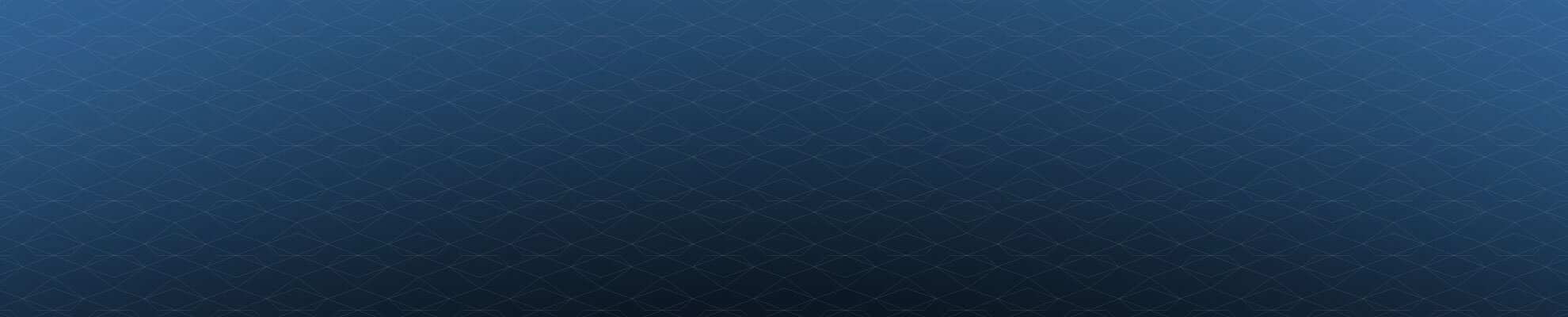
News and Resources
Browse by Category
Browse by Product
- All Dressing Products
- All Grinding Products
- CBN-Diamond Superabrasives
- Conventional Abrasives
- Diamond Lapping Compounds
- Diamond Rotary Dressers
- Diamond Stationary Dressers
- Hybrid Bond Grinding Tools
- Metal Bond Grinding Tools
- Plated Grinding Tools
- Resin Bond Grinding Tools
- Vitrified Bond Grinding Tools
Superior Craftsmanship
Dense materials once proved challenging to cut but CDT’s diamond tools provide quality abrasions while eliminating concerns of rough edges or heavy centers.
Dense materials once proved challenging to cut. Specialty diamond blades and tools, however, have redefined every line. These items provide quality abrasions, eliminating concerns of rough edges or heavy centers. Superior craftsmanship is effortless in carbide industries, engineering fields, stone carving and more.
Diamond plated saw blades provide users with ways to effectively grind down difficult materials, such as ceramics, concrete or asphalt. Their sharp teeth, known as segments, effortlessly move against an item and peel away its uneven layers. This creates a polished effect and streamlines abrasive operations.
The potential applications of diamond plated saw blades are endless, and there are now multiple saw designs to make those applications seamless:
Circular Saw: a small disc defines this tool, with diamond-infused teeth surrounding its edges. It's known for its accuracy and ease, with hand-held or table-mounted options available. The Circular Saw is the most common option for manufacturing.
Gang Saw: multiple diamond segments shape this slim, long-bladed saw. These segments are securely mounted to the edges, delivering sharp results. The Gang Saw is typically used for initial cuts, sliding across coarse materials and polishing them before more precise tools are applied.
Band Saw: the Band Saw features a flat design, with one side fitted with industrial diamond teeth. This creates a uniform process, with all cuts consistently delivered with every pass.
Choosing to buy diamond plated saw blades allows users to discover a wealth of possibilities. Industrial diamonds adapt well to materials, especially those noted for their density. Stone, coal balls, composites, fiberglass items and more all yield to these tools. Their even edges and steady cores ensure smooth finishes for every project. These options are also long-lasting, making them ideal for constant usage.
