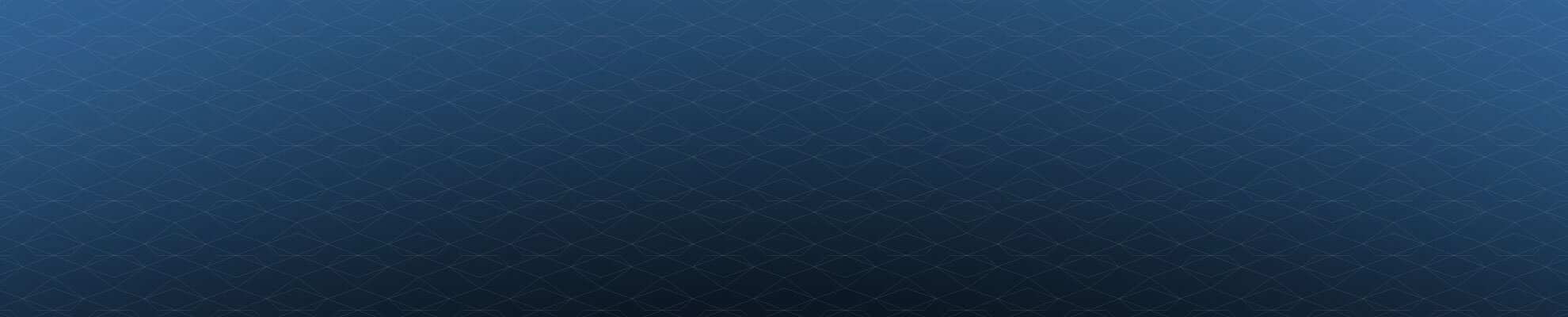
News and Resources
Browse by Category
Browse by Product
- All Dressing Products
- All Grinding Products
- CBN-Diamond Superabrasives
- Conventional Abrasives
- Diamond Lapping Compounds
- Diamond Rotary Dressers
- Diamond Stationary Dressers
- Hybrid Bond Grinding Tools
- Metal Bond Grinding Tools
- Plated Grinding Tools
- Resin Bond Grinding Tools
- Vitrified Bond Grinding Tools
6 Common Grinding Problems and How to Solve Them
Are you experiencing these 6 common grinding problems? If so, your grinding wheel may be at fault. Learn more >
Most grinding problems affect one of two categories: either appearance of the workpiece or productivity and return on investment. After verifying that the grinding machine isn’t at fault, there is one likely culprit causing your grinding problems: your grinding wheel.
Poor surface finish, chatter, and burning all affect the appearance of your product. Productivity issues like short wheel life, slow or inefficient cutting, or the wheel not cutting at all are also costly problems to have.
Let’s take these one at a time to see how a fix to your grinding wheel can solve some of your most challenging grinding issues.
1) Poor surface finish
Why your grinding wheel may be at fault:
In the appearance category, poor finish is a common complaint when your grinding wheel isn’t optimized. Grinding is a multi-point cutting process, but broken down to the microscopic level, it has similarities to a single point operation like turning. Viewed this way, it’s easy to see how surface finish is affected by the same factors: the more material removed by each grinding point, the bigger the individual chips and the rougher the surface.
Solutions:
Select a grinding wheel with a finer grit size
Reduce the relative speed between the wheel and workpiece
Other possibilities:
If grinding wet, the coolant may not be efficiently removing chips from the workpiece or wheel interface.
It's also possible that the wheel is being dressed excessively, creating grinding points that are standing too proud of the wheel surface.
2) Chatter
Why your grinding wheel may be at fault:
Recognizable by a distinct, often audible, pattern on the workpiece, chatter has many causes. Wheel-induced chatter occurs when an out-of-true grinding wheel acts as an excitation source.
Solutions:
In this case the wheel should be trued carefully.
Also check that it isn’t slipping on its mount.
