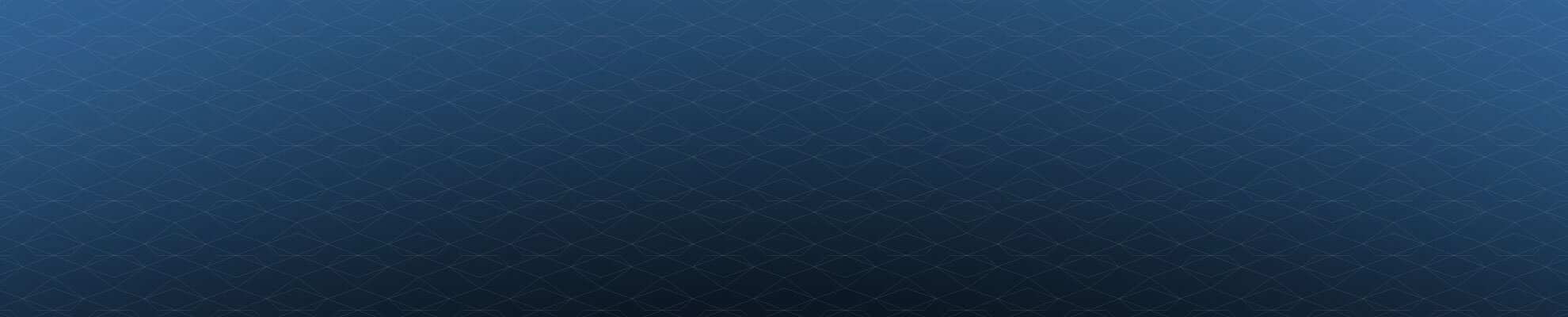
News and Resources
Browse by Category
Browse by Product
- All Dressing Products
- All Grinding Products
- CBN-Diamond Superabrasives
- Conventional Abrasives
- Diamond Lapping Compounds
- Diamond Rotary Dressers
- Diamond Stationary Dressers
- Hybrid Bond Grinding Tools
- Metal Bond Grinding Tools
- Plated Grinding Tools
- Resin Bond Grinding Tools
- Vitrified Bond Grinding Tools
What Is a Diamond Rotary Dresser?
Learn what Diamond Rotary dressers are you used for, the different types and where to purchase them. >
Grinding operations often work best with some form of wheel dressing to re-establish the wheel profile and/or recondition the wheel face. Wheel conditioning typically involves the sharpening and opening of the wheel face, while also removing dull abrasives, excessive bond, and workpiece material (loading). A sharp and open wheel face will allow maximum possible material-removal rates and reduced thermal stress on the workpiece. CDT engineers design each dresser to match your wheel topography so that it performs with superior strength and versatility. All are made with the highest quality CVD, natural diamond, synthetic diamond and combinations to maximize performance and roll life. Because they are custom manufactured, an abundance of configurations are possible.
Types of Diamond Rotary Dressers
There are two manufacturing methods for rotary dressers with several variations in setting/diamond application to best suit the customer application. Below are several examples:
1. Reverse Plated Diamond Roll
Manufactured with high accuracy molds and a tightly controlled electroplating process to deposit the nickel layer. The nickel layer holds the abrasive in place to allow for extremely complex profiles and tight tolerance work, which produce high quality surface finishes. Because of the accuracy on the front end of the process, these rolls require little to no surface conditioning, which leave sharp natural points for superior dressing, resulting in an open grinding wheel and lower grinding forces. Reverse plated rolls are ideal for continuous dress creep feed process, and complex forms like bearings, fuel injection, thread forms, and aerospace root forms.
2. Sintered Diamond Roll
Using a high temperature powdered metal process to create a tough tungsten matrix to secure the abrasive in the roll. This product is ideal for aggressive grinding and harsh working environment, while still holding tight profile tolerances and complex forms. These are all handset products, either pattern set or random set, to allow for a wide range of options on performance, surface finish, and roll life. Because of the manufacturing process, these rolls generally have shorter lead times and can usually be reworked to meet production demands. Sintered rolls are ideal for simple profile rolls to complex valve grinding assemblies.
3. Sintered CVD / Disc Dresser
These dressers use the same tough tungsten matrix as the standard Sintered rolls but are unique in the abrasive they are set with and how they are typically used. They are available using synthetic, natural, or CVD abrasive and can be set in combination to target specific performance, surface finish, and roll life. These are typically used to traverse across the grinding wheel to generate specific profiles and wheel conditions for open and free cutting grinding of the part. This style dresser is ideal for reconditioning, which can restore the roll to its original profile and tolerance in half the normal lead time and a fraction of the cost.
Where Can You Get a Diamond Rotary Dresser?
If you're looking to purchase a diamond rotary dresser, then you should know that Continental Diamond Tool Corporation is the final place to get them.
Experience
Since 1973, our family-owned company has built a reputation as a leading-edge manufacturer with a commitment to excellence.
Quality
Our engineers are highly specialized, and all our products are produced under stringent quality control standards.
Customization
We manufacture to your specific needs, providing you with specialized tools in a timely manner, with guaranteed satisfaction.
Precision
Our state-of-the-art equipment and expertise give our products some of the tightest tolerances in the industry.
Personalized Tech Support
From prototype to production, operations, or replacement tooling, our team works closely to get you the solutions you need.
Multiple Ways to Request an Estimate
Submit your project specifications and upload large files through our website: www.cdtusa.net/contact
Email details of your project with small file attachments to: info@cdtusa.net
Call our customer service team to talk through your project and discuss options: 800.443.6629
Why Choose Continental Diamond Tool?
There are a lot of reasons to consider Continental Diamond Tool, but we’ve narrowed it down to the top three reasons customers choose CDT. Check it out >
There are a lot of reasons to consider Continental Diamond Tool, but the top three reasons customers choose CDT are our high level of service, quality, and consistency.
Quality is the highest priority at CDT. We’re ISO Certified, with checks and balances in place to make sure each tool is the highest quality, every time.
Consistency means repeatability, so your tool is the same from one order to the next. You don’t deviate in your usage, so we have to nail it every time, with the tightest tolerances.
CDT has made customer service a main focus. Jeff Turner, Inside Sales, says, “It’s a priority that I take very seriously. Each customer should feel like they’re our biggest one.”
If you’re wondering why CDT, reach out to us. We will follow up so you can see if we can meet your needs, including our Grinding Lab, where we can show you first hand the benefits that you can get from our tooling.
Learn more about the reasons CDT is committed to you here:
What should you look for in a grinding wheel manufacturer?
Finding the right supplier of custom manufactured grinding wheels is crucial when your production is on the line. Here’s why you should consider trusting in CDT >
When you’re in search of a supplier of custom manufactured grinding wheels, we know you’re going to be focused on three main components: delivery, performance, and support.
At CDT, we deliver engineered solutions to help you complete your project on time. We will also meet or exceed any requirements you have for surface finish, tolerance holding, cycle time reduction, or anything else for which you are needing engineer solutions. We also provide support throughout the duration of the entire project, from beginning to end.
“We provide information and support all along the way,” says Harrison Sheldon, Application Engineer.
Watch our video to find out more about our commitment to excellence for our customers:
Top 10 Super Characteristics of Superabrasives
Here are the top 10 reasons you should consider a superabrasive solution for your precision grinding or finishing process. Check it out >
Superabrasive grinding products get their ‘super’ characteristics from the extremely hard substances used to make them. Unlike conventional grinding wheels that are created using blends of less durable abrasive grains, superabrasives use industry’s the hardest known substances to achieve their abrasive properties.
Diamond has the most extreme Knoop hardness rating around 7,000, with synthetic or manmade diamonds having a more consistent hardness than its naturally occurring counterpart. The other popular superabrasive material, cubic boron nitride (CBN), is an extremely hard synthetic grain with a Knoop rating of 4,700. Conventional grains typically range from 2,100 to 2,500.
