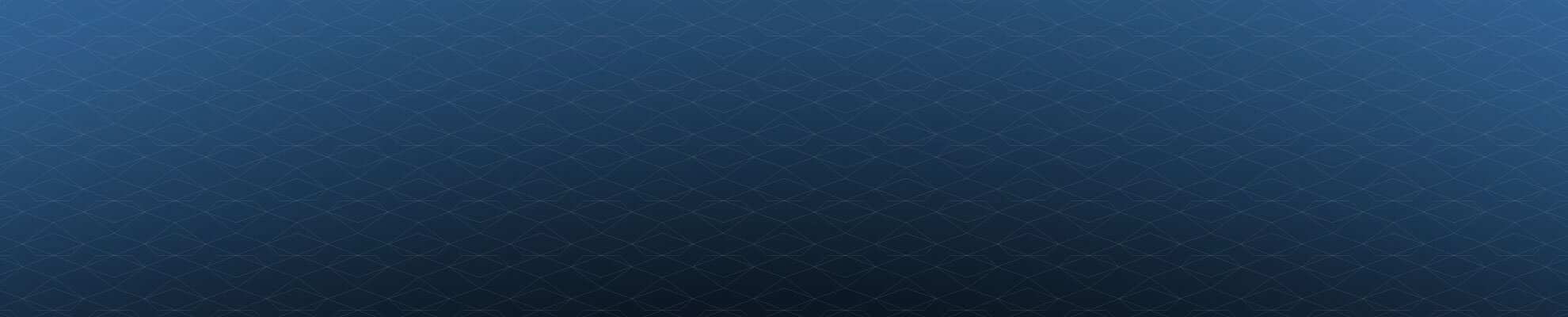
News and Resources
Browse by Category
Browse by Product
- All Dressing Products
- All Grinding Products
- CBN-Diamond Superabrasives
- Conventional Abrasives
- Diamond Lapping Compounds
- Diamond Rotary Dressers
- Diamond Stationary Dressers
- Hybrid Bond Grinding Tools
- Metal Bond Grinding Tools
- Plated Grinding Tools
- Resin Bond Grinding Tools
- Vitrified Bond Grinding Tools
Core Matters: How Different Wheel Body Materials Impact Grinding
Learn how grinding wheel core materials like steel, aluminum, and carbon fiber impact performance, precision, and cost to optimize your grinding applications.
When using superabrasive grinding wheels in precision manufacturing, selecting the right abrasive, bond type, and wheel core material is critical for optimal grinding performance and wheel life. While abrasives and bond types often take center stage, the wheel core can be equally important. The core material is the foundation that provides structural support and stability. The right core material ensures high performance while preventing machine strain, excessive grinding wheel wear, and unnecessary cost. But how do you determine the best core material for your specific needs?
In Episode 10 of The Grinding Chronicles, CDT Engineering Manager Jeff Wirth breaks down the essential properties of core materials and how they influence grinding applications. Watch the video or read the article below to learn how to choose the best option for your application.
The Grinding Chronicles - Episode 10
Selecting the Right Core Material for Grinding Wheels
The core of a superabrasive grinding wheel does more than just hold the abrasive—it directly impacts machine efficiency, grinding precision, and tool longevity. Choosing the right core material not only optimizes performance but also helps prevent unnecessary damage to the wheel, machine, and workpiece while enhancing operator safety.
Common core materials for superabrasive grinding wheels include metals—such as steel, aluminum, and copper—as well as non-metals like ceramics and resin composites. Ceramic or vitrified cores are commonly found in conventional abrasive grinding wheels and are also used in some superabrasive grinding wheels. Resin composite cores may be made from materials like bakelite, abrasive composites, or carbon fiber. Each of these materials has unique properties that affect grinding performance, and understanding their characteristics helps manufacturers make more informed decisions.
Understanding Core Material Properties
Density – Defined as mass per unit volume, density directly affects the weight of a grinding wheel. Heavier cores put added stress on machines and spindle bearings, which is why large-diameter grinding wheels are often designed with lighter core materials like carbon fiber, bakelite, or ceramic. An overly heavy wheel can reduce machine longevity, increase energy consumption, and pose handling risks for operators, making weight an important consideration for both performance and safety.
