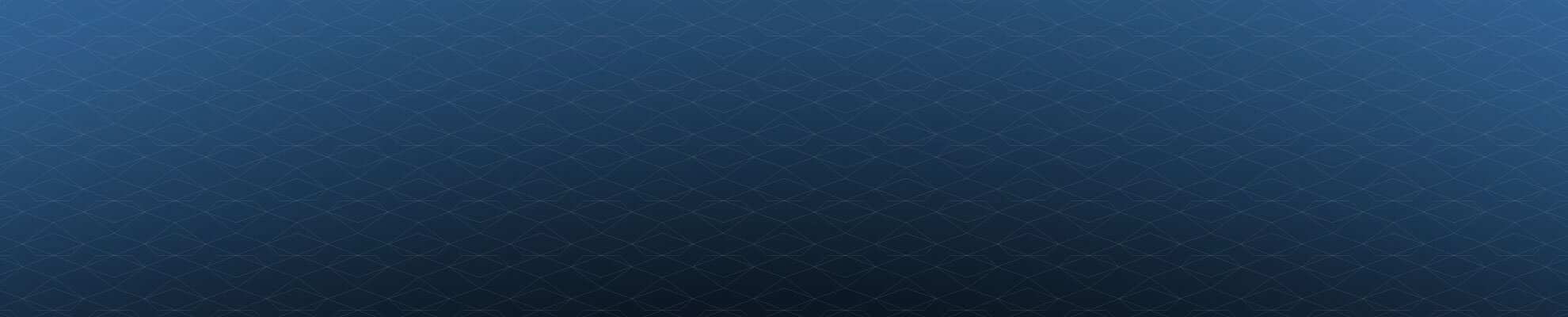
News and Resources
Browse by Category
Browse by Product
- All Dressing Products
- All Grinding Products
- CBN-Diamond Superabrasives
- Conventional Abrasives
- Diamond Lapping Compounds
- Diamond Rotary Dressers
- Diamond Stationary Dressers
- Hybrid Bond Grinding Tools
- Metal Bond Grinding Tools
- Plated Grinding Tools
- Resin Bond Grinding Tools
- Vitrified Bond Grinding Tools
What are Metal Bond Grinding Wheels and What Benefits Do They Offer?
Extensively used in manufacturing diamond grinding wheels, metal bonds are manufactured utilizing three different processes: cold press, semi hot press and hot press modes.
Extensively used in manufacturing diamond grinding wheels, metal bonds are manufactured utilizing three different processes: cold press, semi hot press and hot press modes.
Cold press mode involves pressing the transition layer (no diamonds) and the working layer (with diamonds) of selected diamond portions to forms that on the body of the grinding wheel. These segments are then allowed to interconnect with the grinding wheel's body via slots or teeth. Finally, cold press grinding wheels are placed into sintering furnaces where they are sintered without press.
The semi hot press mode improves on the cold press mode by complementing the sintering process. While grinding wheels are sintering in a furnace, applicable molds are applied and minimal to moderate pressure is added. However, any pressure applied is significantly lower than the amount of pressure applied in hot press mode.
Hot press mode directly sinters diamond particles in molds under preset pressure levels in induction units. Diamond segments are then affixed on the grinding wheel using high frequency laser welding, high frequency welding or mosaic methods of mechanical welding.
Metal bond grinding wheels are produced when powdered metals or compounds containing cubic boron nitride or diamond are sintered on the wheel, resulting in exceptionally strong tools that maintain shape during rigorous use. In addition, metal bonding extends the life of grinding wheels by reducing the need for repeated dressings and continues being productive longer than market-brand super abrasives.
Benefits of Using Metal Bond Grinding Wheels
Because metal bond grinding wheels are sintered with cobalt, copper, mill, silver or stanum powder, they work exceptionally well on a variety of surfaces (glass, refractories, ceramics, silicon, semi-conductors and quartz).
Whether used for tool cutting, glass grinding, ceramic grinding or form cutting, metal bond grinding wheels provide the longest, most superior quality of service before any type of maintenance is needed.
Metal bond offers the ability to perform outstanding interrupted cuts while retaining the tool's original dimensions even during the most energetic grinding actions, including centerless, cylindrical, creep feed, deburring and cutoff applications.
Although resin bonds are more commonly used than vitrified or electroplated bonds, these bonds do not offer the hardness or wheel retention properties exhibited by metal bond grinding wheels.
As one of the most frequently seen machines in manufacturing plants requiring grinding applications, centerless grinders especially benefit from metal bond grinding wheels because of the slow, precise pace of material removal method demanded of these machines. Additionally, super abrasive centerless grinders necessitate powerful wheels such as metal bond grinding wheels that can effectively make predetermined alterations to products while reducing quality control issues that may arise if lesser quality wheels are used.
Continental Diamond Tool Corporation has been producing Metal Bond products since it was founded in 1973. If you are looking for a custom metal bond wheel, contact our experienced team of product engineers today.
40 Percent Improvement for Carbide Grinding with CDT Wheels on a Studer CNC Grinder
Check out how our engineers were able to add value to carbide grinding using Studer CNC grinders with a custom vitrified grinding wheel by CDT.
“Continental Diamond Tool knows grinding wheels … give them a problem and they tackle it.”
Continental Diamond Tool recently had a customer looking to replace the grinding wheel on their Studer CNC grinder. They were searching for a modern solution that would be compatible with both their newer and older CNC grinder models. With this upgrade, they hoped to reduce their cycle times and increase utilization of their capital equipment.
CDT proposed a transition to a diamond wheel for carbide grinding, and it was determined that our newly formulated vitrified diamond grinding wheel would accomplish their goals in this circumstance. Our engineers customized the core material to improve vibration damping characteristics. We also dynamically balanced the wheel allowing for improved start-up and wheel performance.
After extensive testing of the grinding wheel on their new programmable, variable speed Studers, with the same parameters as the previous competitors wheel, they slowly increased feeds until they reached the optimized 40% cycle time reduction with great success.
