal grain structures with individual orientations.
CVD Diamond: These are synthetic diamonds made by a process known as chemical vapor deposition. CVD diamonds grow from a hydrocarbon gas mixture. They are extremely hard and have a high thermal conductivity that is five times that of copper. They also have broadband optical transparency, are chemically inert, and only reach graphitization at very high temperatures.
Nano-diamonds: These tiny diamonds are the product of a controlled explosion. They are sometimes called detonation nano-diamonds (DND) or an ultra-dispersed diamonds after how they are formed.
These abrasive materials have been labeled as superabrasive due to their extraordinary hardness, unparalleled performance, and longevity. Continental Diamond Tool uses these superabrasive materials to make custom grinding wheels and products, including plated, vitrified, resin bond, metal bond, hybrid bonds, and rotary dressers, for many complex applications.
Superabrasives vs. Conventional Abrasives
Superabrasives, whether natural or manmade, have a hardness range that distinguishes them as some of the most durable materials on Earth. Conventional abrasives are made with much softer abrasive materials that are less expensive but break down faster. The best abrasive product for your application depends on the material you are grinding and what properties you need to achieve your desired results.
Industries that Use Superabrasives
A great number of industries use superabrasive grinding wheels, and the custom-coated abrasives subsection of the abrasives industry continues to grow. Industries that regularly invest in superabrasive grinding wheels are:
Aerospace
Automotive
Medical
Electronics
Composites
Oil Industry
Advantages of Superabrasives
The advantages of superabrasive grinding wheels are more than extraordinary hardness, unparalleled performance, and longevity. These three features of superabrasives are the core of many advantages manufacturers gain by an aggregation of services that normal abrasives simply cannot deliver.
Benefits include:
Less expensive tooling and fixturing costs
More wheels on the spindle, smaller wheels, multiple operations
Less floor space needed for manufacturing
Virtual elimination of wheel wear
Automated CNC machines, less labor intensive operations requiring less training
Consistent surface speed from part to part
Better overall throughput with fewer machines needed
Improved material removal rates, lower per part abrasive costs, and higher speeds
With superabrasives, industries have been able to increase production with automated CNC equipment, compensating for a lack of available, skilled labor. With custom superabrasives that are optimized for their process, machine capabilities, and mechanization, there is less reliance on operator technique. A properly defined process, combined with automatic loaders, make for equipment that can even run itself in some cases with lights out manufacturing.
Industry Outlook
Future growth of the abrasives industries will primarily be in superabrasives. Currently, research and development of superabrasives are taking place in the following areas:
Custom designed “hard to grind” materials in an increasing number of industries
Creep or deep feed grinding
High-speed, high-performance grinding of hardened steel
Form grinding, sometimes with electroplating, in high precision, high-removal, and high-surface quality applications
CNC-control of line grinding machines
Continental Diamond Tool stays on the forefront of new abrasive technology developments in superabrasives with our state-of-the-art grinding lab focused on research and development of new hybrid bonds that take the efficiencies of superabrasives even further.
How to select the right superabrasive
CDT has a strong group of engineers, product managers, and technical sales people who can come out to your facility to review your equipment and processes, and the parts you’re looking to grind. Or, as Troy Giacherio, Product Manager for Rotary Dressers, suggests, “you can come into our facility and we’d be more than happy to have the conversation, review the whole development process, and then make our recommendations based on what we’ve seen and communicated.” Contact us for a free quote.
Learn more about superabrasive grinding solutions in this video:
Does CDT Carry Stock?
A lot of customers ask if we keep stock inventory on the shelf. Check out the answer in this article >
A lot of customers ask if we keep stock inventory on the shelf.
Because our customers’ needs are diverse, there are not a lot of common tools used across industries. Therefore, it is really most beneficial to us - and our customers - to only build custom. This gives us the flexibility to deliver exactly what the customer is looking for in a timely manner.
Customers are often surprised at how quickly and affordably we can deliver custom grinding wheels. We manage our inventory, control our overhead, and keep our costs low, so we can pass those savings on to our customers.
Watch this video to learn more.
To get started with custom superabrasive grinding wheels from CDT, contact us for a free quote.
How much does a Custom Superabrasive Grinding Wheel Cost?
We look at the 'total cost' of a custom superabrasive grinding wheel from CDT, and detail the advantages superabrasives have over conventional grinding products. Check it out >
A Look at the Bigger Picture >
As a custom-made product, the cost of a superabrasive grinding wheel can vary greatly from one design and application to the next. People may shy away from custom products because they think one of two things: it’s going to cost a lot more or it’s going to take a long time to complete. While that may be partially true on the surface, that’s not the whole picture.