All saws require maintenance. Specialty diamond blades and tools are no exceptions. These items battle against hard materials on a regular basis. This can easily dull the blades, causing the grains to fade. Users must, therefore, remember to clean their saws regularly with dry cloths. Be certain that no unwanted particles are present and always note the condition of the diamond segments. If they're worn they'll be ineffective. Test them often to gauge their strength.
Many materials once seemed impossible to cut. Individuals who buy diamond saw blades, however, discover that those same materials are now easily transformed. Discover the convenience, and power, of diamond blades within a wide range of manufacturing fields. Choose CDT today.
Quality Tools and Quality Results
Diamond plated tools quality AND efficiency with their sturdy cores and sharp edges adapting to every need. Seamless manufacturing is now possible.
Every abrasive operation from engineering to optics, stone carving to carbide distribution requires quality tools and quality results. Diamond plated options now offer both, with their sturdy cores and sharp edges adapting to every need. Seamless manufacturing is now possible.
Dense materials (such as concrete, ceramic, coal or asphalt) are no longer a challenge to master. Instead diamond options provide ways to create even finishes every time. Their precise cuts prove invaluable for abrasive manufacturing and there are now items for everyday grinding, sawing and routing.
Abrasive grinding wheels are familiar sights within the manufacturing industry and diamond plated tools are quickly becoming just as familiar. These wheels boast industrial gemstones, whether mined or produced synthetically. They are then inserted into grinding machines (such as cylindrical grinders, bench grinders, wash grinders and more) and immediately begin to smooth out rough materials. They are usually applied to stone or carbide items, but can be used for a variety of tooling needs. Diamond grinding provides effortless results.
Diamond plated mounted saws, as their name suggests, are blades (whether circular, head-rigged or banded) that are infused with gemstones. They are exceptionally sharp, and this allows them to cut through almost any material without bending or breaking. They are most commonly chosen for concrete, bricks, asphalt and similar construction items. Their edges efficiently grind down surfaces and achieve a polished texture.
A router is an essential tool within any abrasive operation. Diamond plated routers, however, provide specialized results. These options can easily rabbit, round and bead once-resistant materials. They quickly hollow out stone, ceramics and more, allowing individuals to better shape their cuts. The industrial gems placed on the routing bits offer long-lasting strength, but can also be easily controlled. This allows them to adapt to most tooling needs.
There are many applications for diamond wheels, blades and routers. Users must remember, however, to maintain all equipment properly. The value of diamond plating is its efficiency. Without regular cleaning and care that efficiency will soon fade. Clear away particles; sharpen every edge. Doing this will protect the integrity of the tools and ensure strong results from now on.
Within the manufacturing industry there are many needs. Those needs can be addressed by a diamond grinding wheel, a diamond plated mounted saw or a diamond plated router. Choose the right option for difficult projects (such as ceramic cutting or shaping lathes) and experience exceptional cutting every day.
Hard Materials Demand Exceptionally Sharp Tools
Exceptionally hard materials demand exceptionally sharp tools. Diamond grinding wheels deliver consistent results, effortlessly getting the job done.
Exceptionally hard materials demand exceptionally sharp tools. Diamond grinding wheels are those tools. These options deliver consistent results, effortlessly peeling back layers and exposing the fine finishes beneath.
Grinding wheels, simply explained, are used during abrasive machining operations. Their coarse materials and rounded shapes create polished textures on even the most dense surfaces. Diamond options are no exception. Every wheel is bonded with industrial gems (pieces of coal that have been slowly compressed over time to strengthen their cores). This forms precise grinding edges, allowing the items to adapt to most tooling needs.
This is what enables diamond wheels to transition through a variety of fields: from carbides and medicine, to stonework and the aerospace industry. The applications are endless, making these pieces vital for every manufacturing environment.
