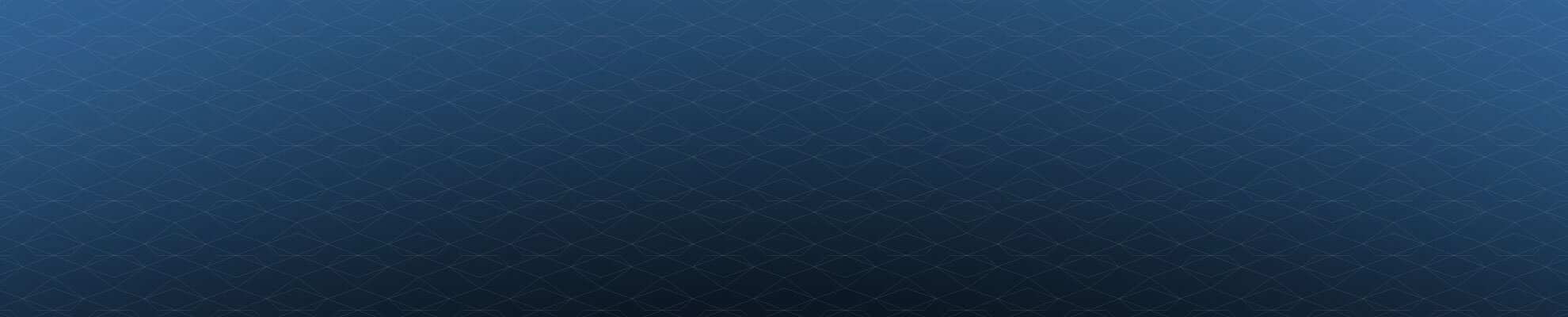
News and Resources
Browse by Category
Browse by Product
- All Dressing Products
- All Grinding Products
- CBN-Diamond Superabrasives
- Conventional Abrasives
- Diamond Lapping Compounds
- Diamond Rotary Dressers
- Diamond Stationary Dressers
- Hybrid Bond Grinding Tools
- Metal Bond Grinding Tools
- Plated Grinding Tools
- Resin Bond Grinding Tools
- Vitrified Bond Grinding Tools
Lapping the Competition in Face Grinding
Quality and precision are essential in complex, face grinding operations. CDT has fixed abrasive grinding wheels for fine grinding, double-disk grinding, blanchard grinding and more.
Quality and precision are essential in complex, face-grinding operations. Whether your job requires fine grinding, double disc grinding, blanchard grinding, flat honing, rotary surface, or insert grinding wheels, you need a high performance tool. The right wheel will minimize costs while providing superior results.
With a custom fixed abrasive grinding wheel, you should expect:
Decreased Cycle Times
Scrap Reduction
Increased Production
Reduced Spindle Wear
Versatility
Cycle time reduction means cost savings for your business. Your processes will be more efficient with less scrap. Your team can produce more output for the same effort. Plus, we'll work to extend the life and functionality of your tools. Often you can grind a broader range of materials with the same wheel. Download brochure.
How do we do it?
At Continental Diamond Tool, our engineers work with your manufacturing team to design, test, and build custom tools specific to your industry's process. We calculate the best grit size, bond type, and grain type to optimize the performance of your machine. The grit size of the diamond and CBN abrasive grains used in our wheels is based on the application and required surface quality. We also use grain types that differ in their characteristics (friable, blocky, free cutting, etc.) to achieve the most superior performance.
With more than 45 years experience in superabrasive manufacturing, we supply products that are compatible with all of industry's most popular machines: Stahli, Peter Wolters/Lapmaster, Viotto, Koyo, Blanchard, Gardner, Agathon, Wendt, Supfina, DCM, EWAG, Coborn, and more.
CDT's fixed abrasive wheels in diamond and CBN can be produced with grit sizes from 80 to 800. Bonds available include resin, cold-pressed vitrified, metal, and hybrid. Our state-of-the-art equipment and expertise allow us to produce some of the tightest tolerances in the industry. We also adhere to stringent quality control standards to ensure that your grinding wheels match or exceed the quality of life of your current tooling, guaranteed.
Our customer service team is available to talk through your face grinding project and provide a free quote through our website online form or call 800-443-6629.
5 Factors for Best Dressing Performance
Find the perfect rotary diamond dresser for your application by considering these 5 factors. Continental Diamond Tool Limited offers decades of expertise and free consultations for customized solutions >
The intricacies of selecting the ideal rotary diamond dresser for your unique application depend on many factors like tolerance, surface finish, configuration of form, grinding machine type, and grinding wheel specification. Continental Diamond Tool (CDT) has extensive experience in designing and crafting dressing solutions that perfectly suits your needs. Customization is key. Read on to discover how tailoring a diamond rotary dresser to your process can improve grinding performance.
Plunge dressing vs. Traverse dressing
Traverse dressing and plunge dressing are two methods that employ diamond rotary dressers in precision grinding applications. Each dressing technique requires a different form to serve its unique purpose.
Traverse dressers are designed to move across the surface of a grinding wheel, gradually shaping and refreshing its profile to maintain consistent performance and geometric precision. This method is ideal for applications where maintaining a constant wheel profile is crucial, such as in high-precision cylindrical grinding.
On the other hand, plunge diamond rotary dressers are employed to create specific, intricate profiles or contours in a grinding wheel. By plunging the dresser directly into the wheel, they generate complex shapes and features with precision. These dressers are particularly valuable in applications requiring customized workpiece forms, like gear grinding or aerospace components.
Both methods play a vital role in the manufacturing industry, ensuring the optimal condition and shape of grinding wheels. This, in turn, guarantees the quality and accuracy of the finished workpieces.
DIAMOND ROTARY DRESSER TYPEs
The diamonds in Diamond Rotary Dressers are what give this technology its cutting edge. There are four unique processes that can be used to adhere the diamonds to the dresser form:
REVERSE PLATED - Reverse Plated Dressers are best suited for applications where high accuracy of profile and a correspondingly high quality surface finish on the component are required.
HANDSET SINTERED - Handset Sintered Dressers are our most commonly used type of Rotary Diamond Dresser. They cover applications where robustness is required and the general tolerance is open.
CVD SINTERED - CVD Sintered Dressers are highly resistant to chipping and fracture, and they wear evenly over the dresser’s entire length. They also have outstanding thermal stability in use.
