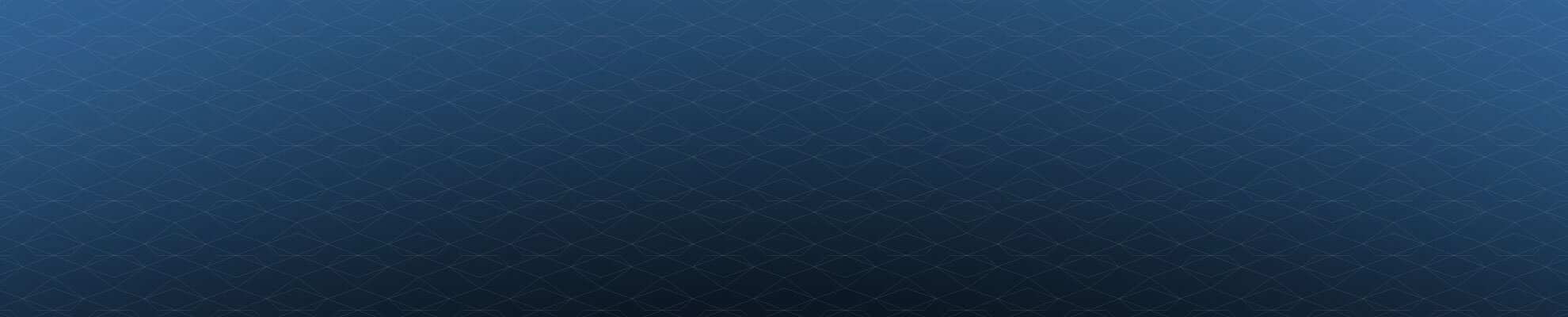
News and Resources
Browse by Category
Browse by Product
- All Dressing Products
- All Grinding Products
- CBN-Diamond Superabrasives
- Conventional Abrasives
- Diamond Lapping Compounds
- Diamond Rotary Dressers
- Diamond Stationary Dressers
- Hybrid Bond Grinding Tools
- Metal Bond Grinding Tools
- Plated Grinding Tools
- Resin Bond Grinding Tools
- Vitrified Bond Grinding Tools
Celebrating Our Apprentices
Apprenticeships at CDT offer hands-on experience, critical skills, and leadership opportunities—more than training, they’re a launchpad for a lifelong career.
CDT Ltd.'s current and former interns (left to right): Corey Lloyd-Jones, Joe Bowles, Stephanie Hughes-Jones, Daniel Hughes-Jones, and Rhys Butler.
Investing in the Future: Celebrating Our Apprentices for National Apprenticeship Week
At Continental Diamond Tool (CDT), we take great pride in nurturing the next generation of engineers through our apprenticeship programs. In celebration of National Apprenticeship Week in the U.K., we’re highlighting the inspiring journeys of five apprentices at our manufacturing center in Wales. Read on to see how these talented individuals have developed their skills, grown within the company, and are shaping the future of engineering.e.”
From Apprentice to Supervisor – Joe Bowles’ Journey
Joe Bowles began his career with Continental Diamond Tool Ltd. in September 2007 as an engineering apprentice. Over the years, his dedication and willingness to learn saw him progress into new roles, gaining invaluable experience along the way. Today, he is the Supervisor of the Grinding Department, where he leads a skilled team and ensures high standards of quality and precision.
Reflecting on his journey, Joe shares:
"From an apprentice 17 years ago to a supervisor, my path has been driven by hard work and the support of a company that values growth, innovation, and investment in people. I look forward to furthering my career with CDT and being part of its bright future."
Joe’s success is a testament to the long-term benefits of apprenticeships, illustrating how they can open doors to leadership and career progression.
Daniel Hughes-Jones – A Key Player in CNC Machining
Daniel joined CDT Ltd. in March 2021, quickly making an impact in the CNC Machining Department. He successfully completed his HNC in Engineering, further strengthening his knowledge and technical expertise. Now, as a key team member, he operates multiple CNC machines and plays an important role in training new apprentices.
"My apprenticeship at CDT provided me with vital knowledge and a developed skill set, and I’m grateful to pass on my knowledge and experiences to the next generation of apprentices." – Daniel Hughes-Jones
Daniel’s ability to mentor new apprentices showcases the value of experienced employees sharing their knowledge, ensuring a strong and skilled workforce for the future.
Corey Lloyd Jones – Building a Strong Foundation
Corey started his apprenticeship with CDT Ltd. in September 2023 and is currently in his second year, working towards his HNC in General Engineering while also completing a Level 3 NVQ. With a strong ambition to learn, Corey is eager to develop his expertise across multiple machines and broaden his engineering knowledge.
"After finishing my apprenticeship, I would like to progress further within the company and learn more skills on more machines. I chose this career path as it looked like a good challenge. I am doing the general engineering HNC course because it opens up a lot of opportunities for me in the future, rather than having just mechanical or electrical HNC." – Corey Lloyd Jones
Corey’s enthusiasm for engineering showcases how apprenticeships provide a solid foundation for career growth, allowing young professionals to tailor their learning to suit their ambitions.
Rhys Butler & Stephanie Hughes-Jones – The Next Generation of Engineers
Rhys Butler and Stephanie Hughes-Jones, Daniel’s younger sister, are the newest members of CDT Ltd.’s apprenticeship program, having joined in September 2024. Though early in their careers, both are already embracing the challenges and opportunities that come with learning on the job.
Rhys shares his thoughts on his apprenticeship so far:
"I've been on my apprenticeship for around seven months now, and I've thoroughly enjoyed it because it has provided hands-on experience, and a deeper understanding of how complex systems come together. The opportunity to apply theoretical knowledge in real-world settings has been both challenging and rewarding. I've gained valuable skills in problem-solving, teamwork, and technical expertise, which have made me more confident in my abilities. Looking ahead, I would love to further develop my expertise in engineering and continue to grow in a role where I can contribute to impactful projects." – Rhys Butler
Stephanie, who was drawn to engineering for its balance of hands-on work and intellectual challenge, shares her experience:
"I chose engineering because I like jobs that are both physically challenging and mentally interesting. My apprenticeship helps me improve my skills as a machinist while giving me chances to keep learning and growing." – Stephanie Hughes-Jones
Their journeys emphasize how apprenticeships provide real-world experience, technical expertise, and career-building opportunities from day one.
Apprenticeships are more than just training—they’re a launchpad for a successful career. They provide a solid foundation for career progression, hands-on experience, and the opportunity to develop vital skills in a fast-paced, innovative environment.
The apprentices above are prime examples of what can be achieved through dedication, hard work, and the right support. From those just starting out to those who have grown into leadership roles, their journeys highlight the value of apprenticeships and the opportunities they create.
👉 Interested in an apprenticeship or know someone who is? CDT Ltd. works closely with Coleg Llandrillo to identify promising candidates for our highly competitive engineering apprenticeship programme. Each year, we offer placements to 2 to 3 students. The next apprenticeships will begin in September 2025. If you’re interested, we encourage you to explore Coleg Llandrillo’s Engineering Programme as the best route to be considered for a future opportunity with us. Learn more about Coleg Llandrillo here: https://www.gllm.ac.uk/
Continental Diamond Tool Limited (CDT Ltd.), based in Kinmel Bay, Rhyl, U.K., is the European subsidiary of Continental Diamond Tool Corporation, headquartered in New Haven, Indiana, U.S.A. For more than 40 years, CDT Ltd. has been a leader in diamond rotary dresser technology, originally operating as Consort Precision Diamond. Since joining CDT, the company has expanded its product line, delivering high-performance diamond plated grinding wheels and other premium superabrasive products to customers worldwide.
Global Growth and Local Jobs Spurred by Cutting Edge Investments at Kinmel Bay Facility
Cllr Nigel Smith visited CDT Ltd. earlier this month to see how £100,000 from the UK Shared Prosperity Fund is driving innovation, growth, and 40 new jobs in North Wales.
Cllr Nigel Smith (left), Conwy Council’s Cabinet Member for Sustainable Economy, visits with Production Manager Justin Hughes (right), showcasing one of the precision-engineered tools made possible by our new cutting-edge equipment, funded in part by the UK Shared Prosperity Fund secured with the help of Conwy Council.
A precision engineering company in North Wales is gearing up for global growth by investing £250,000 in cutting edge equipment.
Recruitment is also underway at Continental Diamond Tool (CDT) in Kinmel Bay as part of an ambitious expansion plan that will create 40 new jobs.
It’s all preparation for a move next year to a 30,000 sq ft factory nearby that’s three times the size of the current premises on the Tir Llwyd Industrial Estate.
Overall, the firm’s Indiana-based American owners, who took it over six years ago, are pumping £4 million into the company to triple production capacity and start making new products.
The niche company specialises in the manufacture of diamond-encrusted rotary dressers and grinding wheels, with tolerances of down to 1,000th of a millimetre in terms of accuracy.
It’s one of only two similar outfits in the UK and supplies a range of manufacturing sectors, including aerospace, automotive, medical and semi-conductors.
The company’s customers include blue chip corporations like Rolls Royce and Tenneco, with more than 60 per cent of the products being exported.
According to the loyal workforce, the investment is the “perfect present” for the company that’s celebrating its 40th anniversary this year.
It was also music to the ears of Cllr Nigel Smith, Conwy Council’s cabinet member for Sustainable Economy, who is one of three councillors who represent Kinmel Bay on the authority.
The council helped CDT secure £100,000 in funding from the UK Shared Prosperity Fund towards the cost of the new equipment.
He came on a visit to see how the money had been spent on “space age kit”, including a high tech machinery centre, lathe and inspection equipment.
Cllr Smith said: “What they do is very impressive, both in terms of the state-of-the-art technology and the high skill employment they provide in Kinmel Bay.
“It’s fantastic that they’re selling their world-leading products to an international market and they have a raft of blue chip customers like Rolls Royce.
“Over the years there has been a good relationship between the company and the council’s business development team and long may that continue.
“We were delighted to be able to help in securing £100,000 towards the cost of these cutting edge machines.
“It’s impressive, top-of-the-range technology and the level of precision they work to is mind-boggling – their tolerances are within microns. It’s engineering of the highest pinnacle.
“With them moving now to larger premises, I’ll be speaking to our team if there is anything more we can do to help them moving forward to help them grow and expand.
“Employment is a key issue in Conwy so have foster and support business where we can to retain our young people.
