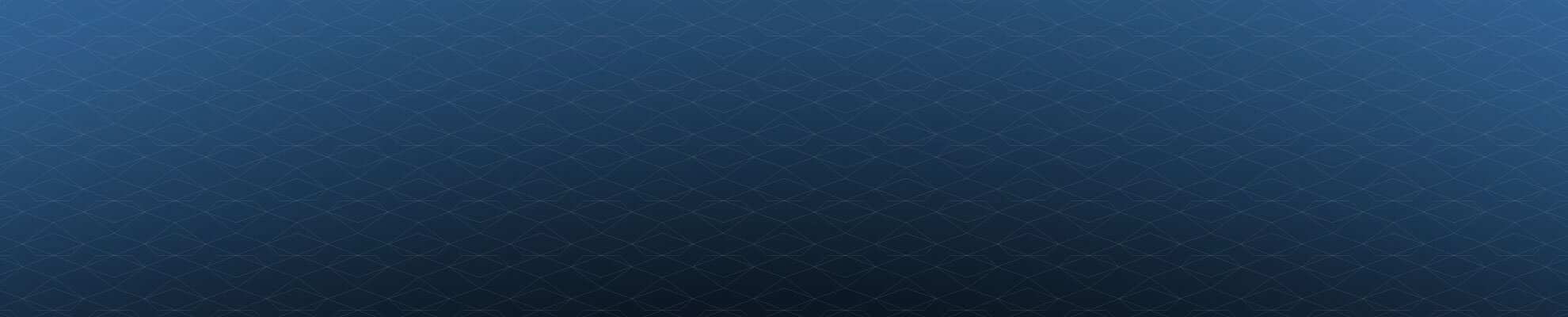
News and Resources
Browse by Category
Browse by Product
- All Dressing Products
- All Grinding Products
- CBN-Diamond Superabrasives
- Conventional Abrasives
- Diamond Lapping Compounds
- Diamond Rotary Dressers
- Diamond Stationary Dressers
- Hybrid Bond Grinding Tools
- Metal Bond Grinding Tools
- Plated Grinding Tools
- Resin Bond Grinding Tools
- Vitrified Bond Grinding Tools
CDT Now Offering Same Day Shipping on Select High Performance Grinding Wheels for the Cutting Tool Industry
If you are in the cutting tool industry and are interested in gaining a competitive edge with CDT's GL™ Series grinding wheels, contact our knowledgeable team of service techs today.
Last year Continental Diamond Tool Corporation introduced its Resin Hybrid Bond — custom formulated grinding wheels with a winning combination of durability, finish, and performance.
The Resin Hybrid Series is the superior option of superabrasive diamond and CBN grinding wheels for the cutting tool industry. Using the latest Advanced Bond technology, competitive trials have proven that the bond grinds up to four times quicker without losing the wheel edge. Flute from solid, regrind, gash and end work, and relief.
Resin Hybrid Bond is not your standard “one size fits all.” This bond is tailored to specific grinding applications, providing the highest quality tool with the most efficient performance. Its unique properties offer key advantages to the CNC Tool and Cutter Grinder in many ways:
Free cutting action with superior form retention and surface finish
Self sharpening bond lengthens wheel life and dressing interval
High material removal rate with high temperature stability
Maximum heat dissipation with low and constant power consumption
Optimal wheel profile stability lowers costs due to wear
Previously cutting tool manufacturers had to commission custom-designed Resin Hybrid wheels to get all these benefits. Now CDT is stocking our most popular shapes and sizes specifically tailored to cutting tool manufacturing at affordable, off-the-shelf prices. CDT wheels are compatible with most of the cutting tool industry's leading CNC Tool and Cutter Grinder machinery.
If you are in the cutting tool industry and are interested in gaining a competitive edge with CDT's Resin Hybrid Series grinding wheels, contact our knowledgeable team of service techs today. Tell us your requirements and we will check our inventory for availability or provide you a custom quote. Wheels in stock ship the same day!
Or call 800-443-6629.
Care and Maintenance of Diamond Wheels
A few simple steps to care for and maintain your diamond wheels will allow you to get the performance and durability you expect from them.
Diamond wheels provide the maximum performance and high-speed cutting on demanding materials. Proper care and maintenance will ensure that the wheel gives the superior results for the maximum time. The steps are not difficult and well worth the effort.
Installation
Make sure that spindles, back plates and flanges are always clean before installing a new wheel. Use a dial indicator to check that the rotation of the wheel is within 0.0005 inch, 12.7 microns, of true. Tighten the flanges once the wheel is true and double-check tightness before use.
Diamond cutting wheels should only be used to make straight cuts. Twisting or jamming the wheel can cause fatigue and segment loss. Excess pressure should not be applied when making cuts.
When performing any cutting or grinding process, all work materials require firm support. Excess overhang should be avoided; even slight tilting can create an angled cut.
Feed and grinding speed
Material must be fed into the wheel at the appropriate speed. A feed rate that is too fast will cause chatter and vibration. This will result in a poor cut and possibly damage the cutting edge of the wheel.
Diamond wheels work best at speeds between 5,000 to 6,000 surface feet per minute. Running at lower speeds can lead to glazing.
Dressing
Using the wrong cutting wheel, one with a bond that is too hard for the working material, will create glazing. The easiest way to avoid this is using a blade that is matched to the material. Dressing the blade is a maintenance technique, but dressing does slow down production and reduce the life of the wheel.
Dressing a diamond wheel cleans the build up of debris from cutting operations that block the abrasive surface. The resurfacing restores the sharp abrasive edges of the diamond coating. A dressing stick, normally aluminum oxide or silicone carbide, is used to cut through or remove the debris and expose new diamond material.
Make an arrow mark on the wheel showing the rotation direction the first time and always dress the wheel with it spinning in the same direction. Dressing a wheel in both directions will destroy it.