With the older Studers, our team ran into a complication. Because those machines use a pulley driven system, the grinders did not have the desired 6500 SFPM for vitrified diamond included. When hurdles like this arise, we meet those challenges head on. The solution to purchase a new pulley size allowed the older Studers to achieve the optimal speed for 40% cycle time efficiencies.
Besides gaining efficiency, the new wheel has extended our customers profile and form capabilities, adding Straight 1A1, Anglehead 1E1, Slotting/Groove, Face 6A2, and ID 1A8 styles. With these new capabilities our customer has been able to increase their through-put by 40% or more.
Additionally, because their old Studers are performing like new with extended capabilities, the customer will be able to delay the replacement of these old CNC grinders. At $450,000 a machine, this is a significant benefit.
Our next project will extend rotary dressing capabilities to their old Studer CNC grinders. They currently off-line dress both their current grinding wheels every other day on these older machines. Their newer Studers have rotary dressers that eliminate off-line dressing. Once rotary dressing is implemented on all their machines, it will greatly reduce their maintenance downtime.
The results from this custom project have been impressive with added value in multiple steps of the process summarized below:
· Reduced cycle times more than 40%
· Increased through-put by more than 40%
· Increased utilization of capital equipment
· Opened the door for the elimination of off line dressing
At CDT, we value our relationship with loyal customers. One of the key aspects of working with them has been our ability to expedite orders when needed and improve product performance and ultimately add value to the bottom line. When we are familiar with a company's unique process, we can often compress our four week standard lead-times to deliver in as little as one week. We can also organize blanket orders with scheduled releases.
When we asked their CFO why they chose CDT for their grinding wheels, he said, "Continental Diamond Tool knows grinding wheels, and their team is always innovating. Give them a problem and they tackle it — with excellent service, quality, and follow through."
It was a pleasure working on this project, and we're always happy to be of service!
Preparing CBN Wheels for Use
Preparing CBN wheels for use requires a bit of effort up front, but will give you long-term benefits that are immeasurable.
Superabrasive grinding wheels, such as diamond and CBN wheels require a little work and effort to set up and make them ready for use. This involves three main steps mounting, preparing (truing) and dressing the wheel so that they work as they should and give you the best possible grind. All three steps are important, but none so much as truing your CBN wheel.
What is Truing?
Truing allows for the face of the CBN wheel to be presented to the work piece properly and give you the best possible performance. After all, a wheel that is untrued can provide a surface finish, stock and removal capability that is undesirable. If you go through the truing process, and choose the right options based on your particular device and the product you are working with, you will get the highest possible performance of your grinding wheel. Additionally, the wheel life will be greatly reduced costing you much more effort and cost in the long run.
The Truing Process
The truing process occurs after you have already hand mounted your CBN wheel to the minimum runout. There are a number of techniques you can utilize to obtain the maximum truing level. Two of the most common include:
1) Multiple point (14 - 40 mesh) or impregnated (40 - 100 mesh or finer) diamond-type dressing tools.
Offers 0005" infeed for each pass (.01MM)
Not recommended for single point & cluster diamond tools
Finer mesh diamond - This technique allows better initial work piece finish
2) Truing brake or motorized dresser
Coarse grit (ranging from J to M hardness)
Silicon carbide or aluminum oxide wheel
001” Infeed per pass (.025MM)
You will apply the truing device to the wheel until contact is made with the entire face of the CBN grinding wheel. Whenever it is possible, you want to use flood coolant as this will extend the life of the CBN wheel. Heavy-duty water-soluble oils will also help add life.
It is important to remember that a resin-bonded wheel is not necessarily ready to go after it has been trued. Properly dressing it is very important as well. If you do not work through all the steps of the process, you will not get the best possible results and you may find yourself changing your wheel again much sooner than you planned to in the future.
Taking the proper preparation steps with your CBN wheels is not necessarily the easiest part of the grinding process, but it can make a big difference in the effectiveness of your wheels as well as with helping them to do their job for a longer length of time. For most factory and workshop applications, it is worth the effort and cost up front. After all, a CBN wheel is one of the most important tools you use on a daily basis, so why not take the time with the process?
Tips To Solving Wheel-Related Grinding Problems
When there are problems with a ground surface finish, when productivity is low, or if costs are too high, the fault may lie with the grinding wheel. Changing the grit, wheel feeds and speeds, or coolant application may be the solution, depending on the precise nature of the problem.
Grinding problems show up in two ways: in the appearance of the workpiece and as cost or productivity issues. After verifying that the grinding machine isn’t at fault, attention should turn to the grinding wheel.
Appearance problems divide into poor surface finish, chatter, and burning. Cost and productivity issues are short wheel life, slow cutting, and the wheel not cutting.
APPEARANCE ISSUES
Poor finish
Grinding is a multi-point cutting process, but down at the microscopic level it’s little different to a single point operation like turning. Viewed this way, it’s easy to see how surface finish is affected by the same factors: the more material removed by each grinding point, bigger the individual chips and the rougher the surface.
The solutions are:
Select a finer grit size
Reduce the relative speed of wheel and workpiece
If grinding wet, it might also be that the coolant is not removing chips from the workpiece/wheel interface. It's also possible that the wheel is being dressed excessively, creating grinding points standing too proud of the wheel surface.
Chatter
Recognizable by a distinct pattern on the workpiece, and often audible, chatter has many causes. If initiated by a vibration in the machine – possibly some kind of resonance – the solution is to vary the grinding speed. Try going 10% faster or slower to remove the forcing excitation.
Wheel-induced chatter occurs when an out-of-true grinding wheel acts as an excitation source. In this case the wheel should be trued carefully. Also check it isn’t slipping on its mount. A detailed discussion of chatter is available at the Abrasive Engineering Society website.
Burning
Machinists use this term to mean thermal damage. It can range from cosmetic discoloration to changes in workpiece hardness and possibly the creation of distortion-inducing internal tensile stresses. Burning is far more common when grinding dry, although can still be experienced in wet grinding if there isn't enough coolant flow to carry away the heat. “Burn Awareness”, originally published in Cutting Tool Engineering, December 2000, provides more information.