In this article, we’re going to take a look at some of the factors that will help you assess the “total cost” of custom grinding products, which includes both what the product is and the value it provides over time. When taking everything into account, our clients often find that the custom grinding product that appeared to be too expensive actually has a return on investment that quickly pays for itself.
Here are 4 advantages to purchasing custom superabrasive grinding wheels from Continental Diamond Tool so you can weigh their value long-term:
1) Custom Grinding Wheel means a better fit.
With the right custom grinding wheel, customers have reported upwards of a 70% improvement in efficiency from conventional wheels. Our engineers work with you to reduce cycle times, maximize removal rates, minimize maintenance requirements, decrease material damage, and improve productivity wherever possible.
During the design phase, we can run simulations from our facility or travel to yours. We frequently visit customers to learn their machinery, materials, and processes so we can design a better grinding wheel that works for what they need. Some of our product options can be incorporated into lights out production which can be an even great boost to your company’s overall efficiency.
With each tool custom designed for your unique application, you get productivity out of your grinding wheel that you’ve likely never seen before. When you factor in these benefits, ROI skyrockets.
2) Custom Grinding Wheel means quality work.
Conventional wheels off the assembly line will never match the quality of custom grinding wheels from an experienced manufacturer. Custom grinding wheel manufacturers generally do not cut corners like you see with commodity products. At CDT, we use the best quality materials because it’s in our best interest to maintain longterm relationships with customers and the superiority of our products.
Experience can also be a factor with quality. Even within the industry of custom superabrasives, inexperienced engineers can cost you in development time, troubleshooting hassles, and subpar products. At CDT, we have almost 50 years of experience in old and new grinding technologies. And we’re always updating our quality control systems with state-of-the-art precision testing equipment to make sure you are getting the most efficiency from your custom grinding wheel investment.
3) Custom Grinding Wheel means the product will last.
Superabrasive grinding wheels are made from natural diamond, manmade diamond, and CBN —some of the strongest materials known to man. Conventional abrasives are made from materials like aluminum oxide and silicon carbide — much softer materials that break down more quickly. Depending on your application, a more durable product that you don’t have to replace as often may actually be a better investment.
Additionally, we have options with some of our superabrasive products where we can recommend dressing tools and even refinishing or replating services that can make your grinding wheels last even longer.
4) Custom Grinding Wheel means a great customer experience.
You may be wondering how great service actually saves you money. First, the customer service team at Continental Diamond Tool provides free quotes, product selection and design assistance. You don’t have to research and guess what you need. A specialist will provide product recommendations and a competitive quote for you for free.
Second, a company like CDT whom you have a personal relationship with will do everything they can to help. For example, we know that waiting on a grinding wheel order can be painful for your company’s productivity and bottom line. Delays may throw off your production calendar and anger customers. That is why we’ve taken measures — like stocking an extensive inventory of raw materials — so we can deliver your order faster than others in the industry. Additionally, once your product has been developed, a reorder can be produced and shipped much faster.
Third, service doesn’t stop at the sale. While some big name custom superabrasive and conventional wheel manufacturers have cut corners in service for better bottom lines, CDT has remained true to our founding principles. Does your grinding wheel supplier train your team on installation and maintenance? Will they come to your facility to review your machinery and processes to make sure your grinding wheel is optimized for peak performance? Do they notify you when new technology becomes available that could make your processes even more efficient? At CDT, our personal sales team and tech support are here to help you overcome the obstacles to increased productivity and success.
Learn more about superabrasives and how they differ from conventional grinding wheels in this video:
To get started with custom superabrasive grinding wheels from CDT, contact us for a free quote.
How Has CDT Handled the 2020 Pandemic and Its Aftermath?
At CDT, we're always looking ahead. In this video, President Nick Viggiano explains how CDT has continued to provide products reliably for customers despite all the challenges of 2020.
2020 was a set back for economies across the world, but by making wise use of this time, CDT is poised to spearhead the recovery for themselves and their customers in 2021 and beyond.
“At CDT, we are always trying to look ahead and prepare for what’s around the corner,” says Nick Viggiano, President of CDT. “In 2020, during the pandemic, we had time to develop a state-of-the-art grinding lab, make improvements to our quality protocols, and upgrade our ERP systems.”
“We felt that production would go through the roof once we got past the pandemic, so we spent more on capital equipment in 2020 than any other year prior. With the explosion in growth we’ve experienced this year, we will surpass that with all the new technology we are bringing into our manufacturing facility.”
