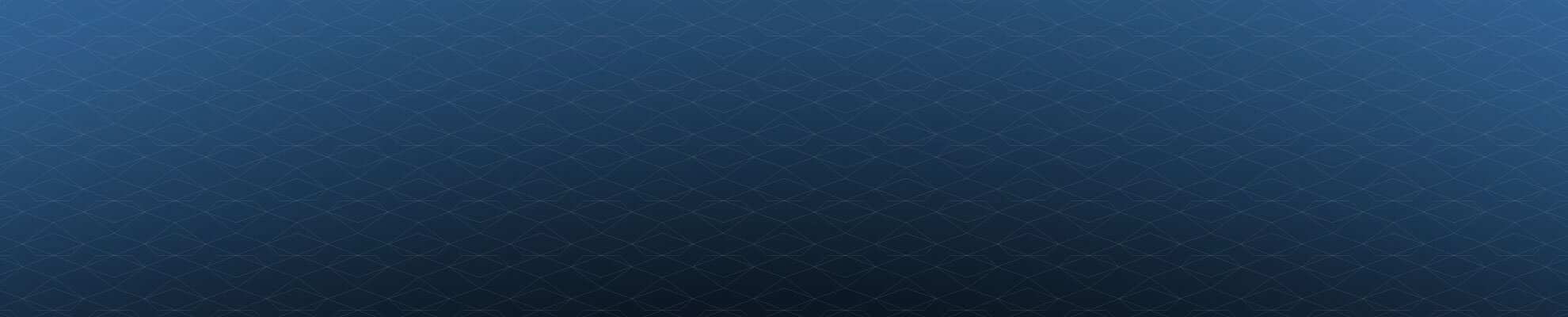
News and Resources
Browse by Category
Browse by Product
- All Dressing Products
- All Grinding Products
- CBN-Diamond Superabrasives
- Conventional Abrasives
- Diamond Lapping Compounds
- Diamond Rotary Dressers
- Diamond Stationary Dressers
- Hybrid Bond Grinding Tools
- Metal Bond Grinding Tools
- Plated Grinding Tools
- Resin Bond Grinding Tools
- Vitrified Bond Grinding Tools
CDT’s Lab Evaluates Blaser Coolants in Flute Grinding Applications
Check out how we tested Blaser coolants on EVO hybrid bond wheels in CDT’s grinding lab to see which best enhances cutting, tool life, and quality in precision flute grinding.
At Continental Diamond Tool (CDT), we pride ourselves on pushing the limits of grinding technology. In one recent trial, The Grinding Chronicles team has partnered with Blaser Swisslube to test the performance of different coolants on our EVO hybrid bond grinding wheels. This experiment in CDT’s grinding lab aims to determine which coolant best enhances cutting performance, tool life, and workpiece quality in precision flute grinding applications.
Parameters for Success
Leading this effort is CDT Application Engineer Harrison Sheldon and CDT Engineering Consultant Jon VanSant, who are testing three different Blaser fluids under controlled conditions. They are measuring key parameters such as power, force, and grinding wheel wear while closely inspecting the visual quality of the workpiece for signs of burn or other surface finish issues.
“Our focus is on how the grinding wheel cuts, wears, and the resulting workpiece quality,” Jon explains. “By measuring parameters like power and force, we aim to collect data that can objectively compare the performance of each coolant under consistent conditions.”
Three representatives from Blaser joined Harrison and Jon last week at CDT’s lab: Senior Application Engineer Brett Reynolds from the New York plant, and Grinding Business Development Managers Tom Cappadona, also from New York, and Simon Stalder, representing Blaser’s headquarters in Switzerland. For this trial, Blaser has provided the coolant fluids, while CDT is supplying the EVO hybrid bond grinding wheels and the data collection equipment in the grinding lab. This setup ensures a comprehensive, scientific approach to analyzing performance with these coolants.
“When Tom approached us about this trial, we saw an opportunity to try something new with the equipment in our grinding lab,” says Harrison. “We’re excited to see how each formula stacks up to help the team at Blaser guide their customers in optimizing their process.”
Simon Stalder expressed his enthusiasm for the trial results, eager to share the findings with his engineering team in Switzerland. These results will provide valuable insights into how Blaser’s latest coolant technology enhances grinding performance and efficiency. As a global leader in metalworking fluids, Blaser delivers tailored formulas for every material, industry, and application.
Benefits of a Dynamic Testing Environment
The dynamic testing environment in CDT's grinding lab allows Harrison and Jon to adjust parameters on the fly, testing variables such as feed rate while maintaining consistent wheel speed. This enables them to evaluate the optimal feed rate range for each coolant type.
“One key advantage of running trials in the lab is the ability to collect objective data in controlled conditions,” says Jon. “Unlike in the field, where varied operator techniques can affect outcomes, our lab setting allows us to isolate variables and focus on actionable insights.”
While Blaser has come to CDT's lab primarily for the technical instrumentation and grinding know-how of our team, customers do not have to travel to take advantage of the lab’s capabilities. “CDT’s grinding lab is exceptionally flexible due to its portability. We frequently gather data directly from our customers’ processes by installing equipment at their site and analyzing it in our lab,” Harrison notes, “or we can simulate their operations on our machines and collaborate remotely to tweak their process.”
The expertise of Blaser’s application engineer, Brett Reynolds, has also been instrumental in these trials. “Brett brings a deep understanding of Blaser’s fluid formulation and their customer applications, which complements our grinding expertise,” adds Jon.
Trials on the Walter Helitronic Machine
As a 5-axis tool and cutter grinder, the Walter Helitronic is a purpose-built machine that is a centerpiece in CDT’s grinding lab and perfect for trials like this. Its versatility and precision are critical for evaluating different grinding configurations.
“The Walter machine is capable of thousands of functions, but it’s most commonly used for round cutting tools, making it perfect for flute grinding trials with our EVO Hybrid Bond fluting wheels,” Harrison says. “Its high precision, repeatability, and compatibility with advanced cooling systems make it the ideal platform for these tests.”
Jon elaborates, “The Walter allows us to make real-time adjustments to speed, feed rate, and pressure, which is essential for testing performance during these trials. Its automation and sensitive readings ensure accurate, repeatable results.”
The team at Blaser is currently reviewing the data gathered from last week’s trial and discussing how to incorporate the insights into future marketing and product development.
Accessing Our Grinding Lab Services
At CDT, we believe in the importance of real-world testing to optimize grinding processes and improve part quality. Our grinding lab is available for trials like these, whether you’re testing new grinding wheels or assessing some other metric of performance.
“Our team’s diverse areas of expertise ensures we can accommodate unique customer needs,” Harrison shares. “Whether it’s conducting tests in our lab or traveling to your site, we provide valuable solutions tailored to each challenge.”
If you’re interested in running a grinding trial with CDT, contact us with details about your process. We can recreate it in our lab or connect at your facility to gather data. From there, we develop testing parameters, share results, and make tailored recommendations for specific tools and production settings.
Learn more about Blaser Swisslube at:
Linkedin.com/company/blaser-swisslube
Youtube.com/user/blaserswisslube1
Harnessing the Power of a Grinding Lab
The best grinding process optimization starts with CDT’s Grinding Lab. Get data-driven insights on cut, wear, quality, and cost to improve efficiency and performance.
When it comes to grinding, the first step in overcoming your challenges is gaining a clear, data-driven understanding of your process. Episode 2 of The Grinding Chronicles, hosted by CDT Application Engineer Harrison Sheldon, shows how using objective data from a grinding lab can significantly improve your process. Watch the video or read on to discover how CDT’s Grinding Lab can help you transition from subjective assessments to actionable insights.
The Grinding Chronicles - Episode 2
Making Sense of the Complex Grinding Process
Grinding is one of the most complex machining processes, involving more variables than most. Traditionally, operators have relied on their senses—sight, sound, and feel—to measure performance. While this may have worked in the past, it introduces subjectivity into the process. No two operators experience grinding in exactly the same way, leading to inconsistencies and inefficiencies. That’s where a grinding lab steps in, providing a more reliable and consistent way to measure performance.
Data-Driven Optimization
At CDT, we believe in using objective data to optimize grinding processes, and our Grinding Lab is at the forefront of this approach. The lab uses a variety of sensors to collect data across four key categories: cut, wear, quality, and cost. By focusing on these areas, we are able to make informed decisions that directly improve performance and efficiency.
Here’s how we break it down:
Cut: The way a grinding wheel cuts is one of the most critical factors in overall performance. In our lab, we focus on three specific variables that help us understand how efficiently a wheel cuts: power, force, and vibration. Power is the energy input to the grinding process, while force reflects the mechanical effort required for material removal. Vibration is a crucial indicator of smoothness and stability in the grinding operation. By collecting data on these variables, we can ensure that the wheel is cutting at its optimal capacity.
Wear: Wear is an inevitable part of any grinding process, but controlling and understanding it is essential for maximizing efficiency. In our Grinding Lab, we use precise measurement techniques to run the wheel through a test coupon, giving us an exact rate of wear. This data allows us to optimize wheel life, reducing the frequency of wheel changes and improving productivity.