These grinders have the ability to smooth out rough edges. Diamond options are, however, meant for particularly difficult projects. They are most commonly applied to gems, concrete, stone, ceramics and cutting tips (such as non-rotary items for lathes and linear planers). They can quickly, and thoroughly, reshape these materials, sparing users the constant worry of broken pads and uneven results.
It’s this trait that marks a diamond grinding wheel as a worthwhile option for any manufacturing field. Basic surface grinding””such as tapering gear teeth, jig cutting, concaving chisels or even twisting drills””simply will not suffice for every project. Instead diamond items, like their equally efficient Cubic Boron Nitride (CBN) grinding wheel cousins, are sometimes needed.
The most common grinding option in manufacturing is Aluminum Oxide. It’s applied to most surface tools and can prove useful for day to day demands. Its bonding principles won’t stand up to dense stones or jewels, however. It will instead fail. A diamond, therefore, becomes the only alternative.
All users must, of course, remember that every diamond wheel is only as useful as its current condition. These items must be properly maintained over the years. Remember to frequently clean the wheels, eliminating any unwanted particles. This will expose fresh grains and help to create a smoother finish. It will also reduce unwanted, and potentially dangerous, vibrations. A mounted grinding dresser is strongly recommended to streamline the process, keeping every piece centered and sharp.
Grinding wheels are essential to the manufacturing world. Diamond options simply provide more specialized efforts, transforming hard materials with ease. Consider them for concrete cutting, carbide reductions and more. The finishes will be forever fine.
The Right Tools for the Job
From cars to delicate eyeglasses, you need precision shaping, polishing and grinding tools. CDT makes the tools you need for each job.
Everything can’t be made from wood all the time. For everything else, from cars to delicate eyeglasses, you need precision shaping, polishing and grinding tools. Without the right tools, you can’t work with metal, glass, ceramics or many other materials used by different industries. Use super-abrasive tooling for those machining needs, and enjoy large company capabilities that allow you to handle many more products.
Take a look at plating grinding tools if you want to perform diamond grinding, shaping and polishing. Plated wheels have a single layer of tough diamond that’s exposed, rather than embedded, to create a highly durable bond. The secret of these plated diamond grinding wheels is their replating ability. Send your worn-down diamond grinding wheel to us, and we’ll set you up with an affordable plan so you get a like-new tool. Through the replating process, the tool is completely refurbished to work as it did when you first purchased it.
We have CBN grinding wheels made with the same plating process as well. Shop for plated hole saws or plated bank saw blades to start shaping and manufacturing all the products you want. Looking for a different type of CBN wheel? Look to our selection of metal bonded tools. Cubic boron nitride, CBN, is also used to make many metal bonded CBN grinding wheels.
The metal bonded process gives you a CBN grinding wheel that can handle ceramics, silicon, quartz, glass, optic materials and many other mediums. Metal bonded tools are very long-wearing and low-maintenance. Use them in both wet and dry grinding to complete your project.
Shaping and sculpting is all part of manufacturing, and you want your company involved in all types of manufacturing to appeal to the widest possible base of customers. Shop for super-abrasive tooling that will allow you to get the job done. With our industry best, fast delivery policy, you’ll have grinding tools in as little as one week after purchase. Our products have affordable pricing to give you large company capabilities without the big corporate price tag.
Start getting more done with your business, and get more customers. The right tools allow you to get many more jobs done. Expand your business, and start making more out of your company. When you can start making more products, the sky’s the limit on what you can eventually do. It all begins with good tools suited to the tasks you have on your list.
Which Type of Grinding Wheel Is Right For The Job?
Shaping metal is serious business, and for that you need serious tools like the grinding wheels from Continental Diamond Tool.
You can always work with materials that are easy to shape, like pipe cleaners, but if you want to build something strong you've got to build with metal. It stands up to wear and tear, and once you shape metal it stays that way. But shaping metal is serious business, and for that you need serious tools from grinding wheels manufacturers.