Upfront cost for these superabrasive grinding products is very high when compared to conventional abrasives, so what makes them so valuable to many industries? The secret is in this product’s return on investment.
Here are the top 10 reasons you should consider a superabrasive solution for your precision grinding or finishing process.
10. Decreased Cost Per Part
9. Decreased Cost in Swarf Management
8. Increased Production Parts Per Dress
7. Multiple Profile Grinds Without Dress
6. Less Residual Stress or Damage to the Part
5. Increased Throughput
4. Lower Grinding Pressure
3. Higher Removal Rates
2. Improved Surface Finish
…and the number one reason superabrasive products are a ‘super’ solution to your grinding and finishing needs:
1. Lower Overall Tooling Costs
When companies add up the superior precision, efficiency, quality, and durability that comes with a superabrasive grinding wheels, superabrasive grinding wheels and tools quickly justify their upfront cost.
If you are interested in a free quote, contact our customer service team to discuss how a superabrasive solution can be used to improve your company’s bottom line.
What is the benefit of having a grinding lab on site?
Our grinding lab gives us the opportunity to work with customers to develop grinding processes that are specific to their materials, equipment, and applications. Learn more >
Here at CDT, we have a technologically advanced research and development grinding lab. This gives us the opportunity to work with customers to develop grinding processes that are specific to their materials, equipment, and applications. Our setup is unique, in that we’ve added numerous extra sensors to capture data on every element of the grinding process, to replicate what’s happening in the customer’s actual facilities.
We have a twofold product commitment to the Grinding Lab. One, we can develop processes for the customer and their specific application. Two, we can internally develop advanced new products that solve issues for customers before they are even known.
CDT’s customer service commitment includes the lab as well, inviting customers to reach out to us, to use our grinding lab to solve their grinding problems. Benefits to CDT customers include:
Faster product development
Cost savings/reduced risk
Opportunities to innovate
Valuable data
Remote product testing
Read more about these benefits here or watch clips of the Grinding Lab in action, and hear more about it from Jeff Wirth, our Engineering Manager in this video:
Why Superabrasives?
Superabrasive grinding wheels last longer, grind faster, cut cleaner, leave a better finish and create a sharper edge. The real question is—Why not?
When the material you are trying to process is either too hard or too delicate for conventional abrasives, custom superabrasive grinding tools might be the best solution.
What are Superabrasives?
The term “superabrasives” refers to a class of tools used in precision grinding for many industries. Superabrasive grinding products contain natural diamond, manmade diamond, and/or CBN — some of the hardest materials that can be made. Superabrasives are also sometimes called industrial diamonds: an industrial diamond is a non-gem quality small diamond that is for abrasives, cutting, and drilling tools. Other types of superabrasives include:
Cubic boron nitride (CBN): Usually called CBN, this is the second hardest cutting tool material after a diamond.
Polycrystalline: This is an abrasive material that has multiple collections of crystal grain structures with individual orientations.
CVD Diamond: These are synthetic diamonds made by a process known as chemical vapor deposition. CVD diamonds grow from a hydrocarbon gas mixture. They are extremely hard and have a high thermal conductivity that is five times that of copper. They also have broadband optical transparency, are chemically inert, and only reach graphitization at very high temperatures.
Nano-diamonds: These tiny diamonds are the product of a controlled explosion. They are sometimes called detonation nano-diamonds (DND) or an ultra-dispersed diamonds after how they are formed.
These abrasive materials have been labeled as superabrasive due to their extraordinary hardness, unparalleled performance, and longevity. Continental Diamond Tool uses these superabrasive materials to make custom grinding wheels and products, including plated, vitrified, resin bond, metal bond, hybrid bonds, and rotary dressers, for many complex applications.
Superabrasives vs. Conventional Abrasives
Superabrasives, whether natural or manmade, have a hardness range that distinguishes them as some of the most durable materials on Earth. Conventional abrasives are made with much softer abrasive materials that are less expensive but break down faster. The best abrasive product for your application depends on the material you are grinding and what properties you need to achieve your desired results.
Industries that Use Superabrasives
A great number of industries use superabrasive grinding wheels, and the custom-coated abrasives subsection of the abrasives industry continues to grow. Industries that regularly invest in superabrasive grinding wheels are:
Aerospace
Automotive
Medical
Electronics
Composites
Oil Industry
Advantages of Superabrasives
The advantages of superabrasive grinding wheels are more than extraordinary hardness, unparalleled performance, and longevity. These three features of superabrasives are the core of many advantages manufacturers gain by an aggregation of services that normal abrasives simply cannot deliver.
Benefits include:
Less expensive tooling and fixturing costs
More wheels on the spindle, smaller wheels, multiple operations
Less floor space needed for manufacturing
Virtual elimination of wheel wear
Automated CNC machines, less labor intensive operations requiring less training
Consistent surface speed from part to part
Better overall throughput with fewer machines needed
Improved material removal rates, lower per part abrasive costs, and higher speeds
With superabrasives, industries have been able to increase production with automated CNC equipment, compensating for a lack of available, skilled labor. With custom superabrasives that are optimized for their process, machine capabilities, and mechanization, there is less reliance on operator technique. A properly defined process, combined with automatic loaders, make for equipment that can even run itself in some cases with lights out manufacturing.
Industry Outlook
Future growth of the abrasives industries will primarily be in superabrasives. Currently, research and development of superabrasives are taking place in the following areas:
Custom designed “hard to grind” materials in an increasing number of industries
Creep or deep feed grinding
High-speed, high-performance grinding of hardened steel
Form grinding, sometimes with electroplating, in high precision, high-removal, and high-surface quality applications
CNC-control of line grinding machines
Continental Diamond Tool stays on the forefront of new abrasive technology developments in superabrasives with our state-of-the-art grinding lab focused on research and development of new hybrid bonds that take the efficiencies of superabrasives even further.
How to select the right superabrasive
CDT has a strong group of engineers, product managers, and technical sales people who can come out to your facility to review your equipment and processes, and the parts you’re looking to grind. Or, as Troy Giacherio, Product Manager for Rotary Dressers, suggests, “you can come into our facility and we’d be more than happy to have the conversation, review the whole development process, and then make our recommendations based on what we’ve seen and communicated.” Contact us for a free quote.
Learn more about superabrasive grinding solutions in this video:
How to Order Custom Grinding Wheels
Check out this guide on how to order custom grinding wheels that are a perfect fit for your operations.
Professionals in certain manufacturing industries use grinding wheels as a normal part of their abrasive cutting, grinding, and machining processes. There are numerous types of grinding wheels, as well as assorted types of abrasive materials and grains. Having and using the right tool for the job is essential, especially for precision manufacturing. It is important to determine what you need before you place an order or get a quote.
TYPES OF GRINDING WHEELS
These are only a few examples of numerous types of grinding wheels and their uses:
Centerless and feed wheels for creating extremely close tolerances on metal cylindrical parts, such as those for aircraft, automotive, and tool manufacturing
Cylindrical wheels for angular, plunge, and reverse grinding
Diamond and hybrid wheels for grinding extremely hard materials, such as carbide tips or concrete
Dish cup wheels for cutter and jig grinding
Mounted point wheels for deburring and profiling work on hard materials
Straight wheels, most commonly used for centerless, cylindrical, and surface grinding on bench and pedestal grinders
Tapered wheels for grinding gear teeth and threaded applications
TYPES OF ABRASIVES
Depending on the job you need to do and the type of grinding wheel you use, the type of abrasive you need varies. Examples of abrasives include:
Conventional: Aluminum Oxide (corundum), Ceramic, and Silicon Carbide
Superabrasive: Natural Diamond, Synthetic or Man Made Diamond, and Cubic Boron Nitride
At Continental Diamond Tool, we produce custom superabrasive grinding solutions. We can help you replace your conventional grinding wheel with the right superabrasive alternative.
