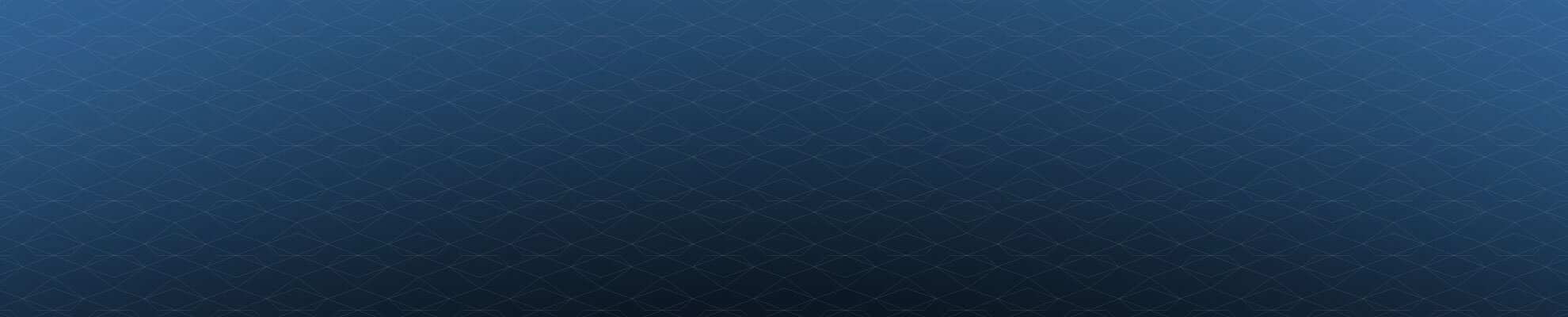
News and Resources
Browse by Category
Browse by Product
- All Dressing Products
- All Grinding Products
- CBN-Diamond Superabrasives
- Conventional Abrasives
- Diamond Lapping Compounds
- Diamond Rotary Dressers
- Diamond Stationary Dressers
- Hybrid Bond Grinding Tools
- Metal Bond Grinding Tools
- Plated Grinding Tools
- Resin Bond Grinding Tools
- Vitrified Bond Grinding Tools
Grinding Wheels In The Medical Industry
Discover the ways that diamond grinding tools are used in the medical industry: it may surprise you!
The medical industry relies on both brand new technology and old world skills and knowledge to help keep people healthy and heal injuries. One of the devices used in medicine that truly bridges the gap between old and new is the plated diamond wheel and other diamond tools. This device can be used in a number of procedures as part of a treatment plan that includes both new and old techniques. Learn a bit more about the use of these tools in medicine and you are sure to appreciate their flexibility.
Creation of Orthotics
Today’s orthotics and implants are more advanced than ever before. Creating these custom pieces of equipment requires careful work and precise sizing. Using plated diamond wheels is one of the best ways to cut the metal and plastic pieces with the level of precision required for these devices. Do some research and you will quickly see that nearly all of these types of medical devices are created using diamond wheels of some type.
Bone Sawing
Working in the emergency room or operating room requires a steady hand and a lot of hard work. However, this work can be made much easier with the right equipment for the job. Sawing bone is something that must be done for many different procedures. Fortunately, a quality diamond plated wheel can be used to saw through the bone with minimal effort and the best possible results. A bone saw is one of the most important pieces of equipment in any high-tech medical facility diamond plated wheels are of the utmost importance
Dental Uses
Diamond plated wheels are used extensively in the creation of dental burs and other tools. Only with the best wheels can you get the best possible dental equipment. Additionally, diamond wheels are used for bone sawing in the mouth too as a way of reaching areas that require serious oral surgery.
Other Uses
These are just a few of the ways that these diamond plated wheels are used by those in the medical profession. You’ll find that many of the devices used in a modern operating room or doctor’s office are shaped and designed with the use of a grinding wheel. Without this technique, the medical procedures of today would be vastly different and likely not as effective.
Now that you better understand the different ways that diamond plated wheels and similar tools can be used in medicine, your appreciation for the products is likely enhanced. If you want to learn more, contact one of the leading diamond tool manufacturers Continental Diamond Tool. One of our experts will be happy to explain more about how diamond tools are used in medicine as well as in other industries. Plus, we can help you find the best products and solutions available from CDT saving you time and money.
The Best Grinding Tools for the Oil Industry
Learn about the benefits of the various types of abrasives used in the oil and gas industry.
The grinding wheels used in petroleum engineering must be specifically developed to provide the performance needed for these applications. Common grinding applications in the oil industry include the manufacture of drill bits, gage blocks and wear parts. Superabrasives made from polycrystalline diamond (PCD) and carbide are common in this industry, especially for drill bits. Additional types of abrasives used on an oil rig include bonded abrasives and coated abrasives.
Benefits
The benefits of abrasives that have been custom developed for oil and gas applications include greater effectiveness, efficiency and tool life. Grinding tools need the latest bonds to deliver the precision needed for grinding the PCD and carbide bits used in modern drilling. These bits often use centerless wheels that offer a high cutting depth with high grind ratios, which cut costs during grinding operations. PCD abrasives are also used on tools that perform highly-efficient chamfer grinding.
Diamond Abrasives
Diamond abrasives usually refer to abrasives made with PCDs. They are most common in the manufacture of down-hole drill components such as drill bits made to gage. These bits are used in a variety of applications such as centerless, chamfer, form and surface grinding.