RANDOM SET SINTERED - Random Set Sintered Dressers are perfect for applications requiring openness, tight form, and improved surface finish. They can be delivered quickly to meet urgent demand.
Sometimes called Truers or Rollers, how do you know which of these will be the best diamond rotary dresser type for your application? Especially when each of these categories contain many further variables of appropriate diamonds and setting patterns.
5 factors for proper dresser selection
Proper dresser selection starts with investigating these five factors. Every well designed dressing tool must meet the specific requirements of these areas:
TOLERANCE - Tolerance refers to the allowable deviation or variation from a specified measurement or dimension in a workpiece. In the context of dressing tools, it's essential to consider the level of precision or accuracy required in the dressing process to meet the desired workpiece tolerances.
SURFACE FINISH - Surface finish pertains to the quality and texture of a workpiece's surface after the grinding or machining process. When designing a dressing tool, you need to account for the desired surface finish, which can range from rough to smooth, as it influences the choice of abrasive grains and dressing techniques.
CONFIGURATION OF FORM - Configuration of form relates to the specific shape, contour, or profile that the dressed grinding wheel should have. It encompasses the design and geometry of the wheel, which needs to be precisely replicated by the dressing tool to achieve the desired workpiece shape or finish.
GRINDING MACHINE TYPE - The type of grinding machine used in a particular application, such as cylindrical, surface, or centerless grinding, significantly impacts the dressing tool's design. Different machines require specific dressing techniques and tools to optimize performance and precision.
GRINDING WHEEL SPECIFICATION - This factor involves the characteristics and properties of the grinding wheel to be dressed. It encompasses details like wheel diameter, abrasive type, grain size, bonding material, and other specifications. The dressing tool must be compatible with these wheel specifications to ensure effective and efficient dressing.
Considering these factors when designing a dressing tool is crucial to achieving the desired precision, surface finish, and workpiece quality in various grinding applications. Correct specification involves the appropriate design, selection and placement of diamonds in a way that takes into account all the factors affecting the individual customer's application. It cannot be achieved by choosing from a small range of general purpose dresser types. Customization is required.
Our team at CDT has decades of experience in specifying and manufacturing Rotary Diamond Dressers for individual applications is second to none. Our processes are what make the Consort Precision™ Diamond Rotary Dresser truly exceptional, winning awards in the industry. We now manufacture and ship our custom diamond rotary dressers from both Europe and North America. The best part? It you costs nothing to consult with us—so contact us first to find the very best fit for your project.
Custom Rotary Diamond Dressers in as little as 4 weeks: How do we do it?
Industry-standard lead times for diamond rolls can take 8 weeks or more. If you are looking for a better, faster rotary diamond dresser alternative, we can expedite service in as little as 4 weeks. Learn how >
Since 1984, Consort Precision Diamond has supplied diamond wheel dressing products to a broad range of industries including aerospace, aircraft, automotive, blade and knife, power generation, medical, cutting tools, tool & die, saw, gear, and bearing and many other applications. What all these grinding operations have in common is that they typically require some form of wheel dressing to re-establish the wheel profile and/or recondition the wheel face.
About Wheel Dressing or Conditioning
Wheel conditioning involves the sharpening and opening of the wheel face, while also removing dull abrasives, excessive bond, and workpiece material (loading). A sharp and open wheel face will allow maximum possible material-removal rates and reduced thermal stress on the workpiece.
Consort’s rotary dressers provide the ideal profile for your desired wheel topography, with superior materials and manufacturing technology. Because your dresser is custom manufactured, demanding and complex configurations are possible.
Diamond Roll Delivery in as Little as 4 Weeks
The question then turns to delivery and lead times. In business, time is money. Industry-standard lead times for custom rotary diamond dressers can take 8 weeks or more. That’s a long time to wait for a critical part in your manufacturing process. Consort has made a reputation for fast delivery with a standard lead time of 6-8 weeks.
Need a tool in a hurry? Customers can request “Expedited Service” for custom diamond roll delivery in as little as 4 weeks. With manufacturing, delaying maintenance can really add to your costs in the long run. When a job is expedited, we work with our customers to get them their tooling as soon as possible.
We pride ourselves on prompt service and communication. At any time, you can reach out to your Consort account representative to begin an order or find out its status. If you do not have an account rep, please reach out to our customer service through our website online form or call 800-443-6629.
Lead times should not be a hurdle in the proper maintenance of your grinding equipment. If you are looking for a better, faster diamond roll supplier, let our service techs help you get the process started.
6 Common Grinding Problems and How to Solve Them
Are you experiencing these 6 common grinding problems? If so, your grinding wheel may be at fault. Learn more >
Most grinding problems affect one of two categories: either appearance of the workpiece or productivity and return on investment. After verifying that the grinding machine isn’t at fault, there is one likely culprit causing your grinding problems: your grinding wheel.
Poor surface finish, chatter, and burning all affect the appearance of your product. Productivity issues like short wheel life, slow or inefficient cutting, or the wheel not cutting at all are also costly problems to have.
Let’s take these one at a time to see how a fix to your grinding wheel can solve some of your most challenging grinding issues.
1) Poor surface finish
Why your grinding wheel may be at fault:
In the appearance category, poor finish is a common complaint when your grinding wheel isn’t optimized. Grinding is a multi-point cutting process, but broken down to the microscopic level, it has similarities to a single point operation like turning. Viewed this way, it’s easy to see how surface finish is affected by the same factors: the more material removed by each grinding point, the bigger the individual chips and the rougher the surface.
Solutions:
Select a grinding wheel with a finer grit size
Reduce the relative speed between the wheel and workpiece
Other possibilities:
If grinding wet, the coolant may not be efficiently removing chips from the workpiece or wheel interface.
It's also possible that the wheel is being dressed excessively, creating grinding points that are standing too proud of the wheel surface.
2) Chatter
Why your grinding wheel may be at fault:
Recognizable by a distinct, often audible, pattern on the workpiece, chatter has many causes. Wheel-induced chatter occurs when an out-of-true grinding wheel acts as an excitation source.
Solutions:
In this case the wheel should be trued carefully.
Also check that it isn’t slipping on its mount.