“It’s good to see the emphasis on training here and the apprenticeships, helped by the fact that they have a very good relationship with the local college.
“It’s always been a great company and there is now a new momentum under the American ownership and it’s very pleasing to see them invest in Kinmel Bay and that will pay dividends.
“The excellent legacy of the original company is now being turbo-charged by the Americans.
“It’s a company with ambition and it’s plain to see how committed the team are here – everybody has a good work ethic and it bodes very well for the future.”
Cllr Smith’s visit was hosted by Production Manager Justin Hughes, whose father was one of the founders of the original company, Peter Hughes.
Justin said: “In this latest investment we have spent £250,000 on the three machines and it’s well in excess of £1 million just on new equipment in the last two or three years.
“We’re very grateful to Conwy Council for their help in facilitating the £100,000 that’s come from the UK Shared Prosperity fund. It’s made a massive difference because it enables us to employ the people to use those machines.
“The skill required by the people we have to do that is of the highest order and is just as important as the machine.
“Training and developing those people is just as key as our processes and our high precision machinery so working with the engineering centre at the local college is a big help.
“I am immensely proud of the company’s legacy and the way things are moving forward. It’s in my blood, this company.
“These are really exciting times with the move to the larger premises which will enable us to have new product lines.
“Continental Diamond Tool are the third biggest superabrasives supplier in the USA and they are looking to become the biggest.
“The American side of the business is growing at a rate of 30 per cent a year and we are the European arm and they are looking to us to emulate that success over here.
“We are developing a name for ourselves against the big multi-national household names and we are becoming one of those names.
Finance Manager Michaela Lawton added: “The expansion into the new premises will enable us to increase capacity and the number of products we make so the sky is the limit.
“All this is happening in the year we are celebrating our 40th anniversary and the American side of the company is celebrating its 50th.
“We’ve got a great team of people here and there’s a shared pride in what we’re achieving.
“The expansion will create another 40 jobs and we have started to recruit people because of the skill sets required and the time it takes to train them.
“We’ve had a steady number of new employees joining us, particularly over the last four or five months so we can get all our ducks in a row.
“We make our products to 1,000th of a millimetre in terms of accuracy so we have to conduct the whole operation with the same level of exceptional quality.”
CDT Ltd. Unveils £4m Expansion Creating 40 New Jobs
Continental Diamond Tool has announced a £4 million expansion plan at its North Wales operation that will double the workforce there by creating 40 new jobs and triple production.
From left: CDT Ltd. Managing Director Jeff Wirth, Finance Manager Michaela Lawton, General Manager Troy Giacherio, Production Manager Justin Hughes, President of Sales Shane Vardaman, and Director Nick Viggiano stand outside the 30,000 sq. ft. factory that the North Wales operation will soon be occupying.
A fast-growing precision engineering firm has announced a £4 million expansion plan that will double the workforce at its North Wales operation by creating 40 new jobs and triple production.
The investment by the American owners of Continental Diamond Tool (CDT) will include moving to a 30,000 sq ft factory that’s nearly three times the size of its current premises in Kinmel Bay and is less than half a mile away on the Tir Llwyd Industrial Estate.
The move is being hailed by staff as the “perfect birthday present” for the North Wales operation which is celebrating its 40th anniversary this year, having been founded as Consort Precision Diamond in 1984, specialising in the manufacture of diamond-encrusted rotary dressers and grinding wheels.
The niche outfit – still one of only two similar companies in the UK – supplies a range of manufacturing sectors, including aerospace, automotive, medical and semi-conductors.
Its products are used in Boeing 777 and 787 Dreamliner aircraft, as well as the Airbus range A330-A380 whose wings are made at the giant Airbus factory in Broughton in Flintshire.
The firm was taken over and rebranded in 2018 by CDT which has its headquarters in New Haven, Indiana.
News of the investment was delivered by company President Nick Viggiano, during his visit to the Kinmel Bay site, along with Shane Vardaman, CDT’s President of Sales.
The bigger factory will enable the company to increase the range of products they make, adding several new types of high precision grinding wheels.
Nick Viggiano said: “Things have worked out even better than I thought and the investment is a real big vote of confidence in the workforce here because they have a similar work ethic and there’s good camaraderie between everyone.
“We expect to be three times the size we are in a few years’ time because there is a very big market for the products we are going to bring over here.
“We expect a swift ramp-up. Given our extensive expertise with these products in the States, we can help the team over here to quickly hit the ground running.
“The new building is like a blank canvas so we can set everything up exactly the way we want, so we’re very excited about it.”
It was as sentiment endorsed by the American Managing Director, Jeff Wirth, who said: “This investment has been a long time coming, with six years of preparation and teambuilding leading up to this moment.
“Our Kinmel Bay team, known for their rotary dressers, has already started producing electro-plated products on a small scale.
“Moving to the new building that’s nearly three times the size will give us the space to expedite that process. Additionally, we plan to manufacture two vitrified products and a hybrid product in the new space.
“This is a big step and it goes hand in hand with the expansion we’re doing in the United States.
“It comes down to Nick having a belief in the people and the team. This is going to put rocket boosters under the company to continue with the growth trajectory.
“With everything consolidated under one roof, we will get to lay it out to maximise efficiency instead of having to work around the nooks and crannies of the current building.
“The accommodation will also be improved for the employees with nice fresh locker rooms and a cafeteria.
“Nick has a supercharged, can do mentality and we expect to be up and running in the new building in the first quarter of next year.”
According to Finance Manager Michaela Lawton, the Kinmel Bay staff were delighted to have the opportunity to finally meet Nick and Shane in person.
She said: “We have a solid leadership team here and a fantastic workforce that has the full backing of our American owners and it’s clear that the team here has proved itself worthy of this massive investment.
“It’s going to be a process over the next few years, with recruitment, upskilling and training and a lot of capital expenditure on fitting out the new factory with the specialist equipment that we need.
“We are aiming to follow in the footsteps of our American counterparts who have seen huge growth over the last 10 years.
“They’ve gone from our current size to employing over 200 people and we want to follow the same path.”
Justin Hughes, the production manager in Kinmel Bay, has worked at the Kinmel Bay site for 17 years and is the son of the retired technical director, Peter Hughes, who was among the founders of Consort Precision Diamond.
He said: “The takeover has been a marriage made in business heaven because the operations on both sides of the Atlantic dovetail perfectly with each other.
“The news about the investment is incredibly exciting and is the perfect birthday present as we celebrate our 40th anniversary.
“It will undoubtedly inspire us to reach even greater heights and become a truly global player. The sky really is the limit.”
CDT Is Boosting Capacity of Plated Grinding Wheels and Dressing Tools
Learn how Continental Diamond Tool is expanding capacity with a new PUMA Lathe, OGP SmartScope, and Doosan Milling Machine for plated grinding wheels and diamond rotary dressers.
An electroplated grinding wheel completes machining on CDT’s new PUMA DNT 2600LM CNC Lathe.
At Continental Diamond Tool, we invest in cutting-edge technology, skilled professionals, and continuous improvement. We aim to be the world’s most reliable source for innovative, high-quality, customized precision grinding solutions, offering exceptional performance and long life. The market has responded, and the last several years we have experienced tremendous growth.
To meet growing demand, our manufacturing center in North Wales has recently acquired three new pieces of equipment, made possible in part by the Conwy – UK Shared Prosperity Grant. This strategic investment is set to significantly expand our production capabilities for the manufacture of electroplated grinding wheels and diamond rotary dressers.
The Journey of Investment
In Q3 2023, CDT Ltd. in the United Kingdom embarked on an ambitious venture with the introduction of a new product line at its facility: custom-engineered electroplated cBN and diamond grinding wheels and tools. To support this initiative, we purchased dedicated electroplating tanks, stripping lines, and specialized manufacturing equipment for product testing and prototyping. This setup has been essential in ensuring that these products maintain the same precision and quality customers expect from CDT.
Meanwhile, our Rotary Diamond Dressers line — the specialty of this business center — continues to thrive. Sharing machining equipment between this booming line and the growing orders for electroplated products has become a challenge. Additionally, we are starting to see strain in our inspection capacity with the increased demand for these two technologies.
Strategic Acquisitions for Expanding Production
The introduction of a Puma lathe, OGP SmartScope, and Doosan milling machine addresses these challenges and paves the way for sustainable growth, diversification, and more efficient delivery for our customers.
Puma DNT 2600LM CNC Lathe
The first new equipment delivery took place in May with the arrival of the Puma DNT 2600LM CNC Lathe. This piece of equipment is crucial to meet the increasing demand for electroplated products independently from our rotary diamond dressers. Having a dedicated Puma Lathe for plated products assists in the timely delivery of these high-quality tools to our customers without compromise.
OGP SmartScope
In June we received the OGP SmartScope, a revolutionary 3-axis video measurement system. The SmartScope E7, with its IntelliCentric™ fixed lens optical system, 6-megapixel camera, and 5-position digital zoom, delivers high-resolution images that are essential for precise metrology. This state-of-the-art equipment will expand our inspection capacity to maintain the high standards expected of our precision products.
Doosan Milling Machine
Delivered in early September, the Doosan Milling Machine completes our trio of new equipment purchased with the government grant. This addition further bolsters production, ensuring we have the capacity to meet growing demands and continue our commitment to excellence.
A CNC operator programs CDT’s new PUMA Lathe that was delivered and installed in May.
A CDT quality tech measures a coupon on the new OGP SmartScope that was delivered in June.
A technician operates CDT's Doosan Milling Machine that was delivered in September.
Impact and Future Prospects
With the Puma Lathe, OGP SmartScope, and Doosan Milling Machine now up and running, we are already seeing the benefits in our production processes. The ability to utilize these machines for Plated products independently of our Rotary Diamond Dressers line has optimized our workflow and improved our overall efficiency.
These investments also support a long term strategy for CDT Ltd. They not only address our current production challenges but also set the stage for future growth and diversification at this facility. As we continue to innovate and expand our capabilities, we remain committed to the timely delivery of the high-quality products our clients expect.
Stay tuned for more updates as we continue to enhance our production capabilities and explore new horizons in the industry.
For more information on the Puma DNT 2600LM CNC Lathe, visit here.
Continental Diamond Tool Ltd., located in Kinmel Bay on the Western Coast of North Wales in the United Kingdom, is dedicated to providing top-tier superabrasive products for precision grinding and dressing.
