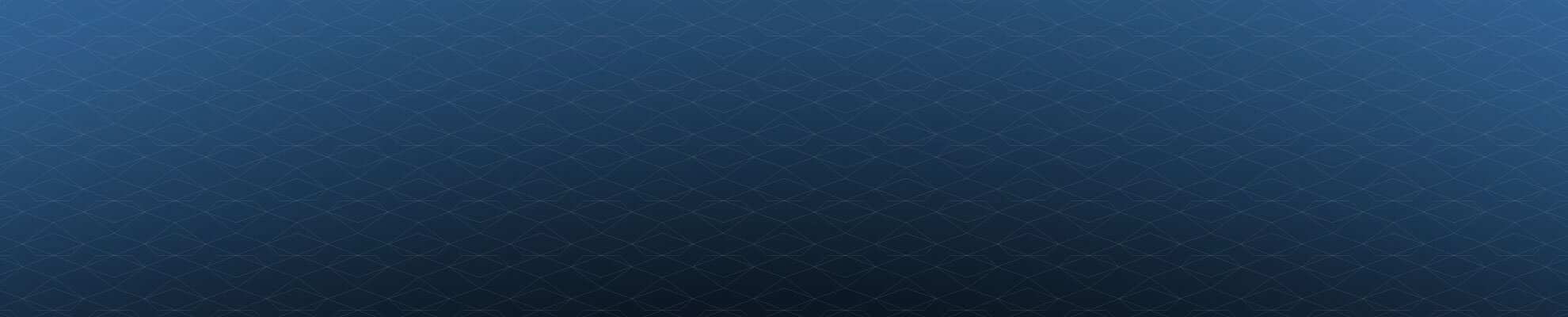
News and Resources
Browse by Category
Browse by Product
- All Dressing Products
- All Grinding Products
- CBN-Diamond Superabrasives
- Conventional Abrasives
- Diamond Lapping Compounds
- Diamond Rotary Dressers
- Diamond Stationary Dressers
- Hybrid Bond Grinding Tools
- Metal Bond Grinding Tools
- Plated Grinding Tools
- Resin Bond Grinding Tools
- Vitrified Bond Grinding Tools
Core Matters: How Different Wheel Body Materials Impact Grinding
Learn how grinding wheel core materials like steel, aluminum, and carbon fiber impact performance, precision, and cost to optimize your grinding applications.
When using superabrasive grinding wheels in precision manufacturing, selecting the right abrasive, bond type, and wheel core material is critical for optimal grinding performance and wheel life. While abrasives and bond types often take center stage, the wheel core can be equally important. The core material is the foundation that provides structural support and stability. The right core material ensures high performance while preventing machine strain, excessive grinding wheel wear, and unnecessary cost. But how do you determine the best core material for your specific needs?
In Episode 10 of The Grinding Chronicles, CDT Engineering Manager Jeff Wirth breaks down the essential properties of core materials and how they influence grinding applications. Watch the video or read the article below to learn how to choose the best option for your application.
The Grinding Chronicles - Episode 10
Selecting the Right Core Material for Grinding Wheels
The core of a superabrasive grinding wheel does more than just hold the abrasive—it directly impacts machine efficiency, grinding precision, and tool longevity. Choosing the right core material not only optimizes performance but also helps prevent unnecessary damage to the wheel, machine, and workpiece while enhancing operator safety.
Common core materials for superabrasive grinding wheels include metals—such as steel, aluminum, and copper—as well as non-metals like ceramics and resin composites. Ceramic or vitrified cores are commonly found in conventional abrasive grinding wheels and are also used in some superabrasive grinding wheels. Resin composite cores may be made from materials like bakelite, abrasive composites, or carbon fiber. Each of these materials has unique properties that affect grinding performance, and understanding their characteristics helps manufacturers make more informed decisions.
Understanding Core Material Properties
Density – Defined as mass per unit volume, density directly affects the weight of a grinding wheel. Heavier cores put added stress on machines and spindle bearings, which is why large-diameter grinding wheels are often designed with lighter core materials like carbon fiber, bakelite, or ceramic. An overly heavy wheel can reduce machine longevity, increase energy consumption, and pose handling risks for operators, making weight an important consideration for both performance and safety.
Expansion – Core materials expand due to heat and mechanical forces, which can impact grinding accuracy. Minimizing expansion is crucial for applications with tight tolerances, as it helps prevent wheel distortion and ensures consistent precision. Expansion occurs in two forms:
Mechanical Expansion: At high speeds, some core materials naturally expand due to centrifugal forces. Materials with high tensile strength resist this growth, maintaining stability and accuracy over time.
Thermal Expansion: Heat generated during grinding can cause materials to expand, leading to dimensional changes and reduced precision. Materials with low thermal expansion coefficients are essential for consistently achieving tight tolerances.
For high-speed and high-precision grinding applications, grinding wheels with cores made from high-tensile steel, carbon fiber, or vitrified ceramic often perform better. These materials minimize mechanical and/or thermal expansion, ensuring consistent performance, reduced deformation, and greater accuracy under extreme conditions.
Thermal Conductivity – This property determines how well a core material dissipates heat. Efficient heat transfer prevents thermal damage (burning) to the workpiece, improves surface quality, and extends tool life. Metal materials like Copper and Aluminum with high thermal conductivity remove heat, leading to lower wear and improved performance in high heat applications such as fluting drills.
Modulus of Elasticity (MOE) – This measurement indicates a material’s ability to resist deformation under stress. A higher MOE means the material is stiffer and less likely to flex or deform. Steel has a very high MOE. This can be beneficial for applications with high grinding forces that require tight tolerances, as a flexible core can introduce inconsistencies in grinding performance.
Comparing Core Materials: Strengths and Weaknesses
Each core material offers specific advantages and drawbacks. Here’s how some of the most common materials compare:
Steel is strong, durable, and resistant to mechanical expansion. However, its heavy weight can strain machinery.
Aluminum is lighter and often more affordable than steel, with higher thermal conductivity and resistance to corrosion. However, it has significantly higher thermal expansion compared to steel and other materials.
Copper offers excellent thermal conductivity and a high modulus of elasticity (MOE), but its weight and cost make it less suitable for large grinding wheels.
Ceramic is lightweight, cost-effective, and resistant to expansion, but low thermal conductivity and high stiffness or brittleness can be a drawback.
Resin composites, including bakelite, are affordable and lightweight. However, they lack stiffness and high thermal conductivity, making them more susceptible to expansion and heat buildup in high-force grinding applications.
Carbon fiber is ideal for demanding applications due to its high stiffness and low weight. However, it tends to trap heat and is more expensive than other materials.