During the first half of 2021, CDT experienced major supply chain issues like much of the manufacturing sector. The purchasing team worked closely with vendors to anticipate supply bottlenecks. At the first hint of trouble, CDT ordered six month supplies and quarantined it as safety stock for key materials such as Diamond, CBN, steel, aluminum, and powders.
“We never wanted to tell a customer we couldn’t make something because we didn’t have the materials,” says Nick. “This approach opened new doors for us this year when other less-proactive manufacturers had to let their customers down. They found us, and we were more-than-willing to help!”
The labor shortage has been another source of worry for businesses. To be up 50% this year in manufacturing custom tooling has been a tough challenge for the CDT team.
“We’ve always had a family culture at our workplace that appreciates and rewards our employees’ contributions, but this year we’ve explored more unique ways to attract talent in our area,” says Nick. “We launched a video social media campaign to highlight the fun culture and unique benefits we offer such as golf memberships and fitness center. These efforts have paid off with lots of great new people joining our team while continuing to get 75-100 new applications a month.”
“CDT is growing, and I’m very proud of what this company is achieving and where we are headed!”
Is Continental Diamond Tool ISO 9001 Certified?
Continental Diamond Tool has implemented and maintains a Quality Management System that meets the requirements of ISO 9001:2015, as a manufacturer and distributor of Super Abrasive Grinding Products.
Quality Management
ISO 9001 Certification
Continental Diamond Tool Corporation in New Haven, Indiana, USA, underwent its most recent ISO audit in April 2024, conducted by IsoTec Alliance. A similar recertification audit at Continental Diamond Tool Limited in Kinmel Bay, Rhyl, U.K., was completed in February 2023 in collaboration with BM Trada. The comprehensive review covered all processes and documentation, with a particular emphasis on control plans, training records, and employee interviews across various departments. Following the rigorous four-day assessment, the auditor granted recertification for ISO 9001:2015, highlighting the company's steadfast commitment to maintaining superior quality management practices.
The ISO program mandates meticulous review of all processes, establishment of Standard Operating Procedures (SOPs), work instructions, and control plans, along with comprehensive training sessions for employees at all levels to ensure familiarity with ISO procedures. The Stage 1 audit, typically lasting one day, serves as an initial assessment by IsoTec Alliance to gauge readiness for Stage 2. Upon successful completion of Stage 1 with no issues detected, IsoTec recommends progression to Stage 2. Stage 2 entails a thorough four-day audit, during which auditors scrutinize all facets, including documentation and processes, to validate adherence to prescribed practices. This includes thorough examination of control plans, training records, and interviews with employees across various departments. Following the Stage 2 audit, a closing meeting is convened to assess the company's compliance, and if deemed satisfactory, certification for ISO 9001:2015 is granted. The official certificate is then issued to the company several days after the audit's conclusion.
Recertification audits are obligatory every three years to maintain ISO 9001:2015 status. These audits serve to ensure continued adherence to the stringent requirements outlined by the ISO program, underscoring the company's ongoing dedication to operational excellence and continual improvement.
Custom Rotary Diamond Dressers in as little as 4 weeks: How do we do it?
Industry-standard lead times for diamond rolls can take 8 weeks or more. If you are looking for a better, faster rotary diamond dresser alternative, we can expedite service in as little as 4 weeks. Learn how >
Since 1984, Consort Precision Diamond has supplied diamond wheel dressing products to a broad range of industries including aerospace, aircraft, automotive, blade and knife, power generation, medical, cutting tools, tool & die, saw, gear, and bearing and many other applications. What all these grinding operations have in common is that they typically require some form of wheel dressing to re-establish the wheel profile and/or recondition the wheel face.
About Wheel Dressing or Conditioning
Wheel conditioning involves the sharpening and opening of the wheel face, while also removing dull abrasives, excessive bond, and workpiece material (loading). A sharp and open wheel face will allow maximum possible material-removal rates and reduced thermal stress on the workpiece.
Consort’s rotary dressers provide the ideal profile for your desired wheel topography, with superior materials and manufacturing technology. Because your dresser is custom manufactured, demanding and complex configurations are possible.
Diamond Roll Delivery in as Little as 4 Weeks
The question then turns to delivery and lead times. In business, time is money. Industry-standard lead times for custom rotary diamond dressers can take 8 weeks or more. That’s a long time to wait for a critical part in your manufacturing process. Consort has made a reputation for fast delivery with a standard lead time of 6-8 weeks.