Quality: Quality is paramount in grinding, and factors like surface finish and burn must be closely monitored. Burn, for example, is a sign that the grinding process is too aggressive, potentially damaging the workpiece. By measuring surface finish and detecting burn, we ensure that the grinding process meets the high standards required by manufacturers without sacrificing quality.
Cost: In any manufacturing process, cost is a key consideration. Our lab calculates the cost of running the grinding wheel under various conditions, allowing us to find the most cost-effective solution. Whether it’s reducing power consumption, minimizing wear, or improving quality, we aim to optimize processes to deliver the best possible performance at the lowest cost.
Optimizing Your Process
Once we have collected data from the four categories—cut, wear, quality, and cost—we begin the process of optimization. By adjusting key variables, such as wheel speed, we can examine how changes impact the overall performance of the grinding process.
For example, in a recent test we compared two different wheel speeds: 14 meters per second and 24 meters per second. At the higher speed, the system produced more energy, but this came at a cost—burn was observed on the surface of the workpiece. On the other hand, the slower speed resulted in no burn and delivered a smoother surface finish. By analyzing these results, we were able to determine that the slower speed was a better option for both quality and cost-efficiency in that specific scenario.
This is the true power of our data-driven approach. Rather than relying on guesswork or subjective measures, we generate detailed, actionable insights that allow us to make informed decisions. These insights help us to improve efficiency, extend tool life, and reduce operational costs for our customers.
Bringing the Lab to You
One of the unique advantages of CDT’s Grinding Lab is its portability. We understand that every production environment is different, and the conditions in a controlled lab might not perfectly reflect the realities of your facility. That’s why we offer the option to bring our Grinding Lab directly to your site.
Using portable sensors and equipment, we can set up quickly and begin collecting data on your production machines. In as little as an hour, we can install the sensors, return the machines to operation, and start gathering valuable data. This allows us to analyze your specific grinding process in real time, helping you make immediate improvements without needing to transport your equipment or materials to an offsite location.
Whether you are developing a new grinding process or optimizing an existing one, CDT’s portable Grinding Lab offers a fast and effective way to gain insight into your operations.
Why Use a Grinding Lab?
The value of using CDT’s Grinding Lab lies in the objective, reliable data it provides. Unlike subjective measures, which vary from one operator to another, data from the lab is consistent, accurate, and easy to analyze. This data allows us to make informed decisions that improve efficiency, reduce costs, and enhance quality.
By measuring key variables such as power, force, and vibration, we are able to identify areas where performance can be improved. This level of precision is simply not possible with traditional observation methods. The end result? A more efficient, cost-effective grinding process that delivers consistent, high-quality results.
Get in Touch
Are you ready to take the first step toward solving your grinding challenges? Let CDT’s Grinding Lab help you move beyond guesswork and into the world of data-driven optimization. Email us at thegrindingchronicles@cdtusa.net to find out how we can help you develop or optimize your grinding process.
Check out more episodes of The Grinding Chronicles on our YouTube channel, where we continue to explore innovative solutions to your grinding challenges.
And remember, at CDT, we believe in the power of data to drive performance. Be sure to hit like, follow, and subscribe to our channels to stay up to date on our latest insights and updates!
An Essential Guide to Grinding Process Optimization for Boosting Performance in Precision Manufacturing
Optimize your grinding process with expert tips on speeds, feeds, Q-prime, and advanced bond technology to boost efficiency in precision manufacturing.
To stay competitive in precision manufacturing, grinding operations require continuous improvement in performance and efficiency. Understanding the factors that influence grinding, such as speeds, feeds, and material removal rates, can significantly impact your results. In this comprehensive guide from Continental Diamond Tool, Product Engineer Thi Dang and Engineering Consultant Jon VanSant share their expertise as they unpack the essential elements of grinding process optimization. Episode 8 of The Grinding Chronicles offers valuable insights into maximizing Q-prime, balancing G ratios, and selecting the right grinding wheel speeds. Whether you’re looking to refine your current operations or upgrade to the latest in bond technology, our engineering team’s breakdown outlines the key factors you need to consider to enhance your grinding processes. Watch the video or read on to discover practical tips and advanced strategies for getting the most out of your grinding tools.
The Grinding Chronicles - Episode 8
Unlocking the Secrets to Optimizing Your Grinding Process
In this article, you will learn the essentials for optimizing your grinding process, focusing on the metrics that matter most for achieving peak performance. From understanding the basics of speeds and feeds to exploring advanced bond technology, this guide provides actionable insights for any precision manufacturing operation. Whether you're new in the field or looking to enhance your current practices, this informative article from The Grinding Chronicles team offers valuable knowledge to help you get ahead in the industry.
Understanding the Basic METRICS in GRINDING
One of the first considerations when optimizing a grinding process is understanding the basics—speeds, feeds, and material removal rates. These elements are fundamental to the grinding process and play a crucial role in determining the efficiency and quality of the finished product.
Speeds and Feeds:
Speeds refer to the rotational speed of the grinding wheel, typically measured in surface feet per minute (SFM). Feeds, on the other hand, relate to the rate at which the workpiece is fed into the grinding wheel. Together, these parameters influence the rate of material removal, surface finish, and the overall efficiency of the grinding process.
It's essential to understand that faster isn't always better. While higher speeds can increase material removal rates, they can also lead to increased wheel wear and the potential for thermal damage to the workpiece. Therefore, finding the optimal balance between speed and feed is key to maintaining both efficiency and quality.
Material Removal Rate (Q-prime):
Q-prime, or material removal rate, is a critical measure of grinding performance. It is calculated by multiplying the depth of cut by the feed rate, resulting in the amount of material removed per unit time. Higher Q-prime values typically indicate shorter cycle times, which can significantly enhance productivity.
However, achieving high Q-prime values requires careful consideration of other factors, such as wheel wear and the quality of the finished surface. A high Q-prime might reduce cycle times, but if it leads to excessive wheel wear or poor surface quality, the overall efficiency of the process may suffer. Thus, optimizing Q-prime involves balancing it with other critical parameters, such as the G ratio.
The G Ratio:
The G ratio is another vital metric in grinding. It is defined as the volume of material removed from the workpiece divided by the volume of wheel wear. A high G ratio indicates efficient grinding, where more material is removed with less wheel wear. However, similar to Q-prime, achieving an optimal G ratio requires balancing various factors.
Maximizing Q-prime WHILE Balancing the G Ratio
Maximizing Q-prime while maintaining a high G ratio is the key to optimizing grinding processes. To achieve this balance, it’s important to consider the following:
Wheel Speed: Higher wheel speeds can lead to increased wheel wear due to elevated temperatures. Therefore, it’s crucial to find an optimal speed that maximizes material removal without excessively wearing the grinding wheel.
Coolant Delivery: Proper coolant delivery is essential in controlling the temperature during grinding. Efficient coolant systems help dissipate heat, reducing thermal damage to the workpiece and wear on the grinding wheel. This, in turn, helps maintain a high G ratio.
Machine Stiffness and Power: The stiffness of the grinding machine and the power of the spindle also play significant roles. Machines with low power or poor stiffness may limit the achievable Q-prime and G ratio, restricting the overall efficiency of the grinding process.
By carefully considering these factors, manufacturers can optimize their grinding operations to achieve both high Q-prime and G ratios, leading to improved productivity and efficiency.
The Evolution of Bond Technology
Bond technology plays a critical role in the performance of grinding wheels, particularly in their ability to achieve high Q-prime and G ratios. The history of bond technology in grinding wheels is a testament to the continuous advancements that have been made in this field.
A Look Back:
In the 1960s, phenolic resin bonds were the standard, offering Q-prime values of around three. By the 1970s, the introduction of polyimide bonds pushed Q-prime values to around five. The year 2000 marked another leap with hybrid bonds, which increased Q-prime to approximately seven.
Today, we are capable of removing material at rates between 10 and 15, thanks to the latest advancements in bond technology. This evolution highlights the importance of continuously upgrading to the latest bond technology to stay competitive in the market.
Introducing CDT's EVO Hybrid Bond:
Continental Diamond Tool has been at the forefront of these advancements with its EVO Hybrid Bond. Released earlier this year, the EVO Hybrid Bond represents a significant step forward in bond technology, offering the ability to achieve Q-prime values over 10 without compromising the G ratio.
The development of the EVO Hybrid Bond was driven by the need for a bond system that could grind aggressively while minimizing wear and maintaining excellent corner retention. This bond was also designed with thermal conductivity in mind, to transfer heat away from the part and prevent damage to the diamond, which is sensitive to high temperatures. Learn more about CDT’s EVO Hybrid Bond product here.
Practical Tips for Optimizing Your Grinding Process
Now that we’ve covered the theoretical aspects of grinding optimization, let’s look at some practical tips that can help you apply this knowledge to your operations:
Evaluate Your Current Operations: Start by assessing your current grinding processes. Measure your Q-prime and G ratio to establish a baseline. Identify areas where improvements can be made, whether in speed, feed rate, or wheel selection.