Choosing the Right Core Material for Your Application
Selecting the best core material depends on several factors, including the type of grinding being performed, the machine’s limitations, and cost considerations. For example:
Flute grinding and medical drill bits operate at traditional speeds with lower grinding forces. This means that a wide variety of core materials can be used without significant performance issues. In these cases, ceramic cores are often recommended because they provide an excellent balance of cost and functionality.
High-speed applications like camshaft grinding generate significant heat and grinding forces. This makes high-stiffness materials like carbon fiber or high-tensile steel essential to be able to perform effectively and safely.
Hybrid or combination cores are an innovative solution for balancing weight, stiffness, and cost. This approach involves layering or combining different materials to optimize performance while keeping costs manageable. For instance, a steel core can be reinforced with carbon fiber to reduce weight without sacrificing strength.
Practical Considerations in Core Material Selection
Beyond material properties, cost plays a major role in selecting the right core material for grinding wheels. While core materials like carbon fiber and vitrified ceramic are both resistant to mechanical and thermal expansion and lighter weight, they come at very different price points. Once all process requirements are met, cost is usually the deciding factor, as manufacturers balance performance needs with material costs to avoid unnecessary expenses.
Budget-Friendly Options – Ceramic and resin composites provide cost-effective solutions for applications with lower grinding forces and minimal heat generation. These materials perform well in traditional grinding operations without adding unnecessary expense.
Mid-Range Solutions – Aluminum and standard steel cores offer a balance between affordability and durability. These materials are commonly used in medium-duty grinding applications where moderate strength and thermal properties are required, optimizing cost per part without sacrificing performance.
Premium Core Materials – High-tensile steel and carbon fiber provide top-tier performance, making them ideal for high-speed and high-force applications. While their higher price point increases the initial cost of the grinding wheel, their longevity and reliability often justify the investment by reducing long-term cost per part through extended tool life and efficiency gains.
When selecting a core material, it is essential to consider not just the upfront cost but also long-term savings from reduced machine wear, improved grinding efficiency, and longer tool life. CDT’s engineering team can help assess cost-effectiveness based on your specific grinding application, ensuring the best balance between performance and cost per part.
Optimize Your Grinding Wheel Performance with CDT
Choosing the right core material is critical for achieving consistent, high-performance grinding results. Whether you're working with grinding applications for heavy-duty industrial engine components or high-precision medical tool manufacturing, the engineering team at Continental Diamond Tool is ready to assist in customizing a grinding wheel with the materials that are best for your needs.
If you have questions about selecting the best core material for your specific application, CDT’s engineers are here to help. Reach out to TheGrindingChronicles@cdtusa.net for expert advice.
Check out more videos from The Grinding Chronicles and follow CDT on Linked In for the latest news in grinding technology.
An Essential Guide to Grinding Process Optimization for Boosting Performance in Precision Manufacturing
Optimize your grinding process with expert tips on speeds, feeds, Q-prime, and advanced bond technology to boost efficiency in precision manufacturing.
To stay competitive in precision manufacturing, grinding operations require continuous improvement in performance and efficiency. Understanding the factors that influence grinding, such as speeds, feeds, and material removal rates, can significantly impact your results. In this comprehensive guide from Continental Diamond Tool, Product Engineer Thi Dang and Engineering Consultant Jon VanSant share their expertise as they unpack the essential elements of grinding process optimization. Episode 8 of The Grinding Chronicles offers valuable insights into maximizing Q-prime, balancing G ratios, and selecting the right grinding wheel speeds. Whether you’re looking to refine your current operations or upgrade to the latest in bond technology, our engineering team’s breakdown outlines the key factors you need to consider to enhance your grinding processes. Watch the video or read on to discover practical tips and advanced strategies for getting the most out of your grinding tools.
The Grinding Chronicles - Episode 8
Unlocking the Secrets to Optimizing Your Grinding Process
In this article, you will learn the essentials for optimizing your grinding process, focusing on the metrics that matter most for achieving peak performance. From understanding the basics of speeds and feeds to exploring advanced bond technology, this guide provides actionable insights for any precision manufacturing operation. Whether you're new in the field or looking to enhance your current practices, this informative article from The Grinding Chronicles team offers valuable knowledge to help you get ahead in the industry.
Understanding the Basic METRICS in GRINDING
One of the first considerations when optimizing a grinding process is understanding the basics—speeds, feeds, and material removal rates. These elements are fundamental to the grinding process and play a crucial role in determining the efficiency and quality of the finished product.
Speeds and Feeds:
Speeds refer to the rotational speed of the grinding wheel, typically measured in surface feet per minute (SFM). Feeds, on the other hand, relate to the rate at which the workpiece is fed into the grinding wheel. Together, these parameters influence the rate of material removal, surface finish, and the overall efficiency of the grinding process.
It's essential to understand that faster isn't always better. While higher speeds can increase material removal rates, they can also lead to increased wheel wear and the potential for thermal damage to the workpiece. Therefore, finding the optimal balance between speed and feed is key to maintaining both efficiency and quality.
Material Removal Rate (Q-prime):
Q-prime, or material removal rate, is a critical measure of grinding performance. It is calculated by multiplying the depth of cut by the feed rate, resulting in the amount of material removed per unit time. Higher Q-prime values typically indicate shorter cycle times, which can significantly enhance productivity.
However, achieving high Q-prime values requires careful consideration of other factors, such as wheel wear and the quality of the finished surface. A high Q-prime might reduce cycle times, but if it leads to excessive wheel wear or poor surface quality, the overall efficiency of the process may suffer. Thus, optimizing Q-prime involves balancing it with other critical parameters, such as the G ratio.
The G Ratio:
The G ratio is another vital metric in grinding. It is defined as the volume of material removed from the workpiece divided by the volume of wheel wear. A high G ratio indicates efficient grinding, where more material is removed with less wheel wear. However, similar to Q-prime, achieving an optimal G ratio requires balancing various factors.
Maximizing Q-prime WHILE Balancing the G Ratio
Maximizing Q-prime while maintaining a high G ratio is the key to optimizing grinding processes. To achieve this balance, it’s important to consider the following:
Wheel Speed: Higher wheel speeds can lead to increased wheel wear due to elevated temperatures. Therefore, it’s crucial to find an optimal speed that maximizes material removal without excessively wearing the grinding wheel.
Coolant Delivery: Proper coolant delivery is essential in controlling the temperature during grinding. Efficient coolant systems help dissipate heat, reducing thermal damage to the workpiece and wear on the grinding wheel. This, in turn, helps maintain a high G ratio.