Need a tool in a hurry? Customers can request “Expedited Service” for custom diamond roll delivery in as little as 4 weeks. With manufacturing, delaying maintenance can really add to your costs in the long run. When a job is expedited, we work with our customers to get them their tooling as soon as possible.
We pride ourselves on prompt service and communication. At any time, you can reach out to your Consort account representative to begin an order or find out its status. If you do not have an account rep, please reach out to our customer service through our website online form or call 800-443-6629.
Lead times should not be a hurdle in the proper maintenance of your grinding equipment. If you are looking for a better, faster diamond roll supplier, let our service techs help you get the process started.
How Long Does it Take to Get a Custom Grinding Wheel?
In business, time is money. Industry-standard lead times for custom grinding wheels can take 8 weeks or more. If you are looking for a better, faster grinding wheel alternative, let our service techs help you get the process started.
Customized superabrasive grinding solutions have many advantages over conventional grinding wheels — primarily in performance. Custom CBN and Diamond grinding wheels improve efficiencies, last longer, and produce better quality results. Once you transition to a custom grinding wheel, the value of the investment becomes clear.
The question then turns to delivery and lead times. In business, time is money. Industry-standard lead times for custom grinding wheels can take 8 weeks or more. That’s a long time to wait for a critical part in your manufacturing process. CDT has made a reputation for fast delivery with a standard lead time of 4 weeks.
Need a tool in a hurry? Customers can request our Rush Program to expedite service for custom grinding wheel delivery in as little as 2 weeks. With manufacturing, every minute a machine is down, you feel the pinch. When a job is a rush, we work with our customers to get them up and running as soon as possible.
We pride ourselves on prompt service and communication. At any time, you can reach out to your CDT account representative to find out the status of your order, or email customer service at info@cdtusa.net. We send tracking numbers via email with your invoice when your order ships. You can also request tracking information through customer service at 800-443-6629 or through our website contact form.
Once you have placed an order with us, your wheel specifications will be held on file for quick processing and delivery of reorders through your account rep or our customer service department.
Lead times do not have to be a hurdle for transitioning to custom superabrasives. If you are looking for a better, faster grinding wheel alternative, let our service techs help you get the process started.
Where to Get Grinding Wheels in Stock, on Demand
At CDT, we cater to our customers needs. We keep precise records of every wheel we manufacture. If there is a wheel you regularly need in stock, let us know and we will make it available upon request.
At CDT, we are often asked if we stock grinding wheels. As a custom grinding wheel manufacturer, our wheels are designed to specific manufacturing processes. Universal (stock) grinding wheels rarely match the performance of our custom superabrasives in unique manufacturing settings.
That said, we can help you design a grinding wheel that maximizes performance, and make sure that wheel is available when you need it. Or if there is a stock wheel you know works great, we can have that on hand for you, too. When you find a grinding wheel manufacturer that understands your process, reorders are easy.
Choosing Your Grinding Wheel Manufacturer
CDT, like most manufacturers, lists the grit type, grit size, wheel hardness, structure, and bond using a code for every grinding wheel produced. However, there is no standard among manufacturers defining what these codes mean — the specification alone does not tell the whole story. This makes it difficult to take a grinding wheel from one manufacturer and substitute it for another grinding wheel of equal marking.
What if you are unhappy with your current grinding wheel source? Assuming you need your grinding wheel to perform exacting work and you want to limit your grief, we recommend you get guidance from an experienced grinding wheel specialist before making a substitution.
At CDT, we can interpret the codes on your grinding wheel and get a close approximation. Even so, you should expect some trial and error when converting from one brand of wheel to another. Dialing in the precise settings is a process, but it’s worth it to find a grinding wheel manufacturer who offers consistently competitive quality, delivery times, and price.
Ordering Replacement Grinding Wheels
Once you have your custom grinding wheel working efficiently, and you are happy with your manufacturer, you want to know you can get that grinding wheel on demand.
At CDT, we cater to our customers needs. We keep precise records of every wheel we manufacture. If there is a wheel you regularly need in stock, let us know and we will make it available upon request.
What Products Are Available?
CDT manufactures all the most popular superabrasive products on the market today: plated, resin bond, metal bond, and vitrified grinding wheels. Within our resin line, we have our GL Series that is comparable to a hybrid bond wheel and provides even more customizable performance options. Your best choice depends on your industry, material, process, and objectives.
In addition, we offer many types of dressers to keep your grinding wheels operating at peak performance — from diamond rotary to stationery varieties. We also have diamond lapping compounds, used in polishing materials to a mirror finish.
Why Use Plated Diamond or Cubic Boron Nitride Tools?