Invest in the Latest Technology: Consider upgrading to the latest bond technology, such as CDT’s EVO Hybrid Bond. Newer bonds can significantly improve your material removal rates and reduce wheel wear, leading to better overall efficiency.
Optimize Coolant Delivery: Ensure that your coolant system is operating efficiently. Proper coolant delivery is essential for controlling temperatures and reducing thermal damage, which can extend the life of your grinding wheels and improve the quality of your finished products.
Regularly Maintain Equipment: Regular maintenance of your grinding machines is crucial. Ensure that your machines are running at optimal stiffness and power to maximize performance and avoid limitations in Q-prime and G ratios.
Train Your Team: Make sure your team is trained on the latest grinding techniques and technologies. A well-informed team can make better decisions on the shop floor, leading to improved productivity and efficiency. At Continental Diamond Tool, our application engineers are here to help. We regularly connect with our customers to fine-tune their equipment and train their operators on the optimized speeds and feed rates to use with our grinding wheels.
Optimizing grinding processes is essential for staying competitive in precision manufacturing. By understanding and balancing key factors like Q-prime, G ratio, and wheel speed, manufacturers can significantly enhance their grinding operations. Continental Diamond Tool’s latest advancements, including the EVO Hybrid Bond, provide valuable tools for achieving these goals. Whether you’re looking to improve your current processes or invest in new technologies, the insights provided in this guide offer a clear path to optimizing your grinding operations. Implement these strategies to ensure your manufacturing processes are both efficient and effective, helping you to stay ahead in a demanding industry.
How to Diagnose Surface Pattern Problems in Grinding
Learn how to diagnose and fix common surface pattern problems in precision grinding with expert insights from CDT's Senior Product Engineer, Paul Christy.
Many precision grinding operations require impeccable surface finishes for both function and aesthetics. Addressing surface pattern problems is vital for ensuring the quality of the final product, eliminating waste, and controlling costs. In this detailed overview, we expand on the insights provided by Paul Christy, Senior Product Engineer at Continental Diamond Tool, as he explains how to troubleshoot and fix common causes of surface patterns. In Episode 7 of The Grinding Chronicles, Paul covers the complexities of surface patterns caused by various types of vibrations, runout, and servo system instability. Watch Paul’s video or read on to learn more about identifying and addressing these issues to optimize your grinding operations.
The Grinding Chronicles - Episode 7
Surface Pattern Troubleshooting Guide
Surface pattern problems in grinding can significantly impact the quality and precision of your workpieces. Diagnosing and resolving these issues requires a deep understanding of the underlying causes and appropriate troubleshooting techniques. This article explores common causes of surface patterns in grinding and provides expert insights into their diagnosis and elimination.
Self-Excited Vibration
One of the primary causes of surface pattern problems is self-excited vibration, which occurs at the natural frequency of the machine system. This type of vibration indicates that some component within the machine—such as the spindle, the part, or the dresser—is being excited. The resulting oscillating pattern is called chatter. Notably, this vibration only manifests when the grinding wheel and the workpiece (or the wheel and the dresser) are in contact.
Self-excited vibration results from a lack of sufficient component stiffness. The key to mitigating this issue lies in increasing the machine's stability, which requires a greater machine stiffness compared to the process stiffness. There are three main process variables that can be adjusted to help eliminate self-excited vibration:
Velocity of the Workpiece: Lowering the workpiece's speed can reduce process stiffness.
Velocity of the Grinding Wheel: Decreasing the grinding wheel's speed similarly lessens process stiffness.
Width of Contact: Reducing the contact width between the grinding wheel and the workpiece can also help.
By strategically lowering one or more of these variables, you can effectively diminish the impact of self-excited vibration.
Forced Vibration
Forced vibration occurs at a frequency corresponding to a driving force within or outside the machine. Common examples of such driving forces include unbalanced rotating bodies and pump pulsations. This type of vibration can often be diagnosed using a process of elimination. By sequentially turning on and off all rotating bodies within the machine, you can identify the source of the vibration when it ceases upon the deactivation of a specific component.
Runout
Runout is a prevalent issue in grinding due to the inherent imperfections of rotating components. It occurs when the outer surface of a rotating component does not maintain perfect concentricity with its axis or center line. Specifically, runout in a traversing diamond roll can create a pattern in the grinding wheel, which is then transferred to the workpiece. This pattern typically manifests as angled parallel lines, known as Barber Pole or Roping Patterns.
To address surface patterns caused by runout, it is essential to identify the optimal dresser and wheel RPMs. Varying the diamond roll speed during dressing can reduce the likelihood of pattern formation on the grinding wheel, preventing its transfer to the workpiece. Another effective solution is lapping the diamond roll to the machine's spindle bearings, thereby eliminating runout.
Servo System Instability
Servo system instability is another potential source of surface patterns on workpieces. The servo system controls the movement accuracy of machine components, using digital feedback to ensure precise positioning. Mechanical decoupling within components such as ball nuts, couplings, bearing support units, or scale mountings can create discord within the servo system. This results in oscillations as the system struggles to determine the correct position, leading to surface patterns on the workpiece.
Solving servo system instability typically requires sophisticated instrumentation and physics-based analysis. Iterative process changes alone are unlikely to resolve this complex issue.
Key Takeaways in Mastering Surface Finish
Diagnosing and fixing surface pattern problems in grinding necessitates a thorough understanding of the potential causes and their specific remedies. Whether dealing with self-excited vibration, forced vibration, runout, or servo system instability, targeted adjustments and precise troubleshooting are essential for maintaining the quality and precision of your grinding operations.
For more detailed information and expert guidance, refer to Episode 7 of The Grinding Chronicles, where Paul Christy shows specific measures you can take to diagnose and eliminate surface pattern problems. If you are experiencing surface patterns similar to those discussed in this article and require further assistance, do not hesitate to contact the Continental Diamond Tool engineering team at TheGrindingChronicles@cdtusa.net.
Understanding and addressing these grinding challenges will enhance your operational efficiency and ensure the superior quality of your manufactured products.
A Breakdown of the 4 Common Bond Systems in High Precision Grinding
Discover CDT's four essential bond systems for superabrasive grinding wheels: Resin, Metal, Vitrified, and Electroplated. Optimize operations with expert insights from Jeff Wirth.
If precision grinding is a critical component of your manufacturing process, understanding the bond system of your grinding wheel will help you in maintaining operational efficiency and product quality. In this detailed overview, we will explore the four most common bond systems used in superabrasive grinding wheels: Resin, Metal, Vitrified, and Electroplated. Continental Diamond Tool Engineering Manager Jeff Wirth breaks down the components of these bond systems, discussing their composition, manufacturing processes, and ideal applications in Episode 6 of The Grinding Chronicles. Watch Jeff’s video or read on to learn more about selecting the right bond to optimize your grinding operations.
The Grinding Chronicles - Episode 6
Understanding the Four Common Bond Systems
Resin Bonds
Resin bonds are plastic-based compounds typically made from phenolics or polyimides. These bonds are versatile and can be enhanced with fillers such as copper or silicon carbide to improve performance. The manufacturing process for resin bonds at CDT begins with creating a tailored formulation that includes the bond material, abrasive, and fillers. This dry powder mixture is blended in special tumblers and then carefully and uniformly packed into mold cavities. The molds undergo hot pressing, where temperature and pressure are meticulously controlled to achieve the desired density. Finally, the wheels are finished by machining and grinding them to the specified size and geometry.
Properties and Applications:
Tough and Durable: Resin bonds are fully dense and easy to use, making them suitable for a variety of grinding applications.
Versatile: They can work with nearly any material, from hard metals to softer alloys.
Enhanced Performance: Fillers like copper or silicon carbide can be added to improve heat dissipation and grinding efficiency.
Wide Range of Applications: Suitable for diverse grinding tasks, including tool and cutter grinding, centerless grinding, and surface grinding.
Metal Bonds
Metal bonds can be composed of various metals, including bronze, copper, and iron, and may sometimes be alloyed with precious metals like silver. Metal bonds are known for their hardness, toughness, and durability, making them ideal for grinding highly abrasive materials such as glass and ceramics. Although metal bonds grind more slowly than other types, they offer the longest lifespan. The manufacturing process for metal bonds at CDT is similar to that of resin bonds, involving formulation, mixing, molding, hot pressing, and finishing.
Properties and Applications:
Hardest and Toughest: Metal bonds are the most challenging to use but provide superior durability.
Long-Lasting: They offer the longest lifespan among bond types, reducing the frequency of wheel changes.
Ideal for Abrasive Materials: Best suited for grinding materials like glass, ceramics, and carbide.
Durability: Excellent for applications requiring extreme durability and extended wheel life, such as in the automotive and aerospace industries.
Vitrified Bonds
Vitrified bonds are made from glass or ceramic materials, creating a porous structure that significantly reduces grinding force. This allows for higher grinding speeds, making vitrified bonds ideal for high-production applications. These bonds offer moderate to high material removal rates and excellent form accuracy, as they can be dressed and profiled in-process using rotary dressers. The manufacturing process for vitrified wheels at CDT involves formulation, mixing, cold pressing, and a sintering (baking) process to fuse the glass or ceramic together. The final step is finishing, similar to the other bond types.