Dressing is accomplished by simply making a straight cut through the dressing stick or bar. Cut off a thin section per pass. Only one or two cuts through the stick should be required.
If a dressing stick is not available, a section of asphalt can be used. Make a few cuts into the asphalt and the blade should be clean.
Overheating
Coolant should be used for maximum results. The coolant needs to spray to contact where the cutting wheel and material meet. A weak soluble oil solution may be used to reduce corrosion.
If dark streaks form along the sides of the cutting edge, the wheel is being overheated. Excess heat can cause the wheel to break apart. If dry cutting is being performed, allow the wheel to cool for about 10 seconds for every 30 seconds of cutting operation.
Use the right grade wheel, designed for the material to prevent injuries from reactive force or throw back. Never use a wheel that shows signs of fracture, fatigue or broken segments.
Industrial Diamond Facts
Find out about industrial diamond shapes, quality and sizes as well how they are used in industrial settings.
Diamonds are used for many industrial settings due to the fact that they are the hardest substance known. Diamonds are a crystalline form of carbon, capable of assuming a variety of shapes, sizes and qualities and are used for grinding, cutting, drilling, polishing and as an abrasive in industrial applications. Although diamonds have a high cost initially, they often cut down on the total labor cost of industrial projects due their efficiency for cutting and grinding.
SIZE AND QUALITY
Diamonds used for industrial purposes vary widely in cost which is based on two factors--size (determined by carat weight) and quality. One carat is equal to 200 milligrams of 1/5 of a gram. Each gram represents five carats. A carat is further defined as having 100 points (the smallest unit of measure in the carat system). Therefore .10 equals 1/10 of a carat, 1.5 equals 1 1/2 carats.
Diamond quality is difficult to assess, determined by highly technical factors representing the considered judgment of a trained diamond expert. For industrial purposes, the best way to judge diamond quality is by performance. The better quality a diamond is, the more structurally sound each individual crystal will be. High-quality diamonds have better shape definition, allowing for longer service and quality dressing action desired on the grinding wheel.
SHAPES
Industrial diamonds can be shaped in a variety of ways as shown below:
A Concise Guide to Single Point Diamond Dressers
Learn about diamond classifications and 10 tips for using single point diamond dressers.
Problematic grinding performance typically arises as a consequence of improper dressing. Choosing the correct diamond quality classifications greatly improves the expected quality of finished products. Moreover, the number of settable points will contribute heavily to acceptable dressing standards.
Classifications of Diamond Qualities
Grade A quality diamonds provide four+ settable points--smooth-surfaced octahedron or dodecahedron.
Grade B quality diamonds provides three+ settable points--possibility of inclusions, although they do not disturb the diamond's integrity.
Grade C quality--two+ settable points exhibiting blockish structure with superficial irregularities. This grade is the most common grade used in tool rooms.
Grade D quality--less than two settable points. Grade D's may have defects around less defined points.
Grade E quality--one settable point, "utility" grade diamond typically presenting cracks and other flaws.
Grade U quality--one settable point, "utility" grade cube-shaped diamond with an opaque surface
10 Tips For Using Single Point Diamond Dressers
1. Extend the life of a single point diamond dresser by inclining the tool at a 10 to 15 degree angle to the wheel radius. Point the tool in the rotation direction of the grinding wheel to maintain a consistently sharp point.
2. When dressing with Polycrystalline (PCD), grit, diamond single points or arbitrary stone tools, the infeed has to be .001 since a diamond dressing tool inevitably pulverizes the vitrified bond. Anything higher than .001 will cause cracking into the wheel--as much as .009 deep--that forces the bond to degenerate. In addition, gullets develop that produce loading by catching chips and overheating the wheel. Consequences of excessive infeed are chatter, bounce, bad finish and burn.
3. Sharply-tipped, crystal octahedrons should be utilized for straight dressings. For 46 grit and 60 grit wheels, crystal octahedrons shaped in a gothic style work well. Points associated with crystal octahedrons stay sharp if you turn the tool six to 12 indexes every revolution, or as necessary.
4. Make sure to use enough coolant to moderate dressing temperature, otherwise overheating occurs which may chemically transforms diamond into graphite. Diamonds will also suffer cracking if subjected to large temperature gradients.
5. The objective of dressing is to generate and expose novel, superficial cutting edges on the wheel. Single point diamond dressers achieve this objective by shattering existing gravelly grains and facilitating the emergence of desired abrasive particles. Dressing increases in-feed as well as feed and must be performed regularly to maintain optimal grain protrusion and grain edge sharpness.
6. Always begin dressing at the center of the wheel, which is the biggest diameter. Starting a dressing procedure at a wheel's side will probably result in shattering or even destroying the highest quality diamonds.
7. To prevent wheel taper, place the single point diamond dress as close as possible to the grinding area.
8. Grinding wheel grain sizes are contingent on longitudinal feeds, which significantly influences the structure of the surface of a grinding wheel. Additionally, reduced feed rates will predictably provide finer, more desirable surfaces.
9. Rotate the dresser 20 to 40 degrees in the shank if a flat appears on the diamond so that the dresser maintains an optimally conical point.
10. Avoid letting the diamond erode until the shank is visible. Doing so could allow the stone to dislodge or fall out.
The Plating Process - The How and the Why
Plating is a rather complex process, but the coating it provides to grinding wheels and other tools can add unbeatable strength and durability.
Diamond tools come in many different styles. One of the more commonly used types of diamond tools are those that have been electroplated. Understanding what exactly electroplating is, how the electroplating process works and what these tools are used for is important - especially if you plan to use any type of diamond tools in your machining process. That way, you can determine if these are the right solution for your machining needs.
What is Electroplating?