At Continental Diamond Tool, we are excited about these investments and look forward to leveraging this equipment to further our mission of excellence in the industry. If you need a solutions provider for your precision grinding applications, please contact our sales team through our website contact form or
call +44 1745-343951 (UK) / 1-800-443-6629 (USA).
Essential Role of Diamond Rotary Dressers in Precision Grinding
This article explores the essential role of Diamond Rotary Dressers in maintaining the efficiency and precision of grinding wheels across various industries, highlighting their types, bond structures, applications, and the expertise of Continental Diamond Tool in providing customized, high-quality solutions.
Grinding wheels, essential for precision manufacturing and shaping of materials, inevitably wear down with use. This wear occurs due to the abrasive action against hard materials, causing gradual degradation of the wheel’s surface. Over time, the cutting edges of the abrasive particles dull, and the bond holding these particles in place can break down, leading to a loss of material from the wheel. This wear not only reduces grinding efficiency but also affects the accuracy and finish of the ground parts.
"Every grinding wheel, whether it be conventional or superabrasive, requires dressing to maintain its profile and cutting performance. Rotary Diamond Dressers are especially useful for precision applications, when you're trying to achieve micron-level tolerances," explains Ed Pitock, Production Manager for Rotary Diamond Dressers.
The Best tool for Grinding Wheel maintenance
Types of Diamond Rotary Dressers
There are two primary types of diamond rotary dressers, also called diamond rolls:
Traverse-Style Diamond Rolls: Move across the grinding wheel, providing a comprehensive dressing solution. Often a single traverse-style dresser can be programmed for use with many different profiles.
Plunge-Style Diamond Rolls: Plunge directly into the grinding wheel, offering uniform dressing of a single precise profile for a specific application.
At Continental Diamond Tool, we custom design both types for our customers to meet the requirements of their processes, machines, and part specifications. This ensures that the desired surface finish and geometry are consistently achieved.
Bond Structures
The bond structure in Diamond Rotary Dressers refers to the material and method used to hold the abrasive diamond particles in place. The bond structure determines the strength, durability, and performance characteristics of the dresser. There are different types of bond structures, each suited for specific applications:
Infiltrated Bond Structure: Also known as sintered, this structure involves filling the spaces between diamond particles with a powdered metal that is then sintered. It is known for its robustness and longevity, making it suitable for demanding applications.
Reverse Plated Bond Structure: In this method, diamond particles are electroplated with a layer of nickel. While not as durable as infiltrated bonds, reverse plated bonds allow for more complex geometries and are used for specialized applications.
CVD Inserts
In the context of Diamond Rotary Dressers, CVDs refer to Chemical Vapor Deposition diamonds. These synthetic diamonds are created in a controlled environment, allowing for the production of high-purity and high-quality diamond material. Advantages include:
Purity: CVD diamonds have fewer impurities compared to natural diamonds, resulting in reliable and predictable performance.
Consistency: The controlled manufacturing process ensures uniformity and consistency in diamond quality for reliable results.
Customization: The CVD process allows for the production of diamonds with specific properties that are advantageous to industrial applications. This material can also be cut into specific sizes and shapes for reinforcing of a high wear areas or used as the main lot abrasive in the roll.
CVD diamonds are sometimes added to Diamond Rotary Dressers due to their unique properties, including exceptional hardness, wear resistance, and thermal conductivity. By incorporating CVD diamonds, rotary diamond dressers become a powerhouse in micron-scale precision, superior durability, and enhanced efficiency, making them ideal for highly demanding dressing applications.
Industrial Applications
Diamond Rotary Dressers are utilized across various industries, offering precise solutions for different needs. Key sectors include:
Automotive: These dressers ensure that automotive components meet stringent tolerance requirements, contributing to the reliability and performance of vehicles.
Aerospace: The precision of Diamond Rotary Dressers is critical for producing aerospace components capable of withstanding extreme conditions.
Cutting Tools: These dressers maintain the sharpness and efficiency of cutting tools, enhancing their performance and longevity.
Bearings: Precision dressing is essential for producing high-quality bearings that meet the rigorous demands of various applications.
By maintaining critical dimensions, enhancing longevity and sharpness, and providing smooth and flawless surfaces, Diamond Rotary Dressers play a vital role in supporting these key industries.
Quality and Customization in Manufacturing
The quality and custom design of Diamond Rotary Dressers are paramount to their effectiveness. "When customers visit our Indiana facility here, they're blown away," notes Troy Giacherio, Product Manager for Rotary Diamond Dressers. "They're going to see the attention to detail, the quality that's taken in every step of the process, and the meticulous customization that we do."
Each product is designed specifically for the customer's process, machine, and part, ensuring a precise fit and optimal performance. This level of customization ensures that the unique needs of each customer are met, providing the ideal solution to their grinding processes.
Customer Support and Technical Expertise
At Continental Diamond Tool, customers also benefit from our extensive support and technical expertise. In 1984, Consort Precision Diamond Company set out to build a reputation as the finest maker of the emerging Diamond Rotary Dresser technology.
Fast-forward 40 years, under Continental Diamond Tool’s leadership, these advancements have been added to the mix at its 200,000 sq. ft. manufacturing center in the United States. Combining the British ingenuity with CDT’s 50 years of excellence in superabrasive grinding wheels, CDT has solidified its position as a leader in offering this cutting-edge solution for precision manufacturing.
Our Diamond Rotary Dresser departments span two continents and have decades of combined experience. Our team is readily available to assist with any challenges, ensuring that customers receive tailored solutions and guidance. "Here at CDT, our customers can always rely on our experience, our technical expertise, and our customer service," Giacherio emphasizes.
An Essential in Advanced Manufacturing
Diamond Rotary Dressers provide essential solutions for maintaining the efficiency and precision of grinding wheels across multiple industries. With robust bond structures, customization options, and applications in sectors like automotive, aerospace, cutting tools, and bearings, these tools are critical for achieving high-precision outcomes. Continuous investment in advanced technology and quality assurance ensures that Diamond Rotary Dressers from Continental Diamond Tool meet and often exceed customer expectations. By utilizing the latest advancements in superabrasives and precision engineering, these tools address the evolving needs of various industries in their precision manufacturing processes.
How to Dress a Vitrified CBN Grinding Wheel with a Diamond Rotary Dresser
In episode 5 of The Grinding Chronicles, CDT Product Manager Troy Giacherio shares top techniques for dressing Vitrified CBN grinding wheels using Diamond Rotary Dressers. Learn how to use key parameters such as velocity ratio and overlap ratio to enhance dressing and truing operations in precision grinding.
If you work in manufacturing, particularly in the specialized area of precision grinding, it cannot be overstated the importance of wheel dressing to maintain operational efficiency and product quality. In this comprehensive guide, we will look at the best techniques for traverse dressing a vitrified cubic boron nitride (CBN) wheel using Rotary Diamond Dressers. In Episode 5 of The Grinding Chronicles, CDT Product Manager Troy Giacherio details the specific parameters and most important factors necessary for achieving peak performance in dressing and truing operations. Watch Troy’s video or read on to learn more.
The Grinding Chronicles - Episode 5
Best Techniques for Success When Dressing a Grinding Wheel
Before plunging into the specifics of dressing a Vitrified CBN wheel, it's imperative to understand the dichotomy between two fundamental processes: truing and dressing. Truing involves sculpting the shape or profile of the grinding wheel, while dressing focuses on sharpening the wheel and removing accumulated debris. While diamond rotary dressers serve both functions, understanding this distinction facilitates the implementation of effective dressing strategies.
Essential Parameters for Dressing Success
There are four key parameters to measure for optimizing the dressing of a grinding wheel:
Velocity Ratio At the heart of dressing lies the velocity ratio, calculated by dividing the velocity of the diamond roll by the velocity of the grinding wheel. This parameter holds significant importance in dressing operations. For Vitrified CBN wheels, the recommended velocity ratio stands at 0.8. Maintaining this ratio ensures that the diamond roll adeptly removes the bond material, laying bare fresh abrasives for optimal grinding performance.
Overlap Ratio The overlap ratio describes the velocity at which the diamond dresser traverses the wheel's face to sculpt its profile and hone its edge. For Vitrified Bond CBN wheels, an overlap ratio ranging between 2 to 4 is ideal. Sustaining a steady pace ensures a seamless traversal across the grinding wheel. It is important to prevent the dresser from dwelling in any single spot to guarantee uniform dressing proficiency.
Depth of Dress The depth of dress measures the extent to which the diamond roll plunges into the grinding wheel, thereby dictating the volume of material extracted per pass. When it comes to Vitrified CBN wheels, we recommend a precise depth of dress set at 0.0002 inches per pass. Adherence to this specification not only optimizes grinding efficiency and minimizes downtime, particularly in high-volume production environments, but also preserves the longevity of the grinding wheel, yielding an optimized return on investment.
Dress Interval The dress interval is defined as the frequency at which the grinding wheel needs dressing, and it is closely tied to the application at hand. Unlike their conventional abrasive counterparts, Vitrified CBN wheels do not require frequent dressing. On the contrary, it is not uncommon to grind hundreds of parts between each dressing session. However, it is important to remain vigilant. Keep an eye on the process and be prepared to adjust the dress interval if part quality diminishes.
When Should I Dress My Grinding Wheel?
Dressing frequency varies depending on several factors specific to your process. Here are two key indicators to monitor in order to assess grinding efficacy and determine when it's time to dress your grinding wheel.
Power Draw The power draw during grinding operations can be a reliable indicator for grinding wheel dressing. A drop in power draw signals that the wheel is cutting freely, with utmost efficiency, while an uptick in power suggests a looming need for dressing. Neglecting timely dressing can lead to issues such as burn or unwanted variations in surface finish. That’s why it is important to keep a close eye on power draw dynamics to prevent such issues.
Surface Finish The surface finish of machined parts relies heavily on consistently high levels of grinding performance. A well dressed wheel produces exceptional surface finishes characterized by minimal variations and unyielding consistency in part quality and dimensional accuracy. Therefore, regular dressing sessions conducted with meticulous technique are essential for maintaining superb parts quality and excellence.
Troubleshooting and Optimization
If you are still experiencing issues such as finish patterns or burn despite adhering to prescribed dressing parameters, it may be time to call in the assistance of an expert. Companies like Continental Diamond Tool have application engineers who are trained to analyze grinding processes, pinpoint underlying issues, and facilitate optimization for enhanced performance. Armed with a portable grinding lab, these experts bring their expertise on-site to meticulously evaluate coolant delivery systems, fine-tune machine settings, and traverse a gamut of other variables to resolve persistent challenges. With their help, you can galvanize productivity to unprecedented heights. If you would like help with your wheel dressing or grinding process, don't hesitate to reach out to our engineering team at TheGrindingChronicles@CDTUSA.net.