Properties and Applications:
Porous Structure: Lowers grinding force and allows increased speeds, enhancing efficiency.
High Production: Ideal for high-production applications such as automotive part manufacturing.
Moderate to High Material Removal Rates: Efficient for large-scale operations, balancing speed and precision.
High Form Accuracy: Can be dressed and profiled in-process using rotary dressers, making them suitable for precise and consistent grinding tasks.
Electroplated Bonds
Electroplated (or plated) bonds consist of a single layer of abrasive held by a nickel-based metal bond. The process begins with machining the desired wheel size and geometry onto a steel wheel core. The non-plated surfaces are masked to prevent unwanted plating. The wheel core is then placed in a bath with a nickel-based solution and the abrasive material. By applying a positive charge on one side and a negative charge on the other, nickel plating is deposited onto the wheel core, causing a single layer of abrasive to adhere. Excess abrasive is removed, and the plating process continues until the abrasive layer is encapsulated to the desired level, typically 50-100% depending on the application. Electroplated products are suitable for complex geometries and low to medium production applications due to their high material removal rates and fast grinding speeds.
Properties and Applications:
High Material Removal Rates: Provides the fastest grinding speeds, ideal for rapid material removal.
Cost-Effective: Single layer of abrasive can be stripped and replated, extending the wheel’s life.
Ideal for Complex Geometries: Precise form replication with minimal finishing, suitable for intricate designs.
Low to Medium Production: Suitable for specific applications requiring detailed shapes and efficient material removal.
Key Considerations for Selecting the Right Bond System:
Choosing the appropriate bond system for your grinding application is crucial for achieving optimal performance and quality. Each bond type offers unique properties and advantages, making them suitable for different materials and grinding conditions. By understanding the composition, manufacturing processes, and ideal applications of Resin, Metal, Vitrified, and Electroplated bonds, you can make informed decisions to enhance your grinding operations.
Factors in Bond System Selection:
Material to be Ground: The hardness and abrasiveness of the material significantly influence the choice of bond.
Grinding Speed and Efficiency: Consider whether the application requires high-speed grinding or if longevity and durability are more critical.
Application Specifics: Determine if the grinding operation involves complex geometries or requires high form accuracy.
Production Volume: High-production environments may benefit from vitrified bonds, while electroplated bonds are ideal for low to medium production with intricate details.
If you have any questions or want to learn more about which bond type would work best for your application, please reach out to our application engineers at TheGrindingChronicles@CDTUSA.net. For more industry insights and expert advice, check out these articles or watch our playlist for The Grinding Chronicles on YouTube. By leveraging the right bond system and understanding its properties, you can significantly improve your grinding efficiency, product quality, and operational cost-effectiveness.
How to Dress a Vitrified CBN Grinding Wheel with a Diamond Rotary Dresser
In episode 5 of The Grinding Chronicles, CDT Product Manager Troy Giacherio shares top techniques for dressing Vitrified CBN grinding wheels using Diamond Rotary Dressers. Learn how to use key parameters such as velocity ratio and overlap ratio to enhance dressing and truing operations in precision grinding.
If you work in manufacturing, particularly in the specialized area of precision grinding, it cannot be overstated the importance of wheel dressing to maintain operational efficiency and product quality. In this comprehensive guide, we will look at the best techniques for traverse dressing a vitrified cubic boron nitride (CBN) wheel using Rotary Diamond Dressers. In Episode 5 of The Grinding Chronicles, CDT Product Manager Troy Giacherio details the specific parameters and most important factors necessary for achieving peak performance in dressing and truing operations. Watch Troy’s video or read on to learn more.
The Grinding Chronicles - Episode 5
Best Techniques for Success When Dressing a Grinding Wheel
Before plunging into the specifics of dressing a Vitrified CBN wheel, it's imperative to understand the dichotomy between two fundamental processes: truing and dressing. Truing involves sculpting the shape or profile of the grinding wheel, while dressing focuses on sharpening the wheel and removing accumulated debris. While diamond rotary dressers serve both functions, understanding this distinction facilitates the implementation of effective dressing strategies.
Essential Parameters for Dressing Success
There are four key parameters to measure for optimizing the dressing of a grinding wheel:
Velocity Ratio At the heart of dressing lies the velocity ratio, calculated by dividing the velocity of the diamond roll by the velocity of the grinding wheel. This parameter holds significant importance in dressing operations. For Vitrified CBN wheels, the recommended velocity ratio stands at 0.8. Maintaining this ratio ensures that the diamond roll adeptly removes the bond material, laying bare fresh abrasives for optimal grinding performance.
Overlap Ratio The overlap ratio describes the velocity at which the diamond dresser traverses the wheel's face to sculpt its profile and hone its edge. For Vitrified Bond CBN wheels, an overlap ratio ranging between 2 to 4 is ideal. Sustaining a steady pace ensures a seamless traversal across the grinding wheel. It is important to prevent the dresser from dwelling in any single spot to guarantee uniform dressing proficiency.
Depth of Dress The depth of dress measures the extent to which the diamond roll plunges into the grinding wheel, thereby dictating the volume of material extracted per pass. When it comes to Vitrified CBN wheels, we recommend a precise depth of dress set at 0.0002 inches per pass. Adherence to this specification not only optimizes grinding efficiency and minimizes downtime, particularly in high-volume production environments, but also preserves the longevity of the grinding wheel, yielding an optimized return on investment.
Dress Interval The dress interval is defined as the frequency at which the grinding wheel needs dressing, and it is closely tied to the application at hand. Unlike their conventional abrasive counterparts, Vitrified CBN wheels do not require frequent dressing. On the contrary, it is not uncommon to grind hundreds of parts between each dressing session. However, it is important to remain vigilant. Keep an eye on the process and be prepared to adjust the dress interval if part quality diminishes.
When Should I Dress My Grinding Wheel?
Dressing frequency varies depending on several factors specific to your process. Here are two key indicators to monitor in order to assess grinding efficacy and determine when it's time to dress your grinding wheel.
Power Draw The power draw during grinding operations can be a reliable indicator for grinding wheel dressing. A drop in power draw signals that the wheel is cutting freely, with utmost efficiency, while an uptick in power suggests a looming need for dressing. Neglecting timely dressing can lead to issues such as burn or unwanted variations in surface finish. That’s why it is important to keep a close eye on power draw dynamics to prevent such issues.
Surface Finish The surface finish of machined parts relies heavily on consistently high levels of grinding performance. A well dressed wheel produces exceptional surface finishes characterized by minimal variations and unyielding consistency in part quality and dimensional accuracy. Therefore, regular dressing sessions conducted with meticulous technique are essential for maintaining superb parts quality and excellence.
Troubleshooting and Optimization
If you are still experiencing issues such as finish patterns or burn despite adhering to prescribed dressing parameters, it may be time to call in the assistance of an expert. Companies like Continental Diamond Tool have application engineers who are trained to analyze grinding processes, pinpoint underlying issues, and facilitate optimization for enhanced performance. Armed with a portable grinding lab, these experts bring their expertise on-site to meticulously evaluate coolant delivery systems, fine-tune machine settings, and traverse a gamut of other variables to resolve persistent challenges. With their help, you can galvanize productivity to unprecedented heights. If you would like help with your wheel dressing or grinding process, don't hesitate to reach out to our engineering team at TheGrindingChronicles@CDTUSA.net.
Mastering Wheel Dressing
Proper dressing of a Vitrified CBN grinding wheel with a Diamond Rotary Dresser is the key to optimal grinding performance and part quality. By incorporating the parameters and techniques we’ve outlined in this article, manufacturers can achieve reductions in downtime, extension of wheel life, and unwavering consistency in high quality results.
Additionally, by closely watching power draw and surface finish, you will know when it is time to dress before problems get out of hand. With consistent dressing, and seeking expert help when needed, companies can overcome grinding challenges and greatly improve productivity.
Whether transitioning from conventional abrasives to CBN or seeking to refine existing grinding processes, mastering proper dressing techniques with Diamond Rotary Dressers holds the key to consistent and dependable success. Check out more grinding related topics in other episodes of The Grinding Chronicles from Continental Diamond Tool.
Conventional Abrasives vs. Superabrasives
In Episode 4 of The Grinding Chronicles learn how the properties of common abrasives impact wheel life and cutting efficiency. Avoid pitfalls with industry expert Jon VanSant.
In Episode 4 of The Grinding Chronicles, Continental Diamond Tool Engineering Consultant Jon VanSant investigates the history of common abrasive materials and their key differentiating characteristics that impact wheel life, cutting performance, and efficiency. Using the wrong abrasive for your application can significantly increase your cost per part. Watch Jon’s video or read the article below to learn the differences between conventional abrasives and superabrasives.