Electroplating is the process where a metal object is coated with a thin layer of another metal using electrolysis. For most applications these metal coatings are thin, less than .002 inch thick. With diamond tools, a strong layer of metal tool is electroplated to bond a single layer of diamond to the tool. This adds strength to the tool and additionally, it makes a tool that can grind even the hardest materials.
How Does the Electroplating Process Work?
A solution is created using a “salt” of metal coating plus water. This is referred to as an electrolytic bath. The object or tool that will be plated is placed in the electrolytic bath. Then, a metal bar is added to the bath. It may be the metal used for plating or another material that isn’t affected (insoluble electrode). After this, the object is connected to a source of direct current and the bar is connected as well. Once power is applied, the electrolysis process occurs creating a plating. Multiple layers can be applied to achieve the desired levels of plate.
What Are Electroplated Tools Used For?
The electroplated tools are stronger than even standard tools or composite tools. With the right plating, an old, worn tool or wheel can be sharper and stronger than ever. These are used in machining mainly for grinding or cutting processes. These tools are used in the manufacturing of components for the auto industry, medicine, aerospace, computers and factory work. The strength, affordability and usability of electroplated tools make them highly desirable within all levels of the manufacturing process.
Now that you understand more about electroplating and diamond tools, it may be time to determine the best options for your business. CDT (Continental Diamond Tool) sells new electroplated diamond tools, or we can work with you to electroplate your current tools to help you accomplish more than you ever thought possible. Call or contact us to learn more about our services and solutions we would love to work with you!
Machining and Composite Materials - The Basics
It's important to understand what makes composites different from traditional materials and the process involved with machining these compounds.
Composite materials, which are sometimes called composition materials, are created by combining two or more materials that have a significantly different make up of chemical or physical properties. When these materials are produced, the material produced often has characteristics that are different from the component materials that create it. Composites are very popular today in the manufacture of a number of different products, and they will likely only become more useful in the future.
Manufacturers choose composites for a number of reasons. Generally, the purpose is to gain the benefits of two different materials for example a lightweight material and a strong material. Composites are used within a number of different industries. From tools to golf clubs to ceramics, composites are an excellent choice for creating top-quality products.
The one problem with composite materials is that the means of working with traditional materials often do not work with composites. Machining composite materials is a challenge that requires a powerful solution. Continental Diamond Tools (CDT) Diamond tools do just that.
There are a number of diamond tool manufacturers out there, but many do not produce a tool that is adequate for the needs of working with some of the more complex composite materials. CDT understands the complexity and problems you may face when you are working with machining composite materials. We stepped up our production to meet the challenge and developed diamond products and technology that is specifically designed for this purpose.
CDT’s plated process is perfectly suited for composites. Our diamond tools provide outstanding cutting speed and efficiency for even the trickiest composite. Additionally, our engineering team specializes in helping our customer create a successful and cost effective solution for manufacturing needs. Whether working with metallic or non-metallic composites, the CDT diamond tools will provide the best possible results each and every time.
No matter what type of composite you work with, from FRP to fiberglass to Kevlar® aramid fiber, our products are the perfect solution. CDT’s electroplated wheels are useful for all areas of composites, including: automotive, boating, aerospace, sporting equipment (golf clubs, archery equipment, bicycles and scooters, etc), wind energy, and military applications.
Instead of worrying that your current machine process won’t get the job done or will fail when you need it most, switch to a process that is proven to achieve results. Call or contact us at CDT to discuss the composites you process and your current machine set-up. We can help you find the perfect diamond tools that can grind and shape your composites just as required.
Why Cubic Boron Nitride Is Better Than Diamond for Grinding
Diamond grinding tools have always been an industrial mainstay but Cubic Boron Nitride (CBN) may be a better solution in many applications.
Diamond grinding tools have always been an industrial mainstay but Cubic Boron Nitride (CBN) may be a better solution in many applications. CBN grinding wheels provide the same benefits as diamond tools and even perform better in some applications.
The desirable characteristics of any abrasive include:
Hardness
Strength
Abrasion resistance
Thermal and chemical resistance
Ability to maintain sharp cutting edges during use
Hardness is perhaps the most critical property of every abrasive. Abrasives tend to lose hardness during application as a response to very high temperatures. One of the greatest advantages to using CBN is that it maintains its hardness at room temperature and over a wide variety of temperature ranges.
About CBN
CBN is the second hardest material after synthetic diamond. The process of making CBN abrasive is similar to that of synthetic diamonds: scientists treat hexagonal boron nitride at high temperature and pressure to create cubic boron nitride and treat graphite in the same way to create diamond.
About CBN
CBN is the second hardest material after synthetic diamond. The process of making CBN abrasive is similar to that of synthetic diamonds: scientists treat hexagonal boron nitride at high temperature and pressure to create cubic boron nitride and treat graphite in the same way to create diamond.
Machinists make CBN grinding wheels by plating CBN particles on steel, using plated nickel to hold grit in place. A single layer of CBN grit applied to the surface of a metal disc can grind even the hardest surfaces and last for years.
CBN has several attractive characteristics that make it superior to diamond:
Withstands heat, especially during high-speed applications
Does not cause grit that can dull bits
Stays sharp and cool because it does not react with steel
Diamonds can also react with transition metals, limiting their usefulness for grinding certain materials. Cubic boron nitride is stable and does not tend to react unfavorably with standard transition metals.
But What About Diamonds?
Diamond super-abrasive grinding wheels do have their advantages in some applications, especially in grinding abrasive or hard materials such as aluminum oxide, ferrites, ceramics, tungsten carbide, gray and ductile iron, and carbon. These grinding wheels also have the ability to cut freely with a cool cutting action, which is handy in applications where coolants could damage materials. Diamonds will likely remain a popular choice in many grinding applications in the future but nanotechnology may propel CBN into the top position.