Other possibilities:
If the problem is tracked down to a vibration in the machine — possibly some kind of resonance — the solution is to vary the grinding speed. Try going 10% faster or slower to remove the forcing excitation.
A detailed discussion of chatter is available at the Abrasive Engineering Society website.
3) Burning
Why your grinding wheel may be at fault:
Machinists use the term “burning” to describe thermal damage. It can show up as cosmetic discoloration, changes in workpiece hardness, and possibly distortion-inducing internal tensile stresses. Burning can occur if the wheel is glazed or loaded, causing more rubbing and friction. This often occurs if the machinist is trying to push the wheel through the workpiece too quickly or using a wheel that’s too durable.
Solutions:
Dress the wheel with the correct dressing tool
Reduce the feed rate or the relative velocity between wheel and workpiece.
Other possibilities:
Burning is far more common when grinding dry, although can still be experienced in wet grinding if there isn't enough coolant flow to carry away the heat.
See “Burn Awareness”, originally published in Cutting Tool Engineering, December 2000, for more information.
4) Wheel life too short
Why your grinding wheel may be at fault:
This costly issue can be caused by a wheel that's either too hard or too soft for the workpiece. When this is the case, the grinding wheel loads up or wears away too quickly.
Solutions:
Try a grinding wheel manufactured with a different material that is better suited for your grinding operation.
Other possibilities:
Insufficient coolant
Dressing your grinding wheel too frequently
Wheel speed too low
5) Wheel cutting slowly
Why your grinding wheel may be at fault:
This productivity issue is usually caused by feeds and/or wheel speeds that are too low. If you are using the wrong type of grinding wheel, you may be forced to cut slowly to avoid burning, but ultimately that’s not efficient for your process.
Solution:
The solution is to find a wheel that can grind as fast as possible without burning. A grinding wheel specialists can suggest alternatives that will increase speed for your specific operation.
6) Wheel not cutting at all
Why your grinding wheel may be at fault:
Most likely, this happen when the grinding wheel is glazed by truing.
Solution:
The solution is to dress the wheel lightly until the grit opens up. For dressing advice, consult with a grinding specialist.
OUR BEST ADVICE: THINK LOGICALLY
Most grinding problems can be solved by tracing the fault back to basic principles. With all grinding applications, imagine your material being removed by individual cutting points. Thinking from this perspective, a solution usually emerges.
Also, use your resources. The grinding experts at CDT are happy to discuss your cutting and grinding issues and offer solutions that will set your manufacturing operations on track to success.
The Hardest Materials Just Became EASY
Customers report significant improvements to the grinding process and cost savings with CDT’s latest generation of Vitrified Diamond grinding wheels. Learn more »
Have you struggled to grind hard materials such as Silicon Carbide, Aluminum Oxide, Glass, Carbide, and others? With these substances, it has always been difficult to improve cycle times and reduce chipping and scrap ... until now.
Significant Gains in Grinding Performance
CDT’s latest generation of Vitrified Diamond grinding wheels combines high bond strength with porosity levels that significantly improve the grinding process. Better yet, this wheel is optimized for grinding hard, problematic materials such as Silicon Carbide, Ceramics, CMC, PCD, and more. With our VIPER™ Bond Technology, customers have reported significant improvements to the grinding process and cost savings.
*Vitrified Diamond grinding wheels with the new VIPER™ Bond Technology have been found to reduce cycle times up to 70% when compared with conventional resin bond grinding processes. Cycle times were reduced 30% or more when compared with other vitrified grinding products.
The Science Behind VIPER™ Bond Technology
Vitrified Diamond grinding wheels already take the hardest known superabrasives held mechanically and chemically in a ceramic bond to form some of the most efficient grinding products available on the market. Our custom-engineered wheels use varying concentrations, porosity levels, and bond hardness to optimize performance specific to your grinding process. The payoff? Vitrified—Improved—Performance
"With this new bond we saw cycle time reductions of 20% or more and the same amount of wear compared to our first generation vitrified wheel, which was already a vast improvement over a conventional wheel."
— Jim Elliott, Advanced Carbide
If you thought you knew what to expect from your Vitrified Diamond grinding wheel, it may be time to take another look. Contact us today to see how VIPER™ Bond Technology might improve your tool's performance.
CDT Engineers Assist With NASA SpaceX Prototyping
CDT’s Rapid Prototyping Team of engineers were responsible for turning ideas from NASA’s engineers into tools specific for their SpaceX mission. Learn more »
This SpaceX Falcon 9 rocket carries two astronauts in the Crew Dragon capsule on the Demo-2 mission to the International Space Station from Kennedy Space Center in Florida. Date: 30 May 2020. Source: WikiMedia. Photo by: Daniel Oberhaus.
What do you do when you need a part that doesn’t exist to get your innovation off the ground, but your internal resources of time and talent are not skilled with this type of manufacturing or stretched too thin? You know where you’re headed, but you need help getting there.
That’s the question NASA asked themselves during their recent SpaceX project testing. They came to CDT with theoretical concepts, and our team of engineers ran with their ideas to make them a reality.
At CDT, we’ve had the capability to prototype products for a long time. Typically, we use our equipment when we’re working to optimize the performance of our products for different customer environments. For SpaceX, we assembled a team of engineers who had the sole purpose of turning ideas from NASA’s engineers into tools specific for their mission.
The biggest challenge? We were on a strict deadline. The laws of planetary motion won't wait for delays. From NASA's concepts, our Rapid Response Team had to design, develop, and deliver prototypes to be used in field tests in a matter of days.
"It was a pleasure for my team and I to work with the experienced engineers from Space X. Assisting with tool designs for difficult and problematic projects is a key aspect to our daily routine. We look forward to more opportunities to work with the NASA and the SpaceX team," says Allen Meyer, CDT Plating Engineer.
Because we had the collective knowledge, experience, and tools right here at our disposal, our team was able to meet NASA’s deadline with no delay to the mission. It was a proud day seeing the recent launch of the Demo-2 Mission, knowing we played a small part in making that happen. We wish the astronauts a safe voyage and return!
“The only way to discover the limits of the possible is to go beyond them into the impossible.”
–Arthur C. Clarke
What far out idea do you need to get off the ground? Our Rapid Response Team is ready to help you move your innovation forward. Contact us today!