Bonded Abrasives
Bonded abrasives include resinoid abrasives and vitrified abrasives. Wheels that use these abrasives in the oil and gas industry can perform both precision and rough grinding applications. Components that are ground with wheels that use bonded abrasives typically have a hard face with a durable coating. These components include the following:
Couplings
Down hole stabilizers
Frac pump plungers
Pistons
Polish rods
Pony rods
Reamer shoes
Shafts
Valves
Bonded abrasives often use proprietary bond and grain formulas to provide performance gains over traditional abrasives such as silicon carbide and aluminum oxide. These benefits include longer grind cycles and a net reduction in cost per part.
Coated Abrasives
Coated abrasives may be used in a variety of forms such as belts, discs, rolls, sheets and wheels. These products are typically composed of cloth, fiber, film and paper for applications that include rough grinding, finishing, lapping and polishing. Products that use coated abrasives can be found in virtually every segment of the oil and gas industry, including petrochemical plants, oil reserves, pipelines and rigs.
Structured abrasives are commonly used to create a consistent finish, while flexible abrasives provide excellent results in high-velocity oxygen fuel spraying applications. Coated abrasives with an agglomerate grain are often used to improve performance with non-woven products such as convolute wheels, belts and discs. Users who wish to lower their total costs for coated abrasive products should consider ceramic belts, flap discs and specialty discs.
Choosing the Right Grinding Tools for the Aerospace Industry
Learn about the role that diamond-grinding tools play in the aerospace industry.
Abrasive technology is an important manufacturing process in many industrial sectors, including aerospace engineering. This technique requires the use of grinding wheels with coated abrasives such as diamond powder, which is extremely abrasive due to diamond's hardness. The best choice of material for bonding the abrasive material to the grinding wheel varies greatly and may need to be customized for a specific application. Diamond grinding creates surfaces with a smoother finish and sharper edges, which is often essential in aerospace research. Superabrasives provide better results in grinding operations that require greater duration, higher speed and cleaner cuts.
Hardness
The most significant factor in selecting the best abrasive material to use in a particular application is the hardness of the material being ground. The Rockwell hardness scales are the most common method of measuring hardness for these applications, especially the Rockwell C scale. This scale is commonly known as the material's RHC, which uses a 120-degree cone under a force of 150 kilogram-force to make an indention in the test material. The RHC measures hardness as a dimensionless number, with values between 20 and 100 generally considered reliable. Superabrasive grinding wheels typically become cost effective for materials with a hardness greater than 45 RHC.
Speed and Cutting
Grinding wheels have ideal ranges for operating speeds and cutting depth that primarily depend on the abrasive material. Diamond grinding wheels should operate at a surface speed between 3,000 feet and 8,000 feet per minute, such that greater speed is better for applications involving frequent interruptions or small areas of contact between the work piece and the grinding wheel. Operators should minimize the depth of the cut to create the best finish and extend the life of the work wheel. The maximum DOC for each pass depends on the particle size of the abrasive material. Abrasives with a grit size between 80 and 150 micrometers shouldn't cut more than 0.002 inches per pass, and abrasives with a grit size between 180 and 220 micrometers should be limited to 0.001 inches per pass. Grit with a size between 240 and 400 micrometers has a maximum DOC of 0.0005 inches per pass, and a 500 to 600 grit size has a maximum DOC of 0.0003 inches.
Bonding
The choice of bonding material is more complex than many of the other decisions involved in diamond grinding. The material comprising the work piece is a critical factor, as is the size of the abrasive particles. Aerospace engineers must also consider the operating speed of the grinding wheel and the type of coolant that will be used. Additional factors in selecting a bonding material include the type of bonding material and its hardness. Some grinding applications use electroplating rather than bonding to attach the abrasive material to the grinding wheel.
To find more information on which application is best for your project, contact CDT today.
The Importance of Maintaining your Grinding Wheels
Learn how to use dressing tools effectively so your grinding wheels will have a long and productive life span.
To understand how important it is to dress grinding wheels, you must first understand just how grinding wheels work. A grinding wheel is an abrasive cutting tool. It rotates quickly while in use and is very similar to a saw. However, a saw blade is only sharp along the edge. A grinding wheel has small sharp grains distributed over the surface of the wheel. Dressing grinding wheels is important maintenance.
When you press another material to the grinding wheel, its surface is gradually worn away. The results range from subtle to dramatic depending on the wheel and its intended use. Grinding wheels come in different materials. The surface material of the grinding wheel will decide what items it will work on. For example, aluminum oxide wheels work well on many steels, wrought iron, annealed malleable iron, and bronzes. Silicon carbide works well on rubber and stone.
Grinding wheels come in various shapes, including cup, dish, and cylinder shapes. The shape of the wheel typically changes over time with use. When you notice that the wheel's shape is different from that initially displayed, it’s time to discuss the matter of dressing grinding wheels. You have options available to you such as diamond dressers for grinding wheels and aluminum oxide dressing sticks. Each has its own distinctive features.
Grinding wheel dresser diamond tools are an extremely hard and efficient option. Diamonds are best known for their sparkle and elegance, but they also have a durable quality that makes them ideal for dressing tools. The hard diamonds score and reshape most dressing wheels very quickly and efficiently. A diamond dresser for grinding wheels will work with nearly any material. Choose the dresser design that’s best for your desired finish and get to work returning your grinding wheel to its former glory.
Aluminum oxide dressing sticks are a good option as well. Aluminum oxide is often used to dress tools made from diamond. The diamonds are easily sharpened with aluminum oxide. If the tool you’re working with is itself diamond, opt for this type of dressing stick to keep it maintained.
Dressers come in many shapes so you can restore any type of grinding wheel easily. A chisel dresser creates a fine contour. Plunge dressers are best for a concave radius. Grit dressers have broad even faces for fast dressing on a large surface. There’s a tool for any grinding wheel so you can always keep your surfaces in top shape. Plan to use your dressing tools often and your grinding wheels will have a long life span.