Burning can occur if the wheel is glazed or loaded, so there is more rubbing and hence more friction, by trying to push the wheel through the workpiece too quickly, or by using a wheel that’s too durable.
Solutions are:
Dress the wheel with a dressing stick
Reduce the feed rate or the relative velocity between wheel and workpiece.
COST AND PRODUCTIVITY ISSUES
Wheel life too short
This can be caused by:
Insufficient coolant
Dressing too often
A wheel that's either too hard or too soft for the workpiece (so it loads up or wears away too quickly)
Wheel speed too low
Slow cutting
Usually caused by feeds and/or wheel speeds that are too low, the solution is to grind as fast as possible without burning.
Wheel not cutting
This happens when the wheel is glazed by truing. The solution is to dress the wheel lightly until the grit opens up.
THINK LOGICALLY
Most grinding problems can be solved by relating the fault back to basic principles. Picture material being removed by individual cutting points and a solution usually emerges.
Supplier to Rolls Royce Creating Additional Jobs
Consort Precision Diamond, U.K. manufacturer of sophisticated cutting tools for Rolls Royce and other automotive and aerospace companies, is to create 23 new jobs. Consort is a subsidiary of Continental Diamond Tool Corp.
Consort Precision Diamond, the Continental Diamond Tool subsidiary that specializes in Rotary Diamond Dressers, was recently featured in the Daily Post in Wales. Read the article below or link to the Daily Post website here.
Supplier to Rolls Royce Creating Additional Jobs
BY OWEN HUGHES, Business Correspondent | Daily Post
A company that manufactures sophisticated cutting tools for Rolls Royce and other automotive and aerospace companies is to create 23 new jobs.
Economy Minister, Ken Skates (pictured) visited Consort Precision Diamond in Kinmel Bay, Conwy to discuss the expansion plans, which will be supported by £200k from Welsh Government.
The Minister also spoke to the company’s management team about the types of challenges they are facing in the run up to Brexit, and urged them to take advantage of the range of support offered to Welsh business to help them prepare and build resilience ahead of Brexit.
Ken Skates said: “I am delighted that the Welsh Government is supporting Conwy based Consort Precision Diamond in its plan to expand its facilities and create an additional 23 highly skilled jobs at Kinmel Bay.
“The support from Welsh Government will help fund the first phase of a five year plan that will see Consort Precision Diamond building a new premises and increasing its head count to just shy of 170.
“It was also good to speak to the company about its Brexit preparations and to ensure they are aware of, and are accessing the full range of Welsh Government support.
“Consort Precision Diamond actually exports extensively to markets outside of the EU, meaning that it is a stronger position to deal with the changes and challenges that Brexit will bring.
“I would urge any business in Wales to access our comprehensive range of exporting support and advice so they can put themselves in the strongest possible position to navigate the journey ahead.
“Of course we know that what business really needs, and continues to call for, is certainty.
“For our part we will keep pushing the UK Government to take No Deal off the table and work to secure a Brexit that protects Welsh jobs and our economy.”
Source: https://wales247.co.uk/rolls-royce-supplier-creates-23-new-jobs-with-welsh-government-support/
How to Keep your Grinding Wheels Performing Every Time
Properly dressing your grinding wheels is an important step in helping them to work as they should.
Grinding wheels are a very important tool in many factory and shop situations. They can be used for any number of projects; because of this, they tend to become something that are taken for granted. You expect that when you go to the shop that the grinding wheels will work as intended.
However, there are a number of issues that can occur that prevent the wheels from grinding as they should. While some of these problems are big and require a replacement wheel, others are reparable. One of the most common problems is a wheel that is not providing as heavy of a grind as it should.
Commonly, new wheels may not have the same grinding power as wheels that have been “broken in” and used for some time. As such, it is important to understand the concept of dressing grinding wheels.
To get the best cutting performance from your grinding wheel it is important that the wheel have a sharp abrasive grain with cutting points that are well exposed and able to connect with the piece with which you are working.
The ultra-hard abrasive crystals often used in grinding wheels will remain sharp simply through the process of grinding itself. Essentially, the wheels will slowly expose further crystals and you will not need to continuously dress the wheel. This is one of the biggest benefits of these superabrasive grinding wheels.
However, one problem is when you are working with new wheels. Usually these wheels have a smoother grinding surface. This occurs because the crystals and the surrounding bond are still flush to the edge of the cutting surface. If you try to operate a wheel without first dressing it, you will find performance is lacking. This is called “loading.” A wheel that is loaded will have poor cutting performance and may even cause some burning to your work piece.
This is where dressers come in. Diamond dressing sticks or rotary diamond dressers (also known as diamond rolls) are supplementary tools that keep your wheel operating at peak performance.
Dressing your superabrasive grinding wheel enhances grain exposure and brushes away some of the bond so that the wheel will work as it should. However, it is important that you choose the right type of dressing for your wheel to get the performance you desire. Some of the qualities you should consider with your grinding wheel dressing include:
Hand held aluminum oxide or silicon carbide stick
Soft (G, H hardness)
Fine grit (200-400 mesh)
Another strategy is to lower the RPM of the spindle, at least temporarily. This will open the wheel quicker and expose the abrasive surface for a more open surface. Then, you can increase the RPM in the future when the abrasive surface has been properly dressed and exposed.
While dressing your wheel is often something that only occurs when the wheel is new, it is possible to experience burning and poor cutting even on an older wheel. If this happens, you can simply use the same stick and technique to re-expose the surface and reopen the wheel.
As you can see, there is a lot to think about when you are first setting up your grinding wheel or if you are working with a wheel that does not seem to offer the best performance. It is possible to get the performance you desire it just takes a little work and effort up front!
Hardness Matters. Best Materials for Drilling, Cutting and Grinding
Superabrasives are split into two categories: CBN for use with ferrous material, and diamond for almost all other materials. At only half the hardness of a natural diamond, CBN is the only other material besides synthetic diamonds that is hard enough to be considered a superabrasive.