ORDER GRINDING WHEELS
While some companies have local suppliers for their grinding wheels and abrasives, it's often more convenient to request a quote online, especially when you are looking to order custom grinding solutions. Here are the steps to take to order a custom grinding wheel:
Step 1
Determine the abrasive specifications required for the job. The proper grinding wheel is dependent on many factors including the grinder, coolant, material being ground, wheel dressing method, and more. To give you the best engineered solution for your grinding application, your supplier will need certain information to ensure you get the results you are looking for. Details you'll want to gather include:
Type of material: carbide, ceramics, concrete or stone, glass, or metal.
Type of grinder: manual or CNC
Type of grinding application: OD, ID, Cylindrical, Surface, Rotary Surface, Angle Head, Double Disc, Plunge, Traverse, etc.
Wheel diameter: varying from 0.008” to 40”
Thickness range: varying from 0.030” to 12”
Arbor hole size: varying from 0.040” to 20 inches
Desired finish: extra fine, fine, medium, or coarse (for minimal to heavy removal).
Coolant type
Dressing method & tools
Stock removal: If you know your selected abrasive material and required grit (varying from 20 to 8000 mesh), note that too.
Step 2
Call or use the online contact order form for your online supplier. For a custom grinding wheel, provide lots of detail about the type of tool you are using, along with its description, dimensions, and intended use. Continental Diamond Tool has a quote request form that walks you through the information we need to provide an accurate quote, and you can upload reference files if needed. Or you can always call us if you want to talk through the parameters of your project.
Step 3
At Continental Diamond Tool, we specialize in custom superabrasive grinding wheels and tools. Our team of engineers will work with you on a custom solution to your grinding needs. Depending on the nature of your project, we can run remote simulations or in-person trials and test prototypes before manufacturing the final piece. The whole process typically takes a number of weeks, but can be fast tracked if needed. At the end, our engineers will work with your team to guarantee that the grinding wheel is properly installed and performing as expected. They can also offer instruction on how to maintain your grinding wheel for ongoing high performance.
Stop getting by with a grinding wheel that isn’t optimized for the job. It's best to consult an expert to make sure your tool is a good fit for your process. In many cases, custom grinding wheels quickly pay for themselves with increased efficiency and extended tool life, and you'll see the difference to your company’s bottom line. It starts with calling 800-443-6629 or requesting a free quote online today:
Superabrasive Manufacturing: The Industries We Serve
Here’s a rundown of industries that are known to benefit from the toughness and precision of custom CBN and diamond grinding solutions through CDT. Check it out >
For industries that need to shape some of the world’s hardest substances like tungsten carbide, ceramics, and superalloys, only an extremely tough tool can do the job. Applications like these require grinding wheels and tools made with the most durable materials for cutting: natural or man-made diamond and cubic boron nitride (CBN).
Ironically, delicate substances like silicone also require the special characteristics that only these superabrasive materials can provide. With a wide variety of forms, grades, and bonds, CDT is proud to supply high-precision custom superabrasive grinding and finishing solutions for a variety of commercial, industrial, and military applications.
Here’s a rundown of industries that are known to benefit from the toughness and precision of custom CBN and diamond grinding solutions:
AEROSPACE & MILITARY
Top aircraft turbine manufacturers in the United States and around the world require precision plated form wheels and form mandrels in the manufacturing of turbine blades and other various engine parts. CBN grinding technology can be used for both the manufacturing of aircraft engine components and land-based turbine engine components. Efficient manufacturing needs shorter production runs and longer cycle times. Plated CBN wheels are the preferred choice for high precision form grinding applications of this nature.
CDT engineers are experienced with the demands of military and commercial aerospace applications, particularly in regard to turbine engine tooling and grinding solutions. We've even manufactured tooling for interplanetary use. As a leader in the manufacturing of diamond grinding tools for both air frame and aerostructure components, CDT is well-equipped to tackle this industry’s most challenging manufacturing needs.
For aerospace and military applications, superabrasive solutions are useful in working with:
Composites
Composite Material
Honeycomb Composites
Graphite & Kevlar
Reinforced Plastics
Titanium
AUTOMOTIVE
Over the years, CDT has proven to be a reliable partner to the automotive industry as a supplier of grinding tools for machining engine, chassis, and transmission components. We provide the continuous innovation, wide range of superabrasive capabilities, high quality standards, and delivery reliability that the automotive industry needs to stay competitive in an ever changing world.
The automotive industry uses superabrasive grinding products in the manufacture of many components such as:
Engines
Brakes
Steering, Suspension Systems
Parts
Rubber, Tires
Windshield Glass, Mirrors
Body Parts
CERAMICS
With extreme hardness that in some cases surpasses that of metals, the properties of ceramics offer unique opportunities and challenges for grinding in this industry. From circuit board parts, kitchenware, solar panels, pipes, and tubes to advanced technical ceramics and refractories, the ceramics industry manufactures a vast range of products that require the special characteristics of superabrasive wheels and tools. With our reputation for high precision diamond grinding wheels that work longer, cut faster, and are more durable, leaders in the ceramics industry regularly turn to CDT engineers to help them achieve their most demanding grinding and finishing requirements.
The ceramics industry uses superabrasive tools for the grinding and finishing of:
Glass
Brick, Refactories
Ceramics
Carbon, Graphite
Lavatory
Alumina
COMPOSITES, FIBERGLASS & PLASTICS
CDT has an electroplated process that is specially formulated for composites and provides outstanding cutting speed and efficiency. Our engineering team specializes in helping our customers create successful, cost effective solutions for their manufacturing needs. This applies to all types of composites, from FRP to fiberglass to Kevlar® aramid fiber. CDT's electroplated wheels have seen great success in all areas where composites are used, including: automotive, aerospace, sporting equipment (golf clubs, archery, bicycles, etc), wind energy, and military applications.
Many industries turn to superabrasive solutions when manufacturing requires these composite and fiber-reinforced plastic materials:
FRP Corrosive Resistant Material
Marine Fiberglass
Cultured Marble Types
Thermoset Resin Materials
Fiberglass Reinforced Plastics (FRP)
Composites
CUTTING TOOLS
For those companies involved in the manufacturing or resharpening of cutting tools, superabrasives have the strength and durability that such metal manipulation requires. Superabrasive tools that are custom designed to the required specs can reduce the cost per part, meet high-precision quality standards, and provide superior value.
Our engineering department has much experience achieving tighter tolerances and better performance, even with this industry’s extremely tough materials. A well designed custom grinding wheel can take a company to the next level, increasing efficiency while saving resources and time.
For the cutting tools industry, superabrasive tools are superior at grinding and finishing metals such as:
Carbide
High Speed Steel
FOOD PROCESSING, PAPER & CARDBOARD
Manufacturers of cutlery and hand tools turn to CDT superabrasives for many grinding applications. Cool cutting, fast stock removal, excellent finish, superior wheel life, and an attractive return-on-investment are prerequisites for success in the demanding grinding required in food processing and paper/cardboard.
Industries involving food processing, paper, and cardboard use superabrasive grinding products in applications such as:
Blade & Knife Sharpening
GEM
Precious Stone
Semi-Precious Stone
Corrugated & Flat Cutters
GEARS
CDT is a partner to the gear industry. Our areas of expertise include grinding wheels for virtually every operation needed in the production of gears and gear components. More broadly, our custom engineering department helps companies develop products that will maintain and improve production efficiencies on a continuous basis for whatever the customer’s need.
The gear industry uses superabrasive tools in the manufacture of:
Gear, Thread
Gear Guide, Bed
MEDICAL/DENTAL
From bone sawing to intravascular applications, CDT is regularly commissioned to engineer high precision tools for medical use. Our engineers understand the thorough testing and quality processes associated with medical device manufacturing . Our products are designed with exacting standards to achieve the tight tolerance demanded by this industry.