Mastering Wheel Dressing
Proper dressing of a Vitrified CBN grinding wheel with a Diamond Rotary Dresser is the key to optimal grinding performance and part quality. By incorporating the parameters and techniques we’ve outlined in this article, manufacturers can achieve reductions in downtime, extension of wheel life, and unwavering consistency in high quality results.
Additionally, by closely watching power draw and surface finish, you will know when it is time to dress before problems get out of hand. With consistent dressing, and seeking expert help when needed, companies can overcome grinding challenges and greatly improve productivity.
Whether transitioning from conventional abrasives to CBN or seeking to refine existing grinding processes, mastering proper dressing techniques with Diamond Rotary Dressers holds the key to consistent and dependable success. Check out more grinding related topics in other episodes of The Grinding Chronicles from Continental Diamond Tool.
Students Build Careers in Engineering with CDT Apprenticeships
Continental Diamond Tool Ltd. is shaping engineering careers for Kinmel Bay-area students like Rhys Butler and Corey Jones. Follow Rhys's eight-week work experience apprenticeship alongside Corey at CDT's precision manufacturing facility in North Wales.
(From left to right) Rhys Butler, left, and Corey Jones who are building careers in engineering with the apprenticeship programme at Continental Diamond Tool Ltd. in collaboration with Coleg Llandrillo in North Wales.
An 18-year-old sixth form student is getting a taste of the world of precision engineering after being inspired by the success of a high flying company.
Rhys Butler, a pupil at Ysgol Glan Clwyd in St Asaph, is now on an eight-week work experience programme after writing to Continental Diamond Tool, on the Tir Llwyd Industrial Estate in Kinmel Bay, which is withing walking distance of his home.
According to Rhys, he was prompted to get in touch when he read a news story about the firm which supplies sophisticated parts for production machinery for Rolls-Royce and other aerospace companies in the UK.
Continental Diamond Tool Ltd. (CDT), which employs 40 skilled staff and is celebrating its 40th anniversary this year, is one of only two companies of its kind in the UK.
It makes a range of highly specialised diamond tools for advanced manufacturing industries, including the aerospace, automotive, medical and semi-conductor sectors.
Rhys said: “I saw the story about the company being under new American ownership and I was looking for work experience for my CV so I emailed in an application and they came back to me straight away.
“They’ve given an eight-week programme so I go in one day a week and I’m going through the different processes they do and they show me and explain how they work.
“One Wednesday I was actually working on putting the diamonds into the tooling. It’s been a brilliant opportunity.
“I’ve always been interested in cars and how machines work and I’m doing engineering in sixth form and go to the Llandrillo College campus in Rhyl every Thursday which is really helpful.”
Rhys often works alongside Corey Jones, 19, also from Kinmel Bay, now in his second year as an apprentice who also took the work experience route to a place with CDT.
He said: “I did my A-levels at Eirias High School in Colwyn Bay and then did Level Three Engineering at Coleg Llandrillo’s site at Rhyl with work experience here and they offered me an apprenticeship.
“They wanted me to get used to what’s involved so I worked here through my summer holidays and started my apprenticeship in September in Level Four Engineering.
“I knew there was a lot of maths in engineering and I’d always enjoyed that and I like to challenge myself by learning about the different machines so I’m really enjoying it.
“I had tried a few places for work experience and Coleg Llandrillo suggested here and it’s been brilliant.
“The people here are really great and very knowledgeable with lots of experience you can learn from – I work with someone who has experience on every machine and he’s a big help.
“We’re working for businesses like Rolls-Royce which is fantastic so I want to do the best I can and really build a career here.”
Michaela Lawton, CDT Finance Manager, said: “We have been running an apprenticeship scheme here for a long time and historically it’s been successful and two of our apprentices who moved on after a few years have actually come back to us.
“We have a very good relationship with Coleg Llandrillo and it really helps that they have a campus at Rhyl with a strong and well-equipped engineering department.
“What we do here is so unique and so niche that we expect our apprentices to learn the core skills in college to give them the platform to build on with the highly specialised work we do here.”
CDT has been boosted by a £1.6million investment by their American owners and has opened a second production unit on the Tir Llwyd Estate to house its new electro-plating operation which has received support from Welsh Government.
More than 60 per cent of the company’s products are exported to 30 countries, with sales growing particularly strongly across Europe and Asia, as well as North America.
The company, which celebrates its 40th anniversary this year, was founded originally as Consort Precision Diamond and in 2018 was bought and rebranded by Continental Diamond Tool Corporation, based in New Haven, Indiana.
Related Links:
https://www.gllm.ac.uk/news/rhys-and-corey-shine-with-diamond-tool-firm
Images captured by Mandy Jones Photography.
High Flying Engineering Firm Says Fond Farewell to Founder Steve
Celebrating the journey of Steve Noakes, founder of Consort Precision Diamond Company, which later became Continental Diamond Tool Limited. Hear about his retirement celebration and the company's bright future with CDT.
A specialist engineering company that keeps the world’s airlines flying will reach new heights thanks to investment from its new American owners, according to one of the firm’s founders.
Former production director Steve Noakes, 67, from Trefriw, in the Conwy Valley, was speaking at a presentation ceremony to mark his retirement from Continental Diamond Tool in Kinmel Bay which is celebrating its 40th anniversary this year.
Among his leaving gifts was a nickel plated version of the graphite mould for a diamond rotary dresser of the type used to grind the turbine blades of Rolls Royce aero engines, with the signatures of each of his 40 colleagues engraved onto it.
Steve was one of the eight people who established the niche company as Consort Precision Diamond in 1984, specialising in the manufacture of diamond-encrusted rotary dressers and grinders.
The firm – still one of only two similar companies in the UK – supplies a range of manufacturing sectors, including aerospace, automotive, medical and semi-conductors.
It’s products are used in Boeing 777 and 787 Dreamliner aircraft, as well as the Airbus range A330-A380 whose wings are made at the giant Airbus factory in Broughton.
The company was acquired and rebranded in 2018 by American outfit Continental Diamond Tool which has its headquarters in New Haven, Indiana.
Father-of-two Steve was the last man standing because all the other members of the original team had already retired.
He left “safe in the knowledge” that the company was in good hands. having seen the new management team investing £1.6 million to launch a second production line to make electro-plated grinding wheels, with record profits and sales soaring by 70 per cent.
Steve said: “I am extremely proud of what we have achieved, employing people for 40 years in skilled, well paid jobs.
“I’m also very proud that we’re now part of Continental Diamond Tool. Acquisitions can be messy affairs but this was actually a really happy process.
“They have the same mindset as a family-oriented company, looking after their employees and building a successful business with a very good future. The fit is excellent because they can invest more than we were able to as an independent company.”
He was delighted by the “perfect” gift of the inscribed nickel-plated mould which was presented by his old boss, the original managing director, Dave Morris, who came back for the emotional occasion.
He said: “Steve made a huge contribution – he’s a real diamond. In one sense this is a sad day but it’s also a good one for him because we know our legacy is safe. They’re a good bunch of people.”
There were also good wishes from CDT president, Nick Viggiano, who said: “We will always be indebted to Steve and his fellow founders for their grace, helpfulness and goodwill in managing the transition to the new ownership.
“Steve played an integral role in building a very successful company with a global reputation for excellence in a very competitive niche market. He should be incredibly proud of what he achieved.”
The current managing director, Jeff Wirth, adds, “We are determined to build on those firm foundations and continue to grow and prosper as we look forward to the next 40 years of success.”
The baton has also been passed to current production manager Justin Hughes, son of the firm’s original technical director, Peter Hughes.
He said: “We now have backing behind us which enables us to push forward and aim at new markets because we have a big safety net behind us. It gives us reassurance.
“I spoke to our new managing director, Jeff Wirth, who was incredibly complimentary about the existing workforce and said how brilliant it was and the high level of skill and work ethic here.”
It was a sentiment echoed by finance manager Michaela Lawton who said: “We have a lovely team here and everyone’s really very excited about the future.
“We’ve had an investment of £1.6 million and the company’s been on an upward trajectory in terms of growth, turnover and profit and being able to diversify our product range is the next step forward.
“It’s great for Steve, who’s been with the company from the very beginning, to see that that the company is going to continue to grow and expand into new markets.
“Every business goes through a life cycle and the acquisition happened at a perfect time with the original founders reaching retirement age. It was a marriage made in business heaven and the sky’s the limit.”
Related Links:
https://www.insidermedia.com/news/wales/engineering-firm-set-to-reach-new-heights
https://www.wales247.co.uk/high-flying-engineering-firm-says-fond-farewell-to-founder-steve
Continental Diamond Tool Limited Soars with Record Sales Driven by £1.6 Million Investment
Learn about Continental Diamond Tool Limited's remarkable growth and success fueled by a £1.6 million investment and their expertise in crafting diamond-encrusted tools for diverse global industries.
Continental Diamond Tool Limited — CDT’s subsidiary stationed in Kinmel Bay, Conwy, in North Wales— is experiencing an era of remarkable growth thanks to a substantial £1.6 million investment initiative. According to Jeff Wirth, the Managing Director, this rapid expansion is a result of a perfect blend of Welsh dedication and backing from its American stakeholders.
"As part of our expansion strategy, we opened a second production unit, which has facilitated the establishment of a new electro-plating operation. With support from the Welsh Government, this move marks a significant leap for us," said Wirth.
Continental Diamond Tool Limited is a niche outfit, one of merely two similar enterprises in the UK that specializes in crafting diamond-encrusted rotary dressers and grinders. The team designs their custom products for diverse manufacturing sectors like aerospace, automotive, medical, and semiconductor industries.
"In aerospace, our rotary diamond dressers play a pivotal role in crafting engine parts for prominent aircraft like the Boeing 777 and 787 Dreamliner, as well as the Airbus A330-A380 series," commented Wirth. These aircraft parts are notably crafted at the Airbus facility in Broughton.
"Over 60% of our products find their way to 30 countries globally, experiencing substantial growth across Europe, Asia, and North America," added Wirth.