Coatings applied during the plating process are either metallic, diamond, or cubic boron nitride. Learn the properties of each and which is best >
Layering metal parts via electrolysis with special substances that improve their strength or appearance and protect parts from oxidation and corrosion is called electroplating. Typically less than .05 millimeters thick, coatings applied during the plating process are either metallic, diamond, or cubic boron nitride. Decorative objects such as jewelry or tableware are usually plated with silver or gold while steel and iron items are plated with zinc, chromium, nickel or tin. However, grinding tools require cubic boron nitride or diamond coatings to optimize their functioning, provide better cutting action and deter rapid deterioration of tools.
Advantages of Electroplated Diamond Tools
Tools sent through an electroplating process that coats them with a diamond layer cleaved by a tough nickel alloy retain their precise proportions and original structure throughout their working life. Unlike resin bond or metal bond diamond products involving diamond particles that have been cached in bond and joined together by embedded resin or metal binder, electroplating facilitates the protrusion of diamond fragments to extend beyond the bond matrix. This further provides electroplated diamond tools with the exceptional ability to cut freely and rapidly without generating excessive heat. Less heat generation means better grinding efficiency, reduced risk of cracks or burns on the workpiece's surface and a significant decrease in equipment energy consumption.
Electroplated diamond tools are well-suited to process:
Abrasive or hard non-metallic entities such as asphalt, stone, ceramics, concrete, semiconductor materials and glass.
Non-ferrous metals (copper, aluminum and their alloys) and pliable but tough materials (resin and rubber, for example).
Since diamonds react with iron, cobalt, nickel, chromium and vanadium under elevated temperatures produced during grinding actions, diamond tools should not be used to process common steels and tough alloy steels. For work involving these materials, electroplated cubic boron nitride tools are recommended.
Advantages of Electroplated Cubic Boron Nitride Tools
Considered the best technological advancement made for facilitating grinding of superalloy and hardened ferrous materials, cubic boron nitride is second to diamonds on the hardness scale and offers nearly five times the abrasion resistance afforded by traditional abrasives. Electroplated CBN tools also provide the following additional benefits not found in any other electroplated tools:
Remarkable thermal conductivity and chemical resistance
Enhanced surface integrity for grinding hardened cobalt-based superalloys as well as nickel and hardened alloy steels
Eliminates the expense of post heat-treat grinding operations
Produces polished surface finishes by providing taut dimensional management of tools to users
Creates no bit-dulling grit
The ability to induce nanostructuring of carbon boron nitride has allowed engineers to further increase the hardness of CBN by incorporating the Hall-Petch Effect, which describes the "tendency for hardness to intensify as grain size is decreased". In addition, carbon boron nitride's chemical resistant and strong thermal stability properties make it well-suited to machine ferrous materials that cannot be machined by electroplated diamond tools.
Which Blade Is Right For You?
If you're in the market for diamond sawblades, you may occasionally need some advice on exactly what you need, why these are the best choice, and where you should get them. It's important to first realize how essential it is to look for quality diamond blade manufacturer, so that you know you're getting a machine that will do exactly what you need.
If you're in the market for diamond sawblades, you may occasionally need some advice on exactly what you need, why these are the best choice, and where you should get them. It's important to first realize how essential it is to look for quality diamond blade manufacturer, so that you know you're getting a machine that will do exactly what you need. It's so much better to go with a company that understands the importance of quality work in a high-tech, professional setting, has an amazing customer service department, and provides quick turn-around for all products and tools. But what comes next?
Diamond blade saws are more than capable of cutting a variety of materials, so begin by thinking about your needs. For instance, do you want a saw that will work with different things or one that works best with something specific, such as stone or granite. Remember, a diamond cutting disc is excellent for cutting concrete and asphalt of all kinds, marble, ceramic, bricks, granite, carbide, quartz, optic materials, fiberglass, and many metals. With such far-reaching possibilities, diamond blades are the go-to choice in aerospace and medical engineering, construction, certain types of masonry, and stonework for statuary and memorials.
Next, remember that there's a difference between dry and wet cutting. Diamond blades grind the materials they go up against, they don't cut in the traditional sense. Grinding creates smoother, cleaner lines, so diamond saws chip far less and they're easier to control. However, with certain materials, the grinding does lead to dust. That's why those who work with stone, granite, concrete, and marble, especially, often prefer a wet cut. For work that demands a flawless finish, this is definitely one of the biggest benefits to consider.