CBN Grinding Wheel 101
For projects that require intricate attention to detail, check out cubic boron nitrite (CBN) grinding wheels, their benefits, and who to trust as a supplier.
Cubic boron nitrite grinding wheels are used for projects that require intricate attention to detail. They provide a high-quality tool that will help you produce a beautiful, well manufactured product.
What is a CBN Grinding Wheel?
A CBN wheel is made from cubic boron nitride. This material is one of the hardest materials available, second only to diamonds. The main feature of the material is that it features a high abrasion resistance and thermal conductivity that maintains its sharp cutting edges. It’s a great choice when doing advanced products that require a high attention to details.
Why Use This Type of Wheel?
CBN wheels are important for grinding HSS. This is because it's a better material for sharpening and for durability, one of the best available. Diamond is harder than CBN, but over time many people have discovered that diamond is not a suitable abrasive grain and isn’t a good choice when grinding on high speed dry wheels. Choosing to buy grinding wheels with cubic boron nitrate will offer you the durability you need, while giving you the finished product you desire.
Benefits of CBN Grinding Wheels
These types of wheels have an almost indefinite life span when they are properly cared for. Many have chosen to use these wheels instead of the normal granular wheel because of their durability. The strong nature of the wheels comes from the bonding that takes place between the grains and the supporting steel hub. Thanks to this bonding feature, the wheels can be used dry without any coolant. Only a small amount of pressure is needed to sharpen a tool. The grind is very fine and there are almost no sparks when used for sharpening, unlike similar grinding wheels. The wheel remains cooler than a conventional wheel as well, making it nearly impossible to burn the tools. Choose certified wheel suppliers when looking for a grinding wheel.
Why Buy Grinding Wheels?
Those who have used grinding wheels have seen the benefits of the strong material. The main advantages are that it doesn't heat up when used for sharpening, it provides a perfectly balanced wheel, and has a low risk of blowing up. When it comes to your projects, time, and money, these are benefits that soon become valuable.
Choose certified CBN grinding wheel suppliers when looking for a grinding wheel. You’ll save time and money when you choose a supplier that is well versed in the benefits.
The Right Tools for Every Application
Certain manufacturing would never be possible without serious tools that do a tough job.
It’s not the discovery and control of fire that really separated man from the other animals – it’s tool-making that truly took the human race out of caves and into civilization. Tools changed the course of human history, and today they are still at the heart of every great item made by the hand of man. When you want to make amazing products, you need truly amazing tools. Get the right abrasive grinding wheels for your metal-shaping projects and you’ve got the tools you need to make your business a success.
Certain manufacturing would never be possible without serious tools that do a tough job. We carry everything from mounted grinding wheels to plated wheels, machinery to suit any type of manufacturing project. Isn’t it time you add large company capabilities to your business’s resume?
Grinding Wheels for Maximum Productivity
If it’s maximum productivity you need, look for CBN grinding wheels. The metal bonding on these wheels creates a very tough tool that holds its shape even after hard use. They’re commonly used in wet grinding. They work well on glass, quartz, silicon, ceramics and many other materials, including optics. This offers very low-maintenance, high-quality machining.
Replating for Extended Use
Have a used grinding wheel diamond bonded tool replated for long use. Once the bond has begun to dull, send the tool back to us. On an affordable plan, it’s easy to have that tool replated so that it performs like new again. These tools have an aggressive bond to hold form even after lots of use.
Grinding Wheels for High Efficiency and Precision
Copper or phonelic resin is at the heart of resin bonded grinding wheels. Use these when you want high-efficiency equipment that works precisely and quickly. They self-sharpen, and despite the superabrasive grinding they tend to stay at low temperatures. Use these wheels to polish, sharpen or grind at will. Like bonded wheels, these tools perform well for wet and dry tasks. Use them for glass, alloys, ceramics and many other materials.
Carborundum — the trusted name in grinding wheels
Look for Carborundum grinding wheels when you want a trusted, name brand tool. It’s a well-known name in the grinding business, and their tools are available in many different sizes and types.
Get the quality superabrasive tooling you need in one week or less with our fast delivery policy. Start manufacturing like a large company at prices even small companies can afford. You need the right equipment for every job to get the right results. Start with a company that has all the right machinery. Start with technical experts at Continental Diamond Tool Corporation.
Continental Diamond Tool has acquired Consort Precision Diamond
Continental Diamond Tool Corporation (CDT), an industry leader in Diamond & CBN grinding wheels and tools, today announces their acquisition of Consort Precision Diamond Company Limited, a leading manufacturer of Rotary Diamond Dressers in the United Kingdom. You can find them exhibiting together at GrindTec 2018 this week: Hall 4, Booth 4082.
Continental Diamond Tool Corporation (CDT), an industry leader in Diamond & CBN grinding wheels and tools, today announces their acquisition of Consort Precision Diamond Company Limited, a leading manufacturer of Rotary Diamond Dressers in the United Kingdom. You can find them exhibiting together at GrindTec 2018 this week: Hall 4, Booth 4082.
About CDT
Continental Diamond Tool, a private company located in New Haven, Indiana, is a leading producer in the global market for superabrasive grinding wheels and custom tooling. For more than 40 years, they have specialized in the design, manufacture and application of diamond and CBN cutting and grinding products and services. Their Electroplated, Resin Bond, Metal Bond, Vitrified Bond, and CDT-exclusive Hybrid Bond products serve a wide range of industries, including medical, oil & gas, automotive, aerospace, cutting tools, power generation, wood & saw, electronics, and many others.