Continental Diamond Tool Corporation COVID-19 Update
Continental Diamond Tool values our partnership and would like to keep you updated as the COVID-19 pandemic continues to evolve.
March 24, 2020
Dear Continental Diamond Tool Partner,
Continental Diamond Tool values our partnership and would like to keep you updated as the COVID-19 pandemic continues to evolve.
Continental Diamond Tool will remain open in accordance with the Department of Homeland Security’s “Guidance on the Essential Critical Infrastructure Workforce” (https://www.cisa.gov/publication/guidance-essential-critical-infrastructure-workforce) dated March 18, 2020.
As part of the “Critical Infrastructure Segment,” the products that Continental Diamond Tool provides are essential in several critical industries, including but not limited to: Food and Agriculture, Energy, Healthcare and Public Health, Communications, and Critical Manufacturing.
Continental Diamond Tool continues to take an abundance of caution to ensure the safety of our team members and to make sure production goes uninterrupted. Please send any questions to: info@cdtusa.net. We thank you for your continued support.
Sincerely,
Nick Viggiano
President
Continental Diamond Tool
Diamond or CBN?
Having decided to leave conventional grinding wheels in favor of superabrasives, buyers are confronted with a difficult choice between diamond or CBN grit.
Having decided to leave conventional grinding wheels in favor of superabrasives, buyers are confronted with a difficult choice: diamond or CBN abrasive?
Both are extremely hard and offer the potential for greatly improved grinding productivity, but there are differences between the two. It's important to understand these and match the abrasive to the task if peak productivity, and lowest cost-per-piece are to be achieved.
A CHEMISTRY LESSON
Diamond is a crystalline form of carbon. Under heat and pressure carbon atoms link with adjacent atoms to create the hardest known material. This makes it an ideal cutting tool, or would do but for it's rarity and price. However, in the mid 20th century scientists figured out how to manufacture diamond, and today most diamond grit used in superabrasive grinding wheels is man-made.
Unlike diamond, cubic boron nitride (CBN) doesn't exist in nature and is synthesized from boron and nitrogen. When chemically bound together these two elements behave much like carbon in that they can create an immensely strong crystal lattice structure. Of the two, diamond is considerably harder at room temperature, (knoop hardness around 7,500 versus the 4,500 of CBN,) but CBN has better thermal and chemical stability, remaining inert at temperatures up to 1,000 oC, versus the 800 oC at which diamond begins to degrade.
CHEMISTRY DETERMINES APPLICATIONS
As the harder of the two, diamond is preferred for shaping extremely hard workpiece materials such as ceramics, carbides, stone and glass. It is not however suitable for use with steels. This is because carbon and iron have a strong affinity for one another, especially at elevated temperatures. This results in rapid erosion of the diamond grit, quickly destroying the grinding wheel.
CBN is better suited to grinding applications that generate high temperatures, meaning it can be used at higher speeds. And it's unreactive nature makes it the preferred choice for grinding most steels, such as tool steel and HSS.
IMPACT ON WHEEL CONSTRUCTION
The relatively low thermal limit of diamond also affects the type of wheel construction it can be used in. Vitrified wheels are made by firing a clay mix at very high temperatures: if the mix includes a proportion of diamond grit the firing temperature must be kept below 800 oC otherwise the diamond will start to react. For this reason, CBN is more common in vitrified grinding wheels.
TAKEAWAY
Use diamond on the hardest workpiece materials, but don't let it get too hot. Use CBN on ferrous workpiece materials to avoid the chemical reaction that will quickly wear diamond.
Continental Diamond Tool Acquires Jalsons International
Continental Diamond Tool Corporation (CDT), an industry leader in Diamond and CBN grinding wheels and tools, today announces their acquisition of Jalsons International Company, a manufacturer and supplier of Stationary Diamond Dressers.
New Haven, IN – Continental Diamond Tool Corporation (CDT), an industry leader in Diamond and CBN grinding wheels and tools, today announces their acquisition of Jalsons International Company, a manufacturer and supplier of Stationary Diamond Dressers located in North Canton, Ohio.
“CDT has had a great relationship with Jalsons for 20+ years. The acquisition allows us to increase our product offering and fits into our current Metal Bond Stationary and Rotary Diamond Dresser product line. Ultimately, it’s about giving our customer the best possible dressing option," says Nick Viggiano, President of CDT.
About CDT
Continental Diamond Tool, a private company located in New Haven, Indiana, is a leading producer in the global market for superabrasive grinding wheels and custom tooling. For more than 47 years, they have specialized in the design, manufacture and application of diamond and CBN cutting and grinding products and services. Their Plated, Resin Bond, Metal Bond, Vitrified Bond, Rotary Dressers, and GL™ Bond products serve a wide range of industries, including medical, oil & gas, automotive, aerospace, cutting tools, power generation, wood & saw, electronics, and many others.
About Jalsons International
Jalsons is a private company established in 1984 in North Canton, Ohio, by Pravin Shah as a specialized Diamond Dresser supplier to the Bearing, Automotive, and many other markets. Jalsons specializes in custom engineered tooling for their customers' applications to increase tool life, cost savings, and first-class customer service.
Diamond or CBN Grit with your Vitrified Grinding Wheel?
Each type of bond, vitrified, resin, metal or plated, has distinct performance characteristics. Learn about the choice between diamond and CBN as it relates to vitrified grinding wheels.
WHY USE A VITRIFIED GRINDING WHEEL
With a very hard and porous structure, vitrified grinding wheels are a popular choice amongst high productivity applications due to the great chip clearance and excellent coolant delivery. This type of grinding wheel has an extremely low wear rate and results in a high ratio of stock removal to wheel usage. The enhanced ability to dress a vitrified wheel allows for a larger layer depth with continual renewing of the grinding layer. The customization of this type of grinding wheels allows for the wheel to meet a wide range of customer applications, using either diamond or CBN as the abrasive.
Compared to other product lines, the structure of a vitrified grinding wheel allows for no deflection as the wheel feeds into part. As the grit starts to take chips of material out of the part, the finished piece size is strongly controlled and an enhanced surface finish from any customer’s requirements. Vitrified wheels do not need to run as fast as other products in the industry and coupling that with the ability to flow coolant through the open structure, results in less heat generated and minimal thermal damage to the workpiece.