Expansion – Core materials expand due to heat and mechanical forces, which can impact grinding accuracy. Minimizing expansion is crucial for applications with tight tolerances, as it helps prevent wheel distortion and ensures consistent precision. Expansion occurs in two forms:
Mechanical Expansion: At high speeds, some core materials naturally expand due to centrifugal forces. Materials with high tensile strength resist this growth, maintaining stability and accuracy over time.
Thermal Expansion: Heat generated during grinding can cause materials to expand, leading to dimensional changes and reduced precision. Materials with low thermal expansion coefficients are essential for consistently achieving tight tolerances.
For high-speed and high-precision grinding applications, grinding wheels with cores made from high-tensile steel, carbon fiber, or vitrified ceramic often perform better. These materials minimize mechanical and/or thermal expansion, ensuring consistent performance, reduced deformation, and greater accuracy under extreme conditions.
Thermal Conductivity – This property determines how well a core material dissipates heat. Efficient heat transfer prevents thermal damage (burning) to the workpiece, improves surface quality, and extends tool life. Metal materials like Copper and Aluminum with high thermal conductivity remove heat, leading to lower wear and improved performance in high heat applications such as fluting drills.
Modulus of Elasticity (MOE) – This measurement indicates a material’s ability to resist deformation under stress. A higher MOE means the material is stiffer and less likely to flex or deform. Steel has a very high MOE. This can be beneficial for applications with high grinding forces that require tight tolerances, as a flexible core can introduce inconsistencies in grinding performance.
Comparing Core Materials: Strengths and Weaknesses
Each core material offers specific advantages and drawbacks. Here’s how some of the most common materials compare:
Steel is strong, durable, and resistant to mechanical expansion. However, its heavy weight can strain machinery.
Aluminum is lighter and often more affordable than steel, with higher thermal conductivity and resistance to corrosion. However, it has significantly higher thermal expansion compared to steel and other materials.
Copper offers excellent thermal conductivity and a high modulus of elasticity (MOE), but its weight and cost make it less suitable for large grinding wheels.
Ceramic is lightweight, cost-effective, and resistant to expansion, but low thermal conductivity and high stiffness or brittleness can be a drawback.
Resin composites, including bakelite, are affordable and lightweight. However, they lack stiffness and high thermal conductivity, making them more susceptible to expansion and heat buildup in high-force grinding applications.
Carbon fiber is ideal for demanding applications due to its high stiffness and low weight. However, it tends to trap heat and is more expensive than other materials.
Choosing the Right Core Material for Your Application
Selecting the best core material depends on several factors, including the type of grinding being performed, the machine’s limitations, and cost considerations. For example:
Flute grinding and medical drill bits operate at traditional speeds with lower grinding forces. This means that a wide variety of core materials can be used without significant performance issues. In these cases, ceramic cores are often recommended because they provide an excellent balance of cost and functionality.
High-speed applications like camshaft grinding generate significant heat and grinding forces. This makes high-stiffness materials like carbon fiber or high-tensile steel essential to be able to perform effectively and safely.
Hybrid or combination cores are an innovative solution for balancing weight, stiffness, and cost. This approach involves layering or combining different materials to optimize performance while keeping costs manageable. For instance, a steel core can be reinforced with carbon fiber to reduce weight without sacrificing strength.
Practical Considerations in Core Material Selection
Beyond material properties, cost plays a major role in selecting the right core material for grinding wheels. While core materials like carbon fiber and vitrified ceramic are both resistant to mechanical and thermal expansion and lighter weight, they come at very different price points. Once all process requirements are met, cost is usually the deciding factor, as manufacturers balance performance needs with material costs to avoid unnecessary expenses.
Budget-Friendly Options – Ceramic and resin composites provide cost-effective solutions for applications with lower grinding forces and minimal heat generation. These materials perform well in traditional grinding operations without adding unnecessary expense.
Mid-Range Solutions – Aluminum and standard steel cores offer a balance between affordability and durability. These materials are commonly used in medium-duty grinding applications where moderate strength and thermal properties are required, optimizing cost per part without sacrificing performance.
Premium Core Materials – High-tensile steel and carbon fiber provide top-tier performance, making them ideal for high-speed and high-force applications. While their higher price point increases the initial cost of the grinding wheel, their longevity and reliability often justify the investment by reducing long-term cost per part through extended tool life and efficiency gains.
When selecting a core material, it is essential to consider not just the upfront cost but also long-term savings from reduced machine wear, improved grinding efficiency, and longer tool life. CDT’s engineering team can help assess cost-effectiveness based on your specific grinding application, ensuring the best balance between performance and cost per part.