The Grinding Chronicles - Episode 4
Understanding Abrasive Evolution
In the early 1800s, precision grinding relied on naturally occurring abrasives like emery. Fast forward to the late 19th century, and we witnessed pivotal developments with the advent of "Carborundum" or silicon-carbide by Dr. Edward Acheson in 1891, followed by the patenting of 'Alundum' or aluminum oxide by Aldus Higgins in 1904. The landscape changed once again with the introduction of synthetic diamond in 1954 and cubic boron nitride (cBN) in 1957, marking the emergence of superabrasives. Although superabrasives were first synthesized in the 1950’s, it took two decades before commercial products became available.
Distinguishing Characteristics
To understand the difference between conventional abrasives and superabrasives, let’s examine three key characteristics: hardness, thermal conductivity, and friability.
Hardness: An important consideration in abrasive selection, superabrasives like cBN and Diamond demonstrate superior hardness compared to Aluminum Oxide and Silicon Carbide. This is part of what makes superabrasives super, and makes them particularly efficient when grinding extremely hard materials.
Thermal Conductivity: Enhanced thermal conductivity facilitates efficient heat transfer during grinding operations, ensuring minimal damage to the workpiece. This is critical where surface finish is concerned.
Friability: Friability reflects the fracture or impact toughness of an abrasive and underscores another crucial aspect. Analysis reveal a substantial disparity between conventional and superabrasives, with the latter exhibiting remarkable compression fracture strength. When comparing the compression fracture strength of diamond and aluminum oxide at a particle size of 400 microns, there is a 10:1 difference between the conventional abrasive and the superabrasive.
Performance Metrics
Moving beyond physical attributes, an examination of performance metrics such as cut, wear, and dressing efficiency further demonstrates superabrasives prowess.
Cutting Efficiency: Superabrasives like Diamond and cBN require less power and force for cutting operations, ensuring efficient material removal.
Wear Resistance: Superabrasives demonstrate significantly higher wear resistance, leading to prolonged wheel life and reduced downtime when compared to conventional abrasives.
Dressing Efficiency: Superabrasives also excel when considering downtime for dressing since they maintain dressing efficiency over extended periods. In some cases, we have seen up to 20 times the parts per dress. With less frequent dressing comes more consistent performance. Plus, you’re only taking off a tenth of the material in dressing, so your wheel lasts much longer.
Cost Considerations
Superabrasives, with their many advantages, do come with a substantial up-front investment. Even so, many companies see sustainable returns.
Long-Term Value: Superabrasives offer enhanced productivity and cost-effectiveness that often results in lower cost per part over time.
Application Considerations: Recognizing that not every application warrants a superabrasive grinding wheel, factors such as machine tools, fluid compatibility, and work volume must be considered. Superabrasives are most cost effective in high volume, extremely demanding applications.
Expert Guidance
Thank you for joining us on this exploration of grinding wheel abrasives. If you would like help deciding which abrasive would work best to optimize your grinding process, don't hesitate to reach out to our engineering team at TheGrindingChronicles@CDTUSA.net. Until next time, check out additional insights and discoveries on other episodes of The Grinding Chronicles.
Coolant Application Techniques to Reduce Wheel Wear and Burn in Grinding
Discover essential coolant application strategies to enhance grinding performance, reduce wheel wear, and prevent burn in this article with video.
In Episode 3 of The Grinding Chronicles, Continental Diamond Tool Application Engineer Blu Conrad explains some essential aspects of coolant application that can impact your grinding performance. By having the correct placement of coolant lines and optimizing your coolant setup, you can significantly reduce cycle times, minimize wheel wear, and prevent burning during the grinding process. Watch Blu’s video or read the article below to learn how.
The Grinding Chronicles - Episode 3
Coolant Application and Its Impact on Grinding Performance
Most grinding operators know that reducing heat generation in grinding is crucial for avoiding excessive wheel wear and burn. However, you might not be aware of the various strategies available for achieving this goal. In this article, we will explore how coolant application can mitigate these factors. It starts with four key considerations in cooling: Velocity, Flow, Line Placement, and Temperature.
Velocity Matters
One critical factor in effective coolant application is ensuring that the coolant is spraying at the correct velocity, typically ranging between 70% and 100% of your grinding wheel speed. This velocity is essential because of a force called the air barrier.
As a grinding wheel rotates, it creates an air barrier around its perimeter. To penetrate this barrier and deliver coolant to the grinding zone, the coolant stream must travel at the appropriate velocity. If it is too slow, the grinding wheel can blow the coolant away. Conversely, if the velocity is too high, the coolant may make contact with the grinding wheel and bounce off, rendering it ineffective in reaching the desired area.
Balancing Flow Rate
In addition to velocity, the amount of coolant flowing from the coolant line, known as the Flow Rate, is equally crucial. Flow rate and velocity are interrelated, and their optimization is a balancing act.
In grinding, you often have a choice between low-pressure, high-flow setups, or high-pressure, low-flow configurations. If the flow rate is too low, there won't be enough coolant to adequately cool the grinding process, potentially leading to overheating and damage. Conversely, if the flow rate is excessively high, you will be wasting coolant, resulting in inefficiency and increased operational costs.
Utilizing Nozzles for Optimization
A practical approach to achieving the ideal Velocity and Flow is by using nozzles. While standard jet nozzles are suitable for many grinding applications, different grinding processes may require wheels with distinct shapes, such as flat or radial profiles.
In such cases, it is often more effective to employ nozzles and coolant lines that have been specifically engineered, designed, and tuned to accommodate these unique wheel types. This ensures that the coolant is delivered with the appropriate velocity, flow, and, equally importantly, in the correct position.
Positioning and Direction
The position and direction of the coolant are critical factors in coolant application efficiency. Ideally, you want your coolant jet to spray just before the point of contact, where the grinding wheel and workpiece meet. Additionally, the coolant should flow in the same direction as the rotation of the grinding wheel.
If the coolant stream strikes too far above or behind the point of grinding contact, it will fail to effectively enter the grinding zone, missing the opportunity to cool the process where it is needed most.
Achieving Efficiency in Your Grinding Process
Optimizing coolant applications is a fundamental aspect of enhancing the efficiency and performance of your grinding processes. By carefully considering Velocity, Flow, Line Placement, and Temperature, you can significantly improve cycle times, reduce wheel wear, and prevent burning during grinding operations.
At Continental Diamond Tool, we understand the importance of precision coolant applications and many other factors in achieving superior results. Whether you require standard jet nozzles or specialized coolant solutions tailored to your specific needs, we have the expertise and technology to help you isolate those parameters that are holding back your grinding performance.
To explore our range of grinding solutions and learn more about how we can assist you in achieving exceptional cycle times and wheel life, email us at TheGrindingChronicles@cdtusa.net. Our engineers welcome the opportunity to meet your most challenging tooling requirements.
Releasing "The Grinding Chronicles" Your Gateway to Optimized Grinding Processes
Check out CDT's new video series 'The Grinding Chronicles' as our team explores strategies to optimization the grinding process. Watch episodes 1 and 2 now >
Exciting news for those involved in precision grinding! This month, Continental Diamond Tool (CDT) proudly unveiled "The Grinding Chronicles," a video series aimed at unraveling the complexities of grinding techniques. Led by our team of expert product and application engineers, this series aims to empower and educate individuals seeking to enhance efficiency and reduce costs in their grinding operations.
Episode 1
Introduction to The Grinding Chronicles
The series kicks off with Nick Viggiano, President of CDT, extending a warm welcome to viewers. He introduces the team and outlines the series' core mission: addressing common grinding queries and tackling significant challenges encountered during the grinding process. With decades of expertise in crafting precision grinding products and innovative solutions, CDT promises to share valuable insights throughout this series.
Episode 2
Harnessing the Power of a Grinding Lab
In episode two, CDT Application Engineer Harrison Sheldon explores the benefits of using a grinding lab to improve grinding processes. Relying solely on personal judgments during grinding can lead to mistakes. Sheldon shows how sensors gather objective data, providing more accurate measurements. Discover how CDT's lab collects and analyzes data in four critical areas: Cut, Wear, Quality, and Cost.
Engage with The Grinding Chronicles
"The Grinding Chronicles" isn't just a viewing experience; it's a platform tailored to your needs. CDT invites active participation, encouraging viewers to submit their questions, challenges, and episode ideas. This series aims to address specific concerns of industry professionals who use our products.
Email us at TheGrindingChronicles@cdtusa.net with your questions, and we will do our best to answer them.
Explore Further with CDT's Grinding Lab
CDT's grinding lab has been a game-changer for those who have used it, enhancing operations through data-driven decision-making rather than relying on instinct. It can simulate various grinding environments and offers on-site analysis, ensuring minimal downtime for CDT customers. Plus, it’s complimentary for our customers to use.
In episode 2, you can witness how lab-generated data optimizes real-world grinding processes. Sheldon demonstrates how manipulating and measuring variables, like wheel speed, can help make smarter choices, yielding better results and cost savings.
If you're interested in leveraging a data-centric approach for process development or optimization, reach out to us at TheGrindingChronicles@cdtusa.net. Improving efficiency and precision is what we do.