Nanotechnology and CBN
In January 2013 issue of Nature, a scientist from University of Chicago’s Center for Advanced Radiation Sources and his colleagues reported they had been able to make ultrahard CBN by drastically shrinking grain size. The researchers were also able to rearrange the crystals into a zigzag formation of boron and nitrogen rather than in conventional flat layers to give it super resilience.
“Now, we can make this material as hard as single crystal diamond,” says the lead scientist, Yanbin Wang. “In some ways, it’s a better tool than diamonds, especially given its high fracture toughness.”
What to Look For When Choosing A Diamond Wheel Supplier
Look for these qualities when choosing a diamond wheel supplier.
The suppliers your company chooses can affect your business in many ways. Qualities like expert support, competitive pricing and speedy turnarounds can make significant differences in your success. Continental Diamond Tool is a world leader in the field of superabrasives for industries that include medical tool manufacturing, construction and aerospace engineering. Our small company philosophies and big company capabilities mean that you are in the hands of ethical, hardworking and capable support. Among the qualities that set us apart from the rest:
Speedy Delivery
Every day your supplies take to get to you is one that can hold up your operation. And, when you deal with another grinding tool supplier, you can wait as long as two months for your custom equipment, leading to slowdowns and delays.
We maintain an extensive inventory of raw materials so that we can complete your order fast in our in-house manufacturing facility. These allow us to supply an unlimited number of superabrasive products that fit your needs, timeline and budget. Our average shipping time is between 15 and 18 working days. We are proud of ability to create tools to order at a speed that gets you back to work as quickly as possible, saving you from expensive downtime.
Helpful Technical Support
Our commitment to you doesn't end when our product leaves the door. We have highly trained and knowledgeable staff that can help you with every phase of production, from prototypes to replacements, to improvements and enhancements. We can help you determine which tools are best for the job, how to implement strategies to make your company's work more efficient. Reach out to us for the assistance that will help you overcome obstacles and clear your way to success.
Global Outreach
Throughout the world, we offer support and custom tools to get the job done. Through innovation and commitment to customers, CDT has become the global leader in superabrasives in a wide range of industries. Our small company values, dedicated technical support and outstanding lead times mean that you can be sure that you can get the tools you need wherever you need them.
Competitive Pricing
CDT produces custom diamond wheels at competitive prices. We help people in all industries keep their costs under control to improve their bottom line and make their businesses more profitable. Our sales and manufacturing team work together to ensure that you are getting quality tools at an affordable price.
Since 1973, CDT has been committed to supplying a wide range of industries with the highest quality custom diamond tools. Contact us today to learn how we can serve your needs.
Grinding Wheels in the Electronics Industry
Grinding wheels and grinding tools of all types play a huge role in the electronic industry - even in ways that many people might not realize.
Grinding wheels and grinding tools of all types play a huge role in the electronic industry - even in ways that many people might not realize. Metal bond grinding tools are used to create a large number of the types of products that we use and love on a daily basis. By taking a look at the types of electronics devices that these important tools help create, you can start to see just how integral of a role they play in life as we know it.
Grinding tools like diamond drills, scoring disks and superabrasive endmills are used during the creation of printed circuit boards, which are a key component to many electronic devices that we find in our homes. If you own a desktop computer, laptop computer, high definition television set or home theater system of any type, you have the advancements enabled by circuit boards to thank for the hours and hours of enjoyment that you have received from these types of devices.
The types of circuit boards that are commonly made using grinding wheels and other grinding tools in the electronics industry are called printed circuit boards. These specific types of deices support various electronic components using tracks and pads that are conductive, allowing electricity to flow from one part of the device to another. The types of printed circuit boards that can be made using grinding wheels of all types include multi-layer boards. Single sided boards, which is a printed circuit board with only one copper layer, and double sided boards, which are a type with two layers of copper, are also commonly made using grinding tools like diamond drills for maximum precision. These types of printed circuit boards are traditionally found in almost every consumer electronic product that you can purchase, except those that are so simplistic in nature that they don't need a circuit board at all.
Part of the reason why diamond drills and metal bond grinding tools are so important to the electronic industry is because of the types of materials that they are capable of processing. Diamond tools in particular are capable of processing carbide alloys, stone, ceramics, semiconductor materials, aluminum, copper, copper alloys, rubber and resin. These types of materials are all used throughout the electronics industry in varying degrees. Copper and copper alloys in particular are hugely useful to electronic devices because they are both incredibly conductive with regards to electricity and resistant to erosion. As a result, they are ideal for situations like copper wiring, like the type that is used to transmit high speed signals into a person's home from a cable television provider.
Grinding Wheels In The Medical Industry
Discover the ways that diamond grinding tools are used in the medical industry: it may surprise you!
The medical industry relies on both brand new technology and old world skills and knowledge to help keep people healthy and heal injuries. One of the devices used in medicine that truly bridges the gap between old and new is the plated diamond wheel and other diamond tools. This device can be used in a number of procedures as part of a treatment plan that includes both new and old techniques. Learn a bit more about the use of these tools in medicine and you are sure to appreciate their flexibility.
Creation of Orthotics
Today’s orthotics and implants are more advanced than ever before. Creating these custom pieces of equipment requires careful work and precise sizing. Using plated diamond wheels is one of the best ways to cut the metal and plastic pieces with the level of precision required for these devices. Do some research and you will quickly see that nearly all of these types of medical devices are created using diamond wheels of some type.
Bone Sawing
Working in the emergency room or operating room requires a steady hand and a lot of hard work. However, this work can be made much easier with the right equipment for the job. Sawing bone is something that must be done for many different procedures. Fortunately, a quality diamond plated wheel can be used to saw through the bone with minimal effort and the best possible results. A bone saw is one of the most important pieces of equipment in any high-tech medical facility diamond plated wheels are of the utmost importance
Dental Uses
Diamond plated wheels are used extensively in the creation of dental burs and other tools. Only with the best wheels can you get the best possible dental equipment. Additionally, diamond wheels are used for bone sawing in the mouth too as a way of reaching areas that require serious oral surgery.