A natural diamond is the hardest material on the Knoop Hardness Scale, as is well known. It is considered a superabrasive, and has a long list of things it is regularly used to drill or otherwise shape. Glass, plastic, cemented carbide, ceramics, fiberglass, electronic components and materials, and titanium alloys are just a sampling of the things a diamond can cut. This is true whether the diamond is natural, manmade, or polysrystalline, as all three of these diamond types top the Knoop Hardness Scale. This means that even non-natural diamonds are harder than anything else except a natural one.
Right after the diamonds comes the Cubic Boron Nitride (CBN). This measures at nearly 5,000 on the Knoop Hardness Scale (compared to the 10,000 for a natural diamond, for comparison). At only half the hardness of a natural diamond, CBN is the only other material besides synthetic diamonds that is hard enough to be considered a superabrasive.
Everything else on the Knoop Hardness Scale is less hard than natural and synthetic diamonds and CBN. This means these things can cut through nearly everything else. The vast difference between the hardness of a natural diamond and the hardness of CBN shows just how relatively soft everything else on earth is in comparison to a natural diamond. If it wasn't for CBN, there would be no other super abrasive at all.
Superabrasives are split into two categories: CBN for use with ferrous material, and diamond for almost all other materials. Conventional Abrasive grinding wheels are also split into the same two categories. Silicon Carbide is known to chemically interact with ferrous materials making it less than ideal for such materials. Aluminum Oxide, despite being somewhat softer than Silicon Carbide, does not have chemical reactivity with Ferrous materials, and is therefore a better choice for these materials.
So the question becomes which is the better choice; conventional abrasive or superabrasive grinding products for your application? In general, superabrasive grinding wheels can provide 100-300 times the grinding wheel life when compared with conventional abrasives due to their higher hardness values, while only costing 10-30 times the wheel price. However, significant other variables have to be considered when determining which type of grinding wheel is best for your application. These include the machine/grinder, dressing of the grinding wheels, work piece material properties, coolant type and delivery, etc…..
Please contact one our experienced engineers to help evaluate your grinding process today to see if superabrasives are the ideal solution for your grinding application.
CDT Now Offering Same Day Shipping on Select High Performance Grinding Wheels for the Cutting Tool Industry
If you are in the cutting tool industry and are interested in gaining a competitive edge with CDT's GL™ Series grinding wheels, contact our knowledgeable team of service techs today.
Last year Continental Diamond Tool Corporation introduced its Resin Hybrid Bond — custom formulated grinding wheels with a winning combination of durability, finish, and performance.
The Resin Hybrid Series is the superior option of superabrasive diamond and CBN grinding wheels for the cutting tool industry. Using the latest Advanced Bond technology, competitive trials have proven that the bond grinds up to four times quicker without losing the wheel edge. Flute from solid, regrind, gash and end work, and relief.
Resin Hybrid Bond is not your standard “one size fits all.” This bond is tailored to specific grinding applications, providing the highest quality tool with the most efficient performance. Its unique properties offer key advantages to the CNC Tool and Cutter Grinder in many ways:
Free cutting action with superior form retention and surface finish
Self sharpening bond lengthens wheel life and dressing interval
High material removal rate with high temperature stability
Maximum heat dissipation with low and constant power consumption
Optimal wheel profile stability lowers costs due to wear
Previously cutting tool manufacturers had to commission custom-designed Resin Hybrid wheels to get all these benefits. Now CDT is stocking our most popular shapes and sizes specifically tailored to cutting tool manufacturing at affordable, off-the-shelf prices. CDT wheels are compatible with most of the cutting tool industry's leading CNC Tool and Cutter Grinder machinery.
If you are in the cutting tool industry and are interested in gaining a competitive edge with CDT's Resin Hybrid Series grinding wheels, contact our knowledgeable team of service techs today. Tell us your requirements and we will check our inventory for availability or provide you a custom quote. Wheels in stock ship the same day!
Or call 800-443-6629.
Care and Maintenance of Diamond Wheels
A few simple steps to care for and maintain your diamond wheels will allow you to get the performance and durability you expect from them.
Diamond wheels provide the maximum performance and high-speed cutting on demanding materials. Proper care and maintenance will ensure that the wheel gives the superior results for the maximum time. The steps are not difficult and well worth the effort.
Installation
Make sure that spindles, back plates and flanges are always clean before installing a new wheel. Use a dial indicator to check that the rotation of the wheel is within 0.0005 inch, 12.7 microns, of true. Tighten the flanges once the wheel is true and double-check tightness before use.
Diamond cutting wheels should only be used to make straight cuts. Twisting or jamming the wheel can cause fatigue and segment loss. Excess pressure should not be applied when making cuts.
When performing any cutting or grinding process, all work materials require firm support. Excess overhang should be avoided; even slight tilting can create an angled cut.
Feed and grinding speed
Material must be fed into the wheel at the appropriate speed. A feed rate that is too fast will cause chatter and vibration. This will result in a poor cut and possibly damage the cutting edge of the wheel.
Diamond wheels work best at speeds between 5,000 to 6,000 surface feet per minute. Running at lower speeds can lead to glazing.
Dressing
Using the wrong cutting wheel, one with a bond that is too hard for the working material, will create glazing. The easiest way to avoid this is using a blade that is matched to the material. Dressing the blade is a maintenance technique, but dressing does slow down production and reduce the life of the wheel.
Dressing a diamond wheel cleans the build up of debris from cutting operations that block the abrasive surface. The resurfacing restores the sharp abrasive edges of the diamond coating. A dressing stick, normally aluminum oxide or silicone carbide, is used to cut through or remove the debris and expose new diamond material.
Make an arrow mark on the wheel showing the rotation direction the first time and always dress the wheel with it spinning in the same direction. Dressing a wheel in both directions will destroy it.
Dressing is accomplished by simply making a straight cut through the dressing stick or bar. Cut off a thin section per pass. Only one or two cuts through the stick should be required.
If a dressing stick is not available, a section of asphalt can be used. Make a few cuts into the asphalt and the blade should be clean.