About Consort Precision
Consort Precision Diamond Company Ltd is a private company established in 1984 by its shareholders as a manufacturing facility specializing in the production of Rotary Diamond Dressers for niche grinding operations. Their highly accurate precision components are used predominantly in automotive, aerospace and land-based turbine engine production.
For information on Consort Precision Diamond's Rotary Diamond Dressers, please contact our Customer Service at 800-443-6629 or info@cdtusa.net and they can assist you with a quote.
What should you look for in a grinding wheel manufacturer?
To get a product that meets your needs and will stand up to the use that is required, you first need to find the right CBN Grinding Wheel Manufacturer. Make sure you answer these 4 questions before choosing where you will purchase your next wheel.
When creating intricate projects that require precision, you will need a quality CBN (cubic boron nitride) grinding wheel. To make sure you are getting a product that meets your needs and will stand up to the use that is required, you need to find the right CBN Grinding Wheel Manufacturers. Not all manufacturers are created equal, so be sure to do some research before choosing where you will purchase your next wheel. Keep the following tips in mind when you are making your decision.
4 ways to identify the best grinding wheel manufacturer
When looking for a grinding wheel supplier, you’ll want to keep a few things in mind. Remember, your project and product need a wheel that will create a high-quality product and you need a supplier that will get you the wheel you need quickly and correctly, with no hassle.
First, ask yourself the following questions:
Is the supplier certified?
Do they have satisfied customers?
What kind of reviews is the supplier getting?
Where do the grinding wheels come from?
Getting some simple answers before you buy will help save your time and money in the long run. Abrasive suppliers offer a wide variety of products for many different kinds of grinding applications. Choosing the wrong product can cost the supplier time and money. Choosing the wrong supplier will cost you even more time and money.
Choosing the right grinding wheel
Now that you know where you are going to buy your next cubic boron nitride grinding wheel, you will need to know how to choose the right grinding wheel. To identify a quality grinding wheel, you should consider:
Are the abrasive grains distributed throughout the wheel?
What is the percentage of grain and bond? The percentages should be spaced throughout the wheel. The grains do the cutting while the bond holds the grain together.
What shape of wheel do I need? Most wheels come as a straight wheel. The grinding face is on the periphery of a straight wheel. Another variation of the straight wheel is the recessed wheel. The right grinding wheel supplier will have a knowledgeable customer service department that can assist you in finding the right wheel for your needs.
Other grinding wheel purchase considerations
The grinding wheel is only one component of a well engineered machine. The wheel, work material, and the working function all combine to create the tool needed for your job. Buying Diamond grinding wheels for carbide takes some time and attention. Be sure to do the research needed before making the investment. Choose the grinding wheel that is best suited for you needs, while taking into account all the components of the process.
Get a custom quote from an experienced supplier of cutting and grinding products now.
The Perfect Cut
Many industries call for the careful touch achieved by diamond-based tools. When you're in the market for a diamond saw blade manufacturer with whom you can build a successful relationship, make sure you go with a versatile company. You need someone who knows the ins-and-outs, not just of diamond saw manufacturing, but also of its uses and benefits. In order to understand all the advantages, you need an expert well-versed in the many uses of diamond tools.
Many industries call for the careful touch achieved by diamond-based tools. When you're in the market for a diamond saw blade manufacturer with whom you can build a successful relationship, make sure you go with a versatile company. You need someone who knows the ins-and-outs, not just of diamond saw manufacturing, but also of its uses and benefits. In order to understand all the advantages, you need an expert well-versed in the many uses of diamond tools.
When customers ask why they need to buy diamond saw blades above all others, versatility is generally the answer. In those industries where a perfect, polished cut is top priority, nothing does it better than diamonds. Because diamond plated and tipped saws grind rather than hack or cut, they lead to a smoother finish. For materials that leave no margin for error, such as marble and granite, composite materials, certain metals, quartz, ceramic, and fiberglass, mere cutting can ruin the finish. Always choose to buy diamond blades, as the super abrasive grinding creates a cleaner, more flawless edge.
The versatility of diamond tools continues. Be aware of the benefits of using a continuous rim diamond blade on wet and dry materials. In fact, using a diamond blade on wet or damp materials sometimes leads to a better, smoother cut. With concrete, granite, and certain kinds of marble, especially, wetting down the material is widely understood to create better results. However, when manufacturing medical tools, working with quartz or fiberglass, or dealing with carbine, a dry grind promises a look that is just as clean and smooth.
It's easy to see why it is so essential to choose a relationship with an expert company. Better still, look for manufacturers of diamond blade saws who guarantee quality work and understand the importance of quick delivery. A speedy turn-around practically ensures repeat business as everyone will be both happy and fully satisfied. It's a win/win situation for everybody. That's why it's essential to forge a solid relationship with a quality manufacturer who will get you the machines you need.
Diamond tip saw blades are the standard in many industries, especially those which depend on professional grade work with no mistakes. Whether you're making a memorial or working on the latest medical innovation, you want flawless craftsmanship created by a company that stands by its work, promises remarkable customer services in all areas, and understands how to manufacture solid, efficient diamond-based tools.
To get your custom quote, click here.
Which Blade Is Right For You?
If you're in the market for diamond sawblades, you may occasionally need some advice on exactly what you need, why these are the best choice, and where you should get them. It's important to first realize how essential it is to look for quality diamond blade manufacturer, so that you know you're getting a machine that will do exactly what you need.
If you're in the market for diamond sawblades, you may occasionally need some advice on exactly what you need, why these are the best choice, and where you should get them. It's important to first realize how essential it is to look for quality diamond blade manufacturer, so that you know you're getting a machine that will do exactly what you need. It's so much better to go with a company that understands the importance of quality work in a high-tech, professional setting, has an amazing customer service department, and provides quick turn-around for all products and tools. But what comes next?