Other Uses
These are just a few of the ways that these diamond plated wheels are used by those in the medical profession. You’ll find that many of the devices used in a modern operating room or doctor’s office are shaped and designed with the use of a grinding wheel. Without this technique, the medical procedures of today would be vastly different and likely not as effective.
Now that you better understand the different ways that diamond plated wheels and similar tools can be used in medicine, your appreciation for the products is likely enhanced. If you want to learn more, contact one of the leading diamond tool manufacturers Continental Diamond Tool. One of our experts will be happy to explain more about how diamond tools are used in medicine as well as in other industries. Plus, we can help you find the best products and solutions available from CDT saving you time and money.
The Best Grinding Tools for the Oil Industry
Learn about the benefits of the various types of abrasives used in the oil and gas industry.
The grinding wheels used in petroleum engineering must be specifically developed to provide the performance needed for these applications. Common grinding applications in the oil industry include the manufacture of drill bits, gage blocks and wear parts. Superabrasives made from polycrystalline diamond (PCD) and carbide are common in this industry, especially for drill bits. Additional types of abrasives used on an oil rig include bonded abrasives and coated abrasives.
Benefits
The benefits of abrasives that have been custom developed for oil and gas applications include greater effectiveness, efficiency and tool life. Grinding tools need the latest bonds to deliver the precision needed for grinding the PCD and carbide bits used in modern drilling. These bits often use centerless wheels that offer a high cutting depth with high grind ratios, which cut costs during grinding operations. PCD abrasives are also used on tools that perform highly-efficient chamfer grinding.
Diamond Abrasives
Diamond abrasives usually refer to abrasives made with PCDs. They are most common in the manufacture of down-hole drill components such as drill bits made to gage. These bits are used in a variety of applications such as centerless, chamfer, form and surface grinding.
Bonded Abrasives
Bonded abrasives include resinoid abrasives and vitrified abrasives. Wheels that use these abrasives in the oil and gas industry can perform both precision and rough grinding applications. Components that are ground with wheels that use bonded abrasives typically have a hard face with a durable coating. These components include the following:
Couplings
Down hole stabilizers
Frac pump plungers
Pistons
Polish rods
Pony rods
Reamer shoes
Shafts
Valves
Bonded abrasives often use proprietary bond and grain formulas to provide performance gains over traditional abrasives such as silicon carbide and aluminum oxide. These benefits include longer grind cycles and a net reduction in cost per part.
Coated Abrasives
Coated abrasives may be used in a variety of forms such as belts, discs, rolls, sheets and wheels. These products are typically composed of cloth, fiber, film and paper for applications that include rough grinding, finishing, lapping and polishing. Products that use coated abrasives can be found in virtually every segment of the oil and gas industry, including petrochemical plants, oil reserves, pipelines and rigs.
Structured abrasives are commonly used to create a consistent finish, while flexible abrasives provide excellent results in high-velocity oxygen fuel spraying applications. Coated abrasives with an agglomerate grain are often used to improve performance with non-woven products such as convolute wheels, belts and discs. Users who wish to lower their total costs for coated abrasive products should consider ceramic belts, flap discs and specialty discs.
Choosing the Right Grinding Tools for the Aerospace Industry
Learn about the role that diamond-grinding tools play in the aerospace industry.
Abrasive technology is an important manufacturing process in many industrial sectors, including aerospace engineering. This technique requires the use of grinding wheels with coated abrasives such as diamond powder, which is extremely abrasive due to diamond's hardness. The best choice of material for bonding the abrasive material to the grinding wheel varies greatly and may need to be customized for a specific application. Diamond grinding creates surfaces with a smoother finish and sharper edges, which is often essential in aerospace research. Superabrasives provide better results in grinding operations that require greater duration, higher speed and cleaner cuts.
Hardness
The most significant factor in selecting the best abrasive material to use in a particular application is the hardness of the material being ground. The Rockwell hardness scales are the most common method of measuring hardness for these applications, especially the Rockwell C scale. This scale is commonly known as the material's RHC, which uses a 120-degree cone under a force of 150 kilogram-force to make an indention in the test material. The RHC measures hardness as a dimensionless number, with values between 20 and 100 generally considered reliable. Superabrasive grinding wheels typically become cost effective for materials with a hardness greater than 45 RHC.
Speed and Cutting
Grinding wheels have ideal ranges for operating speeds and cutting depth that primarily depend on the abrasive material. Diamond grinding wheels should operate at a surface speed between 3,000 feet and 8,000 feet per minute, such that greater speed is better for applications involving frequent interruptions or small areas of contact between the work piece and the grinding wheel. Operators should minimize the depth of the cut to create the best finish and extend the life of the work wheel. The maximum DOC for each pass depends on the particle size of the abrasive material. Abrasives with a grit size between 80 and 150 micrometers shouldn't cut more than 0.002 inches per pass, and abrasives with a grit size between 180 and 220 micrometers should be limited to 0.001 inches per pass. Grit with a size between 240 and 400 micrometers has a maximum DOC of 0.0005 inches per pass, and a 500 to 600 grit size has a maximum DOC of 0.0003 inches.
Bonding
The choice of bonding material is more complex than many of the other decisions involved in diamond grinding. The material comprising the work piece is a critical factor, as is the size of the abrasive particles. Aerospace engineers must also consider the operating speed of the grinding wheel and the type of coolant that will be used. Additional factors in selecting a bonding material include the type of bonding material and its hardness. Some grinding applications use electroplating rather than bonding to attach the abrasive material to the grinding wheel.
To find more information on which application is best for your project, contact CDT today.
CBN Grinding Wheel 101
For projects that require intricate attention to detail, check out cubic boron nitrite (CBN) grinding wheels, their benefits, and who to trust as a supplier.