Overheating
Coolant should be used for maximum results. The coolant needs to spray to contact where the cutting wheel and material meet. A weak soluble oil solution may be used to reduce corrosion.
If dark streaks form along the sides of the cutting edge, the wheel is being overheated. Excess heat can cause the wheel to break apart. If dry cutting is being performed, allow the wheel to cool for about 10 seconds for every 30 seconds of cutting operation.
Use the right grade wheel, designed for the material to prevent injuries from reactive force or throw back. Never use a wheel that shows signs of fracture, fatigue or broken segments.
Industrial Diamond Facts
Find out about industrial diamond shapes, quality and sizes as well how they are used in industrial settings.
Diamonds are used for many industrial settings due to the fact that they are the hardest substance known. Diamonds are a crystalline form of carbon, capable of assuming a variety of shapes, sizes and qualities and are used for grinding, cutting, drilling, polishing and as an abrasive in industrial applications. Although diamonds have a high cost initially, they often cut down on the total labor cost of industrial projects due their efficiency for cutting and grinding.
SIZE AND QUALITY
Diamonds used for industrial purposes vary widely in cost which is based on two factors--size (determined by carat weight) and quality. One carat is equal to 200 milligrams of 1/5 of a gram. Each gram represents five carats. A carat is further defined as having 100 points (the smallest unit of measure in the carat system). Therefore .10 equals 1/10 of a carat, 1.5 equals 1 1/2 carats.
Diamond quality is difficult to assess, determined by highly technical factors representing the considered judgment of a trained diamond expert. For industrial purposes, the best way to judge diamond quality is by performance. The better quality a diamond is, the more structurally sound each individual crystal will be. High-quality diamonds have better shape definition, allowing for longer service and quality dressing action desired on the grinding wheel.
SHAPES
Industrial diamonds can be shaped in a variety of ways as shown below:
New Haven Company Plans to Add 150 Jobs
Continental Diamond Tool is continuously growing and plans to add 150 new jobs by the end of 2023.
by ROSA SALTER RODRIGUEZ | The Journal Gazette
Monday, October 15, 2018 — Continental Diamond Tool, New Haven, plans to invest $5.5 million in real estate improvements and new equipment and more than double its workforce, according to an application for declaration as an economic revitalization area and tax abatements.
That would mean adding about 150 jobs, the application says.
The company last year moved from a facility at 1221 Hartzell St. to 10511 Rose Ave., both in New Haven. Now, the company is outgrowing that building, said Brian Yoh, New Haven's director of planning and economic development.
Plans are to add 15,000 square feet to it at a cost of $1.3 million.
"They are a very, very successful company," Yoh said Monday. "They're having phenomenal growth."
The equipment investment includes $3.575 million in manufacturing equipment and $625,000 in research and development and information technology equipment, according to the application.
Created will be 146 full-time manufacturing jobs at an average salary of $40,000 and four full-time sales positions at an average salary of $56,000. The hiring would be done by Dec. 1, 2023.
Four new part-time janitorial jobs at an average salary of $7,500 and six part-time manufacturing jobs at an average salary of $15,500 are also listed.
The company will pay at least 70 percent of the cost of eligible employees' vacation, sick leave, holidays, health and life insurance and pension benefits.
The company now has 135 employees and a payroll of $7.2 million. The additional employees would add $6.025 million in payroll by Dec. 1, 2023.
The building construction was planned to begin late last month and be finished by April, the application states. Equipment installation would begin then and go through December, 2023, the document states.
The company makes diamond and CBN superabrasive grinding wheels. Company officiaIs did not list gross sales or the company's three largest customers and suppliers, as the application requests.
If the application is approved, the company will qualify for 10-year abatements which would save it $194,266 in real estate taxes and $237,059 in business personal property taxes for a total of $431,325.
The New Haven Council will have a public hearing on the measure at 7 p.m. Oct. 23 at city hall, 815 E. Lincoln Highway.
Source: http://www.journalgazette.net/news/local/20181015/new-haven-company-plans-to-add-150-jobs
A Concise Guide to Single Point Diamond Dressers
Learn about diamond classifications and 10 tips for using single point diamond dressers.
Problematic grinding performance typically arises as a consequence of improper dressing. Choosing the correct diamond quality classifications greatly improves the expected quality of finished products. Moreover, the number of settable points will contribute heavily to acceptable dressing standards.
Classifications of Diamond Qualities
Grade A quality diamonds provide four+ settable points--smooth-surfaced octahedron or dodecahedron.
Grade B quality diamonds provides three+ settable points--possibility of inclusions, although they do not disturb the diamond's integrity.
Grade C quality--two+ settable points exhibiting blockish structure with superficial irregularities. This grade is the most common grade used in tool rooms.
Grade D quality--less than two settable points. Grade D's may have defects around less defined points.
Grade E quality--one settable point, "utility" grade diamond typically presenting cracks and other flaws.
Grade U quality--one settable point, "utility" grade cube-shaped diamond with an opaque surface
10 Tips For Using Single Point Diamond Dressers
1. Extend the life of a single point diamond dresser by inclining the tool at a 10 to 15 degree angle to the wheel radius. Point the tool in the rotation direction of the grinding wheel to maintain a consistently sharp point.
2. When dressing with Polycrystalline (PCD), grit, diamond single points or arbitrary stone tools, the infeed has to be .001 since a diamond dressing tool inevitably pulverizes the vitrified bond. Anything higher than .001 will cause cracking into the wheel--as much as .009 deep--that forces the bond to degenerate. In addition, gullets develop that produce loading by catching chips and overheating the wheel. Consequences of excessive infeed are chatter, bounce, bad finish and burn.
3. Sharply-tipped, crystal octahedrons should be utilized for straight dressings. For 46 grit and 60 grit wheels, crystal octahedrons shaped in a gothic style work well. Points associated with crystal octahedrons stay sharp if you turn the tool six to 12 indexes every revolution, or as necessary.