One of the best reasons to buy diamond blades is because they're so long-lasting. The initial cost is a worth it, especially when you consider every aspect, such as the overall horsepower of the machine you intend to use, the diameters and hole sizes of the blades you choose, and the height and thickness of the segments in which you're interested. If you detail out exactly what you will need, you'll have a quality piece of equipment that you can easily use for years.
Above all, make sure you understand that you need to go with a reputable diamond blade manufacturer who knows what it's doing and does it well. A company that stands by the products it produces will always serve you better. Get a quote now
What You Should Know Before Picking A Supplier
CDT creates grinding wheels and tools in a variety of shapes and sizes so you know your tool will be right for the job from the start.
Diamond grinding wheels are available in a variety of commonly used shapes and sizes, but custom tools are often needed in specialized industries, including medical, aerospace, and ceramics. Weeding through professional grinding wheel manufacturers can be a daunting task, but custom-made surface grinding wheels are necessary for these industries.
Super abrasive products are used throughout the globe and are sought after by a wide assortment of customers. This means that diamond grinding wheel suppliers should be well versed in numerous applications, from electronics and composites to the oil industry, and everything in between. Look for a company that also specializes in plated, resin bond, and metal bond products, since different CBN wheels are designed for different grinding operations.
Cutting wheels consist of five major characteristics, including grain size, material, grain spacing, wheel grade, and bond type. Grain size determines the coarseness of the abrasive while the material indicates the actual abrasive itself, whether it is made from aluminum oxide, silicon carbide, ceramic, diamond, or cubic boron nitride. Grain spacing indicates the density of the wheel and wheel grade determines how hard or soft the bond holds the abrasive. Bond type affects the coolant, finish, and wheel speeds, and can be made of anything from rubber to metal.
Diamond wheels are made with diamonds, just as the name suggests. This gemstone is perfectly suited to grinding because it can stand up to extremely hard materials without breaking down. Some of the materials that diamond wheels are used to grind include other gemstones, concrete, and carbide cutting tips.
It’s important to go with a manufacturer noted for having the industry best lead time. Reputable companies often have a product ready and shipped within 7-10 working days, so never settle for anyone who doesn’t have the capabilities to have a custom super abrasive product ready in a week. Consider that the supplier should have personalized customer service that can pass on knowledge of the products as well, helping customers select the best super abrasive for their individual needs.
Continental Diamond Tool (CDT) is a leading provider of super-abrasives that maintains small company values but boasts large company capabilities, making them a highly sought after supplier. They specialize in the manufacture and application of CBN and diamond products used for both grinding and cutting, and are experienced in a wide range of industries. They also employ skilled experts with decades of experience, all of whom utilize the latest equipment to create a quality product unmatched in the industry.
Why Continental Diamond Tool?
At Continental Diamond Tool, we pride ourselves on not only industry-leading product, but customer service and lead time at the most cost effective price.
Tools That Make the Difference
Whether you work in medical tool manufacturing, aerospace engineering, concrete cutting or construction, or various other industries, you expect quality diamond saw blades — thus quality manufacturers. No matter what the job, the tools you use make all the difference. It's best to find well-made diamond plated routers, blades, tips, and holes that can easily get the job done, but don't stop there. If you're distributing the goods or introducing an industry-insider to the best in the business, make sure you pick a place with a solid reputation, excellent customer service, and quick response time.
Superabrasive tools are top-notch in a variety of industries and manufacturing endeavors. When working with materials such as fiberglass, quartz, various composites, ceramics, carbides, and other materials, diamond tip saw blades get the job done better. For the tools needed in innovative space exploration or high quality stone work, tools such as a continuous rim diamond blade provide a smooth, even, and polished finish.
Utilize a saw blade supplier with a versatile, well-stocked inventory and quick turn-around time. Our customers receive their new diamond plated router, saw blade, or tip, quicker, so they can get started creating products, technology, and innovations that may very well change the world.
Versatility is incredibly important in this industry. For that reason, it's also best to go with diamond saw blade suppliers who offer diamond blades, saws, and other tools that are capable of working with wet and dry materials. When working with marble, granite, concrete, ceramic tiles, and similar materials, the ability to work wet increases accuracy. When paired with a continuous saw, it significantly decreases the risk of chipping or mistakes, leading to flawless, polished work, whatever the need.
Creating statuary, granite or marble memorials, manufacturing tools and electronics used in space, and building tools for the medical field all require spotless, perfect work. The tools make all the difference, which is why it's essential to choose a manufacturer who guarantees quality pieces with many uses.