Optimize Your Grinding Wheel Performance with CDT
Choosing the right core material is critical for achieving consistent, high-performance grinding results. Whether you're working with grinding applications for heavy-duty industrial engine components or high-precision medical tool manufacturing, the engineering team at Continental Diamond Tool is ready to assist in customizing a grinding wheel with the materials that are best for your needs.
If you have questions about selecting the best core material for your specific application, CDT’s engineers are here to help. Reach out to TheGrindingChronicles@cdtusa.net for expert advice.
Check out more videos from The Grinding Chronicles and follow CDT on Linked In for the latest news in grinding technology.
An Essential Guide to Grinding Process Optimization for Boosting Performance in Precision Manufacturing
Optimize your grinding process with expert tips on speeds, feeds, Q-prime, and advanced bond technology to boost efficiency in precision manufacturing.
To stay competitive in precision manufacturing, grinding operations require continuous improvement in performance and efficiency. Understanding the factors that influence grinding, such as speeds, feeds, and material removal rates, can significantly impact your results. In this comprehensive guide from Continental Diamond Tool, Product Engineer Thi Dang and Engineering Consultant Jon VanSant share their expertise as they unpack the essential elements of grinding process optimization. Episode 8 of The Grinding Chronicles offers valuable insights into maximizing Q-prime, balancing G ratios, and selecting the right grinding wheel speeds. Whether you’re looking to refine your current operations or upgrade to the latest in bond technology, our engineering team’s breakdown outlines the key factors you need to consider to enhance your grinding processes. Watch the video or read on to discover practical tips and advanced strategies for getting the most out of your grinding tools.
The Grinding Chronicles - Episode 8
Unlocking the Secrets to Optimizing Your Grinding Process
In this article, you will learn the essentials for optimizing your grinding process, focusing on the metrics that matter most for achieving peak performance. From understanding the basics of speeds and feeds to exploring advanced bond technology, this guide provides actionable insights for any precision manufacturing operation. Whether you're new in the field or looking to enhance your current practices, this informative article from The Grinding Chronicles team offers valuable knowledge to help you get ahead in the industry.
Understanding the Basic METRICS in GRINDING
One of the first considerations when optimizing a grinding process is understanding the basics—speeds, feeds, and material removal rates. These elements are fundamental to the grinding process and play a crucial role in determining the efficiency and quality of the finished product.
Speeds and Feeds:
Speeds refer to the rotational speed of the grinding wheel, typically measured in surface feet per minute (SFM). Feeds, on the other hand, relate to the rate at which the workpiece is fed into the grinding wheel. Together, these parameters influence the rate of material removal, surface finish, and the overall efficiency of the grinding process.
It's essential to understand that faster isn't always better. While higher speeds can increase material removal rates, they can also lead to increased wheel wear and the potential for thermal damage to the workpiece. Therefore, finding the optimal balance between speed and feed is key to maintaining both efficiency and quality.
Material Removal Rate (Q-prime):
Q-prime, or material removal rate, is a critical measure of grinding performance. It is calculated by multiplying the depth of cut by the feed rate, resulting in the amount of material removed per unit time. Higher Q-prime values typically indicate shorter cycle times, which can significantly enhance productivity.
However, achieving high Q-prime values requires careful consideration of other factors, such as wheel wear and the quality of the finished surface. A high Q-prime might reduce cycle times, but if it leads to excessive wheel wear or poor surface quality, the overall efficiency of the process may suffer. Thus, optimizing Q-prime involves balancing it with other critical parameters, such as the G ratio.
The G Ratio:
The G ratio is another vital metric in grinding. It is defined as the volume of material removed from the workpiece divided by the volume of wheel wear. A high G ratio indicates efficient grinding, where more material is removed with less wheel wear. However, similar to Q-prime, achieving an optimal G ratio requires balancing various factors.
Maximizing Q-prime WHILE Balancing the G Ratio
Maximizing Q-prime while maintaining a high G ratio is the key to optimizing grinding processes. To achieve this balance, it’s important to consider the following:
Wheel Speed: Higher wheel speeds can lead to increased wheel wear due to elevated temperatures. Therefore, it’s crucial to find an optimal speed that maximizes material removal without excessively wearing the grinding wheel.
Coolant Delivery: Proper coolant delivery is essential in controlling the temperature during grinding. Efficient coolant systems help dissipate heat, reducing thermal damage to the workpiece and wear on the grinding wheel. This, in turn, helps maintain a high G ratio.