Machine Stiffness and Power: The stiffness of the grinding machine and the power of the spindle also play significant roles. Machines with low power or poor stiffness may limit the achievable Q-prime and G ratio, restricting the overall efficiency of the grinding process.
By carefully considering these factors, manufacturers can optimize their grinding operations to achieve both high Q-prime and G ratios, leading to improved productivity and efficiency.
The Evolution of Bond Technology
Bond technology plays a critical role in the performance of grinding wheels, particularly in their ability to achieve high Q-prime and G ratios. The history of bond technology in grinding wheels is a testament to the continuous advancements that have been made in this field.
A Look Back:
In the 1960s, phenolic resin bonds were the standard, offering Q-prime values of around three. By the 1970s, the introduction of polyimide bonds pushed Q-prime values to around five. The year 2000 marked another leap with hybrid bonds, which increased Q-prime to approximately seven.
Today, we are capable of removing material at rates between 10 and 15, thanks to the latest advancements in bond technology. This evolution highlights the importance of continuously upgrading to the latest bond technology to stay competitive in the market.
Introducing CDT's EVO Hybrid Bond:
Continental Diamond Tool has been at the forefront of these advancements with its EVO Hybrid Bond. Released earlier this year, the EVO Hybrid Bond represents a significant step forward in bond technology, offering the ability to achieve Q-prime values over 10 without compromising the G ratio.
The development of the EVO Hybrid Bond was driven by the need for a bond system that could grind aggressively while minimizing wear and maintaining excellent corner retention. This bond was also designed with thermal conductivity in mind, to transfer heat away from the part and prevent damage to the diamond, which is sensitive to high temperatures. Learn more about CDT’s EVO Hybrid Bond product here.
Practical Tips for Optimizing Your Grinding Process
Now that we’ve covered the theoretical aspects of grinding optimization, let’s look at some practical tips that can help you apply this knowledge to your operations:
Evaluate Your Current Operations: Start by assessing your current grinding processes. Measure your Q-prime and G ratio to establish a baseline. Identify areas where improvements can be made, whether in speed, feed rate, or wheel selection.
Invest in the Latest Technology: Consider upgrading to the latest bond technology, such as CDT’s EVO Hybrid Bond. Newer bonds can significantly improve your material removal rates and reduce wheel wear, leading to better overall efficiency.
Optimize Coolant Delivery: Ensure that your coolant system is operating efficiently. Proper coolant delivery is essential for controlling temperatures and reducing thermal damage, which can extend the life of your grinding wheels and improve the quality of your finished products.
Regularly Maintain Equipment: Regular maintenance of your grinding machines is crucial. Ensure that your machines are running at optimal stiffness and power to maximize performance and avoid limitations in Q-prime and G ratios.
Train Your Team: Make sure your team is trained on the latest grinding techniques and technologies. A well-informed team can make better decisions on the shop floor, leading to improved productivity and efficiency. At Continental Diamond Tool, our application engineers are here to help. We regularly connect with our customers to fine-tune their equipment and train their operators on the optimized speeds and feed rates to use with our grinding wheels.
Optimizing grinding processes is essential for staying competitive in precision manufacturing. By understanding and balancing key factors like Q-prime, G ratio, and wheel speed, manufacturers can significantly enhance their grinding operations. Continental Diamond Tool’s latest advancements, including the EVO Hybrid Bond, provide valuable tools for achieving these goals. Whether you’re looking to improve your current processes or invest in new technologies, the insights provided in this guide offer a clear path to optimizing your grinding operations. Implement these strategies to ensure your manufacturing processes are both efficient and effective, helping you to stay ahead in a demanding industry.
How to Diagnose Surface Pattern Problems in Grinding
Learn how to diagnose and fix common surface pattern problems in precision grinding with expert insights from CDT's Senior Product Engineer, Paul Christy.
Many precision grinding operations require impeccable surface finishes for both function and aesthetics. Addressing surface pattern problems is vital for ensuring the quality of the final product, eliminating waste, and controlling costs. In this detailed overview, we expand on the insights provided by Paul Christy, Senior Product Engineer at Continental Diamond Tool, as he explains how to troubleshoot and fix common causes of surface patterns. In Episode 7 of The Grinding Chronicles, Paul covers the complexities of surface patterns caused by various types of vibrations, runout, and servo system instability. Watch Paul’s video or read on to learn more about identifying and addressing these issues to optimize your grinding operations.
The Grinding Chronicles - Episode 7
Surface Pattern Troubleshooting Guide
Surface pattern problems in grinding can significantly impact the quality and precision of your workpieces. Diagnosing and resolving these issues requires a deep understanding of the underlying causes and appropriate troubleshooting techniques. This article explores common causes of surface patterns in grinding and provides expert insights into their diagnosis and elimination.
Self-Excited Vibration
One of the primary causes of surface pattern problems is self-excited vibration, which occurs at the natural frequency of the machine system. This type of vibration indicates that some component within the machine—such as the spindle, the part, or the dresser—is being excited. The resulting oscillating pattern is called chatter. Notably, this vibration only manifests when the grinding wheel and the workpiece (or the wheel and the dresser) are in contact.
Self-excited vibration results from a lack of sufficient component stiffness. The key to mitigating this issue lies in increasing the machine's stability, which requires a greater machine stiffness compared to the process stiffness. There are three main process variables that can be adjusted to help eliminate self-excited vibration:
Velocity of the Workpiece: Lowering the workpiece's speed can reduce process stiffness.
Velocity of the Grinding Wheel: Decreasing the grinding wheel's speed similarly lessens process stiffness.
Width of Contact: Reducing the contact width between the grinding wheel and the workpiece can also help.
By strategically lowering one or more of these variables, you can effectively diminish the impact of self-excited vibration.
Forced Vibration
Forced vibration occurs at a frequency corresponding to a driving force within or outside the machine. Common examples of such driving forces include unbalanced rotating bodies and pump pulsations. This type of vibration can often be diagnosed using a process of elimination. By sequentially turning on and off all rotating bodies within the machine, you can identify the source of the vibration when it ceases upon the deactivation of a specific component.
Runout
Runout is a prevalent issue in grinding due to the inherent imperfections of rotating components. It occurs when the outer surface of a rotating component does not maintain perfect concentricity with its axis or center line. Specifically, runout in a traversing diamond roll can create a pattern in the grinding wheel, which is then transferred to the workpiece. This pattern typically manifests as angled parallel lines, known as Barber Pole or Roping Patterns.