Bring the best to your customers. Rather than a large, jam-packed company which believes in quantity over quality, choose a smaller, more well-rounded supplier that responds with all the capabilities of a larger company. Whether you distribute to clients or companies that specialize in working with tiles, ceramic, fiberglass, or quartz, make sure that they'll have the best tools with the best reputation.
What Feed & Speed Do I Run the Wheel?
High-speed grinding wheels, like the CBN grinding wheel and diamond wheel can increase a manufacturer’s production rates, improve quality and reduce costs.
High-speed grinding wheels can increase a manufacturer’s production rates, improve product quality, and reduce production costs. Two of the most popular superabrasive products used for these purposes include the CBN grinding wheel and the diamond wheel.
CBN wheels are made with synthesized crystalline material produced in a similar way used for growing manmade diamonds. This is done with high-pressure, high-temperature techniques, so CBN wheels are similar to diamond wheels in that they are resistant to wear and noted for strength.
Abrasive grains for CBN wheels are improving each year leading to more controlled strength and shapes that were once challenges in this industry. Whether a customer chooses to use a CBN wheel or a diamond wheel, it’s important to note which elements are significant in achieving the desired result.
The wheel diameter plays an important role, since the smaller the wheel the easier it is to use and, generally, the less expensive it is. Small wheels are also easier to handle and balance. Larger wheels, however, are more suited to faster operating speeds.
All grinding wheels have a hub that has to be designed with proper mounting techniques in order for it to operate at the highest speeds. This means having the wheel mounted to a spindle that keeps it from shifting even as centrifugal force pushes the wheel into greater speeds. Any type of imbalance will affect the wheel’s stability and could result in dangerous slippage. Experienced CBN and diamond wheel suppliers will have worked out any balance issues and develop a quality superabrasive that will always be balanced and work at high rates of speed.
Coolant is also important with diamond cutting blades and CBN wheels since it keeps the wheels from overheating. Coolant also provides adequate lubrication and flushes out any particles and chips that could interfere with the wheel’s performance. Dressing is another important aspect, which is accomplished with rotary diamond technology.
Whether your needs deal with applications in the aerospace, ceramics, automotive, oil, electronics, or medical industries, it’s important to find a superabrasives supplier that has knowledgeable customer service and skilled experts that provide custom-made cutting and grinding products. Continental Diamond Tool is a leading supplier that has based its business on blending customer relationship with product performance. They boast not only superior superabrasive tooling, but offer some of the industry’s best delivery times, super responsive tech support, and all the latest bond technology. The unsurpassed quality and professionalism of this customer manufacturer makes ordering superabrasives easier than ever.
How do I dress my grinding wheel?
Diamond dressing tools are essential to keep grinding wheels true and free from particle buildup. This enhances grain exposure and abrades away some bond.
In the manufacturing industry, you know you often need one type of tool to maintain the maximum efficiency and life of other types of tools. Diamond dressing tools are among those essential assisting tools that keep grinding wheels true and free from buildup of particles. This dressing procedure keeps grinding tools, drill bits, chisels, and other tools with points or edges honed to their required sharpness.
VALUE OF DRESSING WHEELS
Using the appropriate diamond dressers or other diamond products on these abrasive wheels performs three important functions: (1) trues or re-balances the wheel to a concentric shape; (2) dislodges buildup of abrasive particles and bits of metal, exposing new abrasive surfaces of the wheel for more accurate grinding; and (3) cleans the wheel, renewing its edge and revealing sharper abrasive and fresh grains.
STEPS TO DRESS A GRINDING WHEEL
Here are the steps to take to effectively and properly dress a grinding wheel.
Step 1
Determine the proper dressing tool for the wheel. Make sure the grit of the dressing tool is finer by one or two sizes than the abrasive surface of the grinding wheel. Also make sure you choose the appropriate shape of dressing tool to coincide with your grinding wheel.
Step 2
Turn your grinding machine's coolant pump off (if it has one).
Step 3
Turn on your grinding machine and allow it to operate until it reaches its full RPM; you might choose to turn off your spindle motor, or keep it running, based on your personal preference or experience. Excessive need for truing might dictate keeping the motor on, rather than turning it on and off.
Step 4
Using light to medium pressure, apply the dressing tool to your wheel's abrasive section; continue applying pressure just until the wheel stops rotating.
Step 5
Repeat Step 4 until the dressing tool until the grinding wheel feels as if it is pulling the dressing tool away from you.
Step 6
Repeat Steps 4 and 5 as many times as necessary (four to five times, typically), depending on your grinding wheel's surface condition.