Machine Stiffness and Power: The stiffness of the grinding machine and the power of the spindle also play significant roles. Machines with low power or poor stiffness may limit the achievable Q-prime and G ratio, restricting the overall efficiency of the grinding process.
By carefully considering these factors, manufacturers can optimize their grinding operations to achieve both high Q-prime and G ratios, leading to improved productivity and efficiency.
The Evolution of Bond Technology
Bond technology plays a critical role in the performance of grinding wheels, particularly in their ability to achieve high Q-prime and G ratios. The history of bond technology in grinding wheels is a testament to the continuous advancements that have been made in this field.
A Look Back:
In the 1960s, phenolic resin bonds were the standard, offering Q-prime values of around three. By the 1970s, the introduction of polyimide bonds pushed Q-prime values to around five. The year 2000 marked another leap with hybrid bonds, which increased Q-prime to approximately seven.
Today, we are capable of removing material at rates between 10 and 15, thanks to the latest advancements in bond technology. This evolution highlights the importance of continuously upgrading to the latest bond technology to stay competitive in the market.
Introducing CDT's EVO Hybrid Bond:
Continental Diamond Tool has been at the forefront of these advancements with its EVO Hybrid Bond. Released earlier this year, the EVO Hybrid Bond represents a significant step forward in bond technology, offering the ability to achieve Q-prime values over 10 without compromising the G ratio.
The development of the EVO Hybrid Bond was driven by the need for a bond system that could grind aggressively while minimizing wear and maintaining excellent corner retention. This bond was also designed with thermal conductivity in mind, to transfer heat away from the part and prevent damage to the diamond, which is sensitive to high temperatures. Learn more about CDT’s EVO Hybrid Bond product here.
Practical Tips for Optimizing Your Grinding Process
Now that we’ve covered the theoretical aspects of grinding optimization, let’s look at some practical tips that can help you apply this knowledge to your operations:
Evaluate Your Current Operations: Start by assessing your current grinding processes. Measure your Q-prime and G ratio to establish a baseline. Identify areas where improvements can be made, whether in speed, feed rate, or wheel selection.
Invest in the Latest Technology: Consider upgrading to the latest bond technology, such as CDT’s EVO Hybrid Bond. Newer bonds can significantly improve your material removal rates and reduce wheel wear, leading to better overall efficiency.
Optimize Coolant Delivery: Ensure that your coolant system is operating efficiently. Proper coolant delivery is essential for controlling temperatures and reducing thermal damage, which can extend the life of your grinding wheels and improve the quality of your finished products.
Regularly Maintain Equipment: Regular maintenance of your grinding machines is crucial. Ensure that your machines are running at optimal stiffness and power to maximize performance and avoid limitations in Q-prime and G ratios.
Train Your Team: Make sure your team is trained on the latest grinding techniques and technologies. A well-informed team can make better decisions on the shop floor, leading to improved productivity and efficiency. At Continental Diamond Tool, our application engineers are here to help. We regularly connect with our customers to fine-tune their equipment and train their operators on the optimized speeds and feed rates to use with our grinding wheels.
Optimizing grinding processes is essential for staying competitive in precision manufacturing. By understanding and balancing key factors like Q-prime, G ratio, and wheel speed, manufacturers can significantly enhance their grinding operations. Continental Diamond Tool’s latest advancements, including the EVO Hybrid Bond, provide valuable tools for achieving these goals. Whether you’re looking to improve your current processes or invest in new technologies, the insights provided in this guide offer a clear path to optimizing your grinding operations. Implement these strategies to ensure your manufacturing processes are both efficient and effective, helping you to stay ahead in a demanding industry.
How to Diagnose Surface Pattern Problems in Grinding
Learn how to diagnose and fix common surface pattern problems in precision grinding with expert insights from CDT's Senior Product Engineer, Paul Christy.
Many precision grinding operations require impeccable surface finishes for both function and aesthetics. Addressing surface pattern problems is vital for ensuring the quality of the final product, eliminating waste, and controlling costs. In this detailed overview, we expand on the insights provided by Paul Christy, Senior Product Engineer at Continental Diamond Tool, as he explains how to troubleshoot and fix common causes of surface patterns. In Episode 7 of The Grinding Chronicles, Paul covers the complexities of surface patterns caused by various types of vibrations, runout, and servo system instability. Watch Paul’s video or read on to learn more about identifying and addressing these issues to optimize your grinding operations.