To address surface patterns caused by runout, it is essential to identify the optimal dresser and wheel RPMs. Varying the diamond roll speed during dressing can reduce the likelihood of pattern formation on the grinding wheel, preventing its transfer to the workpiece. Another effective solution is lapping the diamond roll to the machine's spindle bearings, thereby eliminating runout.
Servo System Instability
Servo system instability is another potential source of surface patterns on workpieces. The servo system controls the movement accuracy of machine components, using digital feedback to ensure precise positioning. Mechanical decoupling within components such as ball nuts, couplings, bearing support units, or scale mountings can create discord within the servo system. This results in oscillations as the system struggles to determine the correct position, leading to surface patterns on the workpiece.
Solving servo system instability typically requires sophisticated instrumentation and physics-based analysis. Iterative process changes alone are unlikely to resolve this complex issue.
Key Takeaways in Mastering Surface Finish
Diagnosing and fixing surface pattern problems in grinding necessitates a thorough understanding of the potential causes and their specific remedies. Whether dealing with self-excited vibration, forced vibration, runout, or servo system instability, targeted adjustments and precise troubleshooting are essential for maintaining the quality and precision of your grinding operations.
For more detailed information and expert guidance, refer to Episode 7 of The Grinding Chronicles, where Paul Christy shows specific measures you can take to diagnose and eliminate surface pattern problems. If you are experiencing surface patterns similar to those discussed in this article and require further assistance, do not hesitate to contact the Continental Diamond Tool engineering team at TheGrindingChronicles@cdtusa.net.
Understanding and addressing these grinding challenges will enhance your operational efficiency and ensure the superior quality of your manufactured products.
A Breakdown of the 4 Common Bond Systems in High Precision Grinding
Discover CDT's four essential bond systems for superabrasive grinding wheels: Resin, Metal, Vitrified, and Electroplated. Optimize operations with expert insights from Jeff Wirth.
If precision grinding is a critical component of your manufacturing process, understanding the bond system of your grinding wheel will help you in maintaining operational efficiency and product quality. In this detailed overview, we will explore the four most common bond systems used in superabrasive grinding wheels: Resin, Metal, Vitrified, and Electroplated. Continental Diamond Tool Engineering Manager Jeff Wirth breaks down the components of these bond systems, discussing their composition, manufacturing processes, and ideal applications in Episode 6 of The Grinding Chronicles. Watch Jeff’s video or read on to learn more about selecting the right bond to optimize your grinding operations.
The Grinding Chronicles - Episode 6
Understanding the Four Common Bond Systems
Resin Bonds
Resin bonds are plastic-based compounds typically made from phenolics or polyimides. These bonds are versatile and can be enhanced with fillers such as copper or silicon carbide to improve performance. The manufacturing process for resin bonds at CDT begins with creating a tailored formulation that includes the bond material, abrasive, and fillers. This dry powder mixture is blended in special tumblers and then carefully and uniformly packed into mold cavities. The molds undergo hot pressing, where temperature and pressure are meticulously controlled to achieve the desired density. Finally, the wheels are finished by machining and grinding them to the specified size and geometry.
Properties and Applications:
Tough and Durable: Resin bonds are fully dense and easy to use, making them suitable for a variety of grinding applications.
Versatile: They can work with nearly any material, from hard metals to softer alloys.
Enhanced Performance: Fillers like copper or silicon carbide can be added to improve heat dissipation and grinding efficiency.
Wide Range of Applications: Suitable for diverse grinding tasks, including tool and cutter grinding, centerless grinding, and surface grinding.
Metal Bonds
Metal bonds can be composed of various metals, including bronze, copper, and iron, and may sometimes be alloyed with precious metals like silver. Metal bonds are known for their hardness, toughness, and durability, making them ideal for grinding highly abrasive materials such as glass and ceramics. Although metal bonds grind more slowly than other types, they offer the longest lifespan. The manufacturing process for metal bonds at CDT is similar to that of resin bonds, involving formulation, mixing, molding, hot pressing, and finishing.
Properties and Applications:
Hardest and Toughest: Metal bonds are the most challenging to use but provide superior durability.
Long-Lasting: They offer the longest lifespan among bond types, reducing the frequency of wheel changes.
Ideal for Abrasive Materials: Best suited for grinding materials like glass, ceramics, and carbide.
Durability: Excellent for applications requiring extreme durability and extended wheel life, such as in the automotive and aerospace industries.
Vitrified Bonds
Vitrified bonds are made from glass or ceramic materials, creating a porous structure that significantly reduces grinding force. This allows for higher grinding speeds, making vitrified bonds ideal for high-production applications. These bonds offer moderate to high material removal rates and excellent form accuracy, as they can be dressed and profiled in-process using rotary dressers. The manufacturing process for vitrified wheels at CDT involves formulation, mixing, cold pressing, and a sintering (baking) process to fuse the glass or ceramic together. The final step is finishing, similar to the other bond types.
Properties and Applications:
Porous Structure: Lowers grinding force and allows increased speeds, enhancing efficiency.
High Production: Ideal for high-production applications such as automotive part manufacturing.
Moderate to High Material Removal Rates: Efficient for large-scale operations, balancing speed and precision.
High Form Accuracy: Can be dressed and profiled in-process using rotary dressers, making them suitable for precise and consistent grinding tasks.
Electroplated Bonds
Electroplated (or plated) bonds consist of a single layer of abrasive held by a nickel-based metal bond. The process begins with machining the desired wheel size and geometry onto a steel wheel core. The non-plated surfaces are masked to prevent unwanted plating. The wheel core is then placed in a bath with a nickel-based solution and the abrasive material. By applying a positive charge on one side and a negative charge on the other, nickel plating is deposited onto the wheel core, causing a single layer of abrasive to adhere. Excess abrasive is removed, and the plating process continues until the abrasive layer is encapsulated to the desired level, typically 50-100% depending on the application. Electroplated products are suitable for complex geometries and low to medium production applications due to their high material removal rates and fast grinding speeds.
Properties and Applications:
High Material Removal Rates: Provides the fastest grinding speeds, ideal for rapid material removal.
Cost-Effective: Single layer of abrasive can be stripped and replated, extending the wheel’s life.
Ideal for Complex Geometries: Precise form replication with minimal finishing, suitable for intricate designs.
Low to Medium Production: Suitable for specific applications requiring detailed shapes and efficient material removal.
Key Considerations for Selecting the Right Bond System:
Choosing the appropriate bond system for your grinding application is crucial for achieving optimal performance and quality. Each bond type offers unique properties and advantages, making them suitable for different materials and grinding conditions. By understanding the composition, manufacturing processes, and ideal applications of Resin, Metal, Vitrified, and Electroplated bonds, you can make informed decisions to enhance your grinding operations.