Originally founded as Consort Precision Diamond, the company will be celebrating its 40th anniversary in April of next year (2024). In 2018, it underwent a timely transition when Continental Diamond Tool Corporation acquired it. During the COVID-19 pandemic, the company showed resilience amid adversity as it pivoted its product range to mitigate a significant loss of orders in one of its largest sectors due to grounded passenger planes.
"It would have sunk most companies, but we had already started our diversification and a pretty significant culture change here," remarked Wirth during a visit from the States. "Sales are now at a record high. Over the last five years, our Rotary Diamond Dresser product line in Kinmel Bay has seen remarkable growth of over 70%, despite the negative effects of COVID," he continued.
CEO Nick Viggiano noted, "We believe in the workforce here, we believe in the people, their work ethic, their can do spirit, and the pride they take in their work. At CDT headquarters in New Haven, Indiana, the culture is the same. When you take modern technologies and join it with that culture, it’s a recipe for success.”
"The new energy and substantial investment brought by the new owners has been a game-changer," echoed Michaela Lawton, the finance manager. "We've also had a good relationship with the Welsh Government for some time. The latest support with the £90,000 we received from the Smart Cymru fund helped fast-track the new technology that we introduced through the electro-plated product."
The project has been a source of great pride to production manager Justin Hughes who’s been working at the Kinmel Bay site for the past 17 years.
He said: “We’ve got the backing of the American parent company behind us which enables us to push forward with investment in machinery and people to aim at new markets. It gives us reassurance and confidence as we continue to grow and develop.”
"The company is on an upward trajectory in terms of growth, turnover, profit, and being able to further diversify our product range is the next step forward,” adds Lawton. “It's a very exciting place to work, and the sky really is the limit.”
Related News Links:
https://www.business-live.co.uk/manufacturing/global-engineering-firm-north-wales-28144996
http://www.baysideradio.co.uk/news/kimmel-bay-global-engineering-firm-propelled-by-1-6m-boost-8260
Mastering Precision Grinding with Diamond Rotary Dressers for Plunge Dressing
Master precision grinding with Diamond Rotary Dressers for plunge dressing. Learn how Consort Precision™ Diamond Rotary Dressers provide quicker lead times, hold tighter tolerances, and sustain higher durability in rough environments.
When it comes to precision grinding, achieving exceptional accuracy and control is paramount. One of the key techniques that enable this level of control is Plunge Dressing through the use of a precision diamond rotary dresser. In this blog, we will explore Plunge Dressing and the crucial role it plays in the high tech manufacturing industry. We will also take a step back in time to uncover the history of this essential tool.
Understanding Plunge Dressing
Plunge Dressing is a specialized method used in precision grinding requiring the tightest tolerance controls. The process involves “plunging” a precision rotary diamond dresser with the form of the finish part vertically into the grinding wheel. This approach allows for a mirror image of the part to be put into the grinding wheel which is then used to grind the finished parts to the highest levels of accuracy achievable.
The History of Plunge Dressing
Plunge Dressing, in its essence, is as old as precision grinding itself. It evolved alongside the broader history of abrasive tools and precision engineering, with the diamond rotary dresser as a key component.
The roots of Plunge Dressing can be traced back to the early days of industrialization when grinding processes were becoming essential for the production of precision components. As the manufacturing industry advanced, the need for higher precision, tight tolerances, and complex profile (geometry) control became apparent. This led to the development and refinement of techniques, including the use of the precision diamond rotary dresser or diamond dressing wheel, to enhance the grinding process.
Since 1984, Continental Diamond Tool Limited, then called Consort Precision Diamond Company, has been making precision Hand-Set “Sintered” Rotary Diamond dressers. In 1995, CDT LTD made waves with its development of an electroforming process that greatly reduced the process time for Reverse Plated Diamond Rotary Dressers. With these advances and revolutionary technology in both Sintered and Reverse Plated manufacturing methods, precision Rotary Dressers are now more affordable and accessible to a greater number of industries.
The Benefits of Plunge Dressing with a Diamond Rotary Dresser
Plunge Dressing with diamond rotary dresser, offers a range of benefits that make it a preferred choice in precision grinding:
1. Precise Profile Control: Plunge Dressing with a diamond rotary dresser enables the precise shaping of intricate profiles on workpieces. This level of control is invaluable in applications where tight tolerances and intricate shapes are required with tolerances of 1um or better.
2. Reduced Heat Buildup: The controlled plunge of the diamond rotary dresser results in precise truing and conditioning of the grinding wheel. This is especially important for materials that are sensitive to heat, helping to prevent thermal damage and maintain workpiece integrity.
4. Consistency and Quality: Plunge Dressing with a diamond rotary dresser ensures consistency in material removal, resulting in a high-quality surface finish on workpieces. This consistency is crucial for producing precise components with minimal variation.
The Mechanics of Plunge Roll Dressing
Plunge roll dressing involves a specific mechanical process. Here's a glimpse of how it works:
Preparation: To start, the diamond rotary dresser is set up and aligned with the grinding wheel.
Vertical Movement: Then the dresser is moved vertically into the spinning grinding wheel. The depth of penetration is precisely controlled to ensure the desired material removal.
Material Removal: As the diamond rotary dresser engages with the grinding wheel, it removes material from the wheel's surface. This process allows for the desired profile or shape to be formed on the wheel.
Controlled Withdrawal: After the material removal process is complete, the diamond rotary dresser is withdrawn from the grinding wheel. This is done with the same level of precision and control to maintain the desired profile.
APPLICATIONS for Plunge Dressing with a Diamond Rotary Dresser
Plunge-style diamond rotary dressers find applications in many industries, such as:
Aerospace: In the aerospace industry, where precision and tight tolerances are paramount, plunge dressing with a diamond rotary dresser is used to shape critical components for aircraft and spacecraft.
Medical Devices: Plunge-style diamond rotary dressers are essential for creating intricate and precise components in medical devices to ensure their safety and effectiveness.
Automotive: This type of diamond rotary dresser is regularly employed to craft precision parts for the automotive industry, contributing to the performance and longevity of vehicles.
IN SUMMARY
In the world of precision grinding, plunge dressing with a diamond rotary dresser stands out as a technique that empowers manufacturers to achieve the highest levels of precision and quality. Its control and consistency make it an invaluable tool for industries where tight tolerances and intricate profiles are the order of the day.
Our Consort Precision™ line of Diamond Rotary Dressers offers versatility in design, with custom plunge form dressers available in sintered or reverse plated variants. The plated plunge form rotary dressers have the extra benefit of being able to hold tighter tolerances, where as Sintered Rotary Dressers can have shorter lead times and hold up better in rough environments. Both Sintered and Reverse Plated Rotary Dressers can be manufactured and shipped from our manufacturing facilities in either North America or Europe.
The Story Behind Our Precision Grinding Solutions at Continental Diamond Tool Ltd.
Continental Diamond Tool Limited's Diamond Rotary Dressers set industry standards with cutting-edge technology and award-winning processes. With decades of expertise and product excellence, our dressing and grinding solutions meet the demands of diverse industries worldwide. Learn more about our innovative solutions in precision grinding.
At Continental Diamond Tool Limited, our 40 years of success has been built by delivering the finest custom Diamond Rotary Dressers available in the market. Also called Diamond Rolls, these tools are used extensively in a growing number of grinding operations to primarily facilitate the transfer of highly accurate repeated configurations onto components. What makes a Consort Precision Diamond Rotary Dresser stand out can be summarized in four key aspects: technology, expertise, process, and quality or product excellence. As we have expanded into other product lines, we bring that same commitment to every precision grinding product we produce.
Cutting Edge Technology
In a plunge-style dresser the Rotary Diamond Dresser is mounted onto a spindle of a drive unit which in turn is mounted onto a slideway arrangement that allows the formed periphery of the dresser to infeed into a grinding wheel, thereby transferring the desired shape into it. The form, or configuration, can then be 'ground' on to the component. Plunge dressers are especially accurate for precision grinding as there is no lost form or geometry due to machine movements. Plus, the dressers can be held to submicron levels of accuracy.
Traverse dressing is a grinding wheel dressing technique where the diamond rotary dresser traverses across the surface of the grinding wheel to create a specific profile or shape. Traverse Disc Dressers allow you the flexibility to make profile changes or dress in completely new profiles with the same tool, reducing down time for wheel change overs or roll changes.
INDUSTRY EXPERTISE
Such Industries as the Automotive and Aerospace as well land based Turbine Engine production units employ large quantities of Rotary Diamond Dressers. Typically, within the Aero manufacturing industry, such components as Turbine Blades and Nozzle Guide Vanes as well as Flap Actuating Shafts require their intricate features to be ground with grinding wheels that have been formed with Rotary Diamond Dressers. As can be seen reference is made on our following pages to the many applications within the automotive industry.
CDT Ltd. can offer expertise in the selection of the most appropriate type of Rotary Diamond Dresser by reference to the configuration required and to the grinding machine on which it is to be used. Basically, three processes are employed. Handset Sintered, Random Set Sintered and Reverse Plated. Within each of those categories, selection of diamond type and their placement into the periphery of the Rotary Dresser, plays a major part in determining its operational life and performance. Even before its establishment in 1984, the company’s principals and a large proportion of its employees had many previous years experience in the manufacture of Rotary Diamond Dressers. Bringing with them unique knowledge of the industry, CDT Ltd. — then Consort Precision Diamond — quickly established itself with this one product into the global market of prime and subcontract component manufacturers, earning the respect of competitors and customers alike.
AWARD-WINNING PROCESSES
In respect to the Reverse Plating technique, at Continental Diamond Tool Limited we are particularly proud of the fact that we have been awarded the accolade of winning the BOOST award in the U.K. in 1995 for the design and development of a high speed plating process which dramatically reduced previous lengthy plating times. This achievement gave us a competitive edge against alternative suppliers and satisfied the reduced lead times that customers continue to demand. In the same period, we gained the S.M.A.R.T 1995 award for the development of the electroforming process as an acknowledgement of the reduction in the process time employed in the manufacture of Reverse Plated Rotary Diamond Dressers. CDT Ltd. proudly holds the ISO 9001:2015 Registration Certificate for its Quality Management Systems.