IMPORTANT ADDITIONAL TIPS
Ensure the tool rest is the appropriate distance from the grinding wheel (typically 1/16th of an inch) to prevent damage to the tool or injury to yourself.
Always wear safety glasses to protect your eyes from flying particles.
Avoid wearing loose-fitting clothing, such as long sleeves, and pull back long hair, when working near a spinning grinding wheel.
Which Dressing Tool is Right for You?
Use our dressing tools to ensure that your diamond grinding wheel will perform at maximum efficiency, trouble-free, and enjoy a long, sustainable life.
A diamond grinding wheel dresser is a vital tool in the proper care and maintenance of any grinding wheel. Regular maintenance ensures that your diamond grinding wheel will perform at maximum efficiency, trouble-free, and enjoy a long, sustainable life.
When selecting any dressing tool, including a diamond wheel dressing stick, it’s important to choose the tool that is the proper shape, size, and quality for the grinding wheel. If you don’t know which tool will work best with your application, discuss it with a supplier’s knowledgeable customer service department to determine exactly what you need.
Dressing the wheel will knock off any abrasive particles from the wheel’s surface. This ensures that it’s balanced and concentric, which minimizes any vibration it may get from having too much buildup on the surface. These particles, if left on the surface, have the potential to cover up surface abrasives, making them dull and ineffective. Exposing them by removing particles is essentially a sharpening process, since the fresh abrasive grains are each cutting tools in their own right.
A diamond grinding wheel dresser serves another important function, and that is to clean the grinding wheel. Choosing a dresser or grinding wheel dressing stick that is softer than the grinding wheel will not dislodge any abrasive particles, and can result in a loaded wheel. This is why selecting the proper dressing tools is crucial to a successful grinding wheel dressing.
There are also different types of dressers to consider. Star dressers feature long handles and serrated discs. Diamond dressers are generally preferred because of their superior strength. They also have shorter handles and are great for both dressing and truing. They are also available in single point and multi-set clusters to blade-specific type, and a reputable supplier will be able to determine which design to use based on your project. For example, a single point tool is easy to use and encourages a more pronounced rotation and higher frequency, delivering precise results.
Other benefits of a diamond grinding wheel dresser include a fast dressing of even the most complex wheels, a constant operation that boasts high-precision, and optimal dresser versatility. This type of dresser tool also means a decreased dressing cost per project, making it a cost-effective solution to all of your dressing needs.
How do Superabrasives compare to conventional abrasives?
Superabrasive wheels do not wear away like conventional wheels, therefore your shop and the air you breathe is much cleaner.
Superabrasives 101
If you’re in the market for superabrasives, it’s important to be familiar with common terms and product types that can help you discover which superabrasive is best for your needs. The metal bond grinding wheel is one of the most commonly used wheels, and the name denotes the metal bonding material that is most often used with a variety of grinding wheel types.
Using metal fillers, grinding wheels suppliers will manufacture the metal grinding wheel to specification. Metal bond is available with cubic boron nitride (CBN) and diamond wheels, and are generally used with coolant to prolong the wheel’s lifespan.
There are several advantages to using metal bond wheels, not least of which is its extended life. A metal bond ensures that the wheel has a fast stock removal. It also leads to a reduction in the dressing frequency and boasts more advanced form holding capabilities. Metal bonds are also extremely strong, so they are typically used in internal, form, glass, ceramic, tool cutting, and creep-feed applications.
A grinding wheel dresser, often referred to simply as a wheel dresser or grinding dresser, is an essential tool that dresses the grinding wheel surface. Dressing a wheel knocks any abrasive particles from the surface in order to make the grinding wheel concentric. This means less vibration and an improved finish. The grinding dresser is also important when cleaning the metal bond grinding wheel. One of the main benefits of using a metal bond grinding wheel is that it requires dressing less frequently than other wheel types.
Metal bond even goes beyond grinding wheels, since diamond core drills, solid diamond drills, and disintegrating core drills can all be manufactured using metal bond. Metal bond is primarily used in wet grinding. It can work well on glass, silicon, semi-conductors, refractories, and ceramics. Many industries choose to use metal bond tools because they are low maintenance but offer high productivity, making them ideal for maximum yield endeavors. They are also available in a range of tools, from the more aggressive CNC grinding down to light polishing.
When searching for grinding wheels suppliers, go with a company experienced in custom manufacturing with a wide range of superabrasives, including metal bond. A reputable company will tailor every order to each individual customer’s needs and offer a knowledgeable customer service that can help you determine the type of tools and products you need. Going with an experienced superabrasives provider will result in unmatched quality and a pleasant buying experience.