Cubic boron nitrite grinding wheels are used for projects that require intricate attention to detail. They provide a high-quality tool that will help you produce a beautiful, well manufactured product.
What is a CBN Grinding Wheel?
A CBN wheel is made from cubic boron nitride. This material is one of the hardest materials available, second only to diamonds. The main feature of the material is that it features a high abrasion resistance and thermal conductivity that maintains its sharp cutting edges. It’s a great choice when doing advanced products that require a high attention to details.
Why Use This Type of Wheel?
CBN wheels are important for grinding HSS. This is because it's a better material for sharpening and for durability, one of the best available. Diamond is harder than CBN, but over time many people have discovered that diamond is not a suitable abrasive grain and isn’t a good choice when grinding on high speed dry wheels. Choosing to buy grinding wheels with cubic boron nitrate will offer you the durability you need, while giving you the finished product you desire.
Benefits of CBN Grinding Wheels
These types of wheels have an almost indefinite life span when they are properly cared for. Many have chosen to use these wheels instead of the normal granular wheel because of their durability. The strong nature of the wheels comes from the bonding that takes place between the grains and the supporting steel hub. Thanks to this bonding feature, the wheels can be used dry without any coolant. Only a small amount of pressure is needed to sharpen a tool. The grind is very fine and there are almost no sparks when used for sharpening, unlike similar grinding wheels. The wheel remains cooler than a conventional wheel as well, making it nearly impossible to burn the tools. Choose certified wheel suppliers when looking for a grinding wheel.
Why Buy Grinding Wheels?
Those who have used grinding wheels have seen the benefits of the strong material. The main advantages are that it doesn't heat up when used for sharpening, it provides a perfectly balanced wheel, and has a low risk of blowing up. When it comes to your projects, time, and money, these are benefits that soon become valuable.
Choose certified CBN grinding wheel suppliers when looking for a grinding wheel. You’ll save time and money when you choose a supplier that is well versed in the benefits.
The Right Tools for Every Application
Certain manufacturing would never be possible without serious tools that do a tough job.
It’s not the discovery and control of fire that really separated man from the other animals – it’s tool-making that truly took the human race out of caves and into civilization. Tools changed the course of human history, and today they are still at the heart of every great item made by the hand of man. When you want to make amazing products, you need truly amazing tools. Get the right abrasive grinding wheels for your metal-shaping projects and you’ve got the tools you need to make your business a success.
Certain manufacturing would never be possible without serious tools that do a tough job. We carry everything from mounted grinding wheels to plated wheels, machinery to suit any type of manufacturing project. Isn’t it time you add large company capabilities to your business’s resume?
Grinding Wheels for Maximum Productivity
If it’s maximum productivity you need, look for CBN grinding wheels. The metal bonding on these wheels creates a very tough tool that holds its shape even after hard use. They’re commonly used in wet grinding. They work well on glass, quartz, silicon, ceramics and many other materials, including optics. This offers very low-maintenance, high-quality machining.
Replating for Extended Use
Have a used grinding wheel diamond bonded tool replated for long use. Once the bond has begun to dull, send the tool back to us. On an affordable plan, it’s easy to have that tool replated so that it performs like new again. These tools have an aggressive bond to hold form even after lots of use.
Grinding Wheels for High Efficiency and Precision
Copper or phonelic resin is at the heart of resin bonded grinding wheels. Use these when you want high-efficiency equipment that works precisely and quickly. They self-sharpen, and despite the superabrasive grinding they tend to stay at low temperatures. Use these wheels to polish, sharpen or grind at will. Like bonded wheels, these tools perform well for wet and dry tasks. Use them for glass, alloys, ceramics and many other materials.
Carborundum — the trusted name in grinding wheels
Look for Carborundum grinding wheels when you want a trusted, name brand tool. It’s a well-known name in the grinding business, and their tools are available in many different sizes and types.
Get the quality superabrasive tooling you need in one week or less with our fast delivery policy. Start manufacturing like a large company at prices even small companies can afford. You need the right equipment for every job to get the right results. Start with a company that has all the right machinery. Start with technical experts at Continental Diamond Tool Corporation.
What should you look for in a grinding wheel manufacturer?
To get a product that meets your needs and will stand up to the use that is required, you first need to find the right CBN Grinding Wheel Manufacturer. Make sure you answer these 4 questions before choosing where you will purchase your next wheel.
When creating intricate projects that require precision, you will need a quality CBN (cubic boron nitride) grinding wheel. To make sure you are getting a product that meets your needs and will stand up to the use that is required, you need to find the right CBN Grinding Wheel Manufacturers. Not all manufacturers are created equal, so be sure to do some research before choosing where you will purchase your next wheel. Keep the following tips in mind when you are making your decision.
4 ways to identify the best grinding wheel manufacturer
When looking for a grinding wheel supplier, you’ll want to keep a few things in mind. Remember, your project and product need a wheel that will create a high-quality product and you need a supplier that will get you the wheel you need quickly and correctly, with no hassle.
First, ask yourself the following questions:
Is the supplier certified?
Do they have satisfied customers?
What kind of reviews is the supplier getting?
Where do the grinding wheels come from?
Getting some simple answers before you buy will help save your time and money in the long run. Abrasive suppliers offer a wide variety of products for many different kinds of grinding applications. Choosing the wrong product can cost the supplier time and money. Choosing the wrong supplier will cost you even more time and money.
Choosing the right grinding wheel
Now that you know where you are going to buy your next cubic boron nitride grinding wheel, you will need to know how to choose the right grinding wheel. To identify a quality grinding wheel, you should consider:
Are the abrasive grains distributed throughout the wheel?
What is the percentage of grain and bond? The percentages should be spaced throughout the wheel. The grains do the cutting while the bond holds the grain together.