Diamond blade saws are more than capable of cutting a variety of materials, so begin by thinking about your needs. For instance, do you want a saw that will work with different things or one that works best with something specific, such as stone or granite. Remember, a diamond cutting disc is excellent for cutting concrete and asphalt of all kinds, marble, ceramic, bricks, granite, carbide, quartz, optic materials, fiberglass, and many metals. With such far-reaching possibilities, diamond blades are the go-to choice in aerospace and medical engineering, construction, certain types of masonry, and stonework for statuary and memorials.
Next, remember that there's a difference between dry and wet cutting. Diamond blades grind the materials they go up against, they don't cut in the traditional sense. Grinding creates smoother, cleaner lines, so diamond saws chip far less and they're easier to control. However, with certain materials, the grinding does lead to dust. That's why those who work with stone, granite, concrete, and marble, especially, often prefer a wet cut. For work that demands a flawless finish, this is definitely one of the biggest benefits to consider.
One of the best reasons to buy diamond blades is because they're so long-lasting. The initial cost is a worth it, especially when you consider every aspect, such as the overall horsepower of the machine you intend to use, the diameters and hole sizes of the blades you choose, and the height and thickness of the segments in which you're interested. If you detail out exactly what you will need, you'll have a quality piece of equipment that you can easily use for years.
Above all, make sure you understand that you need to go with a reputable diamond blade manufacturer who knows what it's doing and does it well. A company that stands by the products it produces will always serve you better. Get a quote now
What do Scientists, Construction Workers and the Medical Industry Have in Common?
It sounds like a joke: What do scientists, construction workers, and the medical industry have in common? The answer is...
It sounds like a joke: What do scientists, construction workers, and the medical industry have in common? The answer is diamond cutting blades that let each do extraordinary jobs to make the world a better place. From shaping gemstones into dazzling creations that fit on the most slender finger to grinding through asphalt and concrete to make way for a new mall, these diamond cutting tools represent a marriage of power and precision.
When selecting a diamond cutting blade for a particular job, there are several things you should consider. First, what type or shape of diamond saw blades will work best? The circular blade gets wide usage because it handles so many tasks with ease. It’s also available in extremely slender forms. On the other hand, specialized diamond cutting tools work better for certain jobs. For instance, working with a gemstone requires smaller tools, so bonding diamonds to a thin wire is necessary.
You also need to think carefully about the kind of bond you want for your diamond cutting tools. The bond refers to the powder metals that hold the diamond to the base, and the bond is either soft or hard. Though it might seem a bit counter-intuitive, you want a soft bond on the diamond cutting blades when you’re grinding through very tough material. The softer bond falls away more quickly, allowing new diamond edges to make frequent contact with the material you’re cutting. By creating contact with newer diamond surfaces that are sharp, the diamond saw blades make a better go of cutting up hard material. Don’t forget to consider what size diamonds you need, what concentration of diamonds you need on the blade, and their toughness. Take your cues from the material you’re cutting as you choose the right diamond cutting disc for the job.
Regardless of what kind of work you’re doing, consider whether you need to use water with your diamond cutting wheels. Water reduces dust flying into the air during grinding. It also cools the diamond saw blades and helps give these blades longevity. So, usually, it’s advisable to use diamond cutting tools wet and not dry.
When ordering a diamond cutting disc, be sure to request the correct diameter, blank thickness, arbor hole, and slots. In addition, consider adding diamond plated ribs to your blade to reduce wear and help with side cutting. Also specify the kind of edge you want, either round or square, for your diamond cutting blades. Ask about any special requests you have about tolerance and the thickness of the cut.
An Update on New Facility — Now Hiring!
Continental Diamond Tool is happy to report that construction on its new facility is progressing steadily. The building's exterior is almost complete. Finishing touches will be made to the interior of the building over the next several months, with completion slated for Spring 2018.
Continental Diamond Tool is happy to report that construction on its new facility is progressing steadily. The building's exterior is almost complete. Finishing touches will be made to the interior of the building over the next several months, with completion slated for Spring 2018.
CDT broke ground at their new facility in New Haven earlier this year. This expansion cost nearly $12 million. The new building will also make room for 77 additional jobs.
The new 112,000 sq. ft. manufacturing facility will be equipped with state-of-the art equipment, allowing CDT to maintain their strong growth rate, better serve their customers and potentially double their employment base.
The project includes $5.25 million in manufacturing equipment, $400,000 in research and development equipment and $100,000 in information technology equipment.
If you or someone you know if looking for a new career opportunity, CDT is now hiring for the following positions:
CNC programmersCNC operatorsCNC set upManual MachinistsElectroplatersDraftsmen (proficient in SolidWorks)
Click here to apply.
Resin Hybrid Grinding Wheels are 'Gold' for the Cutting Tool Industry
Last month CDT released its response to the competition's hybrid wheels to handle the extreme cutting conditions in tool grinding. Cutting Tool manufacturers have been pleasantly surprised by the results.
Last month CDT released its response to the competition's hybrid wheels to handle the extreme cutting conditions in tool grinding. Cutting Tool manufacturers have been pleasantly surprised by the results.
In a head-to-head comparison, the competitor's fluting was originally done in two passes. The CDT Hybrid Bond achieved a single pass at double the feed rate with no damage to the workpiece while achieving a 25% increase in finish.
With equally outstanding primary and secondary grind results, the Hybrid Bond increased the primary and secondary operations by four times while continuing to produce a better finish.