Factors in Bond System Selection:
Material to be Ground: The hardness and abrasiveness of the material significantly influence the choice of bond.
Grinding Speed and Efficiency: Consider whether the application requires high-speed grinding or if longevity and durability are more critical.
Application Specifics: Determine if the grinding operation involves complex geometries or requires high form accuracy.
Production Volume: High-production environments may benefit from vitrified bonds, while electroplated bonds are ideal for low to medium production with intricate details.
If you have any questions or want to learn more about which bond type would work best for your application, please reach out to our application engineers at TheGrindingChronicles@CDTUSA.net. For more industry insights and expert advice, check out these articles or watch our playlist for The Grinding Chronicles on YouTube. By leveraging the right bond system and understanding its properties, you can significantly improve your grinding efficiency, product quality, and operational cost-effectiveness.
Understanding the Distinction Between CBN and Aluminum Oxide Abrasives
Uncover the secrets behind top-notch results in grinding and machining of tough steels and metals. Discover the unique properties of Cubic Boron Nitride (CBN) and Aluminum Oxide and learn how to choose the right abrasive for optimal efficiency and precision.
Are you ready to explore the fascinating world of abrasives? In manufacturing, we often encounter Superabrasives and Conventional abrasives. In the Superabrasives corner, we have Diamond and Cubic Boron Nitride (CBN), and their common Conventional abrasive counterparts are Silicon Carbide and Aluminum Oxide. Each serves a specific purpose. What makes CBN and Aluminum Oxide stand out is their exceptional ability to tackle those stubborn steels and metals that can't stand Carbon.
In this blog, we'll explore the properties and applications of CBN and Aluminum Oxide abrasives. Discovering their unique characteristics will help you choose the right abrasive for your specific machining needs, ensuring efficiency and top-notch results. Whether you're working with hardened steels or softer metals, the right abrasive is the key to achieving your desired outcome in grinding and machining. So, let's dive in and unlock the true potential of CBN and Aluminum Oxide abrasives.
What is CBN?
CBN is a synthetic Superabrasive known for its incredible hardness, high thermal conductivity, and thermal stability. Originally released with the trade name Borazon from GE Superabrasives, its cubic crystal lattice structure is similar to Diamond, giving it remarkable abrasive properties. With a hardness close to 10 on the Mohs scale, CBN excels in machining tough materials that require precision grinding. Its chemical composition and high thermal stability prevents chemical reactions and premature breakdown under high temperatures, when grinding ferrous metals and high-temperature alloys. What's more, because CBN doesn't react with ferrous materials, it doesn’t alter or change their properties resulting in longer life in use when ground with CBN.
CBN is a game-changer when grinding hardened ferrous alloys or super alloys that are sensitive to heat. It efficiently grinds hardened steels while maintaining accuracy and surface finish. Plus, it's a favorite for grinding ferrous metals like cast iron and stainless steel, ensuring clean and precise results without chemical alterations. CBN is a must-have tool for achieving precise and efficient outcomes in critical machining tasks.
What is Aluminum Oxide?
Aluminum Oxide, also known as alumina, is a versatile Conventional abrasive. With high hardness and toughness, it is available in various grit sizes, making it perfect for a wide range of machining and finishing applications. Though not as hard as CBN, Aluminum Oxide is fantastic for soft metals, wood, and non-ferrous materials. While it may not match the precision of Superabrasives, it's still a reliable choice for many tasks.
In the machining industry, Aluminum Oxide is the go-to for grinding soft metals like aluminum, brass, and copper. It performs beautifully with non-ferrous materials such as bronze and titanium, without causing any chemical interactions. Its role in achieving desired surface finishes across various industries, from automotive to aerospace, is unparalleled.
Key Differences Between CBN and Aluminum Oxide Abrasives
While CBN and Aluminum Oxide both play significant roles in grinding and machining operations, they have many distinct properties that set them apart.
Crystal Structure and Hardness: CBN's crystal lattice structure is similar to Diamond, resulting in exceptional hardness and wear resistance. Aluminum Oxide, while still hard, has a lower hardness than CBN, making it more suitable for soft metals and certain alloys.
Heat Resistance and Thermal Conductivity: CBN exhibits superior heat resistance and thermal conductivity compared to Aluminum Oxide, making it perfect for grinding high hardness and heat sensitive alloys.
Material Compatibility and Reactivity: Both CBN and Aluminum Oxide are chemically inert with ferrous materials whereas Diamond and Silicon Carbide are not, thus why they are the abrasives for ferrous metals.
Cost and Practicality: CBN grain costs significantly more than Aluminum Oxide grain, resulting in higher grinding wheel prices. Because of higher hardness and better thermal conductivity, CBN wheels can provide lower grinding costs in applications where high workpiece hardness and thermal properties need to be maintained. In cases of grinding soft steels and low volume production, the lower wheel price of Aluminum Oxide makes it a more competitive option.
Safety Considerations and Handling
Whether you choose CBN, Aluminum Oxide, or another solution for your abrasive, ensuring safety during grinding and finishing processes is essential. Proper machine guarding, eye and respiratory protection, proper dust/mist extraction, and careful handling and storage of abrasives are crucial to protect workers and maintain a clean and safe work environment.
Selecting the Right Abrasive for Specific Applications
Choosing the right abrasive for your specific machining needs is vital to achieving optimal results. Making an informed decision will ensure efficient, accurate, and cost-effective grinding and finishing processes. Some factors to consider include:
Workpiece Material Characteristics: Soft metals like aluminum, brass, copper, and mild steels may need moderate hardness abrasives like Aluminum Oxide to prevent excessive material removal, while harder materials like hardened steels and high-temperature alloys such as inconel and hardened Stainless Steel require abrasives with superior hardness and high thermal conductivity like CBN for precise and efficient cutting and grinding.
Machining Operations and Efficiency: Superabrasives like CBN are preferred for high-precision tasks where tight tolerances and maintaining material properties are paramount, while conventional abrasives like Aluminum Oxide offer lower cost solutions for general grinding of mild steel and soft metals.
Surface Finish and Material Removal Rates: Superabrasives like CBN excel in production applications of hardened steels and Superalloys that are sensitive to heat, , while conventional abrasives like Aluminum Oxide are effective in low volume applications and for grinding of soft metals.