The Grinding Chronicles - Episode 7
Surface Pattern Troubleshooting Guide
Surface pattern problems in grinding can significantly impact the quality and precision of your workpieces. Diagnosing and resolving these issues requires a deep understanding of the underlying causes and appropriate troubleshooting techniques. This article explores common causes of surface patterns in grinding and provides expert insights into their diagnosis and elimination.
Self-Excited Vibration
One of the primary causes of surface pattern problems is self-excited vibration, which occurs at the natural frequency of the machine system. This type of vibration indicates that some component within the machine—such as the spindle, the part, or the dresser—is being excited. The resulting oscillating pattern is called chatter. Notably, this vibration only manifests when the grinding wheel and the workpiece (or the wheel and the dresser) are in contact.
Self-excited vibration results from a lack of sufficient component stiffness. The key to mitigating this issue lies in increasing the machine's stability, which requires a greater machine stiffness compared to the process stiffness. There are three main process variables that can be adjusted to help eliminate self-excited vibration:
Velocity of the Workpiece: Lowering the workpiece's speed can reduce process stiffness.
Velocity of the Grinding Wheel: Decreasing the grinding wheel's speed similarly lessens process stiffness.
Width of Contact: Reducing the contact width between the grinding wheel and the workpiece can also help.
By strategically lowering one or more of these variables, you can effectively diminish the impact of self-excited vibration.
Forced Vibration
Forced vibration occurs at a frequency corresponding to a driving force within or outside the machine. Common examples of such driving forces include unbalanced rotating bodies and pump pulsations. This type of vibration can often be diagnosed using a process of elimination. By sequentially turning on and off all rotating bodies within the machine, you can identify the source of the vibration when it ceases upon the deactivation of a specific component.
Runout
Runout is a prevalent issue in grinding due to the inherent imperfections of rotating components. It occurs when the outer surface of a rotating component does not maintain perfect concentricity with its axis or center line. Specifically, runout in a traversing diamond roll can create a pattern in the grinding wheel, which is then transferred to the workpiece. This pattern typically manifests as angled parallel lines, known as Barber Pole or Roping Patterns.
To address surface patterns caused by runout, it is essential to identify the optimal dresser and wheel RPMs. Varying the diamond roll speed during dressing can reduce the likelihood of pattern formation on the grinding wheel, preventing its transfer to the workpiece. Another effective solution is lapping the diamond roll to the machine's spindle bearings, thereby eliminating runout.
Servo System Instability
Servo system instability is another potential source of surface patterns on workpieces. The servo system controls the movement accuracy of machine components, using digital feedback to ensure precise positioning. Mechanical decoupling within components such as ball nuts, couplings, bearing support units, or scale mountings can create discord within the servo system. This results in oscillations as the system struggles to determine the correct position, leading to surface patterns on the workpiece.
Solving servo system instability typically requires sophisticated instrumentation and physics-based analysis. Iterative process changes alone are unlikely to resolve this complex issue.
Key Takeaways in Mastering Surface Finish
Diagnosing and fixing surface pattern problems in grinding necessitates a thorough understanding of the potential causes and their specific remedies. Whether dealing with self-excited vibration, forced vibration, runout, or servo system instability, targeted adjustments and precise troubleshooting are essential for maintaining the quality and precision of your grinding operations.
For more detailed information and expert guidance, refer to Episode 7 of The Grinding Chronicles, where Paul Christy shows specific measures you can take to diagnose and eliminate surface pattern problems. If you are experiencing surface patterns similar to those discussed in this article and require further assistance, do not hesitate to contact the Continental Diamond Tool engineering team at TheGrindingChronicles@cdtusa.net.
Understanding and addressing these grinding challenges will enhance your operational efficiency and ensure the superior quality of your manufactured products.
Continental Diamond Tool Enters Strategic Partnership with Krebs & Riedel
Continental Diamond Tool Corporation partners with Krebs & Riedel, becoming the exclusive source for their abrasive products in North America. Learn more about the collaboration in this article.
New Haven, Indiana – April 30, 2024 – Continental Diamond Tool Corporation (CDT) proudly announces its partnership with Krebs & Riedel, a global leader in the abrasives industry. This collaboration positions CDT as the exclusive North American source for Krebs & Riedel abrasive products within the USA, Canada, and Mexico.
Nick Viggiano, President of Continental Diamond Tool (left), and Florian Riedel, Managing Director of Krebs & Riedel.