A FOCUS ON PRODUCT EXCELLENCE
The Consort Precision name has become synonymous for outstanding quality and performance in Diamond Rotary Dressers. Since 1984, we have been perfecting the design, development, manufacture, install and maintenance of this advanced dressing technology. This long history with a singular focus has given us the unique ability to provide our customers with the best solution technology can offer. We have the engineering, design, manufacturing and staff resources to supply the highest quality Diamond Rotary Dressers available on the market. Our specialized experience ensures each product we supply is the optimum choice for each individual customer, however demanding and complex the configuration. If an application calls for traverse- or plunge-style rotary dressing, Consort Precision™ Diamond Rotary Dressers are the best tool for the job.
With investment from our parent company, Continental Diamond Tool Corporation, we have expanded our facility in Kinmel Bay to manufacture a wider range of superabrasive products and better cater to a global market. In 2021, an expansion of the Plating lab more than doubled our capacity to produce the high quality tight tolerance reverse plated rotary dressers used by some of the world’s most prestigious corporations. It also paved the way for diversification into electroplated grinding wheels, which we began producing in early 2023. As CDT Ltd. continues to evolve and adapt to the ever-changing technological landscape, we remain committed to delivering innovative solutions and superior products to meet the growing demands of our customers worldwide.
Mastering Precision: How Traverse Diamond Dressing Enhances Grinding Wheel Performance
Discover how Traverse Diamond Dressing enhances grinding wheel performance, maintains precision, and reduces scrap rates. Explore applications across industries and choose the right type for your needs.
Precision in manufacturing is the key to producing high-quality components across various industries, from automotive to aerospace, and even in everyday consumer products. One crucial aspect of achieving this precision is the performance of grinding wheels. In precision grinding operations, where the tolerances can be incredibly tight, grinding wheel performance is paramount. Enter the Traverse Diamond Dresser, a type of diamond rotary dresser that plays a pivotal role in ensuring that grinding wheels are in top form. In this blog post, we will delve into the world of Traverse Disc Dressers and explore how they enhance grinding wheel performance.
The Basics of Traverse Diamond Dressing
The Traverse Disc Dresser is an indispensable wheel profiling tool in the realm of precision grinding. Also referred to as Diamond Wheel Dressers, they are designed to dress and shape profile grinding wheels to maintain an optimal condition. The dressing process involves the removal of abrasive material from the grinding wheel's surface, which can become uneven, clogged, or worn over time due to the abrasive grinding process.
Here's how Traverse Disc Dressers work their magic:
1. Material Removal: These dressers feature a wide range of diamond sizes and grades to achieve the desired dressing condition. As the rotary diamond dresser traverses across the grinding wheel's surface, it precisely and efficiently removes small amounts of abrasive material. This effectively 'cleans' the wheel, restoring its cutting ability.
2. Wheel Truing: One primary function of Traverse Disc Dressers is truing the grinding wheel. Over time, grinding wheels can develop irregularities, affecting the precision of the grinding process. The dresser ensures that the wheel runs true and maintains a consistent, flat or cylindrical shape, depending on the application.
3. Form Dressing: In precision grinding, some applications require intricate shapes or profiles to be ground onto workpieces. Traverse Disc Dressers can be employed for form dressing, which shapes the grinding wheel to match specific profiles with utmost precision.
Achieving Superior Grinding Wheel Performance
Now that we understand the role of Traverse Disc Dressers let's explore how these wheel profiling tools enhance grinding wheel performance:
1. Consistency is Key: Precision grinding demands consistency. Traverse Diamond Dressing ensures that the grinding wheel profile remains uniform in shape, minimizing variations in the workpiece's finish and dimensions. This consistency is essential for meeting tight tolerances.
2. Optimized Material Removal: Dressing the wheel not only ensures precision but also optimizes material removal rates. It enhances the wheel's cutting ability, reducing heat generation and the risk of burning the workpiece—a common issue in precision grinding.
3. Reduced Scrap Rates: With a properly dressed grinding wheel, the likelihood of producing defective or out-of-spec parts is significantly reduced. This translates to lower scrap rates and higher yields, ultimately improving the bottom line.
4. Versatility: Traverse Disc Dressers are versatile tools suitable for various grinding applications. Whether you're grinding metals, ceramics, or other materials, these dressers can be adapted to meet your specific needs.
5. Flexibility: Change parts/profile shapes frequently? Traverse Disc Dressers allow you to quickly and easily make profile changes or dress in completely new profiles without making grinding wheel changes, saving you down time for wheel change overs and/or roll changes.
Applications for Traverse Disc Dressers
Traverse Disc Dressers play a pivotal role in a multitude of precision-driven industries. These grinding wheel truers are essential for maintaining and shaping grinding wheels, ensuring that precision grinding processes yield consistent and accurate results. Here's a succinct overview of how key industries rely on Traverse Disc Dressers:
Automotive: Crucial for precision grinding in tasks like crankshaft and camshaft production, gear manufacturing, and engine component fabrication.
Aerospace: Used in grinding operations for aircraft components and jet engine parts, where precision is paramount.
Tool and Die Making: Maintains the sharpness and precision of cutting tools, including end mills, drill bits, and punches.
Medical Device Manufacturing: Ensures precision in the production of surgical instruments, orthopedic implants, and dental tools.
Bearings and Bearing Components: Shapes and maintains grinding wheels to ensure the accuracy of bearing components.
Cutting Tool Manufacturing: Essential for achieving precise tool geometries and cutting-edge profiles in tools like inserts and taps.
Oil and Gas: Involved in precision grinding for drilling equipment, pumps, and valves, vital in this sector.
Metalworking: Used in the production of gears, shafts, and machine components to meet precision requirements.
Die Casting and Foundry: Maintains and shapes grinding wheels to finish cast components with tight tolerances.
Renewable Energy: Supports precision grinding operations for components in renewable energy technologies like wind turbines and solar panels.
These industries rely on Traverse Disc Dressers for precision and consistency in their manufacturing processes, making them essential tools for achieving the highest levels of accuracy in precision grinding operations.
Types of Traverse Disc Dressers
Traverse Disc Dressers come in distinct types, each designed for specific applications. They can be made with a wide range of diamond sizes and grades, with CVD (chemical vapor deposition) stones, or a combination of the two, to achieve the desired dressing condition.
1. Electroplated: Electroplated Traverse Disc Dressers are known for their short lead times and open and aggressive structure allowing for high removal rates with similar performance at a lower cost.
2. Metal Bond: Metal bond Traverse Disc Dressers offer flexibility with a range of bond systems and abrasives to custom fit the application and provide a balance of durability and precision, making them suitable for a wide range of grinding operations.
3. Sintered: Sintered Traverse Disc Dressers offer exceptional durability and precision and are ideal for applications involving hard and abrasive materials with tight profile tolerances.
4. Reverse Plated: Reverse Plated Traverse Disc dressers stand out due to their unique construction, which allows for unmatched precision and efficiency in shaping grinding wheels. They offer benefits such as reduced dressing time, extended wheel life, improved surface finish, and versatility, making them a valuable asset for industries requiring the highest levels of accuracy in their grinding operations.
It's worth noting that CDTUSA manufactures all types of traverse dressers except Reverse Plated, which will be added to our lineup next year. CDT Limited in Europe (previously Consort Precision Diamond) specializes in Reverse Plated, as well as the other types of diamond rotary dressers. When it comes to grinding wheel truers, our dedicated teams are ready to assist you. Feel free to reach out for a free quote, and let us help you achieve precision and excellence in your grinding operations.
Consort Precision Diamond Company Announces New Identity As Continental Diamond Tool Limited
Consort Precision Diamond becomes Continental Diamond Tool Limited, strengthening its precision diamond tools legacy. Expect an expanded product line, unwavering quality, and innovation.
Kinmel Bay, Rhyl, U.K. (September 11, 2023) – Consort Precision Diamond Company, a top manufacturer of precision diamond tools in the United Kingdom, is pleased to share a major announcement. Effective July 10, 2023, the company has officially changed its name to Continental Diamond Tool Limited.
The new name aligns with its parent company, Continental Diamond Tool Corporation (CDT), which acquired Consort in 2018. With headquarters in New Haven, Indiana, U.S.A., CDT is recognized globally for manufacturing high-precision custom superabrasive grinding wheels, which integrates seamlessly with Consort as a distinguished and trusted producer of high-quality precision diamond rotary dressers.
At the core of this name change is a firm dedication to delivering premium quality and innovation. Over the past several years, the company has expanded its facility in Kinmel Bay to manufacture a wider range of superabrasive products and better cater to a global market. In 2021, an expansion of the Plating lab more than doubled the company’s capacity to produce the high quality tight tolerance reverse plated rotary dressers used by some of the world’s most prestigious corporations. It also paved the way for diversification into electroplated grinding wheels, which the facility began producing in early 2023.
This strategic growth is part of the company's unwavering commitment to delivering comprehensive solutions to customers. As the company continues to expand its offerings to encompass more high-performance grinding technologies in step with its parent company, aligning the name and marketing efforts of the two is a logical move.
In the coming weeks, on-lookers can expect to see updates across various aspects of Consort's branding and materials as it transitions to Continental Diamond Tool Limited. This includes revisions to its packaging, marketing materials, website, and all pertinent documentation. The company is committed to ensuring a smooth transition, with minimal disruption to the customer experience.
“For nearly four decades, Consort has faithfully served leaders in the automotive, aerospace, and other precision manufacturing industries. We look forward to continuing our longstanding relationships with customers under our new name,” says Jeff Wirth, Managing Director of Continental Diamond Tool Limited. For further information about this transition, please send any queries to info@cdtltd.com.
About Continental Diamond Tool Limited
Continental Diamond Tool Limited is a globally recognized leader in custom precision diamond tools, specializing in all forms of precision diamond rotary dressers and electroplated grinding products. With a commitment to excellence and innovation, the company serves a diverse range of industries from its advanced manufacturing facility located in the coastal town of Kinmel Bay in Conwy County Borough, Wales, United Kingdom. Learn more at CDTLTD.com.
CDT Expands Diamond Rotary Dresser Production
Continental Diamond Tool is proud to announce that we’re expanding our capabilities to make custom Diamond Rotary Dressers (also known as Diamond Rolls) in our dressing product line.
For companies in need of grinding wheel dressing, conditioning, and shaping, finding a high quality and cost effective supplier for custom dressing solutions is even easier!
Continental Diamond Tool is proud to announce that we’re expanding our capabilities to make custom Diamond Rotary Dressers (also known as Diamond Rolls) in our dressing product line.
Dressing tools are a necessary aspect of maintaining the natural wear and tear that occurs with superabrasive grinding wheels. When your abrasive becomes dull and ineffective due to particle buildup, it is recommended that you use diamond dressers to clear off the particles and make your grinding wheels perform like new again.