REASONS FOR AND AGAINST DIAMOND GRIT TYPE
With its exceptional hardness due to the symmetry of its structure, diamond seems the obvious choice for every grinding wheel operation. However, there are limitations on where diamond can be used in applications as it has a strong affinity for iron and hardened steel. Diamond is a pure crystal of pure carbon, and the carbon and iron molecules like to interact and bond when the heat is generated during a grind. As a result, this can potentially cause issues with the workpiece as well as increases the wear of the grinding wheel.
ARGUMENTS FOR AND AGAINST CBN
In the application where diamond cannot be used, cubic boron nitride (CBN) is the next best alternative. The two big strengths are its ability to cut at extremely high temperatures and refusal to react with iron and other hardened steels when grinding. This makes CBN ideal when grinding tools and high-speed steels. The biggest downside to CBN is that the structure is not nearly as hard as diamond, and as a result, this grit type must run at a higher speed to be able to reach the same cutting abilities as a vitrified diamond grinding. Overall, both vitrified diamond & CBN wheels are available for a wide range of applications and can yield great results on a workpiece for a customer.
How Long Does it Take to Get a Custom Grinding Wheel?
In business, time is money. Industry-standard lead times for custom grinding wheels can take 8 weeks or more. If you are looking for a better, faster grinding wheel alternative, let our service techs help you get the process started.
Customized superabrasive grinding solutions have many advantages over conventional grinding wheels — primarily in performance. Custom CBN and Diamond grinding wheels improve efficiencies, last longer, and produce better quality results. Once you transition to a custom grinding wheel, the value of the investment becomes clear.
The question then turns to delivery and lead times. In business, time is money. Industry-standard lead times for custom grinding wheels can take 8 weeks or more. That’s a long time to wait for a critical part in your manufacturing process. CDT has made a reputation for fast delivery with a standard lead time of 4 weeks.
Need a tool in a hurry? Customers can request our Rush Program to expedite service for custom grinding wheel delivery in as little as 2 weeks. With manufacturing, every minute a machine is down, you feel the pinch. When a job is a rush, we work with our customers to get them up and running as soon as possible.
We pride ourselves on prompt service and communication. At any time, you can reach out to your CDT account representative to find out the status of your order, or email customer service at info@cdtusa.net. We send tracking numbers via email with your invoice when your order ships. You can also request tracking information through customer service at 800-443-6629 or through our website contact form.
Once you have placed an order with us, your wheel specifications will be held on file for quick processing and delivery of reorders through your account rep or our customer service department.
Lead times do not have to be a hurdle for transitioning to custom superabrasives. If you are looking for a better, faster grinding wheel alternative, let our service techs help you get the process started.
Advantages of Metal Bond Grinding Wheels
Every superabrasive grinding wheel consists of diamond or CBN grit held in a supporting matrix material known as the bond. The main bonding systems are resin, vitrified, plated, and metal. Of these, metal bond grinding wheels are perhaps the best known thanks to their overall utility and the length of time they've been available.
Every superabrasive grinding wheel consists of diamond or CBN grit held in a supporting matrix material known as the “bond.” The main bonding systems are resin, vitrified, plated, and metal. Of these, metal bond grinding wheels are perhaps the best known thanks to their overall utility and the length of time they've been available.
CONSTRUCTION AND MANUFACTURE
Metal bond grinding wheels start life as a superabrasive grit mixed with a metal powder. Most often this is bronze, although other metals such as iron and nickel are sometimes used. The mixture is distributed evenly around the periphery of a metal grinding wheel form, then placed in an oven and heated to around 1,4000F (7600C.) At these temperatures the metal grains begin to melt and diffuse into one another. This creates a dense matrix that locks the abrasive grit in place more tightly than in resin or vitreous bond wheels.
STRENGTHS AND WEAKNESSES
The metal bond wheel structure offers a number of advantages.
Metal bond grinding wheels last longer than those made by other methods. This boosts productivity by cutting down on dressing frequency and wheel changes.
Complex forms can be created, and since wear rates are low they last longer than in other types of wheel.
The metal structure is impervious to attack by alkaline coolants, (unlike resin grinding wheels which are susceptible to chemical attack, especially at elevated temperatures,) so is well-suited to use with grinding fluids.
Has excellent impact resistance, (unlike a vitrified wheel,) thanks to the metal wheel form, so stands up well in interrupted cut applications.
Heat is quickly dissipated through the metal core. This makes it appropriate for high material removal rate operations like creep feed grinding, (which are also helped by the ability to use coolant.)
One weakness to be aware of with metal bonded grinding wheels is that they are not easily dressed. Unlike resin and vitrified wheels, the bond material can't be cut away to release dull grit and expose new edges.
MANY APPLICATIONS
Metal bond grinding wheels can be used on a range of materials such as carbides and tool steels. However, their main application areas are those where coolant is needed to remove heat and chips, such as grinding or cutting glass, ceramics, granite, stone and concrete. They are usually recognizable by the presence of the metal core, but the 'M' at the end of the wheel identification code should remove any doubt.
The main advantage of these wheels is their long life/low maintenance nature. This makes them ideal for use when productivity concerns are paramount. Their ability to dissipate heat and work with coolant means they are useful in situations where interface temperatures become high enough to cause burning or size control problems. They are particularly useful in creep feed and internal grinding and also find use in grinding complex forms as the shape is maintained over the course of a long production run.
SEEK ADVICE
Purchasing diamond or CBN grinding wheels is a significant investment, so it's important to select the type of construction most appropriate to the intended application. Metal bond grinding wheels are perhaps the best known type but it may be worth seeking advice from specialists at CDT before ordering.
Where to Get Grinding Wheels in Stock, on Demand
At CDT, we cater to our customers needs. We keep precise records of every wheel we manufacture. If there is a wheel you regularly need in stock, let us know and we will make it available upon request.
At CDT, we are often asked if we stock grinding wheels. As a custom grinding wheel manufacturer, our wheels are designed to specific manufacturing processes. Universal (stock) grinding wheels rarely match the performance of our custom superabrasives in unique manufacturing settings.
That said, we can help you design a grinding wheel that maximizes performance, and make sure that wheel is available when you need it. Or if there is a stock wheel you know works great, we can have that on hand for you, too. When you find a grinding wheel manufacturer that understands your process, reorders are easy.