Medical and dental industry uses for superabrasive tooling include:
Prosthesis
Dental Instruments
Surgical Equipment
OIL & GAS
When the oil and gas industry has a job that calls for high precision grinding of carbide and PCD drill bits, wear parts, and gage blocks for oil and gas drill manufacturing, efficiency and effectiveness are extremely important. ID grinding is an exacting process that requires unparalleled precision for reliable, repeatable results. And, this industry’s CNC OD Grinders have their own unique challenges in these most difficult center-type grinding projects.
CDT has developed superabrasive advanced bond technology perfectly suited to all these needs of the oil industry. We also custom engineer each tool for longer tool life and a high stock removal, making it the best value in the industry.
The oil and gas industry turns to superabrasive tools for:
PCD/Carbide Grinding
I.D. / O.D. Grinding
POWER GENERATION
CDT has the capability to produce thousands of precision-built superabrasive products of high quality, performance, and repeatability for virtually every conceivable manufacturing area involved in power generation. The diversity in this industry calls for Vitrified, Resin Bond, Plated, and Metal Bond Diamond and CBN products to get the job done.
For the power generation industry, superabrasive tools are most commonly used in the manufacture of:
Wind Turbine
Gas & Steam Turbine
Marine Turbine
Blades
WOOD/SAW
CDT is experienced at supplying custom superabrasive products for the lumber and wood products industry. We provide grinding solutions for OEM manufacturers, filing rooms and service shops for their processes of manufacturing and maintaining band saws, circular saws, chippers, planers, and paper knives. All in all, our grinding wheels are designed to help our customers maintain and improve production efficiencies on a continuous basis.
Industry leaders in lumber and wood products use superabrasive tools for applications such as:
Carbide Tip Saw Blades
Band Saws
Knife Sharpening
OTHER MARKETS
Continental Diamond Tool has been providing technically superior precision tooling solutions to numerous other distinct industries since 1973. Over the years, we have witnessed more and more companies realize the productivity increases possible with the use of custom superabrasive products. With more parts processed per wheel and fewer wheel changes, many see how investing in this level of quality and durability pays off.
Along with those highlighted above, below are additional industries who have turned to CDT for superabrasive grinding solutions:
ELECTRONICS
Ferrites, Magnetics
Substrate (Ceramics, Glass, IC)
Quartz Crystal
Semiconductors
Printed Circuit Boards
OPTIC & PRECISION
Lens, Prism
Measuring Instruments
STONE
Lapidary Tools
Refractory Brick
Peek Materials
Granite
TOOL & DIE
Cemented Carbide Tool & Die
Special Steel Tool
Molding Die
Bearing
Pneumatic, Hydraulic, Valve
Jig
WIRE & CABLE
Precision Die
6 Common Grinding Problems and How to Solve Them
We discuss six common grinding problems and offer solutions to help you solve some of your most challenging grinding issues. Check it out >
Most grinding problems affect one of two categories: either appearance of the workpiece or productivity and return on investment. After verifying that the grinding machine isn’t at fault, there is one likely culprit causing your grinding problems: your grinding wheel.
Poor surface finish, chatter, and burning all affect the appearance of your product. Productivity issues like short wheel life, slow or inefficient cutting, or the wheel not cutting at all are also costly problems to have.
Let’s take these one at a time to see how a fix to your grinding wheel can solve some of your most challenging grinding issues.
1) POOR SURFACE FINISH
WHY YOUR GRINDING WHEEL MAY BE AT FAULT:
In the appearance category, poor finish is a common complaint when your grinding wheel isn’t optimized. Grinding is a multi-point cutting process, but broken down to the microscopic level, it has similarities to a single point operation like turning. Viewed this way, it’s easy to see how surface finish is affected by the same factors: the more material removed by each grinding point, the bigger the individual chips and the rougher the surface.
SOLUTIONS:
Select a grinding wheel with a finer grit size
Reduce the relative speed between the wheel and workpiece
OTHER POSSIBILITIES:
If grinding wet, the coolant may not be efficiently removing chips from the workpiece or wheel interface.
It's also possible that the wheel is being dressed excessively, creating grinding points that are standing too proud of the wheel surface.
2) CHATTER
WHY YOUR GRINDING WHEEL MAY BE AT FAULT:
Recognizable by a distinct, often audible, pattern on the workpiece, chatter has many causes. Wheel-induced chatter occurs when an out-of-true grinding wheel acts as an excitation source.
SOLUTIONS:
In this case the wheel should be trued carefully.
Also check that it isn’t slipping on its mount.
OTHER POSSIBILITIES:
If the problem is tracked down to a vibration in the machine — possibly some kind of resonance — the solution is to vary the grinding speed. Try going 10% faster or slower to remove the forcing excitation.
A detailed discussion of chatter is available at the Abrasive Engineering Society website.
3) BURNING
WHY YOUR GRINDING WHEEL MAY BE AT FAULT:
Machinists use the term “burning” to describe thermal damage. It can show up as cosmetic discoloration, changes in workpiece hardness, and possibly distortion-inducing internal tensile stresses. Burning can occur if the wheel is glazed or loaded, causing more rubbing and friction. This often occurs if the machinist is trying to push the wheel through the workpiece too quickly or using a wheel that’s too durable.
SOLUTIONS:
Dress the wheel with the correct dressing tool
Reduce the feed rate or the relative velocity between wheel and workpiece.
OTHER POSSIBILITIES:
Burning is far more common when grinding dry, although can still be experienced in wet grinding if there isn't enough coolant flow to carry away the heat.
See “Burn Awareness”, originally published in Cutting Tool Engineering, December 2000, for more information.
4) WHEEL LIFE TOO SHORT
WHY YOUR GRINDING WHEEL MAY BE AT FAULT:
This costly issue can be caused by a wheel that's either too hard or too soft for the workpiece. When this is the case, the grinding wheel loads up or wears away too quickly.
SOLUTIONS:
Try a grinding wheel manufactured with a different material that is better suited for your grinding operation.
OTHER POSSIBILITIES:
Insufficient coolant
Dressing your grinding wheel too frequently
Wheel speed too low
5) WHEEL CUTTING SLOWLY
WHY YOUR GRINDING WHEEL MAY BE AT FAULT:
This productivity issue is usually caused by feeds and/or wheel speeds that are too low. If you are using the wrong type of grinding wheel, you may be forced to cut slowly to avoid burning, but ultimately that’s not efficient for your process.
SOLUTION:
The solution is to find a wheel that can grind as fast as possible without burning. A grinding wheel specialists can suggest alternatives that will increase speed for your specific operation.
6) WHEEL NOT CUTTING AT ALL
WHY YOUR GRINDING WHEEL MAY BE AT FAULT:
Most likely, this happen when the grinding wheel is glazed by truing.
SOLUTION:
The solution is to dress the wheel lightly until the grit opens up. For dressing advice, consult with a grinding specialist.
OUR BEST ADVICE
THINK LOGICALLY
Most grinding problems can be solved by tracing the fault back to basic principles. With all grinding applications, imagine your material being removed by individual cutting points. Thinking from this perspective, a solution usually emerges.
Also, use your resources. The grinding experts at CDT are happy to discuss your cutting and grinding issues and offer solutions that will set your manufacturing operations on track to success.
Does CDT Carry Stock?
A lot of customers ask if we keep stock inventory on the shelf. Check out the answer in this article >
A lot of customers ask if we keep stock inventory on the shelf.
Because our customers’ needs are diverse, there are not a lot of common tools used across industries. Therefore, it is really most beneficial to us - and our customers - to only build custom. This gives us the flexibility to deliver exactly what the customer is looking for in a timely manner.
Customers are often surprised at how quickly and affordably we can deliver custom grinding wheels. We manage our inventory, control our overhead, and keep our costs low, so we can pass those savings on to our customers.