Other possibilities:
If the problem is tracked down to a vibration in the machine — possibly some kind of resonance — the solution is to vary the grinding speed. Try going 10% faster or slower to remove the forcing excitation.
A detailed discussion of chatter is available at the Abrasive Engineering Society website.
3) Burning
Why your grinding wheel may be at fault:
Machinists use the term “burning” to describe thermal damage. It can show up as cosmetic discoloration, changes in workpiece hardness, and possibly distortion-inducing internal tensile stresses. Burning can occur if the wheel is glazed or loaded, causing more rubbing and friction. This often occurs if the machinist is trying to push the wheel through the workpiece too quickly or using a wheel that’s too durable.
Solutions:
Dress the wheel with the correct dressing tool
Reduce the feed rate or the relative velocity between wheel and workpiece.
Other possibilities:
Burning is far more common when grinding dry, although can still be experienced in wet grinding if there isn't enough coolant flow to carry away the heat.
See “Burn Awareness”, originally published in Cutting Tool Engineering, December 2000, for more information.
4) Wheel life too short
Why your grinding wheel may be at fault:
This costly issue can be caused by a wheel that's either too hard or too soft for the workpiece. When this is the case, the grinding wheel loads up or wears away too quickly.
Solutions:
Try a grinding wheel manufactured with a different material that is better suited for your grinding operation.
Other possibilities:
Insufficient coolant
Dressing your grinding wheel too frequently
Wheel speed too low
5) Wheel cutting slowly
Why your grinding wheel may be at fault:
This productivity issue is usually caused by feeds and/or wheel speeds that are too low. If you are using the wrong type of grinding wheel, you may be forced to cut slowly to avoid burning, but ultimately that’s not efficient for your process.
Solution:
The solution is to find a wheel that can grind as fast as possible without burning. A grinding wheel specialists can suggest alternatives that will increase speed for your specific operation.
6) Wheel not cutting at all
Why your grinding wheel may be at fault:
Most likely, this happen when the grinding wheel is glazed by truing.
Solution:
The solution is to dress the wheel lightly until the grit opens up. For dressing advice, consult with a grinding specialist.
OUR BEST ADVICE: THINK LOGICALLY
Most grinding problems can be solved by tracing the fault back to basic principles. With all grinding applications, imagine your material being removed by individual cutting points. Thinking from this perspective, a solution usually emerges.
Also, use your resources. The grinding experts at CDT are happy to discuss your cutting and grinding issues and offer solutions that will set your manufacturing operations on track to success.
Tips To Solving Wheel-Related Grinding Problems
When there are problems with a ground surface finish, when productivity is low, or if costs are too high, the fault may lie with the grinding wheel. Changing the grit, wheel feeds and speeds, or coolant application may be the solution, depending on the precise nature of the problem.
Grinding problems show up in two ways: in the appearance of the workpiece and as cost or productivity issues. After verifying that the grinding machine isn’t at fault, attention should turn to the grinding wheel.
Appearance problems divide into poor surface finish, chatter, and burning. Cost and productivity issues are short wheel life, slow cutting, and the wheel not cutting.
APPEARANCE ISSUES
Poor finish
Grinding is a multi-point cutting process, but down at the microscopic level it’s little different to a single point operation like turning. Viewed this way, it’s easy to see how surface finish is affected by the same factors: the more material removed by each grinding point, bigger the individual chips and the rougher the surface.
The solutions are:
Select a finer grit size
Reduce the relative speed of wheel and workpiece
If grinding wet, it might also be that the coolant is not removing chips from the workpiece/wheel interface. It's also possible that the wheel is being dressed excessively, creating grinding points standing too proud of the wheel surface.
Chatter
Recognizable by a distinct pattern on the workpiece, and often audible, chatter has many causes. If initiated by a vibration in the machine – possibly some kind of resonance – the solution is to vary the grinding speed. Try going 10% faster or slower to remove the forcing excitation.
Wheel-induced chatter occurs when an out-of-true grinding wheel acts as an excitation source. In this case the wheel should be trued carefully. Also check it isn’t slipping on its mount. A detailed discussion of chatter is available at the Abrasive Engineering Society website.