4. Make sure to use enough coolant to moderate dressing temperature, otherwise overheating occurs which may chemically transforms diamond into graphite. Diamonds will also suffer cracking if subjected to large temperature gradients.
5. The objective of dressing is to generate and expose novel, superficial cutting edges on the wheel. Single point diamond dressers achieve this objective by shattering existing gravelly grains and facilitating the emergence of desired abrasive particles. Dressing increases in-feed as well as feed and must be performed regularly to maintain optimal grain protrusion and grain edge sharpness.
6. Always begin dressing at the center of the wheel, which is the biggest diameter. Starting a dressing procedure at a wheel's side will probably result in shattering or even destroying the highest quality diamonds.
7. To prevent wheel taper, place the single point diamond dress as close as possible to the grinding area.
8. Grinding wheel grain sizes are contingent on longitudinal feeds, which significantly influences the structure of the surface of a grinding wheel. Additionally, reduced feed rates will predictably provide finer, more desirable surfaces.
9. Rotate the dresser 20 to 40 degrees in the shank if a flat appears on the diamond so that the dresser maintains an optimally conical point.
10. Avoid letting the diamond erode until the shank is visible. Doing so could allow the stone to dislodge or fall out.
CDT turns 45 this month!
Continental Diamond Tool Corporation proudly celebrates 45 years of growth
Continental Diamond Tool is proud to celebrate 45 years of business! Since October, 1973, we have worked hard to provide the highest quality precision products, and excellent customer service. Here's a quick overview of how we got to where we are today:
TIMELINE
1973
Ray Viggiano opened the doors on the first 5,000 sq. ft. building
CDT began production of Metal Bond products and Diamond Dressers
1978
Launched Resin Bond product line
1984-1985
Launched Plated product line
1989
First addition to building, now totaling 8,000 sq. ft.
1997
Second addition to building, more than doubling the size to 20,000 sq. ft.
2012
Third addition to building, again doubling the size to 40,000 sq. ft.
2014
Brought Vitrified Engineer on board, and launched Vitrified products line.
2015
Fourth addition to building, increasing to 55,000 sq. ft.
2016
Acquired Sierra Diamond, a manufacturer of Metal Bond tools, in Auburn, California.
2017
Launched new GL™ Series product line
2018
Acquired Consort Precision Diamond Co. Ltd., a leading manufacturer of Rotary Diamond Dressers in the United Kingdom
Completed construction of brand-new 130,000 sq. ft. facility
Began expansion to add an additional 15,000 sq. ft.
…and still growing!
Thanks for letting us share our story with you and celebrating in our achievements. Follow us on facebook.com/ContinentalDiamondTool to watch how we continue to grow and evolve.
The Plating Process - The How and the Why
Plating is a rather complex process, but the coating it provides to grinding wheels and other tools can add unbeatable strength and durability.
Diamond tools come in many different styles. One of the more commonly used types of diamond tools are those that have been electroplated. Understanding what exactly electroplating is, how the electroplating process works and what these tools are used for is important - especially if you plan to use any type of diamond tools in your machining process. That way, you can determine if these are the right solution for your machining needs.
What is Electroplating?
Electroplating is the process where a metal object is coated with a thin layer of another metal using electrolysis. For most applications these metal coatings are thin, less than .002 inch thick. With diamond tools, a strong layer of metal tool is electroplated to bond a single layer of diamond to the tool. This adds strength to the tool and additionally, it makes a tool that can grind even the hardest materials.
How Does the Electroplating Process Work?
A solution is created using a “salt” of metal coating plus water. This is referred to as an electrolytic bath. The object or tool that will be plated is placed in the electrolytic bath. Then, a metal bar is added to the bath. It may be the metal used for plating or another material that isn’t affected (insoluble electrode). After this, the object is connected to a source of direct current and the bar is connected as well. Once power is applied, the electrolysis process occurs creating a plating. Multiple layers can be applied to achieve the desired levels of plate.
What Are Electroplated Tools Used For?
The electroplated tools are stronger than even standard tools or composite tools. With the right plating, an old, worn tool or wheel can be sharper and stronger than ever. These are used in machining mainly for grinding or cutting processes. These tools are used in the manufacturing of components for the auto industry, medicine, aerospace, computers and factory work. The strength, affordability and usability of electroplated tools make them highly desirable within all levels of the manufacturing process.
Now that you understand more about electroplating and diamond tools, it may be time to determine the best options for your business. CDT (Continental Diamond Tool) sells new electroplated diamond tools, or we can work with you to electroplate your current tools to help you accomplish more than you ever thought possible. Call or contact us to learn more about our services and solutions we would love to work with you!
Machining and Composite Materials - The Basics
It's important to understand what makes composites different from traditional materials and the process involved with machining these compounds.
Composite materials, which are sometimes called composition materials, are created by combining two or more materials that have a significantly different make up of chemical or physical properties. When these materials are produced, the material produced often has characteristics that are different from the component materials that create it. Composites are very popular today in the manufacture of a number of different products, and they will likely only become more useful in the future.
Manufacturers choose composites for a number of reasons. Generally, the purpose is to gain the benefits of two different materials for example a lightweight material and a strong material. Composites are used within a number of different industries. From tools to golf clubs to ceramics, composites are an excellent choice for creating top-quality products.
The one problem with composite materials is that the means of working with traditional materials often do not work with composites. Machining composite materials is a challenge that requires a powerful solution. Continental Diamond Tools (CDT) Diamond tools do just that.
There are a number of diamond tool manufacturers out there, but many do not produce a tool that is adequate for the needs of working with some of the more complex composite materials. CDT understands the complexity and problems you may face when you are working with machining composite materials. We stepped up our production to meet the challenge and developed diamond products and technology that is specifically designed for this purpose.
CDT’s plated process is perfectly suited for composites. Our diamond tools provide outstanding cutting speed and efficiency for even the trickiest composite. Additionally, our engineering team specializes in helping our customer create a successful and cost effective solution for manufacturing needs. Whether working with metallic or non-metallic composites, the CDT diamond tools will provide the best possible results each and every time.