Subscribe and Stay Tuned
Subscribe to CDT's YouTube channel to catch new episodes of "The Grinding Chronicles." Here are some upcoming topics you won’t want to miss:
Coolant and Its Effect on Grinding Performance
Conventional Abrasives vs. Superabrasives
Q-Prime, G-Ratio, Speeds & Feeds
How to Extend the Life of Your Electroplated Grinding Wheel
CDT’s “Strip and Replate” Program is designed to give our customers the highest quality grinding wheel abrasives for the longest time possible, in the most cost effective way for the customer. Learn how this process works and when you might need to do this >
CDT offers what’s called the “Strip and Replate” Program, designed to give our customers the highest quality grinding wheel abrasives for the longest time possible, in the most cost effective way for the customer (more on this in a moment)...
First, let’s cover when you’ll want to opt for this program, and how it works.
Stripping and replating a grinding wheel refers to the process of removing the old, worn-out abrasive material from the surface of a grinding wheel and replacing it with new abrasive material.
When customers opt in for this program, we work with you to create customized tooling that you will be able to use and then bring back to CDT for us to return it to “like new” condition after it begins to wear. This keeps your wheel fresh and performing at optimal levels without having to buy new.
When To Strip and Replate?
There are many reasons why you may need to replace your wheel with new abrasive, including:
The particles on the surface of your abrasive get clogged (potentially from metal shavings or debris from the grinding process)
Your wheel becomes dull from the worn out abrasive
You need to switch from grinding one material to another, and the new material requires a different type of abrasive to be put on your wheel
The grinding wheel has worn down unevenly, causing vibrations and reducing your wheel’s effectiveness
How Does The Process Work?
CDT is able to provide high quality strip and replate services through strip technology that will remove the remaining abrasive on your worn down wheel without damaging the surface finish of the core.
Electroplating involves depositing a thin layer of metal and abrasive particles onto the surface of a grinding wheel by using an electrical current in an electrolytic plating solution.
When a grinding wheel has reached its life, we remove the old abrasive material on your wheel by soaking the wheel in a chemical solution that will safely dissolve the deposited plating without damaging the integrity of the core.
Once the old deposit and abrasive have been removed, we apply a new layer of abrasive material through the electroplating process.
After the new abrasive material has been applied, the grinding wheel is re-balanced to ensure you continue to have smooth operation and optimal performance with your returned “like new” wheel.
When is An Electroplated Grinding Wheel The Best Choice?
Electroplated grinding wheels are considered the superior choice for applications that require complex shapes or geometries. Some specific applications include metal cutting tools, saw and knife sharpening, PCD grinding, and surgical tool blade sharpening – among others.
They’re used in a wide range of industries, including metalworking, woodworking, glass and ceramics, aerospace, automotive, medical, and electronics manufacturing.
Common materials that are compatible with an electroplated diamond grinding wheel include:
Cemented carbide
Glass
Ceramics
Fiberglass
Plastics
And more
Whereas common materials that are compatible with an electroplated CBN grinding wheel include:
Die steel
Hardened carbon steels
Hardened stainless steels
Alloy steels
Aerospace alloys
And more
When you add in the ability to strip and replate, it makes electroplating a superior choice in many ways:
It provides a more consistent and uniform distribution of abrasive particles on the surface of your grinding wheel, which can help ensure consistent grinding results and prevent uneven wear in the future.
Electroplating creates a strong bond between the abrasive particles and the wheel substrate, which helps prevent the abrasive from separating or shedding from your wheel during use.
It can be used to apply a wide variety of abrasive materials, including diamond, cubic boron nitride (CBN), and various types of abrasive grains – and it can be used with both brittle materials and soft metals.
Stripping and replating an electroplated grinding wheel is a relatively quick and straightforward process because they are a single layer wheel. It also allows for precise control over the thickness of the abrasive layer, making it an ideal choice for achieving any customizations you may need for your wheel.
Electroplated wheels can withstand heavy use and provide consistent grinding performance. They don’t need to be reconditioned as frequently as other types of grinding wheels, making them a more cost-effective choice in the long run.
Overall, opting for an electroplated grinding wheel to be reconditioned and used again through the CDT “Strip and Replate” Program can result in 40% more in savings, with consistent performance results, rather than opting for brand new plated products.
If you’re ready to learn how CDT can work with you for a customized electroplated grinding wheel that qualifies for our “Strip and Replate” Program, click the button below to request a quote!
The CDT technical team is ready to provide abrasive solutions to your questions that will increase your performance while reducing waste.
What should you look for in a grinding wheel manufacturer?
Finding the right supplier of custom manufactured grinding wheels is crucial when your production is on the line. Here’s why you should consider trusting in CDT >
When you’re in search of a supplier of custom manufactured grinding wheels, we know you’re going to be focused on three main components: delivery, performance, and support.
At CDT, we deliver engineered solutions to help you complete your project on time. We will also meet or exceed any requirements you have for surface finish, tolerance holding, cycle time reduction, or anything else for which you are needing engineer solutions. We also provide support throughout the duration of the entire project, from beginning to end.
“We provide information and support all along the way,” says Harrison Sheldon, Application Engineer.
Watch our video to find out more about our commitment to excellence for our customers:
What is the benefit of having a grinding lab on site?
Our grinding lab gives us the opportunity to work with customers to develop grinding processes that are specific to their materials, equipment, and applications. Learn more >
Here at CDT, we have a technologically advanced research and development grinding lab. This gives us the opportunity to work with customers to develop grinding processes that are specific to their materials, equipment, and applications. Our setup is unique, in that we’ve added numerous extra sensors to capture data on every element of the grinding process, to replicate what’s happening in the customer’s actual facilities.
We have a twofold product commitment to the Grinding Lab. One, we can develop processes for the customer and their specific application. Two, we can internally develop advanced new products that solve issues for customers before they are even known.
CDT’s customer service commitment includes the lab as well, inviting customers to reach out to us, to use our grinding lab to solve their grinding problems. Benefits to CDT customers include:
Faster product development
Cost savings/reduced risk
Opportunities to innovate
Valuable data
Remote product testing
Read more about these benefits here or watch clips of the Grinding Lab in action, and hear more about it from Jeff Wirth, our Engineering Manager in this video:
Why Superabrasives?
Superabrasive grinding wheels last longer, grind faster, cut cleaner, leave a better finish and create a sharper edge. The real question is—Why not?
When the material you are trying to process is either too hard or too delicate for conventional abrasives, custom superabrasive grinding tools might be the best solution.
What are Superabrasives?
The term “superabrasives” refers to a class of tools used in precision grinding for many industries. Superabrasive grinding products contain natural diamond, manmade diamond, and/or CBN — some of the hardest materials that can be made. Superabrasives are also sometimes called industrial diamonds: an industrial diamond is a non-gem quality small diamond that is for abrasives, cutting, and drilling tools. Other types of superabrasives include:
Cubic boron nitride (CBN): Usually called CBN, this is the second hardest cutting tool material after a diamond.
Polycrystalline: This is an abrasive material that has multiple collections of crystal grain structures with individual orientations.
CVD Diamond: These are synthetic diamonds made by a process known as chemical vapor deposition. CVD diamonds grow from a hydrocarbon gas mixture. They are extremely hard and have a high thermal conductivity that is five times that of copper. They also have broadband optical transparency, are chemically inert, and only reach graphitization at very high temperatures.
Nano-diamonds: These tiny diamonds are the product of a controlled explosion. They are sometimes called detonation nano-diamonds (DND) or an ultra-dispersed diamonds after how they are formed.
These abrasive materials have been labeled as superabrasive due to their extraordinary hardness, unparalleled performance, and longevity. Continental Diamond Tool uses these superabrasive materials to make custom grinding wheels and products, including plated, vitrified, resin bond, metal bond, hybrid bonds, and rotary dressers, for many complex applications.
Superabrasives vs. Conventional Abrasives
Superabrasives, whether natural or manmade, have a hardness range that distinguishes them as some of the most durable materials on Earth. Conventional abrasives are made with much softer abrasive materials that are less expensive but break down faster. The best abrasive product for your application depends on the material you are grinding and what properties you need to achieve your desired results.
Industries that Use Superabrasives
A great number of industries use superabrasive grinding wheels, and the custom-coated abrasives subsection of the abrasives industry continues to grow. Industries that regularly invest in superabrasive grinding wheels are:
Aerospace
Automotive
Medical
Electronics
Composites
Oil Industry
Advantages of Superabrasives
The advantages of superabrasive grinding wheels are more than extraordinary hardness, unparalleled performance, and longevity. These three features of superabrasives are the core of many advantages manufacturers gain by an aggregation of services that normal abrasives simply cannot deliver.
Benefits include:
Less expensive tooling and fixturing costs
More wheels on the spindle, smaller wheels, multiple operations
Less floor space needed for manufacturing
Virtual elimination of wheel wear
Automated CNC machines, less labor intensive operations requiring less training
Consistent surface speed from part to part
Better overall throughput with fewer machines needed
Improved material removal rates, lower per part abrasive costs, and higher speeds
With superabrasives, industries have been able to increase production with automated CNC equipment, compensating for a lack of available, skilled labor. With custom superabrasives that are optimized for their process, machine capabilities, and mechanization, there is less reliance on operator technique. A properly defined process, combined with automatic loaders, make for equipment that can even run itself in some cases with lights out manufacturing.