Burning
Machinists use this term to mean thermal damage. It can range from cosmetic discoloration to changes in workpiece hardness and possibly the creation of distortion-inducing internal tensile stresses. Burning is far more common when grinding dry, although can still be experienced in wet grinding if there isn't enough coolant flow to carry away the heat. “Burn Awareness”, originally published in Cutting Tool Engineering, December 2000, provides more information.
Burning can occur if the wheel is glazed or loaded, so there is more rubbing and hence more friction, by trying to push the wheel through the workpiece too quickly, or by using a wheel that’s too durable.
Solutions are:
Dress the wheel with a dressing stick
Reduce the feed rate or the relative velocity between wheel and workpiece.
COST AND PRODUCTIVITY ISSUES
Wheel life too short
This can be caused by:
Insufficient coolant
Dressing too often
A wheel that's either too hard or too soft for the workpiece (so it loads up or wears away too quickly)
Wheel speed too low
Slow cutting
Usually caused by feeds and/or wheel speeds that are too low, the solution is to grind as fast as possible without burning.
Wheel not cutting
This happens when the wheel is glazed by truing. The solution is to dress the wheel lightly until the grit opens up.
THINK LOGICALLY
Most grinding problems can be solved by relating the fault back to basic principles. Picture material being removed by individual cutting points and a solution usually emerges.
Care and Maintenance of Diamond Wheels
A few simple steps to care for and maintain your diamond wheels will allow you to get the performance and durability you expect from them.
Diamond wheels provide the maximum performance and high-speed cutting on demanding materials. Proper care and maintenance will ensure that the wheel gives the superior results for the maximum time. The steps are not difficult and well worth the effort.
Installation
Make sure that spindles, back plates and flanges are always clean before installing a new wheel. Use a dial indicator to check that the rotation of the wheel is within 0.0005 inch, 12.7 microns, of true. Tighten the flanges once the wheel is true and double-check tightness before use.
Diamond cutting wheels should only be used to make straight cuts. Twisting or jamming the wheel can cause fatigue and segment loss. Excess pressure should not be applied when making cuts.
When performing any cutting or grinding process, all work materials require firm support. Excess overhang should be avoided; even slight tilting can create an angled cut.
Feed and grinding speed
Material must be fed into the wheel at the appropriate speed. A feed rate that is too fast will cause chatter and vibration. This will result in a poor cut and possibly damage the cutting edge of the wheel.
Diamond wheels work best at speeds between 5,000 to 6,000 surface feet per minute. Running at lower speeds can lead to glazing.
Dressing
Using the wrong cutting wheel, one with a bond that is too hard for the working material, will create glazing. The easiest way to avoid this is using a blade that is matched to the material. Dressing the blade is a maintenance technique, but dressing does slow down production and reduce the life of the wheel.
Dressing a diamond wheel cleans the build up of debris from cutting operations that block the abrasive surface. The resurfacing restores the sharp abrasive edges of the diamond coating. A dressing stick, normally aluminum oxide or silicone carbide, is used to cut through or remove the debris and expose new diamond material.
Make an arrow mark on the wheel showing the rotation direction the first time and always dress the wheel with it spinning in the same direction. Dressing a wheel in both directions will destroy it.
Dressing is accomplished by simply making a straight cut through the dressing stick or bar. Cut off a thin section per pass. Only one or two cuts through the stick should be required.
If a dressing stick is not available, a section of asphalt can be used. Make a few cuts into the asphalt and the blade should be clean.
Overheating
Coolant should be used for maximum results. The coolant needs to spray to contact where the cutting wheel and material meet. A weak soluble oil solution may be used to reduce corrosion.
If dark streaks form along the sides of the cutting edge, the wheel is being overheated. Excess heat can cause the wheel to break apart. If dry cutting is being performed, allow the wheel to cool for about 10 seconds for every 30 seconds of cutting operation.