Watch this video to learn more.
To get started with custom superabrasive grinding wheels from CDT, contact us for a free quote.
How much does a Custom Superabrasive Grinding Wheel Cost?
We look at the 'total cost' of a custom superabrasive grinding wheel from CDT, and detail the advantages superabrasives have over conventional grinding products. Check it out >
A Look at the Bigger Picture >
As a custom-made product, the cost of a superabrasive grinding wheel can vary greatly from one design and application to the next. People may shy away from custom products because they think one of two things: it’s going to cost a lot more or it’s going to take a long time to complete. While that may be partially true on the surface, that’s not the whole picture.
In this article, we’re going to take a look at some of the factors that will help you assess the “total cost” of custom grinding products, which includes both what the product is and the value it provides over time. When taking everything into account, our clients often find that the custom grinding product that appeared to be too expensive actually has a return on investment that quickly pays for itself.
Here are 4 advantages to purchasing custom superabrasive grinding wheels from Continental Diamond Tool so you can weigh their value long-term:
1) Custom Grinding Wheel means a better fit.
With the right custom grinding wheel, customers have reported upwards of a 70% improvement in efficiency from conventional wheels. Our engineers work with you to reduce cycle times, maximize removal rates, minimize maintenance requirements, decrease material damage, and improve productivity wherever possible.
During the design phase, we can run simulations from our facility or travel to yours. We frequently visit customers to learn their machinery, materials, and processes so we can design a better grinding wheel that works for what they need. Some of our product options can be incorporated into lights out production which can be an even great boost to your company’s overall efficiency.
With each tool custom designed for your unique application, you get productivity out of your grinding wheel that you’ve likely never seen before. When you factor in these benefits, ROI skyrockets.
2) Custom Grinding Wheel means quality work.
Conventional wheels off the assembly line will never match the quality of custom grinding wheels from an experienced manufacturer. Custom grinding wheel manufacturers generally do not cut corners like you see with commodity products. At CDT, we use the best quality materials because it’s in our best interest to maintain longterm relationships with customers and the superiority of our products.
Experience can also be a factor with quality. Even within the industry of custom superabrasives, inexperienced engineers can cost you in development time, troubleshooting hassles, and subpar products. At CDT, we have almost 50 years of experience in old and new grinding technologies. And we’re always updating our quality control systems with state-of-the-art precision testing equipment to make sure you are getting the most efficiency from your custom grinding wheel investment.
3) Custom Grinding Wheel means the product will last.
Superabrasive grinding wheels are made from natural diamond, manmade diamond, and CBN —some of the strongest materials known to man. Conventional abrasives are made from materials like aluminum oxide and silicon carbide — much softer materials that break down more quickly. Depending on your application, a more durable product that you don’t have to replace as often may actually be a better investment.
Additionally, we have options with some of our superabrasive products where we can recommend dressing tools and even refinishing or replating services that can make your grinding wheels last even longer.
4) Custom Grinding Wheel means a great customer experience.
You may be wondering how great service actually saves you money. First, the customer service team at Continental Diamond Tool provides free quotes, product selection and design assistance. You don’t have to research and guess what you need. A specialist will provide product recommendations and a competitive quote for you for free.
Second, a company like CDT whom you have a personal relationship with will do everything they can to help. For example, we know that waiting on a grinding wheel order can be painful for your company’s productivity and bottom line. Delays may throw off your production calendar and anger customers. That is why we’ve taken measures — like stocking an extensive inventory of raw materials — so we can deliver your order faster than others in the industry. Additionally, once your product has been developed, a reorder can be produced and shipped much faster.
Third, service doesn’t stop at the sale. While some big name custom superabrasive and conventional wheel manufacturers have cut corners in service for better bottom lines, CDT has remained true to our founding principles. Does your grinding wheel supplier train your team on installation and maintenance? Will they come to your facility to review your machinery and processes to make sure your grinding wheel is optimized for peak performance? Do they notify you when new technology becomes available that could make your processes even more efficient? At CDT, our personal sales team and tech support are here to help you overcome the obstacles to increased productivity and success.
Learn more about superabrasives and how they differ from conventional grinding wheels in this video:
To get started with custom superabrasive grinding wheels from CDT, contact us for a free quote.
How CNC Automation at Continental Diamond Tool Benefits Customers and Employee
With CDT’s recent investment in CNC automation through robotics, they are seeing benefits to quality, speed, and employee satisfaction. Check out what this new technology means for CDT customers and employees >
Continental Diamond Tool has been in business since 1973, and in that time we’ve grown to rank among the world’s top manufacturers of Diamond and CBN wheels for drilling, cutting, and grinding applications. One key component of our growth has been our investment in innovation, both with our products and our processes. With our recent investment in CNC automation through robotics, we're seeing benefits to quality, speed, and employee satisfaction. Let’s look at what this new technology means for our customers and employees.
Quality Matters
Quality has been an area where Continental Diamond Tool has invested heavily in systems and automations that allow us to test and assure the accuracy of every product that leaves our facility. Robots take this a step further, producing consistent products with minimal, if any, defects. Robots are perfect for doing repetitive jobs with precision and efficiency.
In addition, automatic “error-proofing” is built into our robotic systems. Advanced software in robotics identifies when there is an issue in production and notifies our production team before it causes costly delays.
Reducing Lead Times
Before introducing robotic automation, at Continental Diamond Tool we struggled to reduce lead times on our custom products. Because each machine required highly skilled technicians to operate it, demand could easily exceed our available workforce during periods of peak production. Despite making every effort to expedite orders with on-hand raw materials and first-come-first-served policies, sometimes shipments wouldn’t reach customers until months after initial requests.
Now that all robotic machines can be remotely monitored, operators can observe production from start to finish on multiple machines. Lights-out production means even more efficient use of our facilities and quicker turnaround on orders. Now we've reduced lead times to mere weeks from design to delivery. Even with last minute orders, our robots extend our ability to put in overtime and keep up with unpredictable demand.
“With this tight labor market being what it is, CDT is always striving to become more efficient with what we have," says Jeff Gongaware, CDT Customer Service & Assistant Sales Manager. "It is not uncommon for me to walk through the shop at the end of the day and see the Robotic Arm machining blanks when all of the machinists are gone for the day. It is difficult to be to be more efficient than that.”
Better Service & Innovation
Our team at Continental Diamond Tool is always looking for ways to improve the customer experience. We strive to ensure that our customers receive nothing but quality products. When we implemented robotics into our machine shop, repetitive and maintenance tasks were delegated to robots. The resulting increases in efficiency and revenue has freed up both our human and capital resources for further investment in value-added services like research and development.
"Not only has robotic automation freed our team to make better use of their talents in the areas of service and creative innovation, but none of the robots have contracted COVID yet!" jokes Nick Viggiano, CDT President.
By integrating CNC automation into all phases of production, we have found we have been able to innovate more quickly while also ensuring the high quality of our parts. As a result, CDT is able to better serve our customers.
Better Job Satisfaction
An ongoing myth in manufacturing is that robots are replacing humans on the shop floor. While it’s true that robots are making many of our processes more efficient, CDT has found that automation actually makes life better for our workers. With mundane tasks being performed by robots, our employees can focus their energy elsewhere on bettering production efforts in more impactful ways.
According to CNC machinist Ron Fuller, “It has definitely improved efficiency and productivity in numbers, while also allowing me more time to focus on other projects at the same time. Prior to using the robotic arm, I was producing about 50-60 parts per day and now the arm allows me to produce 80 parts per day."
Repetitive, strenuous tasks tend to pose health and safety issues for CNC machinists and operators. By delegating these tasks to robots, there is less risk for workplace injury. And without this highly physical, repetitive work, we now find we have a wider pool of candidates who are willing and able to perform production work.