The Hybrid Series for Tool & Cutter Grinding uses Advanced Bond technology, allowing for a quicker grind without losing the wheel edge. Flute from solid, regrind, gash and end work, and relief. Cutting Tool manufacturers will find:
Excellent precision at the highest feed rates
Increased productivity while lowering process costs
Superior wheel life and long dressing interval
Withstands cutting forces from high-speed, high-temperature applications
Because the Hybrid bond is not your standard “one size fits all” but is tailored to the specific grinding application, it allows for the highest quality tool in the most efficient amount of time in the Cutting Tool industry. This level of customization is unique to CDT's newest bond.
These one-of-a-kind properties improve the performance of the CNC Tool and Cutter Grinder in many ways:
Free cutting action with superior form retention and surface finish
Self sharpening bond lengthens wheel life and dressing interval
High material removal rate with high temperature stability
Maximum heat dissipation with low and constant power consumption
Optimal wheel profile stability lowers costs due to wear
If it's time to replace your old conventional worn parts with high quality precision grinding wheels and tools, you should consider CDT's Hybrid Series for Tool & Cutter Grinding. Backed by more than 40 years of superior craftsmanship and expertise in this field, CDT products are made in America and generally ship in 15 days. CDT customer service techs are happy to look through the parameters of your project, make recommendations, and supply a competitive quote - call 800-443-6629 for more information.
Do Your Grinding Wheels Need A Tune Up?
It's a fact that grinding wheels will endure wear and tear over time. Because of this, they require regular maintenance to keep them working like new, so grinding wheel dressers and dressing sticks become integral parts of the process.
t’s a fact that grinding wheels will endure wear and tear over time. Because of this, they require regular maintenance to keep them working like new, so grinding wheel dressers and dressing sticks become integral parts of the process.
Grinding wheel dressers are also known as grinding dressers or wheel dressers. Diamond dressers offer many benefits, some of which include a decreased dressing cost per piece, a constant high-precision operation, optimal dresser versatility, and fast dressing of even the most complex wheel profiles. Since different designs and applications call for different dressing tools, it’s important to work with a supplier that can help you determine which type will work best for your needs. Four of the basic types most commonly used with CNC grinders include stationary dressers, crush rolls, diamond crush rolls, and rotary dressers, all of which are used for grinding more complex shapes.
Aside from the grinding dresser itself, you may also need dressing sticks. These are stick-shapes made from a hard material, generally the same material as a dresser, but they use a stronger bonding agent. This gives them a harder composition than the grinding wheel. Properly selected grinding sticks can not only be used for dressing and truing conventional vitrified abrasive wheels, but they can improve the performance of CBN and diamond grinding wheels as well.
Fine particles will be flying off of the wheel during truing or dressing and it’s important to note that, when working with grinding sticks or any superabrasive tools, you should wear safety glasses in order to avoid eye injury. Remember to always store grinding wheel dressers and other metal tools in a dry location to avoid rust. Maintain a clean work area to cut down on the likelihood of injury and check for damaged parts before using any grinding wheel, dresser, or dressing stick.
Whether you use a CBN or diamond grinding wheel or other cutting products, having the right tools for the job is of the utmost importance. A company like Continental Diamond Tool can provide quality tools and custom manufacturing to suit your specific needs, with precision products and outstanding customer service without rival. Order products tailor-made to your project’s needs, produced by skilled technicians who can supply a finished product in as little as a week. Enjoy stellar customer service that will ensure, from start to finish, that you are getting the right product for your needs.
When the Material Gets Tough ...
When you need to cut through thick, abrasive surfaces, equip yourself with a diamond saw blade that has the power to tackle these kinds of jobs. Eliminate frustration by using the best tool for cutting through concrete, glass, marble, granite, and similar hard materials. Used extensively for shaping gems, slicing superconductors, and in construction, these diamond cutting blades offer both heft and precision.
When you need to cut through thick, abrasive surfaces, equip yourself with a diamond saw blade that has the power to tackle these kinds of jobs. Eliminate frustration by using the best tool for cutting through concrete, glass, marble, granite, and similar hard materials. Used extensively for shaping gems, slicing superconductors, and in construction, these diamond cutting blades offer both heft and precision.
The circular design is the most common. However, there are other kinds of diamond saw blades. Stone blocks that need cutting respond well to a grouping of diamond gang saw blades. These consist of diamond segments attached to a steel plate that has a sizable length. Band saws with diamonds typically have them placed on the teeth. Some industries get creative in developing their own tools using diamond blades. For example, diamond abrasives applied to wire become a precision tool for jewelry makers.
What makes a diamond saw blade special is its ability to grind up material and not cut it. Powder metals form the bond that holds the diamond segments to the blade. As the bonds wear down, new diamond surfaces get exposed, creating sharper angular surfaces for grinding. When deciding what type of blade to use, it’s best to select a bond that works well with the material you need to cut. For example, cutting a hard material requires a bond that gives way more quickly so that sharper diamond edges become available fast enough to grind the material.
There are three different ways to make diamond cutting wheels. Sintering and vacuum brazing are not as effective as plating. This process allows a layer of diamond bits to work while being exposed from the bonding agent, a set-up that’s preferable to having them actually embedded in the bond.
Plating allows you to preserve your tools by making it easy to refurbish the saw blade when it’s worn out. Instead of trashing the entire saw, you merely have the blade replated. With plating, it’s possible to remove the run down layer of diamonds and apply a new one. Because diamond cutting blade are restorable in this way, they’re a wise investment for any business or individual who uses them frequently. In addition, through the electroplating process, the diamond layer holds its form for an extended period of time, giving it superior performance. Even though it’s strippable, the abrasive bond is very strong. Plated diamond cutting tools typically last a long time because you can refresh them when the blades wear out.