What shape of wheel do I need? Most wheels come as a straight wheel. The grinding face is on the periphery of a straight wheel. Another variation of the straight wheel is the recessed wheel. The right grinding wheel supplier will have a knowledgeable customer service department that can assist you in finding the right wheel for your needs.
Other grinding wheel purchase considerations
The grinding wheel is only one component of a well engineered machine. The wheel, work material, and the working function all combine to create the tool needed for your job. Buying Diamond grinding wheels for carbide takes some time and attention. Be sure to do the research needed before making the investment. Choose the grinding wheel that is best suited for you needs, while taking into account all the components of the process.
Get a custom quote from an experienced supplier of cutting and grinding products now.
The Perfect Cut
Many industries call for the careful touch achieved by diamond-based tools. When you're in the market for a diamond saw blade manufacturer with whom you can build a successful relationship, make sure you go with a versatile company. You need someone who knows the ins-and-outs, not just of diamond saw manufacturing, but also of its uses and benefits. In order to understand all the advantages, you need an expert well-versed in the many uses of diamond tools.
Many industries call for the careful touch achieved by diamond-based tools. When you're in the market for a diamond saw blade manufacturer with whom you can build a successful relationship, make sure you go with a versatile company. You need someone who knows the ins-and-outs, not just of diamond saw manufacturing, but also of its uses and benefits. In order to understand all the advantages, you need an expert well-versed in the many uses of diamond tools.
When customers ask why they need to buy diamond saw blades above all others, versatility is generally the answer. In those industries where a perfect, polished cut is top priority, nothing does it better than diamonds. Because diamond plated and tipped saws grind rather than hack or cut, they lead to a smoother finish. For materials that leave no margin for error, such as marble and granite, composite materials, certain metals, quartz, ceramic, and fiberglass, mere cutting can ruin the finish. Always choose to buy diamond blades, as the super abrasive grinding creates a cleaner, more flawless edge.
The versatility of diamond tools continues. Be aware of the benefits of using a continuous rim diamond blade on wet and dry materials. In fact, using a diamond blade on wet or damp materials sometimes leads to a better, smoother cut. With concrete, granite, and certain kinds of marble, especially, wetting down the material is widely understood to create better results. However, when manufacturing medical tools, working with quartz or fiberglass, or dealing with carbine, a dry grind promises a look that is just as clean and smooth.
It's easy to see why it is so essential to choose a relationship with an expert company. Better still, look for manufacturers of diamond blade saws who guarantee quality work and understand the importance of quick delivery. A speedy turn-around practically ensures repeat business as everyone will be both happy and fully satisfied. It's a win/win situation for everybody. That's why it's essential to forge a solid relationship with a quality manufacturer who will get you the machines you need.
Diamond tip saw blades are the standard in many industries, especially those which depend on professional grade work with no mistakes. Whether you're making a memorial or working on the latest medical innovation, you want flawless craftsmanship created by a company that stands by its work, promises remarkable customer services in all areas, and understands how to manufacture solid, efficient diamond-based tools.
To get your custom quote, click here.
What do Scientists, Construction Workers and the Medical Industry Have in Common?
It sounds like a joke: What do scientists, construction workers, and the medical industry have in common? The answer is...
It sounds like a joke: What do scientists, construction workers, and the medical industry have in common? The answer is diamond cutting blades that let each do extraordinary jobs to make the world a better place. From shaping gemstones into dazzling creations that fit on the most slender finger to grinding through asphalt and concrete to make way for a new mall, these diamond cutting tools represent a marriage of power and precision.
When selecting a diamond cutting blade for a particular job, there are several things you should consider. First, what type or shape of diamond saw blades will work best? The circular blade gets wide usage because it handles so many tasks with ease. It’s also available in extremely slender forms. On the other hand, specialized diamond cutting tools work better for certain jobs. For instance, working with a gemstone requires smaller tools, so bonding diamonds to a thin wire is necessary.
You also need to think carefully about the kind of bond you want for your diamond cutting tools. The bond refers to the powder metals that hold the diamond to the base, and the bond is either soft or hard. Though it might seem a bit counter-intuitive, you want a soft bond on the diamond cutting blades when you’re grinding through very tough material. The softer bond falls away more quickly, allowing new diamond edges to make frequent contact with the material you’re cutting. By creating contact with newer diamond surfaces that are sharp, the diamond saw blades make a better go of cutting up hard material. Don’t forget to consider what size diamonds you need, what concentration of diamonds you need on the blade, and their toughness. Take your cues from the material you’re cutting as you choose the right diamond cutting disc for the job.
Regardless of what kind of work you’re doing, consider whether you need to use water with your diamond cutting wheels. Water reduces dust flying into the air during grinding. It also cools the diamond saw blades and helps give these blades longevity. So, usually, it’s advisable to use diamond cutting tools wet and not dry.
When ordering a diamond cutting disc, be sure to request the correct diameter, blank thickness, arbor hole, and slots. In addition, consider adding diamond plated ribs to your blade to reduce wear and help with side cutting. Also specify the kind of edge you want, either round or square, for your diamond cutting blades. Ask about any special requests you have about tolerance and the thickness of the cut.
Resin Hybrid Grinding Wheels are 'Gold' for the Cutting Tool Industry
Last month CDT released its response to the competition's hybrid wheels to handle the extreme cutting conditions in tool grinding. Cutting Tool manufacturers have been pleasantly surprised by the results.
Last month CDT released its response to the competition's hybrid wheels to handle the extreme cutting conditions in tool grinding. Cutting Tool manufacturers have been pleasantly surprised by the results.
In a head-to-head comparison, the competitor's fluting was originally done in two passes. The CDT Hybrid Bond achieved a single pass at double the feed rate with no damage to the workpiece while achieving a 25% increase in finish.
With equally outstanding primary and secondary grind results, the Hybrid Bond increased the primary and secondary operations by four times while continuing to produce a better finish.