“In manufacturing in general, the pool of qualified or interested candidates is currently a bit shallow," says Kathy Fell, Human Resources Manager. "However, CDT is able to take what seems difficult and turn it into an opportunity with the idea of modifying job roles.”
For example, CDT has begun hiring recent retirees who want to reenter the workforce. They may no longer want to do heavy machining work, but with robots they can use their expertise in new ways, while working part-time schedules as productive as their full-time positions used to be.
Today CNC operators at CDT are focused on more enjoyable tasks such as programming and preparing multiple machines, designing new products, improving production strategies, and general monitoring of the production line. Robots are making the jobs of our CNC operators more rewarding, as they can produce more with less effort.
Working Smarter
To be successful in business, we have to be good stewards of our resources. By investing in CNC automation, Continental Diamond Tool is able to produce higher-quality products faster and with less waste. This equates to happier customers, greater employee satisfaction, and a stronger financial standing for us as a business. By working smarter through automation, we are all seeing the benefits.
Pushing the Bounds in Grinding Technology
If a customer needs it, CDT makes it happen. Check out just how we accomplish this with our custom superabrasive products in our latest blog article >
In today’s competitive advanced manufacturing space, industry leaders know that staying a step ahead means continuously pushing the bounds of what’s possible. Materials are harder, tolerances are tighter, and cycle times are shorter than ever before. In this environment, precision is essential. Well designed custom tooling can provide the edge you need to make your processes that much better.
When Ray Viggiano set up shop in 1973, his philosophy was simple:
If a customer needs it,
CDT makes it happen.
Over the years, a lot has changed, but this philosophy has stayed the same. In this video, you can see Continental Diamond Tool's state-of-the-art facility. Learn how we've grown into a leading manufacturer of superabrasive grinding wheels and diamond dressers that set new standards in the industry. Watch how we have assembled the technology, materials, and expertise to tackle the toughest jobs out there with precision and excellence. And hear about our can-do culture that has been the foundation for our company's success.
At CDT, we are committed to producing grinding wheels with the highest quality, performance, and accuracy. If you need it, CDT will make it happen. To get started, call us or request a quote.
Plated CBN for Aerospace
The mechanics of producing aircraft to safely transport people in such harsh conditions, however, is particularly challenging. The solution? Plated CBN grinding wheels.
Commercial airline travel may have taken a dramatic hit during the pandemic, but a rebound for the aerospace industry has already begun. 2021 marked the first all-civilian flight into space, and the possibilities this presents are especially exciting.
The mechanics of producing aircraft to safely transport people in such harsh conditions, however, is particularly challenging. Modern jet engines depend on superalloys to handle combustion temperatures of 1400ºC or more. These high-performance nickel-based materials have very high temperature stability, which makes machining components like turbine vanes extremely challenging. The solution is to use plated CBN wheels. Here’s why.
AEROSPACE DEMANDS
The aerospace industry asks a lot from their high-precision grinding tools. Specifically, aerospace grinding wheels must:
Remain hard at high temperatures
Be chemically inert to resist chemical reactions between grinding wheel and the nickel alloys
Provide excellent size control throughout a production run
Be available in complex forms
Not damage the workpiece – no burning or microcracking
Minimize residual stresses in the finished workpiece
Missing from this list is wheel life. While grinding wheel durability is important for Nickel based alloy grinding, it is less of a consideration for aerospace applications since their production runs are generally shorter than other industries like automotive. In this respect, plated grinding wheels provide a perfect middle ground.
Plated wheels are longer lasting than conventional abrasives, and they are capable of being refurbished through replating to extend their use. On the flip side, a plated wheel does not require the downtime for wheel dressing that a longer lasting Vitrified CBN wheel needs to maintain optimal performance. This makes plated wheels particularly well suited for applications with smaller lot sizes that don’t need an especially long life.
All of these considerations make plated CBN wheels an excellent option for aerospace applications.
ADVANTAGES OF CBN GRINDING TECHNOLOGY
As the hardest known substance, diamond might seem the obvious choice for grinding exceptionally hard materials. However, it doesn't perform so well at temperatures over 700ºC as it tends to react chemically with the material and deteriorates due to oxidation at higher temperatures. It's also vulnerable to attack by some of the chemicals found in grinding coolants, which reduces wheel life.
The alternative to diamond is Cubic Boron Nitride (CBN). This is a man-made or synthetic abrasive material that's not as hard as diamond but is harder than anything else. Unlike diamond, it retains its hardness at elevated temperatures. CBN offers superior resistance to chemical attack when grinding ferrous metal alloys. It exhibits no affinity to iron and doesn’t alter the material properties like Diamond does.
WHY PLATED WHEELS?
An electroplated grinding wheel has a single layer of superabrasive tightly bonded by a metallic layer to a solid metallic core. This has several advantages:
The bond material is below the tops of the grains, creating a free-cutting wheel that removes material rapidly with low power consumption, and helps keep interface temperatures down.
Good thermal conductivity helps take heat away from the grinding zone.
Wheel forms are readily achievable by machining needed geometries onto the metallic cores.
Worn wheels can be stripped and re-plated, making them an economical choice.
Costly dressing systems and rotary dressers aren’t needed, thus simplifying and lower capital expenditure on equipment.
THE AEROSPACE PROBLEM-SOLVER
Plated CBN grinding wheels are used extensively in aerospace. They perform well on exceptionally hard superalloys, providing high material removal rates coupled with excellent dimensional control throughout a production run.
The engineers at Continental Diamond Tool Corporation have extensive experience developing tools that can hold up to the rigorous demands of aerospace production. Contact us for a free grinding wheel analysis and quote.
Who Uses Vitrified Grinding Wheels and Why?
At CDT, our Vitrified products generally serve two distinctly different markets, Vitrified CBN and Vitrified Diamond. Learn about what makes a Vitrified wheel and the capabilities Vitrified has.
At CDT, our Vitrified products generally serve two distinctly different markets, Vitrified CBN and Vitrified Diamond. As the two hardest known materials, CBN and Diamond are referred to as superabrasives and both are excellent thermal conductors.
These abrasive properties when combined with our porous vitrified structures allow for:
longer wheel life
shorter grinding cycle times
automated grinding production capabilities with wheels dressed right on the grinder
CBN vs. Diamond
Vitrified CBN products are ideal for steel and ferrous alloy grinding applications in automotive, aerospace, medical, production tooling, etc. They are excellent thermal conductors and do not react with ferrous materials during the grinding process like diamond does.
We regularly customize Vitrified Diamond products for grinding ceramic and carbide materials used in industries such as glass, ceramics, computer chip manufacturing, thermal spray coatings, and more. Diamond is the hardest known material with the best thermal conductivity making it the best abrasive where there is no chemical reaction.
We are uniquely qualified in both types of Vitrified products because of our full range of manufacturing capabilities and technical application support. Because we handle the vitrification process entirely onsite, we have full control of the manufacturing process and a standard lead time of about 3-4 weeks — about half as long as the industry standard.
The Vitrification Process
At CDT, we use a cold press and sintered process to press near net shape with highly and tightly controlled sintering. This fuses the Vitrified/Ceramic bond together with the Diamond or CBN into a porous structure. CDT's vitrification process is unique in how our engineers have developed a series of custom bonds, formulations, and structures to offer our customers superior grinding performance when compared with off-the-shelf or other competing products.
Combining either of these two abrasives with a porous vitrified bond offers a very strong and stiff system in which the porosity brings coolant into the grinding zone. This innovation removes heat and grinding debris (or "swarf") to extend the wheel life and improve performance. CDT's Vitrified Diamond and CBN wheels generally provide 100 to 300 times the grinding wheel life and maximize the amount of material being ground compared with conventional grinding wheels.
Reducing Cycle Times
"Cycle Time" is the term used to describe the grinding process. Our porous vitrified grinding wheels offer greater efficiency through more effective coolant delivery and swarf removal. This also extends the life of the grinding wheel requiring less downtime for wheel dressing.