Tooling and Machinery Considerations: Abrasive selection also needs to account for machinery and tooling capabilities. The truing and dressing of Superabrasive and Conventional Abrasive grinding wheels can be different and require different tools (stationary or rotary dressers of different configurations). Because of the difference in hardness between CBN and Alumina, Alumina being much lower, the amount of grinding debris resulting from wheel wear during grinding can be 100-300 x’s greater with the conventional wheel, which in turn needs to be disposed of. .
Both CBN and Aluminum Oxide abrasives offer distinct advantages in grinding and machining. Considering their unique properties with specific application requirements will lead to efficient and precise processes, ensuring optimal results and safety in the workplace. And if you ever need assistance, our grinding experts at CDT are here to help. Whether it's Superabrasives or Conventional abrasives, we can help find the perfect solution for your process.
Superabrasive Grinding Technology for the Ceramic Industry
We explore the transformative impact of custom superabrasive grinding products on the ceramics industry, highlighting the benefits they offer and the cutting-edge technologies driving these innovations.
The rapid growth of ceramic and carbide components in industries such as Automotive, Aerospace, Medical, and Electronics has created new challenges for grinding professionals. The hardness, abrasiveness, and brittle nature of ceramics and carbides make them difficult to grind efficiently. Yet advancements in superabrasive grinding technology have paved the way for improved grinding processes and reduced cycle times for those that invest in new custom technology. In this article, we explore the transformative impact of custom superabrasive grinding products on the ceramics industry, highlighting the benefits they offer and the cutting-edge technologies driving these innovations.
Overcoming Grinding Challenges in the Ceramics Industry
Ceramic and Carbide materials pose unique challenges when it comes to grinding due to their unique hardness and abrasive properties. Traditional metal bond and resin bond grinding wheels have been the go-to solution for grinding these materials. However, advancements in CNC grinding equipment and the introduction of new bond systems have revolutionized the way ceramic and carbide components are ground.
In different industries like electronics, optics, aerospace, and advanced manufacturing, people are using carbide and ceramic coatings to make components last longer and better at handling heat. Two common ways to add these coatings are HVOF (High-Velocity Oxygen Fuel), which uses high-speed flames to spray the coating onto surfaces, and HVOC (High-Velocity Oxygen-Fuel Cold Spray), which works at lower temperatures with fast-moving gas. Another method is Chemical Vapor Deposition (CVD), where a thin layer of material is deposited on a surface through chemical reactions in the vapor phase. Using CVD or HVOF/HVOC can make components longer lasting and more wear resistant.
The inclusion of carbide or ceramic layers necessitates special consideration during the grinding process because of the inherent hardness and abrasive properties of these materials. Superabrasive grinding wheels offer superior performance in grinding these materials by reducing grinding forces, lowering power consumption, and minimizing subsurface damage. These innovative grinding products are particularly effective in reducing grinding cycle times and reducing scrap, resulting in significant cost savings and enhanced productivity.
Advances in Superabrasive Grinding Technology
The advent of multi-axis CNC grinding with Rotary Dressers has automated grinding processes, increasing efficiency and accuracy. Spindle & High-Pressure Coolant systems have improved the delivery of coolant to critical grinding areas, optimizing swarf removal and improved the cooling and lubrication during the grinding process. High-speed grinding spindles enable a wider range of bond technology and wheel sizes to be used for ID and smaller part grinding.
New "Cutting Tool" designs, such as slotting, high porosity bonds, coolant holes, and CNC adaptors for improved rigidity, have improved tool life and performance. These designs enhance coolant flow, chip evacuation, and overall tool effectiveness, contributing to longer tool life and reduced downtime.
Innovative bond systems have been developed to address the unique challenges of grinding ceramic and carbide materials. These new bonds lower grinding forces, reduce power consumption, and lead to faster cycle times. They also minimize subsurface damage resulting in lower scrap rates while enhancing the quality and integrity of the finished components.
Superabrasive Grinding Products for Ceramic & Carbide Components
CDT's superabrasive solutions deliver significant benefits, including a reduction in grinding forces by 30% or more (compared with resin & metal bonds), reduction in cycle times by up to 50%, and significant reduction in scrap rates on these critical and costly components. These advancements help manufacturers optimize their grinding processes, increase productivity, and reduce costs.
Continental Diamond Tool (CDT), a leading provider of superabrasive solutions, offers a comprehensive range of grinding products designed specifically for the ceramics & carbide industries. Their products are compatible with major industry equipment manufacturers, including Studer, Kellenberger, Danobat, Walters, ANCA, Junker, Okuma, Koyo, USACH, Lapmaster, Peter Wolters, SpeedFam, Stahli, Supfina, and many more. CDT also offers advanced custom tool designs, such as cross cutters and hole drilling with flat bottom drills, to address specific grinding requirements. Their expertise extends to a wide range of equipment, including round tools for Anca, Haas, ITM, Normac, Rollomatic, Star, and Walters, as well as inserts for Agathon, Coborn, EWAG, Waida, and Wendt. Additionally, CDT has created surface grinders for Arter, BLOHM, Brown & Sharp, Chevalier, ELB, and Magerle, as well as Blanchard grinders for Blanchard, Bourn & Koch, and DCM.
Superabrasive grinding products have revolutionized the ceramics & carbide industry, overcoming the challenges presented by the high hardness and abrasive nature of these materials. With reduced grinding forces, faster cycle times, and reduced scrap rates, manufacturers can achieve greater efficiency, productivity, and cost savings. Continental Diamond Tool's advanced superabrasive solutions provide tailored grinding products for a wide range of equipment, enabling manufacturers to optimize their grinding processes and achieve exceptional results. As industries continue to evolve to use more ceramic & carbide materials, the use of superabrasive grinding products will undoubtedly play a crucial role in meeting the growing demand for efficient production of these components.
What are Metal Bond Grinding Wheels and What Benefits Do They Offer?
Extensively used in manufacturing diamond grinding wheels, metal bonds are manufactured utilizing three different processes: cold press, semi hot press and hot press modes.
Extensively used in manufacturing diamond grinding wheels, metal bonds are manufactured utilizing three different processes: cold press, semi hot press and hot press modes.
Cold press mode involves pressing the transition layer (no diamonds) and the working layer (with diamonds) of selected diamond portions to forms that on the body of the grinding wheel. These segments are then allowed to interconnect with the grinding wheel's body via slots or teeth. Finally, cold press grinding wheels are placed into sintering furnaces where they are sintered without press.
The semi hot press mode improves on the cold press mode by complementing the sintering process. While grinding wheels are sintering in a furnace, applicable molds are applied and minimal to moderate pressure is added. However, any pressure applied is significantly lower than the amount of pressure applied in hot press mode.