Superior Craftsmanship
Dense materials once proved challenging to cut but CDT’s diamond tools provide quality abrasions while eliminating concerns of rough edges or heavy centers.
Dense materials once proved challenging to cut. Specialty diamond blades and tools, however, have redefined every line. These items provide quality abrasions, eliminating concerns of rough edges or heavy centers. Superior craftsmanship is effortless in carbide industries, engineering fields, stone carving and more.
Diamond plated saw blades provide users with ways to effectively grind down difficult materials, such as ceramics, concrete or asphalt. Their sharp teeth, known as segments, effortlessly move against an item and peel away its uneven layers. This creates a polished effect and streamlines abrasive operations.
The potential applications of diamond plated saw blades are endless, and there are now multiple saw designs to make those applications seamless:
Circular Saw: a small disc defines this tool, with diamond-infused teeth surrounding its edges. It's known for its accuracy and ease, with hand-held or table-mounted options available. The Circular Saw is the most common option for manufacturing.
Gang Saw: multiple diamond segments shape this slim, long-bladed saw. These segments are securely mounted to the edges, delivering sharp results. The Gang Saw is typically used for initial cuts, sliding across coarse materials and polishing them before more precise tools are applied.
Band Saw: the Band Saw features a flat design, with one side fitted with industrial diamond teeth. This creates a uniform process, with all cuts consistently delivered with every pass.
Choosing to buy diamond plated saw blades allows users to discover a wealth of possibilities. Industrial diamonds adapt well to materials, especially those noted for their density. Stone, coal balls, composites, fiberglass items and more all yield to these tools. Their even edges and steady cores ensure smooth finishes for every project. These options are also long-lasting, making them ideal for constant usage.
All saws require maintenance. Specialty diamond blades and tools are no exceptions. These items battle against hard materials on a regular basis. This can easily dull the blades, causing the grains to fade. Users must, therefore, remember to clean their saws regularly with dry cloths. Be certain that no unwanted particles are present and always note the condition of the diamond segments. If they're worn they'll be ineffective. Test them often to gauge their strength.
Many materials once seemed impossible to cut. Individuals who buy diamond saw blades, however, discover that those same materials are now easily transformed. Discover the convenience, and power, of diamond blades within a wide range of manufacturing fields. Choose CDT today.
Quality Tools and Quality Results
Diamond plated tools quality AND efficiency with their sturdy cores and sharp edges adapting to every need. Seamless manufacturing is now possible.
Every abrasive operation from engineering to optics, stone carving to carbide distribution requires quality tools and quality results. Diamond plated options now offer both, with their sturdy cores and sharp edges adapting to every need. Seamless manufacturing is now possible.
Dense materials (such as concrete, ceramic, coal or asphalt) are no longer a challenge to master. Instead diamond options provide ways to create even finishes every time. Their precise cuts prove invaluable for abrasive manufacturing and there are now items for everyday grinding, sawing and routing.
Abrasive grinding wheels are familiar sights within the manufacturing industry and diamond plated tools are quickly becoming just as familiar. These wheels boast industrial gemstones, whether mined or produced synthetically. They are then inserted into grinding machines (such as cylindrical grinders, bench grinders, wash grinders and more) and immediately begin to smooth out rough materials. They are usually applied to stone or carbide items, but can be used for a variety of tooling needs. Diamond grinding provides effortless results.
Diamond plated mounted saws, as their name suggests, are blades (whether circular, head-rigged or banded) that are infused with gemstones. They are exceptionally sharp, and this allows them to cut through almost any material without bending or breaking. They are most commonly chosen for concrete, bricks, asphalt and similar construction items. Their edges efficiently grind down surfaces and achieve a polished texture.
A router is an essential tool within any abrasive operation. Diamond plated routers, however, provide specialized results. These options can easily rabbit, round and bead once-resistant materials. They quickly hollow out stone, ceramics and more, allowing individuals to better shape their cuts. The industrial gems placed on the routing bits offer long-lasting strength, but can also be easily controlled. This allows them to adapt to most tooling needs.
There are many applications for diamond wheels, blades and routers. Users must remember, however, to maintain all equipment properly. The value of diamond plating is its efficiency. Without regular cleaning and care that efficiency will soon fade. Clear away particles; sharpen every edge. Doing this will protect the integrity of the tools and ensure strong results from now on.
Within the manufacturing industry there are many needs. Those needs can be addressed by a diamond grinding wheel, a diamond plated mounted saw or a diamond plated router. Choose the right option for difficult projects (such as ceramic cutting or shaping lathes) and experience exceptional cutting every day.
Hard Materials Demand Exceptionally Sharp Tools
Exceptionally hard materials demand exceptionally sharp tools. Diamond grinding wheels deliver consistent results, effortlessly getting the job done.
Exceptionally hard materials demand exceptionally sharp tools. Diamond grinding wheels are those tools. These options deliver consistent results, effortlessly peeling back layers and exposing the fine finishes beneath.
Grinding wheels, simply explained, are used during abrasive machining operations. Their coarse materials and rounded shapes create polished textures on even the most dense surfaces. Diamond options are no exception. Every wheel is bonded with industrial gems (pieces of coal that have been slowly compressed over time to strengthen their cores). This forms precise grinding edges, allowing the items to adapt to most tooling needs.
This is what enables diamond wheels to transition through a variety of fields: from carbides and medicine, to stonework and the aerospace industry. The applications are endless, making these pieces vital for every manufacturing environment.