Metal shaping occurs in automotive repair and rebuilding quite commonly, but there are lots of other reasons you might want to shape metal. If you want to build anything brand-new or re-build something older that’s no longer up to par, you’ll have to shape the metal. This tough material gives you the firm foundation you need for your manufacturing projects.
But metal is tough and hard to work, so you’ve got to have the tools that get the job done. Choose the right surface grinding wheels for the tasks you want to carry out. If you do the job right the first time around, you’ll save yourself a lot of trouble and agony later.
When you want something high-efficiency that works quickly, you want resin bonded grinding wheels you can trust. You need something that spins true and cuts with precision, a self-sharpening tool that rarely needs maintenance. That’s exactly what you’re going to find from our resin bonded grinding wheels. They tend to stay at a low temperature even during use, decreasing your risk of burning your project. Use them for sharpening, polishing and all types of grinding work.
Your projects may need diamond grinders or CBN wheels. The plated bond is aggressive, and maintains its edge longer than other types of surface grinding wheels. These plated grinders can also be stripped and replated, prolonging use. Get your diamond grinders or CBN wheel replated by Continental Diamond Tool to affordably refurbish your tools. Use a plan to pay for the process, and you’ll have like-new tools for less.
Companies of all types shape metal, and it's used by manufacturers in medical, optics, aerospace and many other industries. With the right surface grinding tools, you’ll have large company capabilities to manufacture the items you need. The price is right to allow you to hold on to your small company values while delivering products that are worthy of a gigantic corporation. Get quality superabrasive tooling in as little as one week with our fast delivery policy, and get to work.
Your Tools Are Only As Good As Your Dresser
The proper grinding wheel dressing stone is essential for an efficient wheel. Assess your needs and stock up on quality dressing tools.
Your tools are only as good as the care you give them. A brand new product will work wonderfully at first, but nearly anything with a sharp point or fine edge will wear down over time. You’re probably familiar with grinding wheels for sharpening tools, but do you know how to choose and use the tools that keep your grinding wheel in working condition? The proper grinding wheel dressing stone is essential for an efficient wheel. When you’re choosing a dressing tool for grinding wheels, it’s important to understand all your options. A grinding wheel dresser diamond tool is the strongest choice. Other materials like silicon carbide or aluminum oxide are adequate for some wheels, but diamond consistently provides the best performance.
Dressing stones for grinding wheels are available in many different shapes. Choose from a single point diamond dresser with layered clusters, blade-type dressers with hand set diamonds, and grit dressers with uniform distribution of diamonds. Each dresser will give you a distinct finish. As you apply the grinding wheel dressing stick to the surface of your wheel, you’ll remove the top layer of the wheel and reveal a clean, sharp surface for future projects.
Dressing sticks aren't used exclusively on grinding wheels. The right dressing stick is important for maintaining other sharp tools as well. Diamond core drills feature a diamond tip that’s powerful enough to drill through nearly any material. The drill bit itself requires regular care to stay sharp and effective. Though the strength and capabilities of diamonds are certainly impressive, they don’t make diamonds infallible. You must regularly dress diamond core drills with an aluminum oxide dressing stick to keep them in top shape.
With a quality dressing stick, you can keep all your important tools sharp and well-maintained. Get to know every surface in your shop so you can instantly recognize when one is becoming dull and dirty. Grinding wheels can lose their efficiency quickly. You should always have a dressing tool for grinding wheels on hand to sharpen your tools. If you’re not equipped with a good diamond dressing stick, you’ll lose time allotted to active production while you wait for the proper items to arrive.
Assess your needs and stock up on quality dressing tools for every metal grinding wheel, drill, and surface that you use regularly. Dress your tools as often as you need to to keep them in top condition and functioning like new.
Industry Uses for Diamond Saw Blades
Diamond saw blades have many industry applications from healthcare to aerospace. Proper cutting, shaping and developing these materials is essential.