While many tool and cutter grinding shops and other manufacturing facilities use stationary dressers to get that job done, more and more industries are finding uses for diamond rotary dressers — and for good reason!
As industries work with more and more advanced and complex engineering configurations, Diamond Rolls are the clear, superior choice for these applications … but why?
Simple. Diamond Rolls:
Have precision profiles and geometry to match your specific needs
Are designed for your specific needs, surface finish, removal rates, time savings
Come in all shapes and sizes, from simple traverse dress rolls to complex profiles
Not only does it make way for excellent sharpening and fine finishes, it’s cost effective too.
CDT currently offers the following types of Diamond Rolls:
CVD dressers
Sintered Rotary Dressers
Reverse Plated Rotary Dressers
Diamond Rotary Dressers are commonly used in the following industries:
Aerospace
Automotive
Biomedical
Knives and Blades
Bearing
Whether you are in an industry that’s looking for one of the dressing products above — or if you want to work with our engineers to develop something new— CDT is excited to serve your needs with the best possible up-and-coming technology for getting the job done right.
CDT has been in the business of providing solutions for sharpening and refinishing of superabrasive grinding wheels with Stationary Diamond Dressers since our start in 1973. In 2018, we added Diamond Rolls to our dresser line through our acquisition of Consort Precision Diamond in the U.K. who joined us with a solid reputation for making major technological advancements in rotary dresser technology.
Now, after upgrades made in late 2022, Continental Diamond Tool has capabilities to produce many configurations of custom Diamond Rotary Dressers at our U.S. facility in New Haven, Indiana. Call us or complete our contact form for details.
Consort Precision Diamond Celebrating 5 Years With CDT
5 years ago, Continental Diamond Tool made one of our biggest leaps into providing top notch products for our customers by joining forces with our subsidiary – Consort Precision Diamond (CPD) – in the U.K. Learn more about what has been accomplished in the past 5 years >
5 years ago, Continental Diamond Tool made one of our biggest leaps into providing top notch products for our customers by joining forces with our subsidiary – Consort Precision Diamond (CPD) – in the U.K.
CPD is a leading supplier of precision Rotary Diamond Dressers for production grinding applications in aerospace, automotive, medical, tooling, etc.
CPD has and remains fully dedicated to this passion – to provide all customers with the best rotary dresser technology possible.
When it comes to Rotary Diamond Dressers, their focus is all-encompassing:
Design
Process & Product Development
Manufacture
Application Support
By teaming up with CPD, CDT has been able to bring quality rotary diamond dressers to the portfolio of superabrasive product offering, allowing for a fully integrated grinding process to the customer.
This has led to superior results for grinding wheel maintenance. The Rotary Diamond Dressers:
Can perform at high dressing speeds
Capability improvements -0.001um tolerance
Allow for more complex configurations
Improved product performance
Capacity expansions
Additional Products - CVD / Traverse disc dressers
Not only does it make way for excellent sharpening and fine finishes, it’s cost effective too.
But we’ve been up to more than just producing the highest quality rotary diamond dressers these past 5 years… All of which has had a direct, positive impact on the service you’ve come to expect with us at CDT.
More has happened over the past 5 years.
Capacity Expansion (2019/2020)
With the help of the Welch government we invested $500k into CPD.
New lathes
New grinders
New inspection lab/equipment
This improved our product quality, increased our capacity, and allowed us to hold tighter tolerances.
Major Upgrades to The Plating Lab
With the increase in demand, and our drive to supply the best of leading edge tech, we launched an upgrade to the plating lab in 2021.
This extension more than doubled our ability to produce high-quality tight tolerance reverse plated rotary dressers.
Featured In the British Chamber of Commerce Study
The British Chamber of Commerce published a case study featuring CPD and our growth in international trade.
We export to over 20 countries worldwide, including:
Europe
USA
Canada
Brazil
Mexico
China
Nominated for 2 Major Awards
CPD was nominated for the 2022 Chamber Business Awards and the WCNW Chamber Business Awards in Export & International Trade.
2x Faster Production Rate
CPD expansion was supported by the government of Wales with £200k.
This support helped protect/create new jobs and would “help fund the first phase of a five year plan that will see Consort Precision Diamond expand and increasing its head count.”
2023
CPD will be adding a new product line of electroplated grinding wheels in Q2, which will allow further expansion into the superabrasives products in the EU/UK markets.
CPD had championed so much in the past 5 years, maintaining and exceeding expectations for being the top producer of diamond rotary dressers.
Thanks for joining in the 5-year celebration with us! We expect even more great things in the coming 5 years.
To get a full look at all Consort Precision Diamond services, click here.
Diamond Rotary Dressers by Type
Find the perfect rotary diamond dresser for your application by considering these 5 factors. Continental Diamond Tool Limited offers decades of expertise and free consultations for customized solutions >
Industry's increasing demand for high-accuracy, high-speed production has fostered a new branch of engineering technology to ensure grinding wheels are maintained in optimum condition. Diamond Rotary Dressers are now recognised as the most efficient and economic means of dressing and truing grinding wheels to the correct form, tolerance and condition. Their use is growing rapidly in the manufacture of components for automotive, aerospace, power generation, machine tool and precision engineering industries.
Leading in innovation
At Continental Diamond Tool Limited, we have been a frontrunner for decades in innovating rotary dresser technology. As far back as 1995, as Consort Precision Diamond Company, we won industry awards for our development of the high speed plating process which dramatically reduced previous lengthy plating times and is still in use today. We proudly holds the ISO 9001:2015 Registration Certificate for its Quality Management Systems, and we are continuously innovating to increase the efficiency and cost effectiveness of this industry-changing technology.
OUR FOUR MAIN PROCESSES
There are four distinct methods we use in the manufacture of our diamond rotary dressers: reverse plated, hand-set sintered, cvd sintered, and random set sintered. Each has its own benefits, as outlined below.
Type 1 - Reverse-Plated
The High Accuracy dresser
Reverse Plated Dressers are selected where high accuracy of profile detail is required together with a correspondingly high quality surface finish on the component.
Accuracy is achieved by centrifugal dispersion of the specially selected diamonds onto the walls of a mould. These are secured by our electro-deposition process that has won acclaim through the acquisition of industry awards, thereby achieving the short lead times so often required by customers.
The electro-deposition process is stable and unaffected by shrinkage, which results in Rotary Diamond Dressers of exceptional accuracy.
Tolerance Detail
General Surface Finish Produced: 0.4uM. 16 C.L.A.
Typical Applications
Turbine Blade - Fir Tree Root Form
Cam Grinding
Bearing Industry
Ball Joints
Needle Injectors
Type 2 - Handset Sintered Dressers
A CONSORT PRECISION™ SPECIALTY
Of all the rotary dressers for which the Consort Precision name is known, Handset Sintered Dressers are our most popular type. These custom diamond rotary dressers cover many applications where robustness is required and the general tolerance is open.
As the name implies, diamonds are selected and set by hand in a mould, then secured in position by sintering in a tungsten based matrix. Allowances are made for consequential shrinkage to bring the finished dresser within specification tolerances.
Tolerance Detail
General Surface Finish Produced: 0.8uM. 32 C.L.A.
Typical Applications
Turbine Blade
Automobile Valves
Crankshafts
type 3 - CVD Sintered
THE High Performance Dresser
Our CVD sintered rotary diamond dressers have very high thermal oxidation resistance and other excellent thermal properties. CVD is perfect for secure mounting with traditional non-ferrous metal sintering. CVD sintered rotary diamond dressers can also be brazed onto a dresser body using an active braze alloy in a non-oxidizing environment.
Benefits
Highly resistant to chipping and fracture
Wears evenly over the dresser's entire length
Performs regardless of dressing orientation
Outstanding thermal stability
CVD diamond can be manufactured in a multitude of shapes, sizes, thicknesses and grades giving engineers great flexibility with this material's extreme properties.
Dimensions
Our CVD diamond dressers can be ordered in all the standard rectangular dimensions in various lengths and square, but we also specialize in supplying non-standard custom dimensions upon request.
Typical Applications
Metal matrix composites
Aluminium alloys
Glass-reinforced plastics
Carbon fibre-based materials
Plastics and rubbers
Graphite
type 4 - random set sintered
The dresser FOR QUICK DELIVERY
Random Set Sintered Dressers are most suitable where openness is required, coupled with a tight form and improved surface finish.
Very often selected diamonds are strategically placed in the mould to support the form in vulnerable areas. The remaining area is then in-filled by centrifugal dispersion of diamonds and sintered.
Random Set Sintered Dressers have the advantage that they can be delivered quickly to meet urgent customer requirements.
Tolerance Detail
General Surface Finish Produced 0.4 uM. 16 C.L.A.
Typical Applications
Automobile Valves
Turbine Root Forms
Flute Grinding
CHOOSING THE RIGHT DRESSER TYPE
Within each of these categories there are many further variables of appropriate diamonds and setting patterns to consider when ordering dressers of this type. Specialist techniques need specialist suppliers which is why we established our Consort Precision Diamond Rotary Dresser custom product line. Since 1984, we have dedicated substantial resources to developing the finest Diamond Rotary Dressers and support services available.
At Continental Diamond Tool Limited, we focus predominately on the design, development, manufacture, install and maintenance of Rotary Diamond Dressers. And we think that gives us a unique commitment to provide our customers with the best technology can offer.
If an application calls for a Diamond Rotary Dresser, Continental Diamond Tool will provide the best tool for the job. Contact us for a free consultation and quote.
What Is a Diamond Rotary Dresser?
Learn what Diamond Rotary dressers are you used for, the different types and where to purchase them. >
Grinding operations often work best with some form of wheel dressing to re-establish the wheel profile and/or recondition the wheel face. Wheel conditioning typically involves the sharpening and opening of the wheel face, while also removing dull abrasives, excessive bond, and workpiece material (loading). A sharp and open wheel face will allow maximum possible material-removal rates and reduced thermal stress on the workpiece. CDT engineers design each dresser to match your wheel topography so that it performs with superior strength and versatility. All are made with the highest quality CVD, natural diamond, synthetic diamond and combinations to maximize performance and roll life. Because they are custom manufactured, an abundance of configurations are possible.