Industry Outlook
Future growth of the abrasives industries will primarily be in superabrasives. Currently, research and development of superabrasives are taking place in the following areas:
Custom designed “hard to grind” materials in an increasing number of industries
Creep or deep feed grinding
High-speed, high-performance grinding of hardened steel
Form grinding, sometimes with electroplating, in high precision, high-removal, and high-surface quality applications
CNC-control of line grinding machines
Continental Diamond Tool stays on the forefront of new abrasive technology developments in superabrasives with our state-of-the-art grinding lab focused on research and development of new hybrid bonds that take the efficiencies of superabrasives even further.
How to select the right superabrasive
CDT has a strong group of engineers, product managers, and technical sales people who can come out to your facility to review your equipment and processes, and the parts you’re looking to grind. Or, as Troy Giacherio, Product Manager for Rotary Dressers, suggests, “you can come into our facility and we’d be more than happy to have the conversation, review the whole development process, and then make our recommendations based on what we’ve seen and communicated.” Contact us for a free quote.
Learn more about superabrasive grinding solutions in this video:
How to Order Custom Grinding Wheels
Check out this guide on how to order custom grinding wheels that are a perfect fit for your operations.
Professionals in certain manufacturing industries use grinding wheels as a normal part of their abrasive cutting, grinding, and machining processes. There are numerous types of grinding wheels, as well as assorted types of abrasive materials and grains. Having and using the right tool for the job is essential, especially for precision manufacturing. It is important to determine what you need before you place an order or get a quote.
TYPES OF GRINDING WHEELS
These are only a few examples of numerous types of grinding wheels and their uses:
Centerless and feed wheels for creating extremely close tolerances on metal cylindrical parts, such as those for aircraft, automotive, and tool manufacturing
Cylindrical wheels for angular, plunge, and reverse grinding
Diamond and hybrid wheels for grinding extremely hard materials, such as carbide tips or concrete
Dish cup wheels for cutter and jig grinding
Mounted point wheels for deburring and profiling work on hard materials
Straight wheels, most commonly used for centerless, cylindrical, and surface grinding on bench and pedestal grinders
Tapered wheels for grinding gear teeth and threaded applications
TYPES OF ABRASIVES
Depending on the job you need to do and the type of grinding wheel you use, the type of abrasive you need varies. Examples of abrasives include:
Conventional: Aluminum Oxide (corundum), Ceramic, and Silicon Carbide
Superabrasive: Natural Diamond, Synthetic or Man Made Diamond, and Cubic Boron Nitride
At Continental Diamond Tool, we produce custom superabrasive grinding solutions. We can help you replace your conventional grinding wheel with the right superabrasive alternative.
ORDER GRINDING WHEELS
While some companies have local suppliers for their grinding wheels and abrasives, it's often more convenient to request a quote online, especially when you are looking to order custom grinding solutions. Here are the steps to take to order a custom grinding wheel:
Step 1
Determine the abrasive specifications required for the job. The proper grinding wheel is dependent on many factors including the grinder, coolant, material being ground, wheel dressing method, and more. To give you the best engineered solution for your grinding application, your supplier will need certain information to ensure you get the results you are looking for. Details you'll want to gather include:
Type of material: carbide, ceramics, concrete or stone, glass, or metal.
Type of grinder: manual or CNC
Type of grinding application: OD, ID, Cylindrical, Surface, Rotary Surface, Angle Head, Double Disc, Plunge, Traverse, etc.
Wheel diameter: varying from 0.008” to 40”
Thickness range: varying from 0.030” to 12”
Arbor hole size: varying from 0.040” to 20 inches
Desired finish: extra fine, fine, medium, or coarse (for minimal to heavy removal).
Coolant type
Dressing method & tools
Stock removal: If you know your selected abrasive material and required grit (varying from 20 to 8000 mesh), note that too.
Step 2
Call or use the online contact order form for your online supplier. For a custom grinding wheel, provide lots of detail about the type of tool you are using, along with its description, dimensions, and intended use. Continental Diamond Tool has a quote request form that walks you through the information we need to provide an accurate quote, and you can upload reference files if needed. Or you can always call us if you want to talk through the parameters of your project.
Step 3
At Continental Diamond Tool, we specialize in custom superabrasive grinding wheels and tools. Our team of engineers will work with you on a custom solution to your grinding needs. Depending on the nature of your project, we can run remote simulations or in-person trials and test prototypes before manufacturing the final piece. The whole process typically takes a number of weeks, but can be fast tracked if needed. At the end, our engineers will work with your team to guarantee that the grinding wheel is properly installed and performing as expected. They can also offer instruction on how to maintain your grinding wheel for ongoing high performance.
Stop getting by with a grinding wheel that isn’t optimized for the job. It's best to consult an expert to make sure your tool is a good fit for your process. In many cases, custom grinding wheels quickly pay for themselves with increased efficiency and extended tool life, and you'll see the difference to your company’s bottom line. It starts with calling 800-443-6629 or requesting a free quote online today:
Is Continental Diamond Tool ISO 9001 Certified?
Continental Diamond Tool has implemented and maintains a Quality Management System that meets the requirements of ISO 9001:2015, as a manufacturer and distributor of Super Abrasive Grinding Products.
Quality Management
ISO 9001 Certification
Continental Diamond Tool Corporation in New Haven, Indiana, USA, underwent its most recent ISO audit in April 2024, conducted by IsoTec Alliance. A similar recertification audit at Continental Diamond Tool Limited in Kinmel Bay, Rhyl, U.K., was completed in February 2023 in collaboration with BM Trada. The comprehensive review covered all processes and documentation, with a particular emphasis on control plans, training records, and employee interviews across various departments. Following the rigorous four-day assessment, the auditor granted recertification for ISO 9001:2015, highlighting the company's steadfast commitment to maintaining superior quality management practices.
The ISO program mandates meticulous review of all processes, establishment of Standard Operating Procedures (SOPs), work instructions, and control plans, along with comprehensive training sessions for employees at all levels to ensure familiarity with ISO procedures. The Stage 1 audit, typically lasting one day, serves as an initial assessment by IsoTec Alliance to gauge readiness for Stage 2. Upon successful completion of Stage 1 with no issues detected, IsoTec recommends progression to Stage 2. Stage 2 entails a thorough four-day audit, during which auditors scrutinize all facets, including documentation and processes, to validate adherence to prescribed practices. This includes thorough examination of control plans, training records, and interviews with employees across various departments. Following the Stage 2 audit, a closing meeting is convened to assess the company's compliance, and if deemed satisfactory, certification for ISO 9001:2015 is granted. The official certificate is then issued to the company several days after the audit's conclusion.
Recertification audits are obligatory every three years to maintain ISO 9001:2015 status. These audits serve to ensure continued adherence to the stringent requirements outlined by the ISO program, underscoring the company's ongoing dedication to operational excellence and continual improvement.
Custom Rotary Diamond Dressers in as little as 4 weeks: How do we do it?
Industry-standard lead times for diamond rolls can take 8 weeks or more. If you are looking for a better, faster rotary diamond dresser alternative, we can expedite service in as little as 4 weeks. Learn how >
Since 1984, Consort Precision Diamond has supplied diamond wheel dressing products to a broad range of industries including aerospace, aircraft, automotive, blade and knife, power generation, medical, cutting tools, tool & die, saw, gear, and bearing and many other applications. What all these grinding operations have in common is that they typically require some form of wheel dressing to re-establish the wheel profile and/or recondition the wheel face.
About Wheel Dressing or Conditioning
Wheel conditioning involves the sharpening and opening of the wheel face, while also removing dull abrasives, excessive bond, and workpiece material (loading). A sharp and open wheel face will allow maximum possible material-removal rates and reduced thermal stress on the workpiece.
Consort’s rotary dressers provide the ideal profile for your desired wheel topography, with superior materials and manufacturing technology. Because your dresser is custom manufactured, demanding and complex configurations are possible.
Diamond Roll Delivery in as Little as 4 Weeks
The question then turns to delivery and lead times. In business, time is money. Industry-standard lead times for custom rotary diamond dressers can take 8 weeks or more. That’s a long time to wait for a critical part in your manufacturing process. Consort has made a reputation for fast delivery with a standard lead time of 6-8 weeks.
Need a tool in a hurry? Customers can request “Expedited Service” for custom diamond roll delivery in as little as 4 weeks. With manufacturing, delaying maintenance can really add to your costs in the long run. When a job is expedited, we work with our customers to get them their tooling as soon as possible.
We pride ourselves on prompt service and communication. At any time, you can reach out to your Consort account representative to begin an order or find out its status. If you do not have an account rep, please reach out to our customer service through our website online form or call 800-443-6629.
Lead times should not be a hurdle in the proper maintenance of your grinding equipment. If you are looking for a better, faster diamond roll supplier, let our service techs help you get the process started.
How Long Does it Take to Get a Custom Grinding Wheel?