Use the right grade wheel, designed for the material to prevent injuries from reactive force or throw back. Never use a wheel that shows signs of fracture, fatigue or broken segments.
A Concise Guide to Single Point Diamond Dressers
Learn about diamond classifications and 10 tips for using single point diamond dressers.
Problematic grinding performance typically arises as a consequence of improper dressing. Choosing the correct diamond quality classifications greatly improves the expected quality of finished products. Moreover, the number of settable points will contribute heavily to acceptable dressing standards.
Classifications of Diamond Qualities
Grade A quality diamonds provide four+ settable points--smooth-surfaced octahedron or dodecahedron.
Grade B quality diamonds provides three+ settable points--possibility of inclusions, although they do not disturb the diamond's integrity.
Grade C quality--two+ settable points exhibiting blockish structure with superficial irregularities. This grade is the most common grade used in tool rooms.
Grade D quality--less than two settable points. Grade D's may have defects around less defined points.
Grade E quality--one settable point, "utility" grade diamond typically presenting cracks and other flaws.
Grade U quality--one settable point, "utility" grade cube-shaped diamond with an opaque surface
10 Tips For Using Single Point Diamond Dressers
1. Extend the life of a single point diamond dresser by inclining the tool at a 10 to 15 degree angle to the wheel radius. Point the tool in the rotation direction of the grinding wheel to maintain a consistently sharp point.
2. When dressing with Polycrystalline (PCD), grit, diamond single points or arbitrary stone tools, the infeed has to be .001 since a diamond dressing tool inevitably pulverizes the vitrified bond. Anything higher than .001 will cause cracking into the wheel--as much as .009 deep--that forces the bond to degenerate. In addition, gullets develop that produce loading by catching chips and overheating the wheel. Consequences of excessive infeed are chatter, bounce, bad finish and burn.
3. Sharply-tipped, crystal octahedrons should be utilized for straight dressings. For 46 grit and 60 grit wheels, crystal octahedrons shaped in a gothic style work well. Points associated with crystal octahedrons stay sharp if you turn the tool six to 12 indexes every revolution, or as necessary.
4. Make sure to use enough coolant to moderate dressing temperature, otherwise overheating occurs which may chemically transforms diamond into graphite. Diamonds will also suffer cracking if subjected to large temperature gradients.
5. The objective of dressing is to generate and expose novel, superficial cutting edges on the wheel. Single point diamond dressers achieve this objective by shattering existing gravelly grains and facilitating the emergence of desired abrasive particles. Dressing increases in-feed as well as feed and must be performed regularly to maintain optimal grain protrusion and grain edge sharpness.
6. Always begin dressing at the center of the wheel, which is the biggest diameter. Starting a dressing procedure at a wheel's side will probably result in shattering or even destroying the highest quality diamonds.
7. To prevent wheel taper, place the single point diamond dress as close as possible to the grinding area.
8. Grinding wheel grain sizes are contingent on longitudinal feeds, which significantly influences the structure of the surface of a grinding wheel. Additionally, reduced feed rates will predictably provide finer, more desirable surfaces.
9. Rotate the dresser 20 to 40 degrees in the shank if a flat appears on the diamond so that the dresser maintains an optimally conical point.
10. Avoid letting the diamond erode until the shank is visible. Doing so could allow the stone to dislodge or fall out.
The Importance of Maintaining your Grinding Wheels
Learn how to use dressing tools effectively so your grinding wheels will have a long and productive life span.
To understand how important it is to dress grinding wheels, you must first understand just how grinding wheels work. A grinding wheel is an abrasive cutting tool. It rotates quickly while in use and is very similar to a saw. However, a saw blade is only sharp along the edge. A grinding wheel has small sharp grains distributed over the surface of the wheel. Dressing grinding wheels is important maintenance.