Hot press mode directly sinters diamond particles in molds under preset pressure levels in induction units. Diamond segments are then affixed on the grinding wheel using high frequency laser welding, high frequency welding or mosaic methods of mechanical welding.
Metal bond grinding wheels are produced when powdered metals or compounds containing cubic boron nitride or diamond are sintered on the wheel, resulting in exceptionally strong tools that maintain shape during rigorous use. In addition, metal bonding extends the life of grinding wheels by reducing the need for repeated dressings and continues being productive longer than market-brand super abrasives.
Benefits of Using Metal Bond Grinding Wheels
Because metal bond grinding wheels are sintered with cobalt, copper, mill, silver or stanum powder, they work exceptionally well on a variety of surfaces (glass, refractories, ceramics, silicon, semi-conductors and quartz).
Whether used for tool cutting, glass grinding, ceramic grinding or form cutting, metal bond grinding wheels provide the longest, most superior quality of service before any type of maintenance is needed.
Metal bond offers the ability to perform outstanding interrupted cuts while retaining the tool's original dimensions even during the most energetic grinding actions, including centerless, cylindrical, creep feed, deburring and cutoff applications.
Although resin bonds are more commonly used than vitrified or electroplated bonds, these bonds do not offer the hardness or wheel retention properties exhibited by metal bond grinding wheels.
As one of the most frequently seen machines in manufacturing plants requiring grinding applications, centerless grinders especially benefit from metal bond grinding wheels because of the slow, precise pace of material removal method demanded of these machines. Additionally, super abrasive centerless grinders necessitate powerful wheels such as metal bond grinding wheels that can effectively make predetermined alterations to products while reducing quality control issues that may arise if lesser quality wheels are used.
Continental Diamond Tool Corporation has been producing Metal Bond products since it was founded in 1973. If you are looking for a custom metal bond wheel, contact our experienced team of product engineers today.
What to Look For When Choosing A Diamond Wheel Supplier
Look for these qualities when choosing a diamond wheel supplier.
The suppliers your company chooses can affect your business in many ways. Qualities like expert support, competitive pricing and speedy turnarounds can make significant differences in your success. Continental Diamond Tool is a world leader in the field of superabrasives for industries that include medical tool manufacturing, construction and aerospace engineering. Our small company philosophies and big company capabilities mean that you are in the hands of ethical, hardworking and capable support. Among the qualities that set us apart from the rest:
Speedy Delivery
Every day your supplies take to get to you is one that can hold up your operation. And, when you deal with another grinding tool supplier, you can wait as long as two months for your custom equipment, leading to slowdowns and delays.
We maintain an extensive inventory of raw materials so that we can complete your order fast in our in-house manufacturing facility. These allow us to supply an unlimited number of superabrasive products that fit your needs, timeline and budget. Our average shipping time is between 15 and 18 working days. We are proud of ability to create tools to order at a speed that gets you back to work as quickly as possible, saving you from expensive downtime.
Helpful Technical Support
Our commitment to you doesn't end when our product leaves the door. We have highly trained and knowledgeable staff that can help you with every phase of production, from prototypes to replacements, to improvements and enhancements. We can help you determine which tools are best for the job, how to implement strategies to make your company's work more efficient. Reach out to us for the assistance that will help you overcome obstacles and clear your way to success.
Global Outreach
Throughout the world, we offer support and custom tools to get the job done. Through innovation and commitment to customers, CDT has become the global leader in superabrasives in a wide range of industries. Our small company values, dedicated technical support and outstanding lead times mean that you can be sure that you can get the tools you need wherever you need them.
Competitive Pricing
CDT produces custom diamond wheels at competitive prices. We help people in all industries keep their costs under control to improve their bottom line and make their businesses more profitable. Our sales and manufacturing team work together to ensure that you are getting quality tools at an affordable price.
Since 1973, CDT has been committed to supplying a wide range of industries with the highest quality custom diamond tools. Contact us today to learn how we can serve your needs.
Grinding Wheels in the Electronics Industry
Grinding wheels and grinding tools of all types play a huge role in the electronic industry - even in ways that many people might not realize.
Grinding wheels and grinding tools of all types play a huge role in the electronic industry - even in ways that many people might not realize. Metal bond grinding tools are used to create a large number of the types of products that we use and love on a daily basis. By taking a look at the types of electronics devices that these important tools help create, you can start to see just how integral of a role they play in life as we know it.
Grinding tools like diamond drills, scoring disks and superabrasive endmills are used during the creation of printed circuit boards, which are a key component to many electronic devices that we find in our homes. If you own a desktop computer, laptop computer, high definition television set or home theater system of any type, you have the advancements enabled by circuit boards to thank for the hours and hours of enjoyment that you have received from these types of devices.
The types of circuit boards that are commonly made using grinding wheels and other grinding tools in the electronics industry are called printed circuit boards. These specific types of deices support various electronic components using tracks and pads that are conductive, allowing electricity to flow from one part of the device to another. The types of printed circuit boards that can be made using grinding wheels of all types include multi-layer boards. Single sided boards, which is a printed circuit board with only one copper layer, and double sided boards, which are a type with two layers of copper, are also commonly made using grinding tools like diamond drills for maximum precision. These types of printed circuit boards are traditionally found in almost every consumer electronic product that you can purchase, except those that are so simplistic in nature that they don't need a circuit board at all.
Part of the reason why diamond drills and metal bond grinding tools are so important to the electronic industry is because of the types of materials that they are capable of processing. Diamond tools in particular are capable of processing carbide alloys, stone, ceramics, semiconductor materials, aluminum, copper, copper alloys, rubber and resin. These types of materials are all used throughout the electronics industry in varying degrees. Copper and copper alloys in particular are hugely useful to electronic devices because they are both incredibly conductive with regards to electricity and resistant to erosion. As a result, they are ideal for situations like copper wiring, like the type that is used to transmit high speed signals into a person's home from a cable television provider.
The Right Tools for the Job
From cars to delicate eyeglasses, you need precision shaping, polishing and grinding tools. CDT makes the tools you need for each job.
Everything can’t be made from wood all the time. For everything else, from cars to delicate eyeglasses, you need precision shaping, polishing and grinding tools. Without the right tools, you can’t work with metal, glass, ceramics or many other materials used by different industries. Use super-abrasive tooling for those machining needs, and enjoy large company capabilities that allow you to handle many more products.
Take a look at plating grinding tools if you want to perform diamond grinding, shaping and polishing. Plated wheels have a single layer of tough diamond that’s exposed, rather than embedded, to create a highly durable bond. The secret of these plated diamond grinding wheels is their replating ability. Send your worn-down diamond grinding wheel to us, and we’ll set you up with an affordable plan so you get a like-new tool. Through the replating process, the tool is completely refurbished to work as it did when you first purchased it.