Types of Diamond Rotary Dressers
There are two manufacturing methods for rotary dressers with several variations in setting/diamond application to best suit the customer application. Below are several examples:
1. Reverse Plated Diamond Roll
Manufactured with high accuracy molds and a tightly controlled electroplating process to deposit the nickel layer. The nickel layer holds the abrasive in place to allow for extremely complex profiles and tight tolerance work, which produce high quality surface finishes. Because of the accuracy on the front end of the process, these rolls require little to no surface conditioning, which leave sharp natural points for superior dressing, resulting in an open grinding wheel and lower grinding forces. Reverse plated rolls are ideal for continuous dress creep feed process, and complex forms like bearings, fuel injection, thread forms, and aerospace root forms.
2. Sintered Diamond Roll
Using a high temperature powdered metal process to create a tough tungsten matrix to secure the abrasive in the roll. This product is ideal for aggressive grinding and harsh working environment, while still holding tight profile tolerances and complex forms. These are all handset products, either pattern set or random set, to allow for a wide range of options on performance, surface finish, and roll life. Because of the manufacturing process, these rolls generally have shorter lead times and can usually be reworked to meet production demands. Sintered rolls are ideal for simple profile rolls to complex valve grinding assemblies.
3. Sintered CVD / Disc Dresser
These dressers use the same tough tungsten matrix as the standard Sintered rolls but are unique in the abrasive they are set with and how they are typically used. They are available using synthetic, natural, or CVD abrasive and can be set in combination to target specific performance, surface finish, and roll life. These are typically used to traverse across the grinding wheel to generate specific profiles and wheel conditions for open and free cutting grinding of the part. This style dresser is ideal for reconditioning, which can restore the roll to its original profile and tolerance in half the normal lead time and a fraction of the cost.
Where Can You Get a Diamond Rotary Dresser?
If you're looking to purchase a diamond rotary dresser, then you should know that Continental Diamond Tool Corporation is the final place to get them.
Experience
Since 1973, our family-owned company has built a reputation as a leading-edge manufacturer with a commitment to excellence.
Quality
Our engineers are highly specialized, and all our products are produced under stringent quality control standards.
Customization
We manufacture to your specific needs, providing you with specialized tools in a timely manner, with guaranteed satisfaction.
Precision
Our state-of-the-art equipment and expertise give our products some of the tightest tolerances in the industry.
Personalized Tech Support
From prototype to production, operations, or replacement tooling, our team works closely to get you the solutions you need.
Multiple Ways to Request an Estimate
Submit your project specifications and upload large files through our website: www.cdtusa.net/contact
Email details of your project with small file attachments to: info@cdtusa.net
Call our customer service team to talk through your project and discuss options: 800.443.6629
Consort Precision Diamond Featured in British Chambers of Commerce Case Study
Consort Precision Diamond Co Ltd has been featured in a case study by the British Chambers of Commerce discussing Consort's exports strategy and more.
We are pleased to share with you that Consort Precision Diamond Co Ltd has been featured in a case study by the British Chambers of Commerce. The case study has been published on the British Chambers of Commerce website and shared on their social media channels. Here is an excerpt from the article:
The Consort team is immensely proud of their geographically-diverse portfolio of customers, with the export side of their business expanding rapidly. They currently export to over 20 countries worldwide, covering Europe, USA, Canada, South America, and the Far East.
During 2019 and 2020, their international trade accounted for 51% and 63% of their turnover respectively, and 2021 figures indicate that the export side of the business will account for 70% of their revenue. Brazil, Mexico, and USA are amongst the company’s largest markets, followed by Europe.
Click here to read the full article detailing Consort's exports strategy.
In addition, Consort is proud to have been nominated regionally in the 2022 Chamber Business Awards for their exports. We would like to congratulate the award winner, Metalfacture Ltd, who has been recognized as the British Chamber of Commerce National Global Player Export Business of the Year.
Consort has also been nominated for the WCNW Chamber Business Awards in Export & International Trade. The winner for that award will be announced at the ceremony on the 11th of November.
Consort Precision Diamond Company, a subsidiary of Continental Diamond Tool Corporation since 2018, is based in North Wales. They are a manufacturing specialist dedicated to the production of diamond rotary dressers, a complimentary product to CDT's custom diamond and CBN grinding wheels and tools.
Plated Diamond Rotary Dresser Operations Expanding for Increasing Demand
Always striving to stay ahead of the curve in technology, Consort Precision Diamond is excited to announce that thier newly upgraded plating lab is up and running.
Diamond Rotary Dressers are widely recognized as the most efficient, cost effective means of dressing and truing grinding wheels to the correct tolerance, form, and condition. As industry is experiencing an increasing demand for high-accuracy, high-speed production, the need for reverse plated dressers is also increasing.
Always striving to stay ahead of the curve in technology, CDT-subsidiary Consort Precision Diamond is excited to announce that our newly upgraded plating lab is up and running.
"This plating lab expansion more than doubles our capacity to produce the high quality tight tolerance reverse plated rotary dressers used by some of the most prestigious companies in the world," says Troy Giacherio, Product Manager at Consort Precision Diamond. Stephen Noakes, Production Manager, lead the team who worked on the plating lab upgrade.
Choosing the Best Diamond Rotary Dresser
There are two types of production methods for diamond rotary dressers, sintering and plating. Consort Precision Diamond specializes in the manufacture of both types.
Sintered diamond rotary dressers are suitable for large quantities of high precision machining and many types of high hardness grinding wheels.
Reverse plated diamond rotary dressers are best suited for applications where high accuracy of profile detail and a correspondingly high quality surface finish on the component are required.
Our Commitment to Excellence
If your application calls for a Diamond Rotary Dresser, Consort Precision Diamond is committed to providing you the best tool for the job. Our service techs are skilled at helping you find the correct specifications optimized for your application. Contact us today >
Consort Precision Diamond is a subsidiary of custom superabrasive grinding wheel manufacturer Continental Diamond Tool Corporation. Learn more about Consort’s products at www.consortprecision.co.uk.
5 Factors for Best Dressing Performance
Find the perfect rotary diamond dresser for your application by considering these 5 factors. Continental Diamond Tool Limited offers decades of expertise and free consultations for customized solutions >
The intricacies of selecting the ideal rotary diamond dresser for your unique application depend on many factors like tolerance, surface finish, configuration of form, grinding machine type, and grinding wheel specification. Continental Diamond Tool (CDT) has extensive experience in designing and crafting dressing solutions that perfectly suits your needs. Customization is key. Read on to discover how tailoring a diamond rotary dresser to your process can improve grinding performance.
Plunge dressing vs. Traverse dressing
Traverse dressing and plunge dressing are two methods that employ diamond rotary dressers in precision grinding applications. Each dressing technique requires a different form to serve its unique purpose.
Traverse dressers are designed to move across the surface of a grinding wheel, gradually shaping and refreshing its profile to maintain consistent performance and geometric precision. This method is ideal for applications where maintaining a constant wheel profile is crucial, such as in high-precision cylindrical grinding.
On the other hand, plunge diamond rotary dressers are employed to create specific, intricate profiles or contours in a grinding wheel. By plunging the dresser directly into the wheel, they generate complex shapes and features with precision. These dressers are particularly valuable in applications requiring customized workpiece forms, like gear grinding or aerospace components.
Both methods play a vital role in the manufacturing industry, ensuring the optimal condition and shape of grinding wheels. This, in turn, guarantees the quality and accuracy of the finished workpieces.
DIAMOND ROTARY DRESSER TYPEs
The diamonds in Diamond Rotary Dressers are what give this technology its cutting edge. There are four unique processes that can be used to adhere the diamonds to the dresser form:
REVERSE PLATED - Reverse Plated Dressers are best suited for applications where high accuracy of profile and a correspondingly high quality surface finish on the component are required.
HANDSET SINTERED - Handset Sintered Dressers are our most commonly used type of Rotary Diamond Dresser. They cover applications where robustness is required and the general tolerance is open.
CVD SINTERED - CVD Sintered Dressers are highly resistant to chipping and fracture, and they wear evenly over the dresser’s entire length. They also have outstanding thermal stability in use.
RANDOM SET SINTERED - Random Set Sintered Dressers are perfect for applications requiring openness, tight form, and improved surface finish. They can be delivered quickly to meet urgent demand.
Sometimes called Truers or Rollers, how do you know which of these will be the best diamond rotary dresser type for your application? Especially when each of these categories contain many further variables of appropriate diamonds and setting patterns.
5 factors for proper dresser selection
Proper dresser selection starts with investigating these five factors. Every well designed dressing tool must meet the specific requirements of these areas:
TOLERANCE - Tolerance refers to the allowable deviation or variation from a specified measurement or dimension in a workpiece. In the context of dressing tools, it's essential to consider the level of precision or accuracy required in the dressing process to meet the desired workpiece tolerances.
SURFACE FINISH - Surface finish pertains to the quality and texture of a workpiece's surface after the grinding or machining process. When designing a dressing tool, you need to account for the desired surface finish, which can range from rough to smooth, as it influences the choice of abrasive grains and dressing techniques.
CONFIGURATION OF FORM - Configuration of form relates to the specific shape, contour, or profile that the dressed grinding wheel should have. It encompasses the design and geometry of the wheel, which needs to be precisely replicated by the dressing tool to achieve the desired workpiece shape or finish.
GRINDING MACHINE TYPE - The type of grinding machine used in a particular application, such as cylindrical, surface, or centerless grinding, significantly impacts the dressing tool's design. Different machines require specific dressing techniques and tools to optimize performance and precision.
GRINDING WHEEL SPECIFICATION - This factor involves the characteristics and properties of the grinding wheel to be dressed. It encompasses details like wheel diameter, abrasive type, grain size, bonding material, and other specifications. The dressing tool must be compatible with these wheel specifications to ensure effective and efficient dressing.
Considering these factors when designing a dressing tool is crucial to achieving the desired precision, surface finish, and workpiece quality in various grinding applications. Correct specification involves the appropriate design, selection and placement of diamonds in a way that takes into account all the factors affecting the individual customer's application. It cannot be achieved by choosing from a small range of general purpose dresser types. Customization is required.
Our team at CDT has decades of experience in specifying and manufacturing Rotary Diamond Dressers for individual applications is second to none. Our processes are what make the Consort Precision™ Diamond Rotary Dresser truly exceptional, winning awards in the industry. We now manufacture and ship our custom diamond rotary dressers from both Europe and North America. The best part? It you costs nothing to consult with us—so contact us first to find the very best fit for your project.