These grinders have the ability to smooth out rough edges. Diamond options are, however, meant for particularly difficult projects. They are most commonly applied to gems, concrete, stone, ceramics and cutting tips (such as non-rotary items for lathes and linear planers). They can quickly, and thoroughly, reshape these materials, sparing users the constant worry of broken pads and uneven results.
It’s this trait that marks a diamond grinding wheel as a worthwhile option for any manufacturing field. Basic surface grinding””such as tapering gear teeth, jig cutting, concaving chisels or even twisting drills””simply will not suffice for every project. Instead diamond items, like their equally efficient Cubic Boron Nitride (CBN) grinding wheel cousins, are sometimes needed.
The most common grinding option in manufacturing is Aluminum Oxide. It’s applied to most surface tools and can prove useful for day to day demands. Its bonding principles won’t stand up to dense stones or jewels, however. It will instead fail. A diamond, therefore, becomes the only alternative.
All users must, of course, remember that every diamond wheel is only as useful as its current condition. These items must be properly maintained over the years. Remember to frequently clean the wheels, eliminating any unwanted particles. This will expose fresh grains and help to create a smoother finish. It will also reduce unwanted, and potentially dangerous, vibrations. A mounted grinding dresser is strongly recommended to streamline the process, keeping every piece centered and sharp.
Grinding wheels are essential to the manufacturing world. Diamond options simply provide more specialized efforts, transforming hard materials with ease. Consider them for concrete cutting, carbide reductions and more. The finishes will be forever fine.
The Right Tools for the Job
From cars to delicate eyeglasses, you need precision shaping, polishing and grinding tools. CDT makes the tools you need for each job.
Everything can’t be made from wood all the time. For everything else, from cars to delicate eyeglasses, you need precision shaping, polishing and grinding tools. Without the right tools, you can’t work with metal, glass, ceramics or many other materials used by different industries. Use super-abrasive tooling for those machining needs, and enjoy large company capabilities that allow you to handle many more products.
Take a look at plating grinding tools if you want to perform diamond grinding, shaping and polishing. Plated wheels have a single layer of tough diamond that’s exposed, rather than embedded, to create a highly durable bond. The secret of these plated diamond grinding wheels is their replating ability. Send your worn-down diamond grinding wheel to us, and we’ll set you up with an affordable plan so you get a like-new tool. Through the replating process, the tool is completely refurbished to work as it did when you first purchased it.
We have CBN grinding wheels made with the same plating process as well. Shop for plated hole saws or plated bank saw blades to start shaping and manufacturing all the products you want. Looking for a different type of CBN wheel? Look to our selection of metal bonded tools. Cubic boron nitride, CBN, is also used to make many metal bonded CBN grinding wheels.
The metal bonded process gives you a CBN grinding wheel that can handle ceramics, silicon, quartz, glass, optic materials and many other mediums. Metal bonded tools are very long-wearing and low-maintenance. Use them in both wet and dry grinding to complete your project.
Shaping and sculpting is all part of manufacturing, and you want your company involved in all types of manufacturing to appeal to the widest possible base of customers. Shop for super-abrasive tooling that will allow you to get the job done. With our industry best, fast delivery policy, you’ll have grinding tools in as little as one week after purchase. Our products have affordable pricing to give you large company capabilities without the big corporate price tag.
Start getting more done with your business, and get more customers. The right tools allow you to get many more jobs done. Expand your business, and start making more out of your company. When you can start making more products, the sky’s the limit on what you can eventually do. It all begins with good tools suited to the tasks you have on your list.
What You Should Know Before Picking A Supplier
CDT creates grinding wheels and tools in a variety of shapes and sizes so you know your tool will be right for the job from the start.
Diamond grinding wheels are available in a variety of commonly used shapes and sizes, but custom tools are often needed in specialized industries, including medical, aerospace, and ceramics. Weeding through professional grinding wheel manufacturers can be a daunting task, but custom-made surface grinding wheels are necessary for these industries.
Super abrasive products are used throughout the globe and are sought after by a wide assortment of customers. This means that diamond grinding wheel suppliers should be well versed in numerous applications, from electronics and composites to the oil industry, and everything in between. Look for a company that also specializes in plated, resin bond, and metal bond products, since different CBN wheels are designed for different grinding operations.
Cutting wheels consist of five major characteristics, including grain size, material, grain spacing, wheel grade, and bond type. Grain size determines the coarseness of the abrasive while the material indicates the actual abrasive itself, whether it is made from aluminum oxide, silicon carbide, ceramic, diamond, or cubic boron nitride. Grain spacing indicates the density of the wheel and wheel grade determines how hard or soft the bond holds the abrasive. Bond type affects the coolant, finish, and wheel speeds, and can be made of anything from rubber to metal.
Diamond wheels are made with diamonds, just as the name suggests. This gemstone is perfectly suited to grinding because it can stand up to extremely hard materials without breaking down. Some of the materials that diamond wheels are used to grind include other gemstones, concrete, and carbide cutting tips.
It’s important to go with a manufacturer noted for having the industry best lead time. Reputable companies often have a product ready and shipped within 7-10 working days, so never settle for anyone who doesn’t have the capabilities to have a custom super abrasive product ready in a week. Consider that the supplier should have personalized customer service that can pass on knowledge of the products as well, helping customers select the best super abrasive for their individual needs.
Continental Diamond Tool (CDT) is a leading provider of super-abrasives that maintains small company values but boasts large company capabilities, making them a highly sought after supplier. They specialize in the manufacture and application of CBN and diamond products used for both grinding and cutting, and are experienced in a wide range of industries. They also employ skilled experts with decades of experience, all of whom utilize the latest equipment to create a quality product unmatched in the industry.