Because of their application in the medical field, diamond saw blades improve the quality of life for millions of people around the world. In healthcare, diamond blades assist in processes ranging from sawing bones during surgery to precision work inside blood vessels. Creating the ideal prosthetic involves skilled use of diamond saw blades. There are also multiple uses for diamond blades in the dental field including restorative work. Those who need care from an optometrist or ophthalmologist benefit from diamond saw blades that play a role in creating lenses and optical measuring tools.
When it comes to the aerospace industry, diamond blades have multiple applications. For example, these tools work on composite materials, titanium, graphite, Kevlar, and reinforced plastics. Cutting, shaping, and developing these materials is an integral part of the manufacturing and innovation process for aerospace engineers.
In the IT and electronics fields, engineers use diamond saw blades to cut semiconductors. Cutting semiconductors, which are brittle, is no easy task. It requires precision and care. These specialized blades work very well on these delicate materials. Likewise, a diamond blade cuts metals, ferrites, substrates, printed circuit boards, and other materials used to produce electronics.
One of the most useful versions of this cutting tool is the electroplated blade. Superior to blades constructed using the vacuum brazing and sintering techniques, electroplated diamond blades are easy to replate when the blade wears down. This process also utilizes a powerful bonding application while allowing for the removal of the layer when it’s time to replace it. These blades have one layer of diamonds, which are not embedded in the bond itself. Instead, the diamonds are exposed from the bond. Diamond saw blades made using the electroplating process may be very thin, making them ideal for doing precision work.
Being able to remove an abrasive from a diamond blade and apply a new layer helps you protect your tool investment and save money. Rather than replacing the entire tool, you merely get the blade replated. Reapplying the diamond abrasive gives your existing tool something akin to a reboot. It’s once again ready to tackle any task, whether it’s a construction, medical, or aerospace application.
To view some of our recent projects, click here.
Dressing or Truing: What’s the Difference?
Although sometimes known as conditioning, any time a grinding wheel is mounted on a machine it must be both trued and dressed to produce satisfactory work.
Any time a grinding wheel is mounted on a machine it must be trued and dressed to produce satisfactory work. These two terms are sometimes lumped together as “conditioning” but they mean different things. Inexpensive conventional abrasive wheels are relatively robust: dressing and truing can often be performed at the same time and repeated periodically. The same is not true for CBN and diamond grinding wheels.
These superabrasive grinding wheels represent a considerable investment, which should be repaid in longer life and higher productivity. However, achieving that performance demands close attention be paid to truing and dressing.
WHY TRUE A GRINDING WHEEL?
No matter how precisely manufactured, once a grinding wheel is mounted on a spindle there will be some eccentricity. Even if it's less than 0.001” it's going to affect the final size and finish of the workpiece, so to produce high-quality work the wheel must be trued.
One method of finding high spots is with a child's wax crayon. Spin up the wheel and bring in the crayon until it just touches: high spots will quickly gain a colored layer.
TRUING SUPERABRASIVE WHEELS
Conventional grinding wheels are easily trued with a diamond cutter that's harder than the wheel matrix. Diamond and CBN wheels can't be cut, and instead are effectively ground to size. While this can be done by traversing a conventional grinding wheel or sintered diamond roller across the wheel face, many machinists prefer to use a brake-controlled truing device (BCTD.)
Like the other methods, the BTCD presents an abrasive surface to the wheel, but turns more slowly. This speed differential results in a precise and controllable truing operation.
DRESS AFTERWARDS
Truing creates a smooth surface on the wheel periphery, and with no exposed grit the wheel won't cut. Dressing sharpens the wheel by removing bond material and fracturing the superabrasive grit to expose fresh edges, so dressing always follows truing.
A superabrasive grinding wheel is largely self-sharpening, although the workpiece material can cause it to dull or load-up. In such situations the grit starts to either rub against the surface or plow, (pushing material aside). Both affect surface finish, increase cutting forces and create heat, which can damage the workpiece. The solution is periodic dressing.