We have CBN grinding wheels made with the same plating process as well. Shop for plated hole saws or plated bank saw blades to start shaping and manufacturing all the products you want. Looking for a different type of CBN wheel? Look to our selection of metal bonded tools. Cubic boron nitride, CBN, is also used to make many metal bonded CBN grinding wheels.
The metal bonded process gives you a CBN grinding wheel that can handle ceramics, silicon, quartz, glass, optic materials and many other mediums. Metal bonded tools are very long-wearing and low-maintenance. Use them in both wet and dry grinding to complete your project.
Shaping and sculpting is all part of manufacturing, and you want your company involved in all types of manufacturing to appeal to the widest possible base of customers. Shop for super-abrasive tooling that will allow you to get the job done. With our industry best, fast delivery policy, you’ll have grinding tools in as little as one week after purchase. Our products have affordable pricing to give you large company capabilities without the big corporate price tag.
Start getting more done with your business, and get more customers. The right tools allow you to get many more jobs done. Expand your business, and start making more out of your company. When you can start making more products, the sky’s the limit on what you can eventually do. It all begins with good tools suited to the tasks you have on your list.
CDT Launches New Website
CDT is proud to announce the launch of our new website cdtusa.net where you can find product information, industry tips, upcoming trade shows and more.
CDT is proud to announce the launch of our new company website cdtusa.net. We look forward to sharing great information about CDT and our phenomenal products and services, but also serve as a thought leader for everything you need to know about Plated products, Resin Bond products, and Metal Bond products.
We have more than 40 years of experience in the Diamond Tool industry and would like to help any of our customers or visitors by sharing this knowledge. As always, when your product application calls for a diamond or CBN wheel or tooling, you can call on our team of experts and we'll be happy to assist you in any way. Enjoy!
How do Superabrasives compare to conventional abrasives?
Superabrasive wheels do not wear away like conventional wheels, therefore your shop and the air you breathe is much cleaner.
Superabrasives 101
If you’re in the market for superabrasives, it’s important to be familiar with common terms and product types that can help you discover which superabrasive is best for your needs. The metal bond grinding wheel is one of the most commonly used wheels, and the name denotes the metal bonding material that is most often used with a variety of grinding wheel types.
Using metal fillers, grinding wheels suppliers will manufacture the metal grinding wheel to specification. Metal bond is available with cubic boron nitride (CBN) and diamond wheels, and are generally used with coolant to prolong the wheel’s lifespan.
There are several advantages to using metal bond wheels, not least of which is its extended life. A metal bond ensures that the wheel has a fast stock removal. It also leads to a reduction in the dressing frequency and boasts more advanced form holding capabilities. Metal bonds are also extremely strong, so they are typically used in internal, form, glass, ceramic, tool cutting, and creep-feed applications.
A grinding wheel dresser, often referred to simply as a wheel dresser or grinding dresser, is an essential tool that dresses the grinding wheel surface. Dressing a wheel knocks any abrasive particles from the surface in order to make the grinding wheel concentric. This means less vibration and an improved finish. The grinding dresser is also important when cleaning the metal bond grinding wheel. One of the main benefits of using a metal bond grinding wheel is that it requires dressing less frequently than other wheel types.
Metal bond even goes beyond grinding wheels, since diamond core drills, solid diamond drills, and disintegrating core drills can all be manufactured using metal bond. Metal bond is primarily used in wet grinding. It can work well on glass, silicon, semi-conductors, refractories, and ceramics. Many industries choose to use metal bond tools because they are low maintenance but offer high productivity, making them ideal for maximum yield endeavors. They are also available in a range of tools, from the more aggressive CNC grinding down to light polishing.
When searching for grinding wheels suppliers, go with a company experienced in custom manufacturing with a wide range of superabrasives, including metal bond. A reputable company will tailor every order to each individual customer’s needs and offer a knowledgeable customer service that can help you determine the type of tools and products you need. Going with an experienced superabrasives provider will result in unmatched quality and a pleasant buying experience.
What are the benefits of plated vs. bonded?
Our plated products consist of a single layer of Diamond or Cubic Boron Nitride (CBN) which offers the ability for strip and re-plate.
Grinding Wheels 101
A grinding wheel performs a range of abrasive machining operations in industries such as aerospace and petroleum. It can be made by pressing a matrix of coarse particles together into a circular shape, or by coating a solid material with the abrasive compound. The specific materials and shape of a grinding wheel depend on the application, although its manufacture is generally a precise process. Common types of grinding wheels include plated wheels, wheels that use resin to bond the abrasive compound to the wheel and those that use metal bonds.
Plated
A plated grinding wheel has a single layer of abrasive material that’s exposed to the surface, instead of embedding the material within a bonding compound. The abrasive material for this type of grinding wheel is typically cubic boron nitride (CBN) or diamond, which are extremely hard substances. Diamond plated wheels hold their form longer than bonded wheels, and they also form a more aggressive bond.
Plating provides diamond tool manufacturers with the ability to strip the abrasive material from the core product and re-plate it with a new abrasive layer. This advantage results in a plated diamond wheel that’s in “like new” condition, which extends the life of the initial investment.
Resin Bonds
The resins that bond abrasives to grinding wheels are typically phenolic resins, meaning that they are made by reacting phenol. The resin also contains filler materials such as copper and an abrasive material like diamond or CBN. A hot press compresses this mixture into the desired form, which is then cured and machined to a precise shape.
Resin-bonded grinding wheels are highly efficient, allowing them to complete their tasks quickly. These grinding wheels are capable of prolonged use, due to their ability to sharpen themselves and maintain low temperatures during operation. Grinding wheels that use resin bonds are also easy to dress and less prone to overloading. Common applications for these wheels include grinding electrical carbon products such as carbide alloys, ceramics, ferrite and semi-conductors.
Metal Bonds
The metal bonds used by grinding wheels are typically made by sintering powdered metals along with filler materials, and adding an abrasive such as CBN or diamond. These bonds are very strong, providing a grinding wheel that holds its shape well. The durability of metal bonds also means that these grinding wheels require dressing less frequently.
Metal bond abrasive tools offer maximum productivity, and are suitable for a range of applications, from light polishing to aggressive grinding. They’re most often used in wet grinding, but they can also grind dry surfaces such as ceramics, glass, quartz and silicon. Metal-bonded grinding wheels can be used for cutting tools and forms such as refractories. They're also suitable for creep-feed applications.