No matter what type of composite you work with, from FRP to fiberglass to Kevlar® aramid fiber, our products are the perfect solution. CDT’s electroplated wheels are useful for all areas of composites, including: automotive, boating, aerospace, sporting equipment (golf clubs, archery equipment, bicycles and scooters, etc), wind energy, and military applications.
Instead of worrying that your current machine process won’t get the job done or will fail when you need it most, switch to a process that is proven to achieve results. Call or contact us at CDT to discuss the composites you process and your current machine set-up. We can help you find the perfect diamond tools that can grind and shape your composites just as required.
Ribbon Cutting Event to Celebrate CDT’s New High-Tech Manufacturing Center
Continental Diamond Tool Corporation will celebrating the completion of its new manufacturing facility and corporate headquarters with a ribbon-cutting ceremony on Wednesday, August 8 at 10:00 a.m.
New Haven, IN – Continental Diamond Tool Corporation will be joined by the New Haven Chamber of Commerce to commemorate the completion of its new 130,000 sq. ft. manufacturing facility and corporate headquarters with a ribbon-cutting ceremony at 10511 Rose Avenue in New Haven, Indiana. The dedication will take place on Wednesday, August 8 at 10:00 a.m.
The new building, which triples CDT’s former manufacturing space, will accommodate new product development, growing customer demand, and increased employee amenities. Construction began in April 2017 and wrapped up this Summer.
Along with considerable state-of-the-art equipment upgrades, new research and development laboratories will allow CDT to further enhance their customer’s manufacturing productivity. The new headquarters also includes an impressive glass welcoming center with overlooking guest entertaining area, a complimentary barber shop and workout facility for CDT employees, and a modern break area featuring fresh food options and plenty of natural light.
With the growth, CDT is hiring for many positions; interested persons may apply online at www.cdtusa.com/careers.
About CDT
Founded in 1973 by Ray Viggiano, Continental Diamond Tool took shape with just two employees and 4,500 sq. ft. in New Haven, Indiana. CDT has developed into the leader for providing technically superior precision tooling to numerous industries. After multiple expansions, CDT now occupies its custom-built, state-of-the-art, 130,000 sq. ft. manufacturing center and corporate headquarters at 10511 Rose Avenue, New Haven, Indiana, USA. In addition, CDT owns rotary diamond dresser manufacturer Consort Precision Diamond in the United Kingdom, purchased in early 2018.
CDT continues to be a worldwide leader in the manufacturing of superabrasive products. Product lines include plated, metal bond, resin bond, vitrified, and CDT's own unique GL® bond diamond and CBN grinding wheels and tools, as well as diamond dressers and rolls. CDT's quality craftsmen welcome the opportunity to meet industry's most complex critical tooling needs.
Contact
For more information, please contact:
Sarah Fleek, Marketing Administrator
260-493-1294
Visit www.cdtusa.net for more information or find us on facebook.com/ContinentalDiamondTool
Why Cubic Boron Nitride Is Better Than Diamond for Grinding
Diamond grinding tools have always been an industrial mainstay but Cubic Boron Nitride (CBN) may be a better solution in many applications.
Diamond grinding tools have always been an industrial mainstay but Cubic Boron Nitride (CBN) may be a better solution in many applications. CBN grinding wheels provide the same benefits as diamond tools and even perform better in some applications.
The desirable characteristics of any abrasive include:
Hardness
Strength
Abrasion resistance
Thermal and chemical resistance
Ability to maintain sharp cutting edges during use
Hardness is perhaps the most critical property of every abrasive. Abrasives tend to lose hardness during application as a response to very high temperatures. One of the greatest advantages to using CBN is that it maintains its hardness at room temperature and over a wide variety of temperature ranges.
About CBN
CBN is the second hardest material after synthetic diamond. The process of making CBN abrasive is similar to that of synthetic diamonds: scientists treat hexagonal boron nitride at high temperature and pressure to create cubic boron nitride and treat graphite in the same way to create diamond.
About CBN
CBN is the second hardest material after synthetic diamond. The process of making CBN abrasive is similar to that of synthetic diamonds: scientists treat hexagonal boron nitride at high temperature and pressure to create cubic boron nitride and treat graphite in the same way to create diamond.
Machinists make CBN grinding wheels by plating CBN particles on steel, using plated nickel to hold grit in place. A single layer of CBN grit applied to the surface of a metal disc can grind even the hardest surfaces and last for years.
CBN has several attractive characteristics that make it superior to diamond:
Withstands heat, especially during high-speed applications
Does not cause grit that can dull bits
Stays sharp and cool because it does not react with steel
Diamonds can also react with transition metals, limiting their usefulness for grinding certain materials. Cubic boron nitride is stable and does not tend to react unfavorably with standard transition metals.
But What About Diamonds?
Diamond super-abrasive grinding wheels do have their advantages in some applications, especially in grinding abrasive or hard materials such as aluminum oxide, ferrites, ceramics, tungsten carbide, gray and ductile iron, and carbon. These grinding wheels also have the ability to cut freely with a cool cutting action, which is handy in applications where coolants could damage materials. Diamonds will likely remain a popular choice in many grinding applications in the future but nanotechnology may propel CBN into the top position.
Nanotechnology and CBN
In January 2013 issue of Nature, a scientist from University of Chicago’s Center for Advanced Radiation Sources and his colleagues reported they had been able to make ultrahard CBN by drastically shrinking grain size. The researchers were also able to rearrange the crystals into a zigzag formation of boron and nitrogen rather than in conventional flat layers to give it super resilience.
“Now, we can make this material as hard as single crystal diamond,” says the lead scientist, Yanbin Wang. “In some ways, it’s a better tool than diamonds, especially given its high fracture toughness.”
What to Look For When Choosing A Diamond Wheel Supplier
Look for these qualities when choosing a diamond wheel supplier.