When compared with conventional wheels, we see an 80-90% cycle time reduction with our custom vitrified wheels. Even compared with other superabrasives such as Resin and Metal Bond Diamond and CBN wheels, we see 40-75% reductions in cycle times with vitrified wheels.
From military/defense and energy sectors to mold & die markets and everything in between, we have found unique opportunities for more efficient grinding using custom Vitrified products in many industries. Our engineers would be happy to discuss the parameters for your process and provide a free analysis and quote for a custom grinding solution that works best for your application. Contact us today >
Not Your Standard Plating!
Continental Diamond Tool now offers a new generation plated product available on carbide, aluminum, copper, or steel substrate bodies.
Now available in Carbide, Aluminum, Copper, and Brass
Plating has traditionally been a single layer of abrasive with either CBN or diamond attached to a steel body. CDT now has a new generation of plated products available on carbide, aluminum, copper, or steel substrate bodies.
Carbide is a great option for mandrels and similar processes where extra rigidity is needed. Carbide provides superior hardness, unsurpassed corrosion resistance, and the ability to retain its strength at extreme temperatures.
Aluminum is light weight and easier to handle than steel, making it better for processes that require labor intensive lifting. There is less strain on your operator when working with this tool. The reduced weight also exerts less stress and wear on your machine, prolonging the life of spindles and spindle bearings. This material is also resistant to rust and corrosion and has a high strength-to-weight ratio.
Copper also offers great corrosion resistance, and it is also malleable. Its inherent flexibility allows it to maintain adhesion even if a substrate is bent and manipulated post plate. This feature makes it ideal for processes that need extra pliability.
Brass is a solution we also turn to for its malleability. It is also a good choice for dressers, because it will not cause sparking. Many grinding machines run oil-based coolant, and sparks can cause the oil to ignite. Brass is superior for these especially flammable conditions.
Steel substrate is still a highly durable option for aggressive grinding applications. The strength of the steel is long lasting and prevents damage to the core.
Each material has its advantages. When you talk to a CDT grinding specialist, they will gather information about your manufacturing goals and recommend the substrate that has the right features for your application. Stop trying to succeed with the same grinding tools your competitors are using and instead gain an advantage with grinding solutions that are specially design with your process in mind for optimal performance.
If you would like to see if your plated grinding wheels would work better with a different substrate — or to find out about innovations in vitrified, resin bond, or metal bond grinding wheels that may benefit you — contact us for a free quote: 800-443-6629.
Take a Tour of CDT’s Plating Department
Why Switch To A Vitrified Superabrasive Grinding Wheel?
What is a Vitrified Superabrasive Grinding Wheel and what are the benefits of using one? In this blog, you’ll learn who should switch to Vitrified >
How a grinding wheel performs is dictated as much by the bond as the abrasive. Superabrasives, which can be either diamond or cubic boron nitride (CBN) have four types of bond: metal, plated, resin and vitrified. Of these, vitrified may be the least well-known, yet it’s attracting attention, thanks to the improved performance and lower costs that it offers.
WHAT IS A VITRIFIED WHEEL?
In a vitrified wheel superabrasive grit is mixed with a type of glass or ceramic and then pressed before firing in a kiln. This creates a porous, glass-like structure that holds the grit in a rigid matrix.
Unlike a plated wheel where the abrasive is just a single layer, a vitrified wheel can have considerable depth. This means the wheel can wear and go through repeated dressing. Wear rates are very low as the vitrified bonds must fracture to release worn grit and expose fresh edges. It’s also possible to put a form into the wheel to allow grinding of complex profiles, (although this does complicate dressing.)
BENEFITS OF VITRIFIED DIAMOND AND CBN WHEELS
The open, porous structure ensures the grit stands proud of the bond surface, creating a wheel that’s described as ‘free cutting.’ This means good space for chip clearance, which:
increases material removal rate
lessens dressing frequency
reduces wear
carries coolant through the grinding zone
lowers grinding forces, thus creating less heat and less work piece damage
As an additional benefit, these last five points result in lower temperatures at the interface and reduced risk of workpiece burning in metals and less microcracking in ceramic and hard materials.
Lower temperatures help maintain control over final size, as does the very rigid nature of the wheel. With minimal wheel deflection due to grinding forces and low thermal growth very high tolerances can be maintained throughout a production run.
APPLICATIONS
High volume production are ideal applications for vitrified grinding wheels. Low wear rates, combined with a free-cutting nature and ‘dressability’ mean very high material removal rates and less downtime for wheel changes.
Vitrified cubic boron nitride grinding wheels are preferred for grinding hard ferrous workpieces like crankshafts and camshafts as well as tool steels. Vitrified diamond grinding wheels are good in non-ferrous applications such as shaping ceramics and carbides.
THE HIGH-VOLUME WHEEL
Of the four main bond types, the vitrified wheel is best suited for high volume, extended production run applications. The rigid, porous structure delivers high material removal rates and extended life, helping lower manufacturing costs.
Call the engineers at CDT at 800-443-6629 to talk over your specific application and determine if a custom vitrified grinding wheel would benefit your manufacturing process.
The Evolution of Vitrified Grinding Wheels (Part 3)
In part 3 of this 3-part blog series, we explore the advantages and limitations of the Vitrified Grinding Wheel in various grinding applications.
Vitrified Superabrasive wheels use either diamond or CBN in a glassy or ceramic bond. Conventional grinding wheels use either Aluminum Oxide or Silicon Carbide, as with all grinding wheels, the bond imparts certain characteristics, making it better suited to some applications than others.
ADVANTAGES
High strength structures with porosity for clearing chips and bringing coolant to grinding zone allow for reduced grinding cycle times.
Porosity for coolant and chip removal efficiently remove heat and reduce work piece thermal damage and stresses.
Efficient chip removal reduces wheel dressing frequency thus prolonging wheel life thus lowering machine down time for wheel changes and lowering waste removal costs.
High wheel stiffness, long wheel life, and minimal heat generation allow for excellent finish and dimensional tolerancing.
Wheel specifications can be optimized for each specific application (machine, coolant, work piece, stock removal, dressing, etc…)
High product uniformity and performance allows for continuous unmanned grinding operations.
Automated dressing and wheel conditioning.
LIMITATIONS
Wheel manufacturing process controls need to be tight to ensure repeatability and product consistency (most sensitive of bond systems to process variations).
Wheel designs need to be matched to the application (i.e. solid Vitrified wheels are limited to 80m/s operation, Vit wheels with steel cores can be rated for use up to 170m/s operation).
Wheel prices may seem high when compared with conventional or other Superabrasive grinding wheel prices (need to look at all costs, not just wheel price).
Significant capital investment in terms of equipment to maximize cost benefits of higher concentration CBN and Diamond Vit wheels for high volume applications.
Generally requires knowledge of complete grinding process to maximize grinding performance. Grinding application support is necessary in many applications
Difficult to cross reference competing manufacturers wheel specifications
APPROPRIATE APPLICATIONS
Vitrified CBN grinding wheels are ideal for high volume applications where productivity is paramount such as Automotive applications like Cam & Crank shaft grinding, and Aerospace engine component grinding. Recent advances in bonds and wheel specifications has led to the development of wheel structures for use on older less suitable grinding equipment and applications like surface and cylindrical grinding in mold and die shops.
Vitrified diamond grinding wheels are most suited for grinding of very hard Ceramic and Carbide materials. Applications include grinding of PCD and PCBN cutting toolings, structural ceramic components, and Carbides.
CURRENT RESEARCH
Improved bond and wheel strength through continuing work with “Ceramic” bonds.
Abrasive grit customization for better chemical and mechanical bonding in existing and new “Ceramic” bonds.
Improved understanding and modeling of the grinding process.