The Hybrid Series for Tool & Cutter Grinding uses Advanced Bond technology, allowing for a quicker grind without losing the wheel edge. Flute from solid, regrind, gash and end work, and relief. Cutting Tool manufacturers will find:
Excellent precision at the highest feed rates
Increased productivity while lowering process costs
Superior wheel life and long dressing interval
Withstands cutting forces from high-speed, high-temperature applications
Because the Hybrid bond is not your standard “one size fits all” but is tailored to the specific grinding application, it allows for the highest quality tool in the most efficient amount of time in the Cutting Tool industry. This level of customization is unique to CDT's newest bond.
These one-of-a-kind properties improve the performance of the CNC Tool and Cutter Grinder in many ways:
Free cutting action with superior form retention and surface finish
Self sharpening bond lengthens wheel life and dressing interval
High material removal rate with high temperature stability
Maximum heat dissipation with low and constant power consumption
Optimal wheel profile stability lowers costs due to wear
If it's time to replace your old conventional worn parts with high quality precision grinding wheels and tools, you should consider CDT's Hybrid Series for Tool & Cutter Grinding. Backed by more than 40 years of superior craftsmanship and expertise in this field, CDT products are made in America and generally ship in 15 days. CDT customer service techs are happy to look through the parameters of your project, make recommendations, and supply a competitive quote - call 800-443-6629 for more information.
Do Your Grinding Wheels Need A Tune Up?
It's a fact that grinding wheels will endure wear and tear over time. Because of this, they require regular maintenance to keep them working like new, so grinding wheel dressers and dressing sticks become integral parts of the process.
t’s a fact that grinding wheels will endure wear and tear over time. Because of this, they require regular maintenance to keep them working like new, so grinding wheel dressers and dressing sticks become integral parts of the process.
Grinding wheel dressers are also known as grinding dressers or wheel dressers. Diamond dressers offer many benefits, some of which include a decreased dressing cost per piece, a constant high-precision operation, optimal dresser versatility, and fast dressing of even the most complex wheel profiles. Since different designs and applications call for different dressing tools, it’s important to work with a supplier that can help you determine which type will work best for your needs. Four of the basic types most commonly used with CNC grinders include stationary dressers, crush rolls, diamond crush rolls, and rotary dressers, all of which are used for grinding more complex shapes.
Aside from the grinding dresser itself, you may also need dressing sticks. These are stick-shapes made from a hard material, generally the same material as a dresser, but they use a stronger bonding agent. This gives them a harder composition than the grinding wheel. Properly selected grinding sticks can not only be used for dressing and truing conventional vitrified abrasive wheels, but they can improve the performance of CBN and diamond grinding wheels as well.
Fine particles will be flying off of the wheel during truing or dressing and it’s important to note that, when working with grinding sticks or any superabrasive tools, you should wear safety glasses in order to avoid eye injury. Remember to always store grinding wheel dressers and other metal tools in a dry location to avoid rust. Maintain a clean work area to cut down on the likelihood of injury and check for damaged parts before using any grinding wheel, dresser, or dressing stick.
Whether you use a CBN or diamond grinding wheel or other cutting products, having the right tools for the job is of the utmost importance. A company like Continental Diamond Tool can provide quality tools and custom manufacturing to suit your specific needs, with precision products and outstanding customer service without rival. Order products tailor-made to your project’s needs, produced by skilled technicians who can supply a finished product in as little as a week. Enjoy stellar customer service that will ensure, from start to finish, that you are getting the right product for your needs.
When the Material Gets Tough ...
When you need to cut through thick, abrasive surfaces, equip yourself with a diamond saw blade that has the power to tackle these kinds of jobs. Eliminate frustration by using the best tool for cutting through concrete, glass, marble, granite, and similar hard materials. Used extensively for shaping gems, slicing superconductors, and in construction, these diamond cutting blades offer both heft and precision.
When you need to cut through thick, abrasive surfaces, equip yourself with a diamond saw blade that has the power to tackle these kinds of jobs. Eliminate frustration by using the best tool for cutting through concrete, glass, marble, granite, and similar hard materials. Used extensively for shaping gems, slicing superconductors, and in construction, these diamond cutting blades offer both heft and precision.
The circular design is the most common. However, there are other kinds of diamond saw blades. Stone blocks that need cutting respond well to a grouping of diamond gang saw blades. These consist of diamond segments attached to a steel plate that has a sizable length. Band saws with diamonds typically have them placed on the teeth. Some industries get creative in developing their own tools using diamond blades. For example, diamond abrasives applied to wire become a precision tool for jewelry makers.
What makes a diamond saw blade special is its ability to grind up material and not cut it. Powder metals form the bond that holds the diamond segments to the blade. As the bonds wear down, new diamond surfaces get exposed, creating sharper angular surfaces for grinding. When deciding what type of blade to use, it’s best to select a bond that works well with the material you need to cut. For example, cutting a hard material requires a bond that gives way more quickly so that sharper diamond edges become available fast enough to grind the material.
There are three different ways to make diamond cutting wheels. Sintering and vacuum brazing are not as effective as plating. This process allows a layer of diamond bits to work while being exposed from the bonding agent, a set-up that’s preferable to having them actually embedded in the bond.
Plating allows you to preserve your tools by making it easy to refurbish the saw blade when it’s worn out. Instead of trashing the entire saw, you merely have the blade replated. With plating, it’s possible to remove the run down layer of diamonds and apply a new one. Because diamond cutting blade are restorable in this way, they’re a wise investment for any business or individual who uses them frequently. In addition, through the electroplating process, the diamond layer holds its form for an extended period of time, giving it superior performance. Even though it’s strippable, the abrasive bond is very strong. Plated diamond cutting tools typically last a long time because you can refresh them when the blades wear out.