Choosing Your Grinding Wheel Manufacturer
CDT, like most manufacturers, lists the grit type, grit size, wheel hardness, structure, and bond using a code for every grinding wheel produced. However, there is no standard among manufacturers defining what these codes mean — the specification alone does not tell the whole story. This makes it difficult to take a grinding wheel from one manufacturer and substitute it for another grinding wheel of equal marking.
What if you are unhappy with your current grinding wheel source? Assuming you need your grinding wheel to perform exacting work and you want to limit your grief, we recommend you get guidance from an experienced grinding wheel specialist before making a substitution.
At CDT, we can interpret the codes on your grinding wheel and get a close approximation. Even so, you should expect some trial and error when converting from one brand of wheel to another. Dialing in the precise settings is a process, but it’s worth it to find a grinding wheel manufacturer who offers consistently competitive quality, delivery times, and price.
Ordering Replacement Grinding Wheels
Once you have your custom grinding wheel working efficiently, and you are happy with your manufacturer, you want to know you can get that grinding wheel on demand.
At CDT, we cater to our customers needs. We keep precise records of every wheel we manufacture. If there is a wheel you regularly need in stock, let us know and we will make it available upon request.
What Products Are Available?
CDT manufactures all the most popular superabrasive products on the market today: plated, resin bond, metal bond, and vitrified grinding wheels. Within our resin line, we have our GL Series that is comparable to a hybrid bond wheel and provides even more customizable performance options. Your best choice depends on your industry, material, process, and objectives.
In addition, we offer many types of dressers to keep your grinding wheels operating at peak performance — from diamond rotary to stationery varieties. We also have diamond lapping compounds, used in polishing materials to a mirror finish.
How to Match Your Resin Bond Grinding Wheels to the Workpiece
Superabrasive grinding have two equally important components. While the grit, (diamond or CBN,) does the work, it couldn't function without a partner holding it in place. In the case of resin bond grinding wheels, that partner is phenolic resin.
Superabrasive grinding wheels have two equally important components. While the grit, (diamond or CBN) does the work, it couldn't function without a partner holding it in place. In the case of resin bond grinding wheels, that partner is phenolic resin.
The hardness of the phenolic, along with grit size and concentration, determines wheel life, material removal rate, and final surface finish. CDT controls these three parameters precisely, allowing users to match a wheel to the particular workpiece material and type of grinding operation. However, selecting the best wheel depends on understanding the relationship between hardness, grit size and concentration and the wheel wear mechanism.
WHEEL WEAR MECHANISMS
As grit cuts through the workpiece material the edges become dull. Allied to that, chips from the cutting process erode the resin, releasing old grit and exposing fresh edges. The rate at which fresh grit is exposed is critical. Dull edges tend to rub against the workpiece, cutting forces go up and more heat is generated, perhaps burning the workpiece. Conversely, if grit is released early the grinding wheel is wearing faster than necessary, resulting in more frequent replacement.
HARDNESS
Hard workpiece materials, like ceramics and carbides, tend to dull cutting edges quickly, yet because the chips are small and brittle, resin wear is low. In this situation, to ensure a sufficient supply of fresh new cutting edges it's best to use a softer wheel.
Softer materials, like steels and high nickel alloys, (which should be ground with CBN rather than diamond,) produce longer, more ductile chips. These erode the resin faster which, in a soft wheel, results in excessive wear.
Manufacturers of resin bond grinding wheels adjust hardness by varying the mix of fillers in the phenolic resin. The resulting wheel hardness is expressed on a scale from A (softest) to Z (hardest) although superabrasive wheels are generally available just for the range from O through U. If a wheel outside of this range is thought necessary, consult with product specialists here at CDT.
CONCENTRATION
This refers to the proportion of superabrasive grit in the resin and is expressed on a scale of 25, 50, 75, and 100. The highest value indicates a weight to volume ratio of 72 carats per cubic inch, which works out to about 25% by volume.
A higher concentration means more cutting points, which results in faster material removal, but also increases wheel cost. Concentration also affects surface finish: a lower concentration would typically be used for finishing than for roughing.
GRIT SIZE
Larger abrasive particles remove more material on each pass, so coarser grits are used for rough machining and when grinding softer materials. Smaller particles lower cutting forces, so are used for harder materials as well as finishing operations.
MATCH THE WHEEL TO THE WORKPIECE
The choice of grinding wheel depends on the nature of the workpiece material and whether roughing or finishing. Harder materials generally should be ground with a softer wheel and small grit size. Softer materials are better ground with harder wheels and larger grit. Grit concentration should be chosen to suit the type of grinding operation – roughing or finishing.
If in any doubt as to the hardness of wheel to use, consult a grinding wheel specialist.
Diamond Lapping Compounds
CDT lapping and polishing compounds are excellent for mold, die, and tool polishing.
CDT lapping and polishing compounds are excellent for mold, die, and tool polishing. These compounds also provide superior results when polishing to final tolerance of ceramic parts, tool-room use, and many other high finish and tight tolerance performance applications.
Diamond is the hardest and the most abrasive-resistant material used in nearly every type of industry. Our diamond lapping compounds use these unique characteristics to improve your finishing capabilities. You may choose to add diamond powders to the polishing paste in some instances.
Whether your job calls for high stock removal, fast polishing times, or superior finishes, you can find a compound that will help you achieve better results and a mirror finish. Both water and oil soluble compound are available in 5 and 18 gram syringes. Our syringes are disposable plastic dispensers that are convenient and safe from outside impurities.
Key features and benefits include:
Faster cut rates
High surface finish
Excellent surface tension
Quality viscosity
Low evaporation rate
Key adhesion to tools and surfaces
Easily cleans surfaces with both water and oil
Customers often ask what grit do we use for mold, die, and tool polishing? Our engineers are happy to assist you in finding the best compound for your specific application: 800-443-6629.
Since 1973, CDT has lead the field in providing technically superior precision tooling solutions to numerous industries. If you need rapid, accurate lapping, polishing and super-finishing, contact our technical team to learn more about our diamond lapping compounds.
Common Fluting Mistakes — and How to Fix Them
While superabrasive grit does the grinding, the bond material is every bit as important. Learn how resin bond can produce superior surface finish.
Flute Polish or Flute Burnish?