IMPACT OF WHEEL CONSTRUCTION
Resin and vitrified superabrasive grinding wheels have some depth to the matrix. This allows a wheel to be dressed and trued several times. However, plated and metal bond wheels have a much thinner layer of grit and can only be trued to the depth available.
What Feed & Speed Do I Run the Wheel?
High-speed grinding wheels, like the CBN grinding wheel and diamond wheel can increase a manufacturer’s production rates, improve quality and reduce costs.
High-speed grinding wheels can increase a manufacturer’s production rates, improve product quality, and reduce production costs. Two of the most popular superabrasive products used for these purposes include the CBN grinding wheel and the diamond wheel.
CBN wheels are made with synthesized crystalline material produced in a similar way used for growing manmade diamonds. This is done with high-pressure, high-temperature techniques, so CBN wheels are similar to diamond wheels in that they are resistant to wear and noted for strength.
Abrasive grains for CBN wheels are improving each year leading to more controlled strength and shapes that were once challenges in this industry. Whether a customer chooses to use a CBN wheel or a diamond wheel, it’s important to note which elements are significant in achieving the desired result.
The wheel diameter plays an important role, since the smaller the wheel the easier it is to use and, generally, the less expensive it is. Small wheels are also easier to handle and balance. Larger wheels, however, are more suited to faster operating speeds.
All grinding wheels have a hub that has to be designed with proper mounting techniques in order for it to operate at the highest speeds. This means having the wheel mounted to a spindle that keeps it from shifting even as centrifugal force pushes the wheel into greater speeds. Any type of imbalance will affect the wheel’s stability and could result in dangerous slippage. Experienced CBN and diamond wheel suppliers will have worked out any balance issues and develop a quality superabrasive that will always be balanced and work at high rates of speed.
Coolant is also important with diamond cutting blades and CBN wheels since it keeps the wheels from overheating. Coolant also provides adequate lubrication and flushes out any particles and chips that could interfere with the wheel’s performance. Dressing is another important aspect, which is accomplished with rotary diamond technology.
Whether your needs deal with applications in the aerospace, ceramics, automotive, oil, electronics, or medical industries, it’s important to find a superabrasives supplier that has knowledgeable customer service and skilled experts that provide custom-made cutting and grinding products. Continental Diamond Tool is a leading supplier that has based its business on blending customer relationship with product performance. They boast not only superior superabrasive tooling, but offer some of the industry’s best delivery times, super responsive tech support, and all the latest bond technology. The unsurpassed quality and professionalism of this customer manufacturer makes ordering superabrasives easier than ever.
How do I dress my grinding wheel?
Diamond dressing tools are essential to keep grinding wheels true and free from particle buildup. This enhances grain exposure and abrades away some bond.
In the manufacturing industry, you know you often need one type of tool to maintain the maximum efficiency and life of other types of tools. Diamond dressing tools are among those essential assisting tools that keep grinding wheels true and free from buildup of particles. This dressing procedure keeps grinding tools, drill bits, chisels, and other tools with points or edges honed to their required sharpness.
VALUE OF DRESSING WHEELS
Using the appropriate diamond dressers or other diamond products on these abrasive wheels performs three important functions: (1) trues or re-balances the wheel to a concentric shape; (2) dislodges buildup of abrasive particles and bits of metal, exposing new abrasive surfaces of the wheel for more accurate grinding; and (3) cleans the wheel, renewing its edge and revealing sharper abrasive and fresh grains.
STEPS TO DRESS A GRINDING WHEEL
Here are the steps to take to effectively and properly dress a grinding wheel.
Step 1
Determine the proper dressing tool for the wheel. Make sure the grit of the dressing tool is finer by one or two sizes than the abrasive surface of the grinding wheel. Also make sure you choose the appropriate shape of dressing tool to coincide with your grinding wheel.
Step 2
Turn your grinding machine's coolant pump off (if it has one).