STILL EVOLVING
Vitrified Diamond and CBN wheels compositions continue to evolve through the use of new chemistries and processing variables to enhance grinding wheel structures and performance. When it comes to grinding hard to grind materials, there are no better abrasives than Superabrasives; Diamond and CBN. Vitrified structures combined with Superabrasives often times allows for the best compromise between wheel life and grinding performance, thus giving the lowest overall costs in grinding.
The Evolution of Vitrified Grinding Wheels (Part 2)
We reviewed the materials of the Vitrified Grinding Wheel development in part 1 of this blog series, now we will discuss the bond. Learn more >
Any review of vitrified grinding wheel development should cover both the abrasive materials and the bond medium. Part 1 of this series addressed materials; here we turn to the bond.
THE BOND MEDIUM
Grinding wheels probably originated in ancient Egypt where they were likely cut from sandstone. They also appear in sketches by Leonardo da Vinci and it's thought Belgian gem-polishers were using a cast iron wheel impregnated with diamond powder during the late 1700's, but little else is known until the early nineteenth century.
Around this time the first solid-bonded abrasive wheels appeared. These were made in India for hand-grinding gems and used emery or corundum abrasive in a gum resin shellac binder.
Rubber bond grinding wheels were introduced around 1860, again using corundum.
The first Vitrified (glass) bond wheels were commercialized about ten years later. What are today known as Resin (plastic) bonded wheels didn't appear until 1923. Metal bonds for diamond grinding wheels weren't introduced until the early 1940's.
CREATING A VITRIFIED BOND GRINDING WHEEL
The term “Vitrified" in its simplest form means “glassy” or “glass bond." Abrasive Materials such as Aluminum Oxide, Silicon Carbide, Diamond, and CBN are mixed with glass frit (ground glass) and other ceramic materials (clays, feldspars, fluxes, etc…). More recent advances in “Vitrified” bonds has led to the development of “Ceramic” bonds. In general terms, Ceramic bonds are those in which some or all of the glass phase has been converted to a crystalline phase to enhance certain material properties (i.e. higher strengths). Blended grinding wheel compositions are then formed either by “Hot Pressing” or “Cold Pressing” processes.
In Hot Pressing, the blended wheel materials are placed into a suitable mold and simultaneously pressed and sintered (baked). In sintering, the glass & ceramic components are fused and melted together forming the hard Vitrified Bond that holds the abrasive materials in place. Because the grinding wheel is simultaneously pressed and sintered at high temperatures, mold material selection has to withstand the processing temperature. Hot Pressed Vitrified wheels usually have low porosity levels and are very different in their use applications when compared with Cold Pressed Vitrified grinding wheels.
In Cold Pressed Vitrified Products, an extra material called a binder is blended into the wheel composition. The purpose of the binder is to provide handling strength to grinding wheels that are pressed in molds at room or low temperature and then removed for subsequent and separate sintering in kilns (high temperature ovens). In the sintering process, the temporary binder is removed at a low temperature and the glass is fused together at a high temperature forming the rigid hard Vitrified bond. Cold Pressed Vitrified grinding wheels generally have high levels of porosity in their structures.
Grinding wheel properties are adjusted by varying the percentage of abrasives, size of abrasives, blends of abrasives, different bonds and bond types, manufacturing process, etc… Varying the amount of the abrasive in Superabrasive Grinding wheels is referred to as the “Concentration”. Higher Concentrations contain more material and in general provide longer grinding wheel life as there are more Diamond or CBN cutting points to remove material.
CREATING POROSITY IN VITRIFIED GRINDING WHEELS
Porosity carries coolant through the grinding zone and provides space for chip clearance. By providing space to remove grinding swarf (used grinding wheel and removed work piece material), the grinding wheels are able to grind faster, provide better surface finishes (especially if the grinding fluid is filtered to remove the debris). Because open spacing in a wheel structure brings liquid coolants to the grinding zone, they are also known to grind cooler. In so doing, Vitrified Grinding wheels can remove the heat generated during grinding much more efficiently thus allowing faster grinding cycle times and less thermal damage to sensitive materials like Steels and Aerospace Alloys.
Porosity in wheels structures can be created by a variety of methods. In cold press and sinter manufacturing, the wheels are pressed to limited densities and sintering is controlled to limit shrinkage and densification. Another method for creating porosity in grinding wheel structure is through the use of additives in the wheel compositions that are then removed in the sintering stage, thus leaving voids (porosity) where the material once resided. Additional porosity can be generated by adding constituents to wheel compositions that remain within the wheel through manufacturing but are initiated when used. For example, some wheel compositions include material that doesn’t melt in processing but is dissolved in coolant upon use (i.e. Salt). Another example of induced porosity would be the use of hollow microspheres which upon use are broken open, leaving the open void as a pore.
Stay tuned for part 3 of this series where we will explore the advantages and limitations of vitrified diamond and cbn wheels in various grinding applications.
The Evolution of Vitrified Grinding Wheels (Part 1)
The vitrified bond grinding wheel first appeared 150 years ago, and continues to become ever more valuable. Learn more about the evolution >
The vitrified bond grinding wheel first appeared 150 years ago, and continues to become ever more valuable. While some products reach a kind of developmental plateau where there's no potential for further improvement, research continues to uncover ways of making vitrified wheels cut faster and last longer.
When it comes to shaping hard materials quickly, accurately, and cheaply the vitrified superabrasive grinding wheel has few rivals. Low wear, high heat stability, combined with a free-cutting nature and excellent ‘dressability’ mean very high material removal rates and less downtime.
Understanding how this tool evolved yields some fascinating insights into its use in manufacturing. This begins with an overview of grinding wheels and abrasive materials, covers the production process, and explores where the technology might be heading.
HISTORY OF GRINDING WHEELS
Any review of grinding wheel development needs to cover the two primary components: the abrasive materials and the bond medium.
ABRASIVE MATERIALS
It is thought that sandstone was the first abrasive material. Probably used for putting a sharp edge on axes, compacted quartz embedded in the rock grains proved an effective way of removing material, (much like sandpaper today.) However, as a natural material sandstone has the disadvantage that the quartz particles vary in size and shape, resulting in unpredictable performance.
An alternative material, emery, was known to the Greeks and Romans as an abrasive and is still mined on what is today the Greek island of Naxos. Emery is a form of corundum, the second hardest naturally occurring material, is the crystalline form of Aluminum Oxide containing traces of Iron, Titanium, and Chromium.
As an abrasive emery had two problems: it was expensive to extract and ship to the manufacturing centers in the UK and USA, and its performance was unpredictable due to variance in raw materials that are mined. Spotting an opportunity, entrepreneurs set about developing alternatives. The results included synthetic or manmade Silicon Carbide and synthetic Aluminum Oxide (Corundum). These materials are generally known as “Conventional Abrasives."
INTRODUCING SUPERABRASIVES
Natural Diamond, has been used for grinding since at least the seventeenth century when Belgian gem-polishers used Diamond powder embedded in cast iron. Cost and variability of natural Diamond held back wider use until the creation of synthetic Diamond changed the equation in the 1950s.
As the hardest known substance, Diamond makes an excellent abrasive in most instances. There are certain Ferrous, Cast Iron, and Aerospace alloy materials, however, that produce a chemical reaction with Diamond causing it to wear rapidly and to alter the properties of the material. To address this problem, in 1969 General Electric introduced a crystalline material they had developed with a hardness approaching that of Diamond: Cubic Boron Nitride (CBN).
Despite having a lower hardness than Diamond, CBN doesn’t react with Ferrous and Aerospace alloys when grinding and has an even higher temperature stability. Therefore, it offers better grinding performance when grinding these particularly tricky materials.
Diamond and CBN are generally known as “superabrasives" for their unique, highly effective, grinding capabilities.
In part 2 & part 3 of this series, we will look specifically at the vitrified bond medium and its advantages and limitations in various grinding applications.