There is an increasing need for high-quality carbide mills and drills with polished flute faces. Your customers are demanding a surface grinding tool that has a shiny flute, evacuates a metal chip better, and runs at faster speeds.
Sometimes your customer just wants your tool to look like the “other guy’s” tool. Unfortunately, a burnished flute face can be mistaken for true polish. Toolmakers have the challenge of making a cost-effective tool that has great performance and a great finish on the flute face.
Common Fluting Mistakes
Some toolmakers turn to hybrid wheels that grind the flute in no time, but these grinding wheels really don’t polish all that well.
To improve appearances and achieve a smooth finish, a lot of toolmakers use nonwoven products to polish after fluting. But do flute polishing cloths really polish, or do they just burnish the surface?
For a Quality Flute Polish
For a flute cleaning and polishing that really penetrates the surface, you have to remove some material to get through the grind lines leftover after flute grinding.
A resin bonded grinding wheel can give you a finish that is as good or better than nonwoven polishing products, but the resin bonded wheel also removes material from the flute face, taking out subsurface damage.
Resin bond is made by mixing abrasive grit with a phenolic resin. The resulting compound is molded to shape before being baked in an oven. This produces a grinding wheel that's tough, with the resilience to take impacts without shattering. By adding copper and other fillers to the resin base, grinding wheel manufacturers can tailor the properties of the finished grinding wheel to a wide variety of applications.
With resin bond, you can make a tool that not only looks just as good as the “other guy”, but also is actually better quality than the other guy. Resin-bonded superabrasive grinding wheels provide:
Shock-resistance
Excellent surface finish
Low maintenance
The Extra Effort Sets You Apart
The right wheel can help you polish up your act. CDT’s resin bond flute polishing wheel performs as good as it looks — producing a quality tool that shows. We offer resin bond polishing wheels to work in oil or emulsion on all CNC cutter grinders. These grinding wheels can run at high speeds and are available in grits as fine as 1200 or more based on finish requirements.
Grinding wheel manufacturers have years of experience and there are few fluting applications we haven't encountered. Our engineers can help you get the right grinding and polishing solution for your particular application.
Precision Finishing With Diamond Lapping Compounds
In many applications the finish resulting from grinding is good enough. When it isn't, the next step is lapping. As with grinding, diamond makes an excellent abrasive, but for best results needs to be selected and used appropriately.
A good quality grinding wheel on a rigid machine can produce a surface with a roughness around 0.25 microns Ra. In some applications this isn't enough; in others flatness is of greater importance than finish. In either situation the next step is to move on to lapping.
PRECISION FINISHING
In lapping an abrasive compound, composed of abrasive particles in a liquid or paste transport medium, is placed between the work piece and a lapping plate. Movement of the plate rolls the particles across the surface, removing raised peaks and flattening high regions. Depending on the work piece material, roughness numbers of under 0.30 microns Ra are achievable.
Other reasons for lapping are to bring something down to a precise and uniform final size and to produce a very flat surface. (Think of flatness as the rolling of hills and valleys, while roughness is the furrows plowed in the field.) Lapping doesn't put any stress or heat into the surface, and the low cutting forces make it a distortion-free way of finishing thin-wall parts.
LAPPING WITH DIAMOND COMPOUNDS
A number of abrasives can be used but diamond has several advantages:
highest material removal rates, by virtue of it's exceptional hardness
excellent surface finish, because the edges cut cleanly and diamond can be graded down to micron-level. (Producing a uniform, scratch-free surface demands particles of the same size: any that are larger will produce undesirable scratches.)
When lapping, standard practice is to use a cast iron lapping plate. For lapping with superabrasives (diamond or CBN) though it's recommended to use a composite metal plate such as tin, copper or cast iron.
The transport medium used in a diamond lapping compound can be either oil or water soluble. Oil soluble compounds are the most common and can be used on ceramics, carbides, cast iron and other metal surfaces.
A water soluble compound is used when the work piece is sensitive to oil. It's often employed for finishing electronic and electro-optical components and is widely used for magnetic read/write heads and semiconductor applications.
Companies like CDT supply precisely graded diamond lapping compound in syringes for easy dispensing. The coarsest grades, in the region of 40 to 90 microns, gives rapid stock removal while smaller particle sizes are used for finishing. To give one example, an application like preparing metallographic samples needs abrasives of less than two microns in size.
CHOOSE YOUR DIAMONDS CAREFULLY
In many applications the finish resulting from grinding is good enough. When it isn't, the next step is lapping. As with grinding, diamond makes an excellent abrasive, but for best results needs to be selected and used appropriately.
Understand Dresser Options To Cut Costs
Dressing is at the heart of a simple process: Use a diamond to expose fresh grit on the grinding wheel to extend its life. Yet there are dozens of different dressing tools — learn which to choose.
If you look at “Dressers “ or “Diamond Rolls” on the CDT website, it reveals several different types. Dressing is at the heart of a simple process: Use a diamond to expose fresh grit on the grinding wheel, so why so many tool options?
Focus on cost per piece
Stopping to sharpen the wheel means lost production, so it’s tempting to dress infrequently and to do it as fast as possible. Most shops know that’s a mistake, so they look for other routes to cut costs.
For some that means buying the cheapest single point dressers they can find. That’s often false economy. Instead they should try to minimize the dressing cost per work piece. That might mean buying better quality or more sophisticated dressers, which is why so many different types are offered.
Single point
The single point diamond dresser is the workhorse of grinding. It works in practically every application but is especially effective on straight wheels and for creating simple profiles. Special variants of the single point dresser are used for thread forms.
Diamonds aren’t cheap though, especially the better quality ones that better resist microcracking, so it’s important to get as much life from the dresser as possible. That means rotating the diamond regularly and changing the face exposed to the wheel to even out the wear.
Some diamond dressers are resettable, meaning the diamond can be reoriented to expose a fresh point. That adds to the cost but can mean an overall saving when compared with nonresettable dressers that are effectively throwaway items.
Multipoint dressers
In multipoint dressers, several diamond points work together to dress the grinding wheel. They work well for straight pass grinding on larger OD wheels as well as surface and centerless wheels.
A special form of the multipoint dresser is the donut cluster. These consist of a large number of diamonds set in a large crown. Good for dressing large wheels quickly, they are especially recommended for use on cylindrical grinders.