When you press another material to the grinding wheel, its surface is gradually worn away. The results range from subtle to dramatic depending on the wheel and its intended use. Grinding wheels come in different materials. The surface material of the grinding wheel will decide what items it will work on. For example, aluminum oxide wheels work well on many steels, wrought iron, annealed malleable iron, and bronzes. Silicon carbide works well on rubber and stone.
Grinding wheels come in various shapes, including cup, dish, and cylinder shapes. The shape of the wheel typically changes over time with use. When you notice that the wheel's shape is different from that initially displayed, it’s time to discuss the matter of dressing grinding wheels. You have options available to you such as diamond dressers for grinding wheels and aluminum oxide dressing sticks. Each has its own distinctive features.
Grinding wheel dresser diamond tools are an extremely hard and efficient option. Diamonds are best known for their sparkle and elegance, but they also have a durable quality that makes them ideal for dressing tools. The hard diamonds score and reshape most dressing wheels very quickly and efficiently. A diamond dresser for grinding wheels will work with nearly any material. Choose the dresser design that’s best for your desired finish and get to work returning your grinding wheel to its former glory.
Aluminum oxide dressing sticks are a good option as well. Aluminum oxide is often used to dress tools made from diamond. The diamonds are easily sharpened with aluminum oxide. If the tool you’re working with is itself diamond, opt for this type of dressing stick to keep it maintained.
Dressers come in many shapes so you can restore any type of grinding wheel easily. A chisel dresser creates a fine contour. Plunge dressers are best for a concave radius. Grit dressers have broad even faces for fast dressing on a large surface. There’s a tool for any grinding wheel so you can always keep your surfaces in top shape. Plan to use your dressing tools often and your grinding wheels will have a long life span.
Do Your Grinding Wheels Need A Tune Up?
It's a fact that grinding wheels will endure wear and tear over time. Because of this, they require regular maintenance to keep them working like new, so grinding wheel dressers and dressing sticks become integral parts of the process.
t’s a fact that grinding wheels will endure wear and tear over time. Because of this, they require regular maintenance to keep them working like new, so grinding wheel dressers and dressing sticks become integral parts of the process.
Grinding wheel dressers are also known as grinding dressers or wheel dressers. Diamond dressers offer many benefits, some of which include a decreased dressing cost per piece, a constant high-precision operation, optimal dresser versatility, and fast dressing of even the most complex wheel profiles. Since different designs and applications call for different dressing tools, it’s important to work with a supplier that can help you determine which type will work best for your needs. Four of the basic types most commonly used with CNC grinders include stationary dressers, crush rolls, diamond crush rolls, and rotary dressers, all of which are used for grinding more complex shapes.
Aside from the grinding dresser itself, you may also need dressing sticks. These are stick-shapes made from a hard material, generally the same material as a dresser, but they use a stronger bonding agent. This gives them a harder composition than the grinding wheel. Properly selected grinding sticks can not only be used for dressing and truing conventional vitrified abrasive wheels, but they can improve the performance of CBN and diamond grinding wheels as well.
Fine particles will be flying off of the wheel during truing or dressing and it’s important to note that, when working with grinding sticks or any superabrasive tools, you should wear safety glasses in order to avoid eye injury. Remember to always store grinding wheel dressers and other metal tools in a dry location to avoid rust. Maintain a clean work area to cut down on the likelihood of injury and check for damaged parts before using any grinding wheel, dresser, or dressing stick.
Whether you use a CBN or diamond grinding wheel or other cutting products, having the right tools for the job is of the utmost importance. A company like Continental Diamond Tool can provide quality tools and custom manufacturing to suit your specific needs, with precision products and outstanding customer service without rival. Order products tailor-made to your project’s needs, produced by skilled technicians who can supply a finished product in as little as a week. Enjoy stellar customer service that will ensure, from start to finish, that you are getting the right product for your needs.
Your Tools Are Only As Good As Your Dresser
The proper grinding wheel dressing stone is essential for an efficient wheel. Assess your needs and stock up on quality dressing tools.