Step 3
Turn on your grinding machine and allow it to operate until it reaches its full RPM; you might choose to turn off your spindle motor, or keep it running, based on your personal preference or experience. Excessive need for truing might dictate keeping the motor on, rather than turning it on and off.
Step 4
Using light to medium pressure, apply the dressing tool to your wheel's abrasive section; continue applying pressure just until the wheel stops rotating.
Step 5
Repeat Step 4 until the dressing tool until the grinding wheel feels as if it is pulling the dressing tool away from you.
Step 6
Repeat Steps 4 and 5 as many times as necessary (four to five times, typically), depending on your grinding wheel's surface condition.
IMPORTANT ADDITIONAL TIPS
Ensure the tool rest is the appropriate distance from the grinding wheel (typically 1/16th of an inch) to prevent damage to the tool or injury to yourself.
Always wear safety glasses to protect your eyes from flying particles.
Avoid wearing loose-fitting clothing, such as long sleeves, and pull back long hair, when working near a spinning grinding wheel.
Which Dressing Tool is Right for You?
Use our dressing tools to ensure that your diamond grinding wheel will perform at maximum efficiency, trouble-free, and enjoy a long, sustainable life.
A diamond grinding wheel dresser is a vital tool in the proper care and maintenance of any grinding wheel. Regular maintenance ensures that your diamond grinding wheel will perform at maximum efficiency, trouble-free, and enjoy a long, sustainable life.
When selecting any dressing tool, including a diamond wheel dressing stick, it’s important to choose the tool that is the proper shape, size, and quality for the grinding wheel. If you don’t know which tool will work best with your application, discuss it with a supplier’s knowledgeable customer service department to determine exactly what you need.
Dressing the wheel will knock off any abrasive particles from the wheel’s surface. This ensures that it’s balanced and concentric, which minimizes any vibration it may get from having too much buildup on the surface. These particles, if left on the surface, have the potential to cover up surface abrasives, making them dull and ineffective. Exposing them by removing particles is essentially a sharpening process, since the fresh abrasive grains are each cutting tools in their own right.
A diamond grinding wheel dresser serves another important function, and that is to clean the grinding wheel. Choosing a dresser or grinding wheel dressing stick that is softer than the grinding wheel will not dislodge any abrasive particles, and can result in a loaded wheel. This is why selecting the proper dressing tools is crucial to a successful grinding wheel dressing.
There are also different types of dressers to consider. Star dressers feature long handles and serrated discs. Diamond dressers are generally preferred because of their superior strength. They also have shorter handles and are great for both dressing and truing. They are also available in single point and multi-set clusters to blade-specific type, and a reputable supplier will be able to determine which design to use based on your project. For example, a single point tool is easy to use and encourages a more pronounced rotation and higher frequency, delivering precise results.
Other benefits of a diamond grinding wheel dresser include a fast dressing of even the most complex wheels, a constant operation that boasts high-precision, and optimal dresser versatility. This type of dresser tool also means a decreased dressing cost per project, making it a cost-effective solution to all of your dressing needs.
How do Superabrasives compare to conventional abrasives?
Superabrasive wheels do not wear away like conventional wheels, therefore your shop and the air you breathe is much cleaner.
Superabrasives 101
If you’re in the market for superabrasives, it’s important to be familiar with common terms and product types that can help you discover which superabrasive is best for your needs. The metal bond grinding wheel is one of the most commonly used wheels, and the name denotes the metal bonding material that is most often used with a variety of grinding wheel types.
Using metal fillers, grinding wheels suppliers will manufacture the metal grinding wheel to specification. Metal bond is available with cubic boron nitride (CBN) and diamond wheels, and are generally used with coolant to prolong the wheel’s lifespan.