Grit dresser tools
Continuing the progression toward more dressing points, these tools use a diamond grit rather than discrete diamonds. These are long-lasting and allow for rapid dressing, making them very cost effective.
Blade dressers
Similar to a chisel in appearance, these present a line of diamond to the wheel. While they work for straight dressing, it’s more common to use them for profiles. Blade dressers come in both fixed and swivel head geometries for additional versatility.
Rotary diamond dressers
Rotary Diamond Dressers are a highly efficient and cost effective means of dressing and truing grinding wheels. Their use in achieving accurate correct form, tolerance, and condition is rapidly growing in the automotive, aerospace, power generation, machine tool and precision engineering component manufacturing.
Not an easy choice
There are several routes to minimize dressing cost per work piece and even for experienced machinists, it’s not always obvious which to take. That’s why it’s advisable to consult with experts to determine the best type of dresser for your application.
Grind Quickly And Accurately With A Vitrified Superabrasive Wheel
When high material removal and dimensional control is a concern, a vitrified wheel should be the first choice. Learn more benefits of a vitrified wheel >
High material removal rates demand a lot from the workpiece-machine-wheel system. Everything deflects under the high loads, making it difficult to achieve precise control over finished workpiece dimensions.
To combat this grinding machine manufacturers engineer-in as much rigidity as possible, but the wheel has a part to play as well. Resin-bonded wheels tend to “give” slightly under load, making it hard to meet tight tolerances whereas vitrified wheels provide much higher stiffness. This is because the Vitrified wheel is essentially composed of abrasive bound in a ceramic bond that doesn’t deflect as it contacts the workpiece, so size control is better.
VITRIFICATION BENEFITS
A vitrified superabrasive wheel begins life as Diamond or CBN grit incorporated into a specialized ceramic bond. After being formed to the required wheel shape this goes into a kiln where it’s fired at high temperature to fuse the abrasive to the bond. The superabrasive is both mechanically and chemically held.
This provides five other benefits in addition to stiffness:
Low wear rates
Thermal stability – which helps size control
Open structure enables coolant delivery to the grinding zone, keeping interface temperatures down
Oils and other fluids have no effect on wheel integrity
Dress-able, allowing precise forms and extending life
APPLICATIONS
Vitrified superabrasive wheels have a much longer life than conventional Silicon Carbide or Aluminum Oxide grinding wheels and provide exceptionally rapid material removal. This makes them attractive for high volume applications where cycle time and downtime must be minimized.
Vitrified diamond wheels are ideal for grinding PCD cutting tools, as well as carbides, cermets and ceramics. Vitrified CBN wheels are more suited for ferrous metal applications like camshaft and crankshaft grinding in the automotive industry or tool and die machining.
A further advantage of vitrified wheels is the possibility of customization to suit a specific application. Consult CDT to learn what's possible.
CAUTIONS
Glass is brittle and so is a vitrified wheel. It will break down under high pressure. This also means the wheels need to be engineered for the application.
Because of the porous structure of the Vitrified wheels, it is important to adjust the corresponding grit size to match finish when comparing/converting from conventional abrasives or Resin and Metal Bond wheels.
THE HIGH VOLUME SOLUTION
When high material removal is needed and dimensional control is a concern a vitrified wheel should be the first choice. Its high stiffness and porous structure allow rapid grinding while minimizing deflection in the workpiece-machine-wheel system. Add in long life and the result is a wheel suited to the most challenging high volume applications.
Why Use Plated Diamond or Cubic Boron Nitride Tools?
Coatings applied during the plating process are either metallic, diamond, or cubic boron nitride. Learn the properties of each and which is best >
Layering metal parts via electrolysis with special substances that improve their strength or appearance and protect parts from oxidation and corrosion is called electroplating. Typically less than .05 millimeters thick, coatings applied during the plating process are either metallic, diamond, or cubic boron nitride. Decorative objects such as jewelry or tableware are usually plated with silver or gold while steel and iron items are plated with zinc, chromium, nickel or tin. However, grinding tools require cubic boron nitride or diamond coatings to optimize their functioning, provide better cutting action and deter rapid deterioration of tools.
Advantages of Electroplated Diamond Tools
Tools sent through an electroplating process that coats them with a diamond layer cleaved by a tough nickel alloy retain their precise proportions and original structure throughout their working life. Unlike resin bond or metal bond diamond products involving diamond particles that have been cached in bond and joined together by embedded resin or metal binder, electroplating facilitates the protrusion of diamond fragments to extend beyond the bond matrix. This further provides electroplated diamond tools with the exceptional ability to cut freely and rapidly without generating excessive heat. Less heat generation means better grinding efficiency, reduced risk of cracks or burns on the workpiece's surface and a significant decrease in equipment energy consumption.
Electroplated diamond tools are well-suited to process:
Abrasive or hard non-metallic entities such as asphalt, stone, ceramics, concrete, semiconductor materials and glass.
Non-ferrous metals (copper, aluminum and their alloys) and pliable but tough materials (resin and rubber, for example).
Since diamonds react with iron, cobalt, nickel, chromium and vanadium under elevated temperatures produced during grinding actions, diamond tools should not be used to process common steels and tough alloy steels. For work involving these materials, electroplated cubic boron nitride tools are recommended.
Advantages of Electroplated Cubic Boron Nitride Tools
Considered the best technological advancement made for facilitating grinding of superalloy and hardened ferrous materials, cubic boron nitride is second to diamonds on the hardness scale and offers nearly five times the abrasion resistance afforded by traditional abrasives. Electroplated CBN tools also provide the following additional benefits not found in any other electroplated tools:
Remarkable thermal conductivity and chemical resistance
Enhanced surface integrity for grinding hardened cobalt-based superalloys as well as nickel and hardened alloy steels
Eliminates the expense of post heat-treat grinding operations
Produces polished surface finishes by providing taut dimensional management of tools to users
Creates no bit-dulling grit
The ability to induce nanostructuring of carbon boron nitride has allowed engineers to further increase the hardness of CBN by incorporating the Hall-Petch Effect, which describes the "tendency for hardness to intensify as grain size is decreased". In addition, carbon boron nitride's chemical resistant and strong thermal stability properties make it well-suited to machine ferrous materials that cannot be machined by electroplated diamond tools.