Your tools are only as good as the care you give them. A brand new product will work wonderfully at first, but nearly anything with a sharp point or fine edge will wear down over time. You’re probably familiar with grinding wheels for sharpening tools, but do you know how to choose and use the tools that keep your grinding wheel in working condition? The proper grinding wheel dressing stone is essential for an efficient wheel. When you’re choosing a dressing tool for grinding wheels, it’s important to understand all your options. A grinding wheel dresser diamond tool is the strongest choice. Other materials like silicon carbide or aluminum oxide are adequate for some wheels, but diamond consistently provides the best performance.
Dressing stones for grinding wheels are available in many different shapes. Choose from a single point diamond dresser with layered clusters, blade-type dressers with hand set diamonds, and grit dressers with uniform distribution of diamonds. Each dresser will give you a distinct finish. As you apply the grinding wheel dressing stick to the surface of your wheel, you’ll remove the top layer of the wheel and reveal a clean, sharp surface for future projects.
Dressing sticks aren't used exclusively on grinding wheels. The right dressing stick is important for maintaining other sharp tools as well. Diamond core drills feature a diamond tip that’s powerful enough to drill through nearly any material. The drill bit itself requires regular care to stay sharp and effective. Though the strength and capabilities of diamonds are certainly impressive, they don’t make diamonds infallible. You must regularly dress diamond core drills with an aluminum oxide dressing stick to keep them in top shape.
With a quality dressing stick, you can keep all your important tools sharp and well-maintained. Get to know every surface in your shop so you can instantly recognize when one is becoming dull and dirty. Grinding wheels can lose their efficiency quickly. You should always have a dressing tool for grinding wheels on hand to sharpen your tools. If you’re not equipped with a good diamond dressing stick, you’ll lose time allotted to active production while you wait for the proper items to arrive.
Assess your needs and stock up on quality dressing tools for every metal grinding wheel, drill, and surface that you use regularly. Dress your tools as often as you need to to keep them in top condition and functioning like new.
Which Dressing Tool is Right for You?
Use our dressing tools to ensure that your diamond grinding wheel will perform at maximum efficiency, trouble-free, and enjoy a long, sustainable life.
A diamond grinding wheel dresser is a vital tool in the proper care and maintenance of any grinding wheel. Regular maintenance ensures that your diamond grinding wheel will perform at maximum efficiency, trouble-free, and enjoy a long, sustainable life.
When selecting any dressing tool, including a diamond wheel dressing stick, it’s important to choose the tool that is the proper shape, size, and quality for the grinding wheel. If you don’t know which tool will work best with your application, discuss it with a supplier’s knowledgeable customer service department to determine exactly what you need.
Dressing the wheel will knock off any abrasive particles from the wheel’s surface. This ensures that it’s balanced and concentric, which minimizes any vibration it may get from having too much buildup on the surface. These particles, if left on the surface, have the potential to cover up surface abrasives, making them dull and ineffective. Exposing them by removing particles is essentially a sharpening process, since the fresh abrasive grains are each cutting tools in their own right.
A diamond grinding wheel dresser serves another important function, and that is to clean the grinding wheel. Choosing a dresser or grinding wheel dressing stick that is softer than the grinding wheel will not dislodge any abrasive particles, and can result in a loaded wheel. This is why selecting the proper dressing tools is crucial to a successful grinding wheel dressing.
There are also different types of dressers to consider. Star dressers feature long handles and serrated discs. Diamond dressers are generally preferred because of their superior strength. They also have shorter handles and are great for both dressing and truing. They are also available in single point and multi-set clusters to blade-specific type, and a reputable supplier will be able to determine which design to use based on your project. For example, a single point tool is easy to use and encourages a more pronounced rotation and higher frequency, delivering precise results.
Other benefits of a diamond grinding wheel dresser include a fast dressing of even the most complex wheels, a constant operation that boasts high-precision, and optimal dresser versatility. This type of dresser tool also means a decreased dressing cost per project, making it a cost-effective solution to all of your dressing needs.