Erik Van Meter, Senior Product Manager of Conventional Abrasives at Continental Diamond Tool and Krebs & Riedel’s official representative, expresses enthusiasm about the new partnership, stating, "We are thrilled about the high-quality products Krebs & Riedel will bring to the table. They are a well-respected name in conventional grinding wheels and have products for many industrial grinding markets which include automotive, aerospace, gear and medical."
The collaboration between CDT and Krebs & Riedel signifies a partnership deeply rooted in a shared commitment to excellence. For more than half a century, Continental Diamond Tool Corporation has consistently delivered technically superior precision grinding products across a variety of industries. As a thriving second-generation family business, CDT’s commitment to innovation and quality is reflected in its state-of-the-art North American manufacturing facility, which is undergoing a sizable expansion to cater to new product development and meet diverse customer needs. With this and a growing subsidiary in the United Kingdom, it has solidified its status as a premier worldwide manufacturer of custom superabrasive grinding wheels and diamond dressing tools.
Similarly, Krebs & Riedel is a family-owned enterprise headquartered in Bad Karlshafen, Germany, since 1885. It has a proud century-long legacy in providing quality abrasive products globally. With over 30 distributors and subsidiaries, K&R's dedication to customer satisfaction aligns seamlessly with CDT's founding principles. This partnership promises cutting-edge solutions and unwavering commitment to superior products and customer service in the abrasive products landscape. In this strategic move, CDT and Krebs & Riedel are poised to tackle the most critical tooling requirements of a growing market of customers.
“This partnership marks an exciting chapter for Continental Diamond Tool Corporation as we join forces with Krebs & Riedel to expand our product offerings in North America,” said Nick Viggiano, President of CDT. “We are proud to align with Krebs & Riedel's esteemed reputation and look forward to delivering exceptional abrasive products and unparalleled service to our customers across the continent and beyond.”
“With CDT we have found the partner who complements our high-performance products with superior service. From the first meeting we felt the same level of professionality and passion for grinding. I am convinced that our customers in North America will feel the same,” said Florian Riedel, Managing Director of Krebs & Riedel.
For more information about Continental Diamond Tool Corporation and its comprehensive range of precision grinding products, including those from Krebs & Riedel, please visit www.cdtusa.net/products.
Continental Diamond Tool Corporate Office in New Haven, Indiana, USA
About Continental Diamond Tool Corporation:
Established in 1973, Continental Diamond Tool Corporation (CDT) is a premier manufacturer of precision tooling solutions for a variety of global industries. With a legacy of technical expertise and innovation, CDT is renowned for its custom superabrasive grinding wheels and diamond dressing tools. Headquartered in New Haven, Indiana, CDT operates from a state-of-the-art 200,000 sq. ft. manufacturing facility dedicated to delivering high-quality products and exceptional customer service.
Krebs & Riedel Head Office in Bad Karlshafen, Germany
About Krebs & Riedel:
Family owned since its start in 1885, Krebs & Riedel (K&R) has been a prominent global player in the abrasive products industry. With a vast network of over 30 distributors, subsidiaries, sales companies, and representatives worldwide, Krebs & Riedel is renowned for its quality abrasive products and commitment to customer satisfaction.
Conventional Abrasives vs. Superabrasives
In Episode 4 of The Grinding Chronicles learn how the properties of common abrasives impact wheel life and cutting efficiency. Avoid pitfalls with industry expert Jon VanSant.
In Episode 4 of The Grinding Chronicles, Continental Diamond Tool Engineering Consultant Jon VanSant investigates the history of common abrasive materials and their key differentiating characteristics that impact wheel life, cutting performance, and efficiency. Using the wrong abrasive for your application can significantly increase your cost per part. Watch Jon’s video or read the article below to learn the differences between conventional abrasives and superabrasives.
The Grinding Chronicles - Episode 4
Understanding Abrasive Evolution
In the early 1800s, precision grinding relied on naturally occurring abrasives like emery. Fast forward to the late 19th century, and we witnessed pivotal developments with the advent of "Carborundum" or silicon-carbide by Dr. Edward Acheson in 1891, followed by the patenting of 'Alundum' or aluminum oxide by Aldus Higgins in 1904. The landscape changed once again with the introduction of synthetic diamond in 1954 and cubic boron nitride (cBN) in 1957, marking the emergence of superabrasives. Although superabrasives were first synthesized in the 1950’s, it took two decades before commercial products became available.