In business, time is money. Industry-standard lead times for custom grinding wheels can take 8 weeks or more. If you are looking for a better, faster grinding wheel alternative, let our service techs help you get the process started.
Customized superabrasive grinding solutions have many advantages over conventional grinding wheels — primarily in performance. Custom CBN and Diamond grinding wheels improve efficiencies, last longer, and produce better quality results. Once you transition to a custom grinding wheel, the value of the investment becomes clear.
The question then turns to delivery and lead times. In business, time is money. Industry-standard lead times for custom grinding wheels can take 8 weeks or more. That’s a long time to wait for a critical part in your manufacturing process. CDT has made a reputation for fast delivery with a standard lead time of 4 weeks.
Need a tool in a hurry? Customers can request our Rush Program to expedite service for custom grinding wheel delivery in as little as 2 weeks. With manufacturing, every minute a machine is down, you feel the pinch. When a job is a rush, we work with our customers to get them up and running as soon as possible.
We pride ourselves on prompt service and communication. At any time, you can reach out to your CDT account representative to find out the status of your order, or email customer service at info@cdtusa.net. We send tracking numbers via email with your invoice when your order ships. You can also request tracking information through customer service at 800-443-6629 or through our website contact form.
Once you have placed an order with us, your wheel specifications will be held on file for quick processing and delivery of reorders through your account rep or our customer service department.
Lead times do not have to be a hurdle for transitioning to custom superabrasives. If you are looking for a better, faster grinding wheel alternative, let our service techs help you get the process started.
Where to Get Grinding Wheels in Stock, on Demand
At CDT, we cater to our customers needs. We keep precise records of every wheel we manufacture. If there is a wheel you regularly need in stock, let us know and we will make it available upon request.
At CDT, we are often asked if we stock grinding wheels. As a custom grinding wheel manufacturer, our wheels are designed to specific manufacturing processes. Universal (stock) grinding wheels rarely match the performance of our custom superabrasives in unique manufacturing settings.
That said, we can help you design a grinding wheel that maximizes performance, and make sure that wheel is available when you need it. Or if there is a stock wheel you know works great, we can have that on hand for you, too. When you find a grinding wheel manufacturer that understands your process, reorders are easy.
Choosing Your Grinding Wheel Manufacturer
CDT, like most manufacturers, lists the grit type, grit size, wheel hardness, structure, and bond using a code for every grinding wheel produced. However, there is no standard among manufacturers defining what these codes mean — the specification alone does not tell the whole story. This makes it difficult to take a grinding wheel from one manufacturer and substitute it for another grinding wheel of equal marking.
What if you are unhappy with your current grinding wheel source? Assuming you need your grinding wheel to perform exacting work and you want to limit your grief, we recommend you get guidance from an experienced grinding wheel specialist before making a substitution.
At CDT, we can interpret the codes on your grinding wheel and get a close approximation. Even so, you should expect some trial and error when converting from one brand of wheel to another. Dialing in the precise settings is a process, but it’s worth it to find a grinding wheel manufacturer who offers consistently competitive quality, delivery times, and price.
Ordering Replacement Grinding Wheels
Once you have your custom grinding wheel working efficiently, and you are happy with your manufacturer, you want to know you can get that grinding wheel on demand.
At CDT, we cater to our customers needs. We keep precise records of every wheel we manufacture. If there is a wheel you regularly need in stock, let us know and we will make it available upon request.
What Products Are Available?
CDT manufactures all the most popular superabrasive products on the market today: plated, resin bond, metal bond, and vitrified grinding wheels. Within our resin line, we have our GL Series that is comparable to a hybrid bond wheel and provides even more customizable performance options. Your best choice depends on your industry, material, process, and objectives.
In addition, we offer many types of dressers to keep your grinding wheels operating at peak performance — from diamond rotary to stationery varieties. We also have diamond lapping compounds, used in polishing materials to a mirror finish.
How to Match Your Resin Bond Grinding Wheels to the Workpiece
Superabrasive grinding have two equally important components. While the grit, (diamond or CBN,) does the work, it couldn't function without a partner holding it in place. In the case of resin bond grinding wheels, that partner is phenolic resin.
Superabrasive grinding wheels have two equally important components. While the grit, (diamond or CBN) does the work, it couldn't function without a partner holding it in place. In the case of resin bond grinding wheels, that partner is phenolic resin.
The hardness of the phenolic, along with grit size and concentration, determines wheel life, material removal rate, and final surface finish. CDT controls these three parameters precisely, allowing users to match a wheel to the particular workpiece material and type of grinding operation. However, selecting the best wheel depends on understanding the relationship between hardness, grit size and concentration and the wheel wear mechanism.
WHEEL WEAR MECHANISMS
As grit cuts through the workpiece material the edges become dull. Allied to that, chips from the cutting process erode the resin, releasing old grit and exposing fresh edges. The rate at which fresh grit is exposed is critical. Dull edges tend to rub against the workpiece, cutting forces go up and more heat is generated, perhaps burning the workpiece. Conversely, if grit is released early the grinding wheel is wearing faster than necessary, resulting in more frequent replacement.
HARDNESS
Hard workpiece materials, like ceramics and carbides, tend to dull cutting edges quickly, yet because the chips are small and brittle, resin wear is low. In this situation, to ensure a sufficient supply of fresh new cutting edges it's best to use a softer wheel.
Softer materials, like steels and high nickel alloys, (which should be ground with CBN rather than diamond,) produce longer, more ductile chips. These erode the resin faster which, in a soft wheel, results in excessive wear.
Manufacturers of resin bond grinding wheels adjust hardness by varying the mix of fillers in the phenolic resin. The resulting wheel hardness is expressed on a scale from A (softest) to Z (hardest) although superabrasive wheels are generally available just for the range from O through U. If a wheel outside of this range is thought necessary, consult with product specialists here at CDT.
CONCENTRATION
This refers to the proportion of superabrasive grit in the resin and is expressed on a scale of 25, 50, 75, and 100. The highest value indicates a weight to volume ratio of 72 carats per cubic inch, which works out to about 25% by volume.
A higher concentration means more cutting points, which results in faster material removal, but also increases wheel cost. Concentration also affects surface finish: a lower concentration would typically be used for finishing than for roughing.
GRIT SIZE
Larger abrasive particles remove more material on each pass, so coarser grits are used for rough machining and when grinding softer materials. Smaller particles lower cutting forces, so are used for harder materials as well as finishing operations.
MATCH THE WHEEL TO THE WORKPIECE
The choice of grinding wheel depends on the nature of the workpiece material and whether roughing or finishing. Harder materials generally should be ground with a softer wheel and small grit size. Softer materials are better ground with harder wheels and larger grit. Grit concentration should be chosen to suit the type of grinding operation – roughing or finishing.
If in any doubt as to the hardness of wheel to use, consult a grinding wheel specialist.
Common Fluting Mistakes — and How to Fix Them
While superabrasive grit does the grinding, the bond material is every bit as important. Learn how resin bond can produce superior surface finish.
Flute Polish or Flute Burnish?
There is an increasing need for high-quality carbide mills and drills with polished flute faces. Your customers are demanding a surface grinding tool that has a shiny flute, evacuates a metal chip better, and runs at faster speeds.
Sometimes your customer just wants your tool to look like the “other guy’s” tool. Unfortunately, a burnished flute face can be mistaken for true polish. Toolmakers have the challenge of making a cost-effective tool that has great performance and a great finish on the flute face.
Common Fluting Mistakes
Some toolmakers turn to hybrid wheels that grind the flute in no time, but these grinding wheels really don’t polish all that well.
To improve appearances and achieve a smooth finish, a lot of toolmakers use nonwoven products to polish after fluting. But do flute polishing cloths really polish, or do they just burnish the surface?
For a Quality Flute Polish
For a flute cleaning and polishing that really penetrates the surface, you have to remove some material to get through the grind lines leftover after flute grinding.
A resin bonded grinding wheel can give you a finish that is as good or better than nonwoven polishing products, but the resin bonded wheel also removes material from the flute face, taking out subsurface damage.
Resin bond is made by mixing abrasive grit with a phenolic resin. The resulting compound is molded to shape before being baked in an oven. This produces a grinding wheel that's tough, with the resilience to take impacts without shattering. By adding copper and other fillers to the resin base, grinding wheel manufacturers can tailor the properties of the finished grinding wheel to a wide variety of applications.
With resin bond, you can make a tool that not only looks just as good as the “other guy”, but also is actually better quality than the other guy. Resin-bonded superabrasive grinding wheels provide:
Shock-resistance
Excellent surface finish
Low maintenance
The Extra Effort Sets You Apart
The right wheel can help you polish up your act. CDT’s resin bond flute polishing wheel performs as good as it looks — producing a quality tool that shows. We offer resin bond polishing wheels to work in oil or emulsion on all CNC cutter grinders. These grinding wheels can run at high speeds and are available in grits as fine as 1200 or more based on finish requirements.
Grinding wheel manufacturers have years of experience and there are few fluting applications we haven't encountered. Our engineers can help you get the right grinding and polishing solution for your particular application.