There are several advantages to using metal bond wheels, not least of which is its extended life. A metal bond ensures that the wheel has a fast stock removal. It also leads to a reduction in the dressing frequency and boasts more advanced form holding capabilities. Metal bonds are also extremely strong, so they are typically used in internal, form, glass, ceramic, tool cutting, and creep-feed applications.
A grinding wheel dresser, often referred to simply as a wheel dresser or grinding dresser, is an essential tool that dresses the grinding wheel surface. Dressing a wheel knocks any abrasive particles from the surface in order to make the grinding wheel concentric. This means less vibration and an improved finish. The grinding dresser is also important when cleaning the metal bond grinding wheel. One of the main benefits of using a metal bond grinding wheel is that it requires dressing less frequently than other wheel types.
Metal bond even goes beyond grinding wheels, since diamond core drills, solid diamond drills, and disintegrating core drills can all be manufactured using metal bond. Metal bond is primarily used in wet grinding. It can work well on glass, silicon, semi-conductors, refractories, and ceramics. Many industries choose to use metal bond tools because they are low maintenance but offer high productivity, making them ideal for maximum yield endeavors. They are also available in a range of tools, from the more aggressive CNC grinding down to light polishing.
When searching for grinding wheels suppliers, go with a company experienced in custom manufacturing with a wide range of superabrasives, including metal bond. A reputable company will tailor every order to each individual customer’s needs and offer a knowledgeable customer service that can help you determine the type of tools and products you need. Going with an experienced superabrasives provider will result in unmatched quality and a pleasant buying experience.
What are the benefits of plated vs. bonded?
Our plated products consist of a single layer of Diamond or Cubic Boron Nitride (CBN) which offers the ability for strip and re-plate.
Grinding Wheels 101
A grinding wheel performs a range of abrasive machining operations in industries such as aerospace and petroleum. It can be made by pressing a matrix of coarse particles together into a circular shape, or by coating a solid material with the abrasive compound. The specific materials and shape of a grinding wheel depend on the application, although its manufacture is generally a precise process. Common types of grinding wheels include plated wheels, wheels that use resin to bond the abrasive compound to the wheel and those that use metal bonds.
Plated
A plated grinding wheel has a single layer of abrasive material that’s exposed to the surface, instead of embedding the material within a bonding compound. The abrasive material for this type of grinding wheel is typically cubic boron nitride (CBN) or diamond, which are extremely hard substances. Diamond plated wheels hold their form longer than bonded wheels, and they also form a more aggressive bond.
Plating provides diamond tool manufacturers with the ability to strip the abrasive material from the core product and re-plate it with a new abrasive layer. This advantage results in a plated diamond wheel that’s in “like new” condition, which extends the life of the initial investment.
Resin Bonds
The resins that bond abrasives to grinding wheels are typically phenolic resins, meaning that they are made by reacting phenol. The resin also contains filler materials such as copper and an abrasive material like diamond or CBN. A hot press compresses this mixture into the desired form, which is then cured and machined to a precise shape.
Resin-bonded grinding wheels are highly efficient, allowing them to complete their tasks quickly. These grinding wheels are capable of prolonged use, due to their ability to sharpen themselves and maintain low temperatures during operation. Grinding wheels that use resin bonds are also easy to dress and less prone to overloading. Common applications for these wheels include grinding electrical carbon products such as carbide alloys, ceramics, ferrite and semi-conductors.
Metal Bonds
The metal bonds used by grinding wheels are typically made by sintering powdered metals along with filler materials, and adding an abrasive such as CBN or diamond. These bonds are very strong, providing a grinding wheel that holds its shape well. The durability of metal bonds also means that these grinding wheels require dressing less frequently.
Metal bond abrasive tools offer maximum productivity, and are suitable for a range of applications, from light polishing to aggressive grinding. They’re most often used in wet grinding, but they can also grind dry surfaces such as ceramics, glass, quartz and silicon. Metal-bonded grinding wheels can be used for cutting tools and forms such as refractories. They're also suitable for creep-feed applications.