Distinguishing Characteristics
To understand the difference between conventional abrasives and superabrasives, let’s examine three key characteristics: hardness, thermal conductivity, and friability.
Hardness: An important consideration in abrasive selection, superabrasives like cBN and Diamond demonstrate superior hardness compared to Aluminum Oxide and Silicon Carbide. This is part of what makes superabrasives super, and makes them particularly efficient when grinding extremely hard materials.
Thermal Conductivity: Enhanced thermal conductivity facilitates efficient heat transfer during grinding operations, ensuring minimal damage to the workpiece. This is critical where surface finish is concerned.
Friability: Friability reflects the fracture or impact toughness of an abrasive and underscores another crucial aspect. Analysis reveal a substantial disparity between conventional and superabrasives, with the latter exhibiting remarkable compression fracture strength. When comparing the compression fracture strength of diamond and aluminum oxide at a particle size of 400 microns, there is a 10:1 difference between the conventional abrasive and the superabrasive.
Performance Metrics
Moving beyond physical attributes, an examination of performance metrics such as cut, wear, and dressing efficiency further demonstrates superabrasives prowess.
Cutting Efficiency: Superabrasives like Diamond and cBN require less power and force for cutting operations, ensuring efficient material removal.
Wear Resistance: Superabrasives demonstrate significantly higher wear resistance, leading to prolonged wheel life and reduced downtime when compared to conventional abrasives.
Dressing Efficiency: Superabrasives also excel when considering downtime for dressing since they maintain dressing efficiency over extended periods. In some cases, we have seen up to 20 times the parts per dress. With less frequent dressing comes more consistent performance. Plus, you’re only taking off a tenth of the material in dressing, so your wheel lasts much longer.
Cost Considerations
Superabrasives, with their many advantages, do come with a substantial up-front investment. Even so, many companies see sustainable returns.
Long-Term Value: Superabrasives offer enhanced productivity and cost-effectiveness that often results in lower cost per part over time.
Application Considerations: Recognizing that not every application warrants a superabrasive grinding wheel, factors such as machine tools, fluid compatibility, and work volume must be considered. Superabrasives are most cost effective in high volume, extremely demanding applications.
Expert Guidance
Thank you for joining us on this exploration of grinding wheel abrasives. If you would like help deciding which abrasive would work best to optimize your grinding process, don't hesitate to reach out to our engineering team at TheGrindingChronicles@CDTUSA.net. Until next time, check out additional insights and discoveries on other episodes of The Grinding Chronicles.
Understanding the Distinction Between CBN and Aluminum Oxide Abrasives
Uncover the secrets behind top-notch results in grinding and machining of tough steels and metals. Discover the unique properties of Cubic Boron Nitride (CBN) and Aluminum Oxide and learn how to choose the right abrasive for optimal efficiency and precision.
Are you ready to explore the fascinating world of abrasives? In manufacturing, we often encounter Superabrasives and Conventional abrasives. In the Superabrasives corner, we have Diamond and Cubic Boron Nitride (CBN), and their common Conventional abrasive counterparts are Silicon Carbide and Aluminum Oxide. Each serves a specific purpose. What makes CBN and Aluminum Oxide stand out is their exceptional ability to tackle those stubborn steels and metals that can't stand Carbon.
In this blog, we'll explore the properties and applications of CBN and Aluminum Oxide abrasives. Discovering their unique characteristics will help you choose the right abrasive for your specific machining needs, ensuring efficiency and top-notch results. Whether you're working with hardened steels or softer metals, the right abrasive is the key to achieving your desired outcome in grinding and machining. So, let's dive in and unlock the true potential of CBN and Aluminum Oxide abrasives.
What is CBN?
CBN is a synthetic Superabrasive known for its incredible hardness, high thermal conductivity, and thermal stability. Originally released with the trade name Borazon from GE Superabrasives, its cubic crystal lattice structure is similar to Diamond, giving it remarkable abrasive properties. With a hardness close to 10 on the Mohs scale, CBN excels in machining tough materials that require precision grinding. Its chemical composition and high thermal stability prevents chemical reactions and premature breakdown under high temperatures, when grinding ferrous metals and high-temperature alloys. What's more, because CBN doesn't react with ferrous materials, it doesn’t alter or change their properties resulting in longer life in use when ground with CBN.