The suppliers your company chooses can affect your business in many ways. Qualities like expert support, competitive pricing and speedy turnarounds can make significant differences in your success. Continental Diamond Tool is a world leader in the field of superabrasives for industries that include medical tool manufacturing, construction and aerospace engineering. Our small company philosophies and big company capabilities mean that you are in the hands of ethical, hardworking and capable support. Among the qualities that set us apart from the rest:
Speedy Delivery
Every day your supplies take to get to you is one that can hold up your operation. And, when you deal with another grinding tool supplier, you can wait as long as two months for your custom equipment, leading to slowdowns and delays.
We maintain an extensive inventory of raw materials so that we can complete your order fast in our in-house manufacturing facility. These allow us to supply an unlimited number of superabrasive products that fit your needs, timeline and budget. Our average shipping time is between 15 and 18 working days. We are proud of ability to create tools to order at a speed that gets you back to work as quickly as possible, saving you from expensive downtime.
Helpful Technical Support
Our commitment to you doesn't end when our product leaves the door. We have highly trained and knowledgeable staff that can help you with every phase of production, from prototypes to replacements, to improvements and enhancements. We can help you determine which tools are best for the job, how to implement strategies to make your company's work more efficient. Reach out to us for the assistance that will help you overcome obstacles and clear your way to success.
Global Outreach
Throughout the world, we offer support and custom tools to get the job done. Through innovation and commitment to customers, CDT has become the global leader in superabrasives in a wide range of industries. Our small company values, dedicated technical support and outstanding lead times mean that you can be sure that you can get the tools you need wherever you need them.
Competitive Pricing
CDT produces custom diamond wheels at competitive prices. We help people in all industries keep their costs under control to improve their bottom line and make their businesses more profitable. Our sales and manufacturing team work together to ensure that you are getting quality tools at an affordable price.
Since 1973, CDT has been committed to supplying a wide range of industries with the highest quality custom diamond tools. Contact us today to learn how we can serve your needs.
New 130,000 Sq. Ft. Manufacturing Facility Built with Customer and Employee Satisfaction In Mind
The new manufacturing facility for Continental Diamond Tool Corporation (CDT) offers new product development and increased employee amenities.
The new 130,000 sq. ft. manufacturing facility on Rose Avenue in New Haven, Indiana, built by Continental Diamond Tool Corporation (CDT) accommodates new product development, growing customer demand, and increased employee amenities.
The new space is built to improve both customer and employee satisfaction. Along with considerable state-of-the-art equipment upgrades, the new headquarters also includes an impressive glass welcoming center with overlooking guest entertaining area, a complimentary barber shop and workout facility for CDT employees, and an expanded break area with fresh food and plenty of natural light. New research and development laboratories will allow CDT to further enhance their customer’s manufacturing productivity.
In early 2017, CDT began construction on the new manufacturing center. This Spring, CDT began transitioning departments to the new space, starting with CNC machining, office personnel, and sales. Currently 75-percent of the company is up and running in the new facility, with the final department expected to move by the end of summer. With the growth, CDT is hiring for many positions; interested persons may apply online at www.cdtusa.com/careers.
About CDT
Founded in 1973 by Ray Viggiano, Continental Diamond Tool took shape with just two employees and 4,500 sq. ft. in New Haven, Indiana. CDT has developed into the leader for providing technically superior precision tooling to numerous industries. After multiple expansions, CDT now occupies its custom-built, state-of-the-art, 130,000 sq. ft. manufacturing center and corporate headquarters at 10511 Rose Avenue, New Haven, Indiana, USA. In addition, CDT owns rotary diamond dresser manufacturer Consort Precision Diamond in the United Kingdom, purchased in early 2018.
CDT continues to be a worldwide leader in the manufacturing of superabrasive products. Product lines include plated, electroless plating, metal bond, resin bond, vitrified, and CDT's own unique GL® bond diamond and CBN grinding wheels and tools, as well as diamond dressers and rolls. CDT's quality craftsmen welcome the opportunity to meet industry's most complex critical tooling needs.
Contact
To learn more about CDT and tour their new space, please contact:
Sarah Fleek, Marketing Administrator
sarah.fleek@cdtusa.net or 260-493-1294
Visit www.cdtusa.net for more information or find us on facebook.com/ContinentalDiamondTool
Grinding Wheels in the Electronics Industry
Grinding wheels and grinding tools of all types play a huge role in the electronic industry - even in ways that many people might not realize.
Grinding wheels and grinding tools of all types play a huge role in the electronic industry - even in ways that many people might not realize. Metal bond grinding tools are used to create a large number of the types of products that we use and love on a daily basis. By taking a look at the types of electronics devices that these important tools help create, you can start to see just how integral of a role they play in life as we know it.
Grinding tools like diamond drills, scoring disks and superabrasive endmills are used during the creation of printed circuit boards, which are a key component to many electronic devices that we find in our homes. If you own a desktop computer, laptop computer, high definition television set or home theater system of any type, you have the advancements enabled by circuit boards to thank for the hours and hours of enjoyment that you have received from these types of devices.
The types of circuit boards that are commonly made using grinding wheels and other grinding tools in the electronics industry are called printed circuit boards. These specific types of deices support various electronic components using tracks and pads that are conductive, allowing electricity to flow from one part of the device to another. The types of printed circuit boards that can be made using grinding wheels of all types include multi-layer boards. Single sided boards, which is a printed circuit board with only one copper layer, and double sided boards, which are a type with two layers of copper, are also commonly made using grinding tools like diamond drills for maximum precision. These types of printed circuit boards are traditionally found in almost every consumer electronic product that you can purchase, except those that are so simplistic in nature that they don't need a circuit board at all.
Part of the reason why diamond drills and metal bond grinding tools are so important to the electronic industry is because of the types of materials that they are capable of processing. Diamond tools in particular are capable of processing carbide alloys, stone, ceramics, semiconductor materials, aluminum, copper, copper alloys, rubber and resin. These types of materials are all used throughout the electronics industry in varying degrees. Copper and copper alloys in particular are hugely useful to electronic devices because they are both incredibly conductive with regards to electricity and resistant to erosion. As a result, they are ideal for situations like copper wiring, like the type that is used to transmit high speed signals into a person's home from a cable television provider.