CBN is a game-changer when grinding hardened ferrous alloys or super alloys that are sensitive to heat. It efficiently grinds hardened steels while maintaining accuracy and surface finish. Plus, it's a favorite for grinding ferrous metals like cast iron and stainless steel, ensuring clean and precise results without chemical alterations. CBN is a must-have tool for achieving precise and efficient outcomes in critical machining tasks.
What is Aluminum Oxide?
Aluminum Oxide, also known as alumina, is a versatile Conventional abrasive. With high hardness and toughness, it is available in various grit sizes, making it perfect for a wide range of machining and finishing applications. Though not as hard as CBN, Aluminum Oxide is fantastic for soft metals, wood, and non-ferrous materials. While it may not match the precision of Superabrasives, it's still a reliable choice for many tasks.
In the machining industry, Aluminum Oxide is the go-to for grinding soft metals like aluminum, brass, and copper. It performs beautifully with non-ferrous materials such as bronze and titanium, without causing any chemical interactions. Its role in achieving desired surface finishes across various industries, from automotive to aerospace, is unparalleled.
Key Differences Between CBN and Aluminum Oxide Abrasives
While CBN and Aluminum Oxide both play significant roles in grinding and machining operations, they have many distinct properties that set them apart.
Crystal Structure and Hardness: CBN's crystal lattice structure is similar to Diamond, resulting in exceptional hardness and wear resistance. Aluminum Oxide, while still hard, has a lower hardness than CBN, making it more suitable for soft metals and certain alloys.
Heat Resistance and Thermal Conductivity: CBN exhibits superior heat resistance and thermal conductivity compared to Aluminum Oxide, making it perfect for grinding high hardness and heat sensitive alloys.
Material Compatibility and Reactivity: Both CBN and Aluminum Oxide are chemically inert with ferrous materials whereas Diamond and Silicon Carbide are not, thus why they are the abrasives for ferrous metals.
Cost and Practicality: CBN grain costs significantly more than Aluminum Oxide grain, resulting in higher grinding wheel prices. Because of higher hardness and better thermal conductivity, CBN wheels can provide lower grinding costs in applications where high workpiece hardness and thermal properties need to be maintained. In cases of grinding soft steels and low volume production, the lower wheel price of Aluminum Oxide makes it a more competitive option.
Safety Considerations and Handling
Whether you choose CBN, Aluminum Oxide, or another solution for your abrasive, ensuring safety during grinding and finishing processes is essential. Proper machine guarding, eye and respiratory protection, proper dust/mist extraction, and careful handling and storage of abrasives are crucial to protect workers and maintain a clean and safe work environment.
Selecting the Right Abrasive for Specific Applications
Choosing the right abrasive for your specific machining needs is vital to achieving optimal results. Making an informed decision will ensure efficient, accurate, and cost-effective grinding and finishing processes. Some factors to consider include:
Workpiece Material Characteristics: Soft metals like aluminum, brass, copper, and mild steels may need moderate hardness abrasives like Aluminum Oxide to prevent excessive material removal, while harder materials like hardened steels and high-temperature alloys such as inconel and hardened Stainless Steel require abrasives with superior hardness and high thermal conductivity like CBN for precise and efficient cutting and grinding.
Machining Operations and Efficiency: Superabrasives like CBN are preferred for high-precision tasks where tight tolerances and maintaining material properties are paramount, while conventional abrasives like Aluminum Oxide offer lower cost solutions for general grinding of mild steel and soft metals.
Surface Finish and Material Removal Rates: Superabrasives like CBN excel in production applications of hardened steels and Superalloys that are sensitive to heat, , while conventional abrasives like Aluminum Oxide are effective in low volume applications and for grinding of soft metals.
Tooling and Machinery Considerations: Abrasive selection also needs to account for machinery and tooling capabilities. The truing and dressing of Superabrasive and Conventional Abrasive grinding wheels can be different and require different tools (stationary or rotary dressers of different configurations). Because of the difference in hardness between CBN and Alumina, Alumina being much lower, the amount of grinding debris resulting from wheel wear during grinding can be 100-300 x’s greater with the conventional wheel, which in turn needs to be disposed of. .
Both CBN and Aluminum Oxide abrasives offer distinct advantages in grinding and machining. Considering their unique properties with specific application requirements will lead to efficient and precise processes, ensuring optimal results and safety in the workplace. And if you ever need assistance, our grinding experts at CDT are here to help. Whether it's Superabrasives or Conventional abrasives, we can help find the perfect solution for your process.